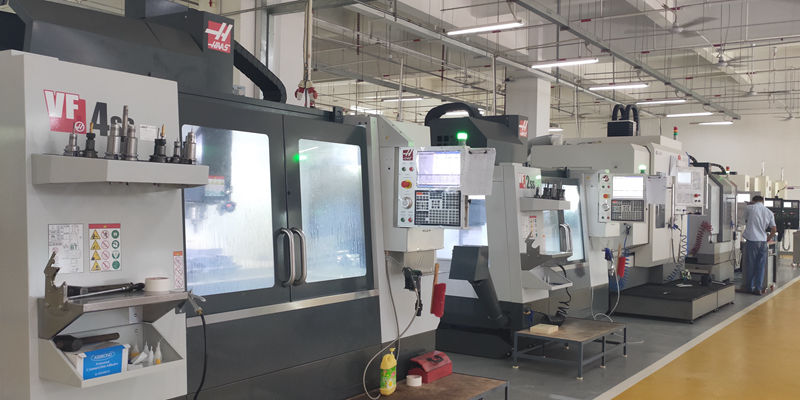
Industrial management is an engineering field where different engineering processes are integrated in order to create a management system. An industrial manager helps to integrate these engineering processes into a single, integrated management system. Here are some important facts about the job. Here are the requirements and benefits of becoming an industrial manager. If you have the qualifications required and are looking for a rewarding job with high rewards, this career is right for you. Continue reading for more information.
Job description
An industrial manager oversees the processes involved in the manufacturing and production of goods and services. This job will cover many aspects of production, but it will also include how to source raw materials or implement equipment. Computer literacy is essential for industrial production managers, who must be able to use computers to coordinate the work of different departments, suppliers, clients, and other parties. In addition, industrial production managers must be well-versed in the latest production technologies and management practices. Many managers take part in professional organizations, attend tradeshows and conferences in the industry, and enroll in courses to earn certification.
Industrial managers coordinate the activities in various departments within an organization, and they also oversee manufacturing processes. They ensure that production lines are productive and meet customer expectations in terms both quality and speed. They can also manage staffing levels, and adjust production levels as needed to reduce inventory. They might also coordinate with other departments and oversee quality control programs. Majority of their responsibilities involve managing people. This involves identifying, training, motivating and motivating employees.
Education Required
For industrial managers, a bachelor's level in business administration, management, engineering or other related fields is not enough. However, certain employers do prefer to hire candidates with a background in one of those fields. A computer-literate industrial manager is also required. Computers are an integral part of manufacturing. They coordinate production across departments, suppliers, customers, and even between clients. This field requires that interested people have the required education and work experience.
Many industrial production managers start their career as production workers and advance to first-line supervisory positions. All professionals must obtain a college business management degree to reach the industrial manager level. However, there are some workers who can get this education on the jobs. Or they might choose to go to classes sponsored and paid by their company. Managers are expected to have at least two to five years' experience in the relevant field before they can become managers.
Your potential to earn
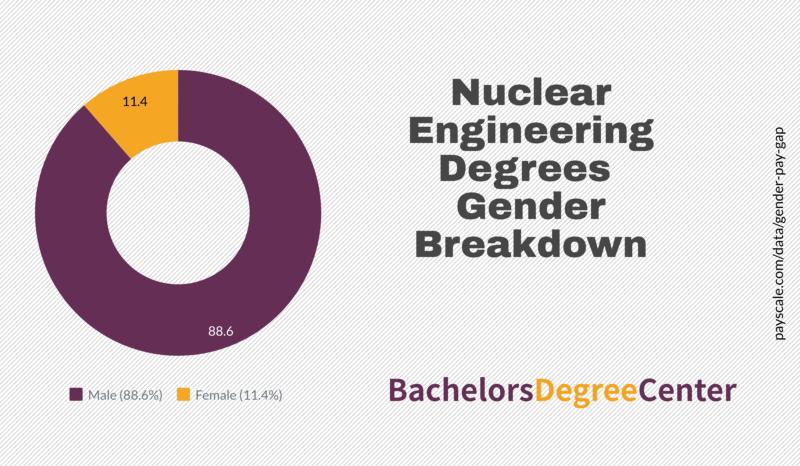
Managers in industrial plants oversee the smooth functioning of the whole process. They determine the best way to use employees and equipment, set production standards and make strategic choices. These people are responsible for evaluating and hiring workers. They also set production schedules and ensure safety. They oversee the day to day activities of a group of workers and analyze the production process continuously to ensure that it runs efficiently and at its peak efficiency.
The employer's experience and the earnings potential of industrial production managers will affect their earning potential. While it's difficult to predict the future earnings of industrial managers, the average salary in May 2016 was $103,380, with the highest paid industrial production managers earning $172,150 annually. Higher earnings may also be available for industrial production managers who have completed advanced training or certification. According to the U.S. Bureau of Labor Statistics (USBoLS), industrial production managers who hold a bachelor's or higher degree in manufacturing management may earn more.
Work environment
An industrial production manager splits time between the office and the production floor, sometimes in the same place. Industrial production managers must observe established health and safety practices and wear appropriate protective equipment when working in a production area. They also spend significant amounts of time in meetings with subordinates and analyzing production data. They may also be responsible for writing reports. As a result, an industrial production manager's work environment is often dynamic.
