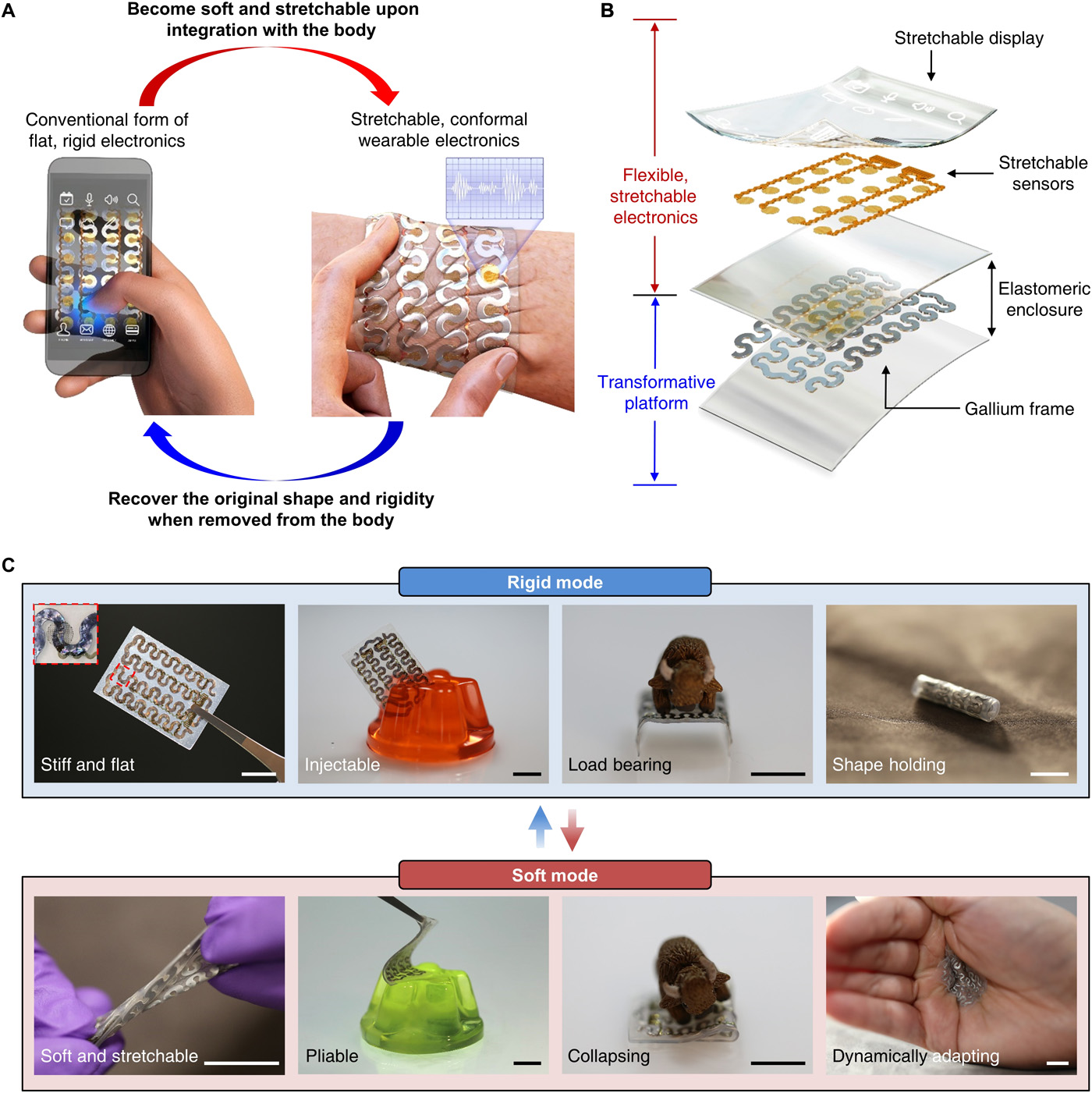
There are many kinds of manufacturers. How do you choose the right one for your business? Learn more about continuous manufacturing, process manufacturing, job shop manufacturing, and discrete manufacturing. Each type of manufacturing has its advantages and disadvantages. This article will show you how the four types of manufacturing differ. Based on your industry, location and product type, you will be able to choose the right model for your business. Once you have chosen the best type for your business, you must consider sales, production, as well as quality control.
