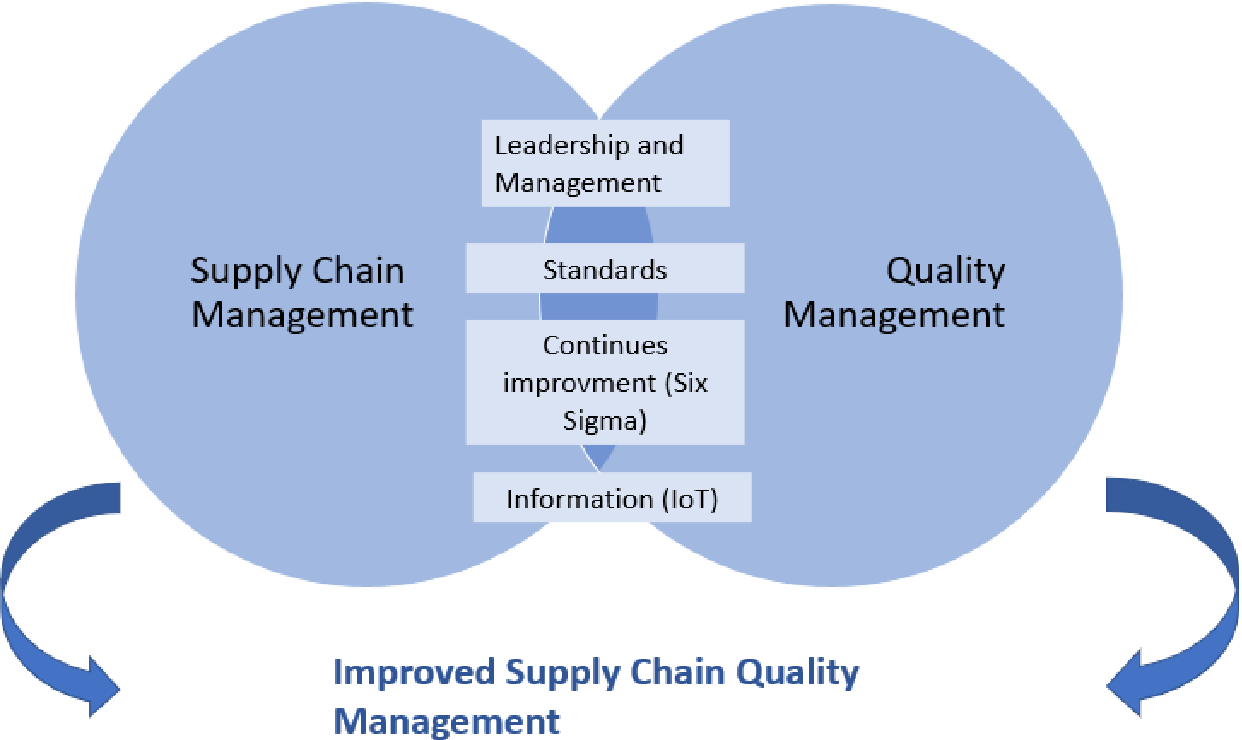
High-paying job opportunities are available for anyone looking to enter the manufacturing industry. There are many types and levels of manufacturing jobs. Explore all the options available and decide the best manufacturing career for you.
The best manufacturing jobs require a combination both of theoretical and practical skills. To determine which skills are most valuable to you, you will need to establish parameters. Ophthalmic laboratory technician is a good choice if you are interested in repair eyeglasses. If you are interested in mechanical or electrical engineering, however, these jobs may be the most lucrative.
The United States' manufacturing industry is an important contributor to the economy. It produces more economic activity per capita than any other sector. It is responsible for a large share of the country's economic growth and has a significant number of its employees. It is also the most important industry in the country, and it holds the largest percentage of the nation’s economic development.