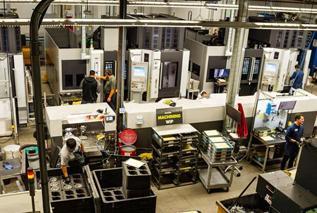
The industrial production manager is an important part of a company's management structure. They are responsible for coordinating the activities of workers and increasing productivity. A manager of industrial production is responsible for increasing productivity and safety. Many levels of management have been eliminated, and support staff has been reduced. This leaves more work for production managers. This can be a significant challenge for any manager, and can make it difficult to do the job as a production manager.
FAQ
How can we improve manufacturing efficiency?
The first step is to identify the most important factors affecting production time. Next, we must find ways to improve those factors. You can start by identifying the most important factors that impact production time. Once you've identified them, try to find solutions for each of those factors.
How can manufacturing avoid production bottlenecks
Production bottlenecks can be avoided by ensuring that processes are running smoothly during the entire production process, starting with the receipt of an order and ending when the product ships.
This includes both planning for capacity and quality control.
This can be done by using continuous improvement techniques, such as Six Sigma.
Six Sigma is a management system used to improve quality and reduce waste in every aspect of your organization.
It's all about eliminating variation and creating consistency in work.
What is the responsibility for a logistics manager
Logistics managers ensure that goods arrive on time and are unharmed. This is accomplished by using the experience and knowledge gained from working with company products. He/she should ensure that sufficient stock is available in order to meet customer demand.
What does it mean to warehouse?
Warehouses and storage facilities are where goods are kept before being sold. It can be an outdoor or indoor area. Sometimes, it can be both an indoor and outdoor space.
Is automation necessary in manufacturing?
Not only is automation important for manufacturers, but it's also vital for service providers. It enables them to provide services faster and more efficiently. It helps them to lower costs by reducing human errors, and improving productivity.
Statistics
- Job #1 is delivering the ordered product according to specifications: color, size, brand, and quantity. (netsuite.com)
- It's estimated that 10.8% of the U.S. GDP in 2020 was contributed to manufacturing. (investopedia.com)
- According to a Statista study, U.S. businesses spent $1.63 trillion on logistics in 2019, moving goods from origin to end user through various supply chain network segments. (netsuite.com)
- According to the United Nations Industrial Development Organization (UNIDO), China is the top manufacturer worldwide by 2019 output, producing 28.7% of the total global manufacturing output, followed by the United States, Japan, Germany, and India.[52][53] (en.wikipedia.org)
- (2:04) MTO is a production technique wherein products are customized according to customer specifications, and production only starts after an order is received. (oracle.com)
External Links
How To
How to Use lean manufacturing in the Production of Goods
Lean manufacturing refers to a method of managing that seeks to improve efficiency and decrease waste. It was developed in Japan between 1970 and 1980 by Taiichi Ohno. TPS founder Kanji Tyoda gave him the Toyota Production System, or TPS award. Michael L. Watkins published the "The Machine That Changed the World", the first book about lean manufacturing. It was published in 1990.
Lean manufacturing refers to a set of principles that improve the quality, speed and costs of products and services. It is about eliminating defects and waste from all stages of the value stream. Lean manufacturing is called just-in-time (JIT), zero defect, total productive maintenance (TPM), or 5S. Lean manufacturing eliminates non-value-added tasks like inspection, rework, waiting.
Lean manufacturing can help companies improve their product quality and reduce costs. Additionally, it helps them achieve their goals more quickly and reduces employee turnover. Lean manufacturing can be used to manage all aspects of the value chain. Customers, suppliers, distributors, retailers and employees are all included. Many industries worldwide use lean manufacturing. Toyota's philosophy is a great example of this. It has helped to create success in automobiles as well electronics, appliances and healthcare.
Lean manufacturing includes five basic principles:
-
Define Value - Determine the value that your business brings to society. Also, identify what sets you apart from your competitors.
-
Reduce waste - Stop any activity that isn't adding value to the supply chains.
-
Create Flow – Ensure that work flows smoothly throughout the process.
-
Standardize & simplify - Make processes consistent and repeatable.
-
Develop Relationships: Establish personal relationships both with internal and external stakeholders.
Lean manufacturing is not a new concept, but it has been gaining popularity over the last few years due to a renewed interest in the economy following the global financial crisis of 2008. Many companies have adopted lean manufacturing methods to increase their marketability. According to some economists, lean manufacturing could be a significant factor in the economic recovery.
Lean manufacturing is now becoming a common practice in the automotive industry, with many benefits. These include better customer satisfaction and lower inventory levels. They also result in lower operating costs.
It can be applied to any aspect of an organisation. Lean manufacturing is most useful in the production sector of an organisation because it ensures that each step in the value-chain is efficient and productive.
There are three types of lean manufacturing.
-
Just-in Time Manufacturing: This lean manufacturing method is commonly called "pull systems." JIT stands for a system where components are assembled on the spot rather than being made in advance. This approach is designed to reduce lead times and increase the availability of components. It also reduces inventory.
-
Zero Defects Manufacturing, (ZDM): ZDM is focused on ensuring that no defective products leave the manufacturing facility. If a part needs to be fixed during the assembly line, it should be repaired rather than scrapped. This applies to finished products, which may need minor repairs before they are shipped.
-
Continuous Improvement (CI), also known as Continuous Improvement, aims at improving the efficiency of operations through continuous identification and improvement to minimize or eliminate waste. It involves continuous improvement of processes, people, and tools.