Discrete manufacturing
Discrete manufacture is a manufacturing process that produces distinct products. These products can include toys, airplanes, and automobiles. Companies can concentrate on one product and not all products with discrete manufacturing. By integrating multiple manufacturing processes, discrete manufacturing allows you to create unique parts for your aircraft. High-tech products are made using discrete manufacturing.
Discrete manufacturing produces distinct items. Instead of producing many identical products discrete manufacturing creates items that are easily identifiable by serial numbers and labels. For example, a smartphone could be composed of several parts that were manufactured in different states. Each part is assembled only after the final product has been sold. The same applies to the bag that holds your smartphone. It may contain different parts from several plants, including the headquarters and the Missouri plant.
Process manufacturing
Process manufacturing refers to a type of manufacturing that uses formulas and recipes. The term process manufacturing is not the same as discrete manufacturing. This refers to manufacturing that involves individual units, bills or materials and the assembly of component parts. Both manufacturing methods have different goals. Each of these methods is important in the manufacturing process. There are three main ways to distinguish process manufacturing from discrete manufacturing. Let's examine each one.
Batch manufacturing is similar to continuous manufacturing but uses larger quantities of raw materials and can run around the clock. Batch manufacturing is common in pharmaceuticals and paper production. This method may not be the right fit for all industries. This method is often too complicated and expensive for small-scale businesses. This is why large-scale companies often use it when they need to make large quantities.
Manufacturing job shop
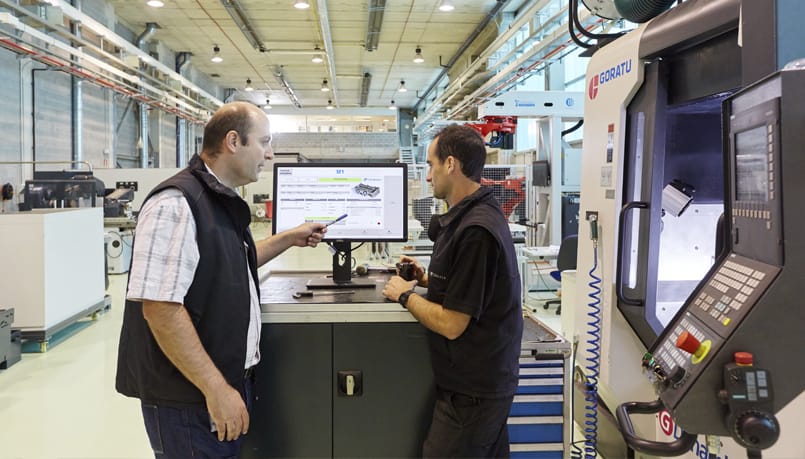
Job shop manufacturing is a small-scale system of production that specializes in custom, batch, and semi-custom manufacturing. Job shop systems can then move on to the next job as each job is finished. This method of production is also called lean manufacturing, as a single-shift operation is more efficient than many other methods. Here are some benefits of job shop manufacturing. You can read on to learn about this type of manufacturing. This method of manufacturing might be beneficial for your business.
First, job shop efficiency must be improved. A critical factor in achieving a lean manufacturing system is incorporating new manufacturing principles. These principles apply to high-volume operations as they emphasize quality control, just-in time production, and are very relevant. Job shops can increase productivity and decrease costs by adopting new manufacturing methods. Each job must be done one at a given time. There should not be any waiting.
Continuous manufacturing
One of the biggest benefits of continuous manufacturing is the fact that it allows for much more flexible tracking. This is especially helpful in the event of product failure. Product data such as the amount of raw material used and the time stamp at each production line can be used for identifying defective batches. This increased tracking helps manufacturers reduce waste and decrease the likelihood of product shortages. Continuous manufacturing is also becoming more popular in the pharmaceutical sector.