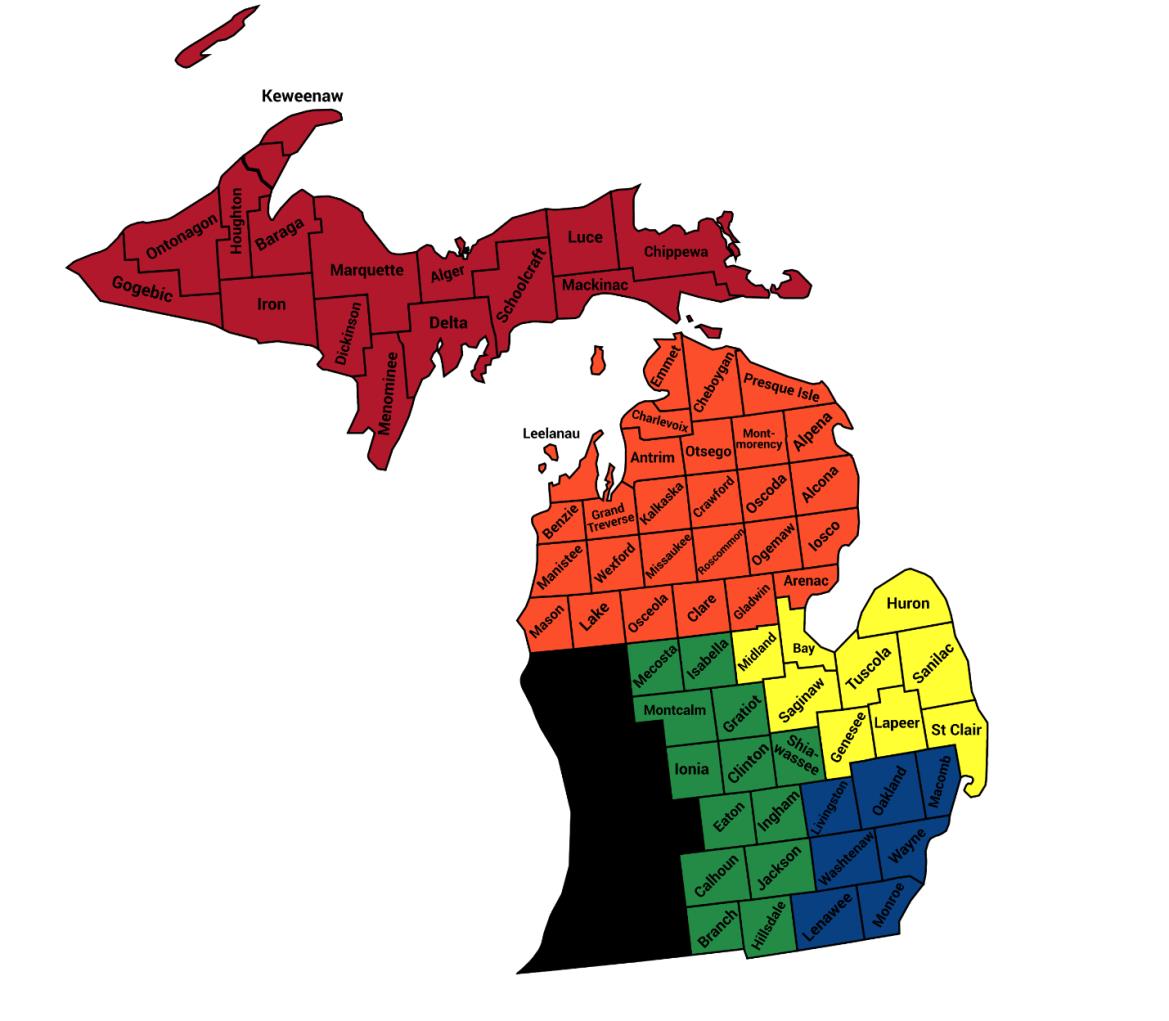
Advanced technical skills and experience are required for the most lucrative manufacturing jobs. But entry-level positions exist and can be a great opportunity to get into the industry. They're also generally well-paying, and offer excellent benefits. In fact, the average advertised salary has risen 1.5% in the last year.
Signing up for an online course can help you get your foot in the door. For coding training, you can enroll in an online bootcamp or a formal coding course. If you're already a certified electrician or welder, you may be in luck, as these are some of the highest paying manufacturing jobs. Many companies will pay experienced manufacturing talent to make it a lucrative career as a contractor.
A variety of skills are required to be successful in manufacturing, including problem-solving and critical thought. You might have to ensure your products are consistent and your manufacturing processes comply with all regulations. You might also want to make the most out of all technology.
Manufacturing jobs are often physically demanding because you need to operate heavy equipment. You may be required to work in a shop or laboratory, depending on the employer. The highest paying manufacturing jobs are the ones that require the most advanced technical skills and experience.
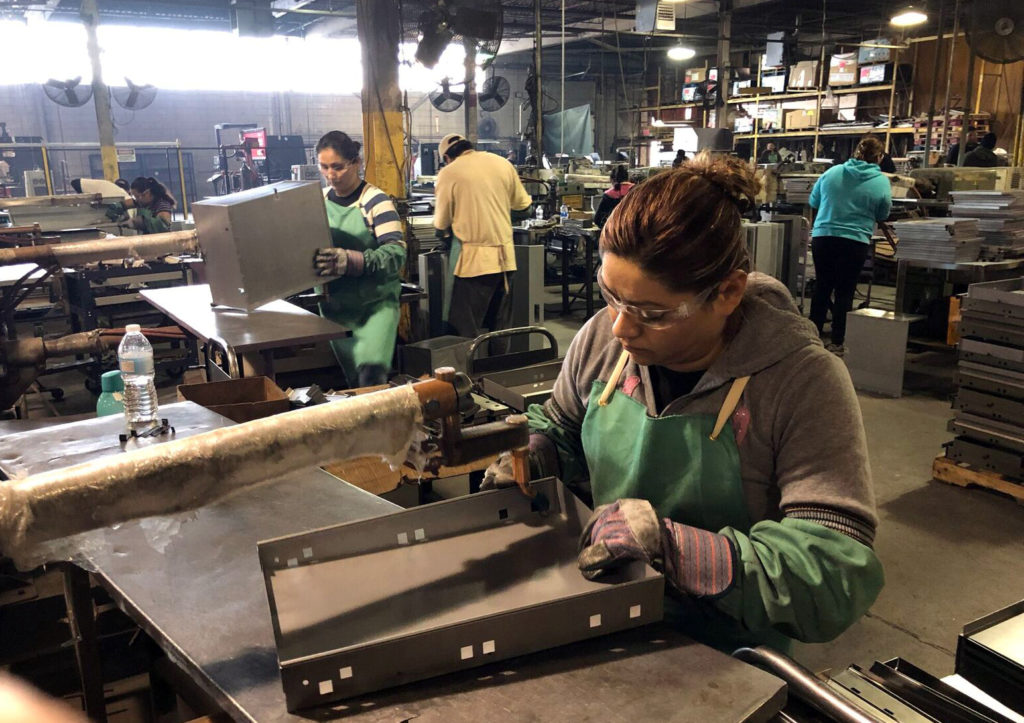
You should look at the various industries and companies in each industry to find out about the highest-paid manufacturing jobs. These range from apparel manufacturers to car factories to electronics production facilities. Choosing the manufacturing job that best suits you can be challenging, but rewarding. This is also a great opportunity to learn new skills.
An electromechanical technician is the best-paid job in manufacturing. As an electromechanical technician, you will be responsible of maintaining and repairing various manufacturing equipment. In order to qualify, you will usually need to have a degree either in engineering or computer sciences. A high school diploma can be enough to get started in the field.
FAQ
What is the difference in Production Planning and Scheduling, you ask?
Production Planning (PP) is the process of determining what needs to be produced at any given point in time. This can be done by forecasting demand and identifying production capabilities.
Scheduling is the process that assigns dates to tasks so they can get completed within a given timeframe.
Are there any Manufacturing Processes that we should know before we can learn about Logistics?
No. No. It is important to know about the manufacturing processes in order to understand how logistics works.
What is meant by manufacturing industries?
Manufacturing Industries are businesses that produce products for sale. Consumers are people who purchase these goods. These companies use various processes such as production, distribution, retailing, management, etc., to fulfill this purpose. They produce goods from raw materials by using machines and other machinery. This covers all types of manufactured goods including clothing, food, building supplies and furniture, as well as electronics, tools, machinery, vehicles and pharmaceuticals.