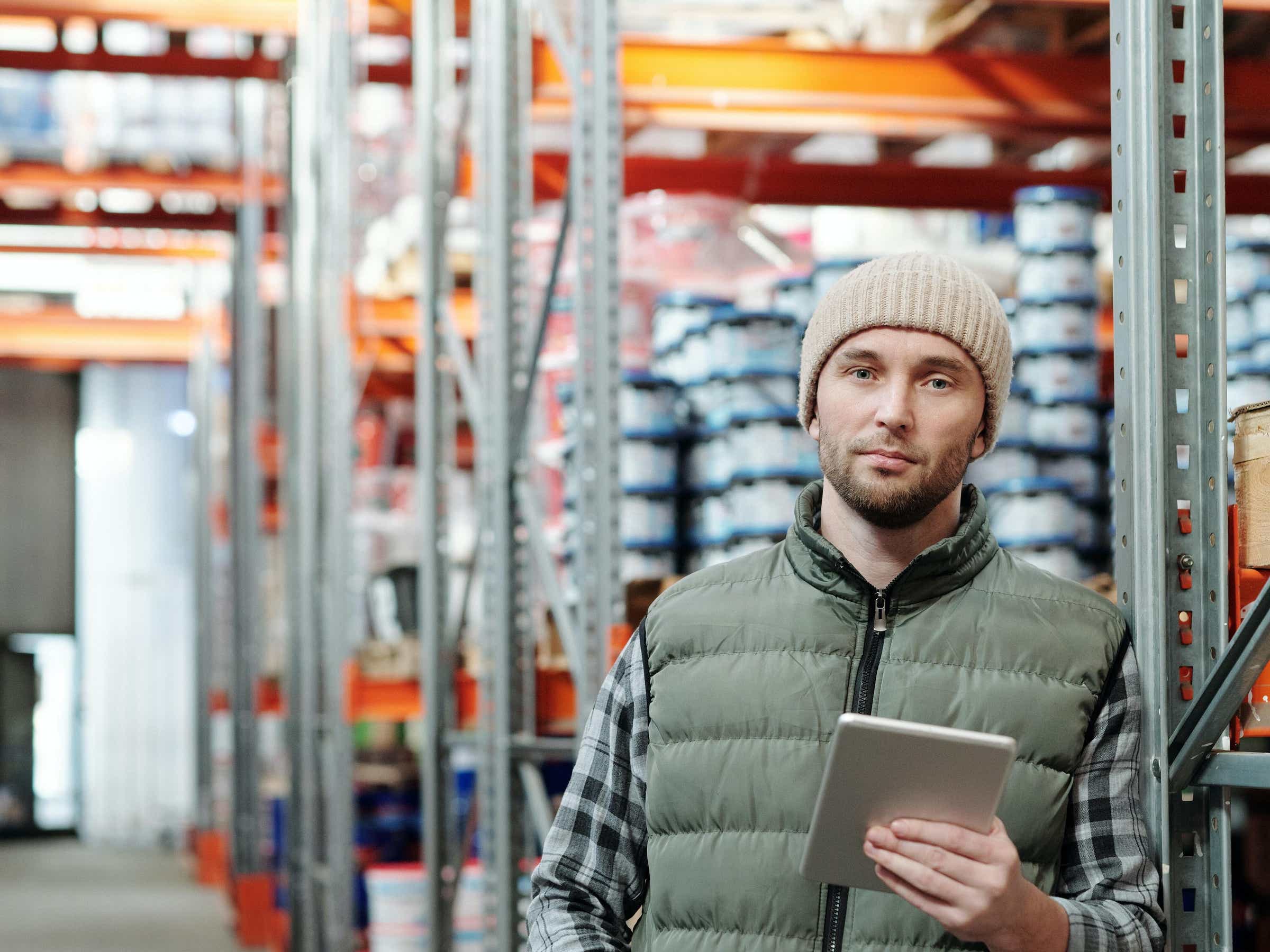
While continuous manufacturing is a great option, it can be slow to implement. The slow pace of implementation can make it difficult to integrate the manufacturing process with the rest. Regardless of the benefits, continuous manufacturing has the potential to be a game changer for the pharmaceutical industry. To be successful, however, the entire process must be integrated with continuous flow as well as end-to–end integration. Continuous manufacturing has long been recognized in the pharmaceutical industry, but its implementation has been slow.
FAQ
What is the importance of automation in manufacturing?
Automating is not just important for manufacturers, but also for service providers. It allows them to offer services faster and more efficiently. It helps them to lower costs by reducing human errors, and improving productivity.