How can manufacturing efficiency improved?
First, we need to identify which factors are most critical in affecting production times. The next step is to identify the most important factors that affect production time. If you don't know where to start, then think about which factor(s) have the biggest impact on production time. Once you identify them, look for solutions.
Why should you automate your warehouse?
Modern warehouses have become more dependent on automation. The rise of e-commerce has led to increased demand for faster delivery times and more efficient processes.
Warehouses must be able to quickly adapt to changing demands. To do so, they must invest heavily in technology. Automating warehouses is a great way to save money. Here are some reasons why it's worth investing in automation:
-
Increases throughput/productivity
-
Reduces errors
-
Increases accuracy
-
Safety Boosts
-
Eliminates bottlenecks
-
Allows companies to scale more easily
-
Increases efficiency of workers
-
It gives visibility to everything that happens inside the warehouse
-
Enhances customer experience
-
Improves employee satisfaction
-
Reduces downtime and improves uptime
-
Ensures quality products are delivered on time
-
Eliminates human error
-
It helps ensure compliance with regulations
How can manufacturing excess production be decreased?
The key to reducing overproduction lies in developing better ways to manage inventory. This would reduce the amount of time spent on unnecessary activities such as purchasing, storing, and maintaining excess stock. This could help us free up our time for other productive tasks.
A Kanban system is one way to achieve this. A Kanban board, a visual display to show the progress of work, is called a Kanban board. Kanban systems allow work items to move through different states until they reach their final destination. Each state is assigned a different priority.
To illustrate, work can move from one stage or another when it is complete enough for it to be moved to a new stage. But if a task remains in the beginning stages it will stay that way until it reaches its end.
This helps to keep work moving forward while ensuring that no work is left behind. A Kanban board allows managers to monitor how much work is being completed at any given moment. This data allows them adjust their workflow based upon real-time data.
Lean manufacturing can also be used to reduce inventory levels. Lean manufacturing emphasizes eliminating waste in all phases of production. Anything that does not contribute to the product's value is considered waste. Some common types of waste include:
-
Overproduction
-
Inventory
-
Packaging that is not necessary
-
Material surplus
These ideas can help manufacturers improve efficiency and reduce costs.
Statistics
- Job #1 is delivering the ordered product according to specifications: color, size, brand, and quantity. (netsuite.com)
- In 2021, an estimated 12.1 million Americans work in the manufacturing sector.6 (investopedia.com)
- According to a Statista study, U.S. businesses spent $1.63 trillion on logistics in 2019, moving goods from origin to end user through various supply chain network segments. (netsuite.com)
- (2:04) MTO is a production technique wherein products are customized according to customer specifications, and production only starts after an order is received. (oracle.com)
- It's estimated that 10.8% of the U.S. GDP in 2020 was contributed to manufacturing. (investopedia.com)
External Links
How To
Six Sigma and Manufacturing
Six Sigma is "the application statistical process control (SPC), techniques for continuous improvement." Motorola's Quality Improvement Department developed it at their Tokyo plant in Japan in 1986. Six Sigma's core idea is to improve the quality of processes by standardizing and eliminating defects. In recent years, many companies have adopted this method because they believe there is no such thing as perfect products or services. Six Sigma's primary goal is to reduce variation from the average value of production. If you take a sample and compare it with the average, you will be able to determine how much of the production process is different from the norm. If there is a significant deviation from the norm, you will know that something needs to change.
Understanding the nature of variability in your business is the first step to Six Sigma. Once you understand this, you can then identify the causes of variation. You'll also want to determine whether these variations are random or systematic. Random variations are caused when people make mistakes. While systematic variations are caused outside of the process, they can occur. Random variations would include, for example, the failure of some widgets to fall from the assembly line. You might notice that your widgets always fall apart at the same place every time you put them together.
Once you've identified where the problems lie, you'll want to design solutions to eliminate those problems. It might mean changing the way you do business or redesigning it entirely. After implementing the new changes, you should test them again to see if they worked. If they don't work, you will need to go back to the drawing boards and create a new plan.