What are the logistics products?
Logistics involves the transportation of goods from point A and point B.
They encompass all aspects transport, including packaging and loading, transporting, storage, unloading.
Logisticians ensure that products reach the right destination at the right moment and under safe conditions. They help companies manage their supply chain efficiency by providing information on demand forecasts, stock levels, production schedules, and availability of raw materials.
They monitor shipments in transit, ensure quality standards, manage inventories, replenish orders, coordinate with suppliers and other vendors, and offer support services for sales, marketing, and customer service.
How can efficiency in manufacturing be improved?
The first step is to determine the key factors that impact production time. We then need to figure out how to improve these variables. You can start by identifying the most important factors that impact production time. Once you identify them, look for solutions.
Why automate your factory?
Modern warehousing has seen automation take center stage. E-commerce has increased the demand for quicker delivery times and more efficient processes.
Warehouses must be able to quickly adapt to changing demands. In order to do this, they need to invest in technology. Automating warehouses is a great way to save money. Here are some benefits of investing in automation
-
Increases throughput/productivity
-
Reduces errors
-
Improves accuracy
-
Boosts safety
-
Eliminates bottlenecks
-
This allows companies to scale easily
-
Increases efficiency of workers
-
Provides visibility into everything that happens in the warehouse
-
Enhances customer experience
-
Improves employee satisfaction
-
Reducing downtime and increasing uptime
-
High quality products delivered on-time
-
Removing human error
-
Helps ensure compliance with regulations
How can manufacturing reduce production bottlenecks?
You can avoid bottlenecks in production by making sure that everything runs smoothly throughout the production cycle, from the moment you receive an order to the moment the product is shipped.
This includes planning for capacity requirements as well as quality control measures.
The best way to do this is to use continuous improvement techniques such as Six Sigma.
Six Sigma is a management method that helps to improve quality and reduce waste.
It is focused on creating consistency and eliminating variation in your work.
What does it mean to be a manufacturer?
Manufacturing Industries refers to businesses that manufacture products. The people who buy these products are called consumers. This is accomplished by using a variety of processes, including production, distribution and retailing. They produce goods from raw materials by using machines and other machinery. This includes all types and varieties of manufactured goods, such as food items, clothings, building supplies, furnitures, toys, electronics tools, machinery vehicles, pharmaceuticals medical devices, chemicals, among others.
Statistics
- [54][55] These are the top 50 countries by the total value of manufacturing output in US dollars for its noted year according to World Bank.[56] (en.wikipedia.org)
- In the United States, for example, manufacturing makes up 15% of the economic output. (twi-global.com)
- (2:04) MTO is a production technique wherein products are customized according to customer specifications, and production only starts after an order is received. (oracle.com)
- According to a Statista study, U.S. businesses spent $1.63 trillion on logistics in 2019, moving goods from origin to end user through various supply chain network segments. (netsuite.com)
- It's estimated that 10.8% of the U.S. GDP in 2020 was contributed to manufacturing. (investopedia.com)
External Links
How To
How to Use 5S to Increase Productivity in Manufacturing
5S stands in for "Sort", the "Set In Order", "Standardize", or "Separate". The 5S methodology was developed at Toyota Motor Corporation in 1954. This methodology helps companies improve their work environment to increase efficiency.
This approach aims to standardize production procedures, making them predictable, repeatable, and easily measurable. This means that daily tasks such as cleaning and sorting, storage, packing, labeling, and packaging are possible. Because workers know what they can expect, this helps them perform their jobs more efficiently.
Five steps are required to implement 5S: Sort, Set In Order, Standardize. Separate. Each step requires a different action to increase efficiency. You can make it easy for people to find things later by sorting them. Once you have placed items in an ordered fashion, you will put them together. You then organize your inventory in groups. Make sure everything is correctly labeled when you label your containers.
Employees need to reflect on how they do their jobs. Employees must be able to see why they do what they do and find a way to achieve them without having to rely on their old methods. To be successful in the 5S system, employees will need to acquire new skills and techniques.
In addition to increasing efficiency, the 5S method also improves morale and teamwork among employees. Once they start to notice improvements, they are motivated to keep working towards their goal of increasing efficiency.