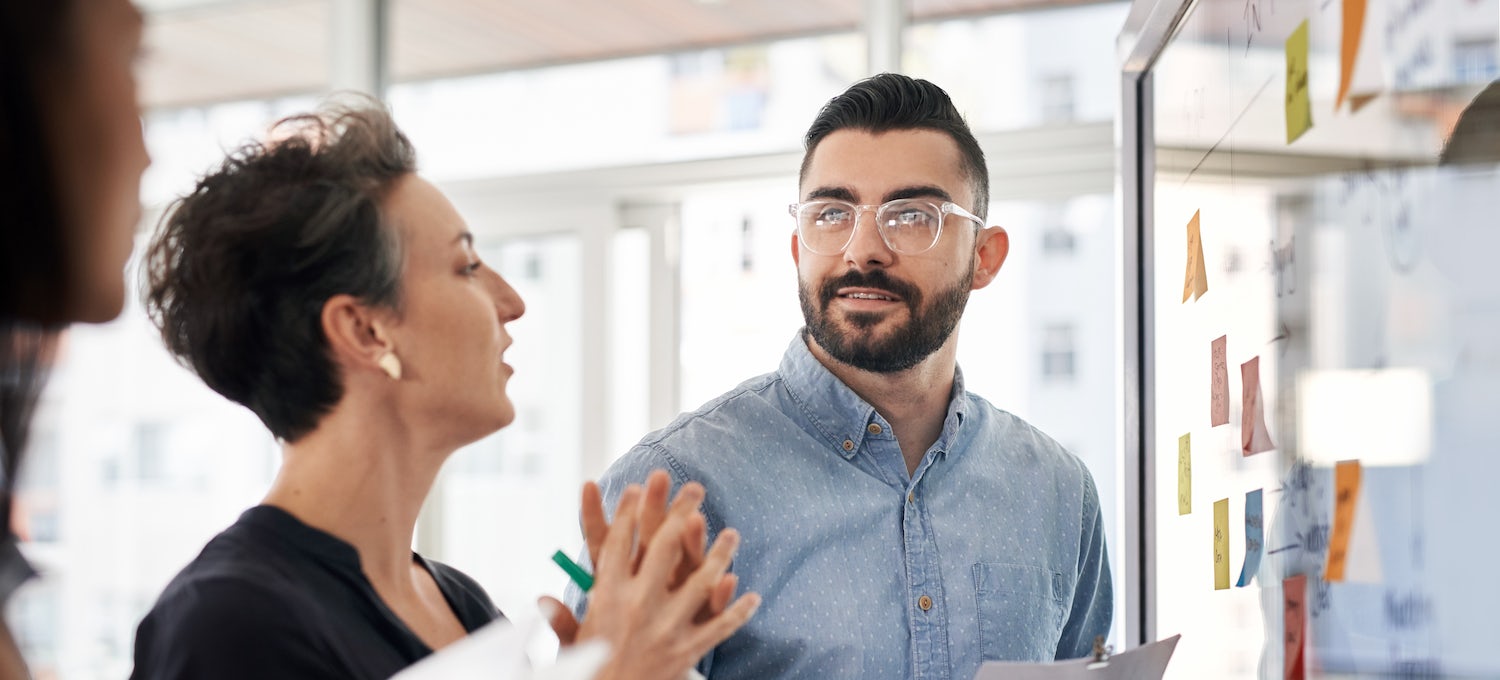
The job director of job manufacturing is similar to the job of a production associate. This article will explain the qualifications required to be a job director in manufacturing. This job requires a highly skilled workforce to complete various operations. A flexible workflow is essential as it helps to track development and manage projects. This production line is a high-skilled job that requires skilled workers who are able keep up with the pace of the production and deliver quality products in a timely manner.
The job of a job director in manufacturing
Job directors of manufacturing are responsible for overseeing the daily operations of a unit of manufacturing. They are responsible for ensuring products are produced on time and to a high level of quality. For a product to be created, a director for manufacturing must work closely alongside engineers and designers. Before a product goes into large-scale production, they have to assess its feasibility, market fit and impact on processes as well as quality. Also, a director in manufacturing must be able to demonstrate leadership skills. They should have the ability to supervise employees and make improvements to processes and equipment.
Typically, directors of manufacturing hold a bachelor's degree or higher. However, many employers prefer to hire candidates with advanced degrees. Directors of manufacturing should have at minimum five years' experience working in management. Candidates should be able and willing to learn quickly.
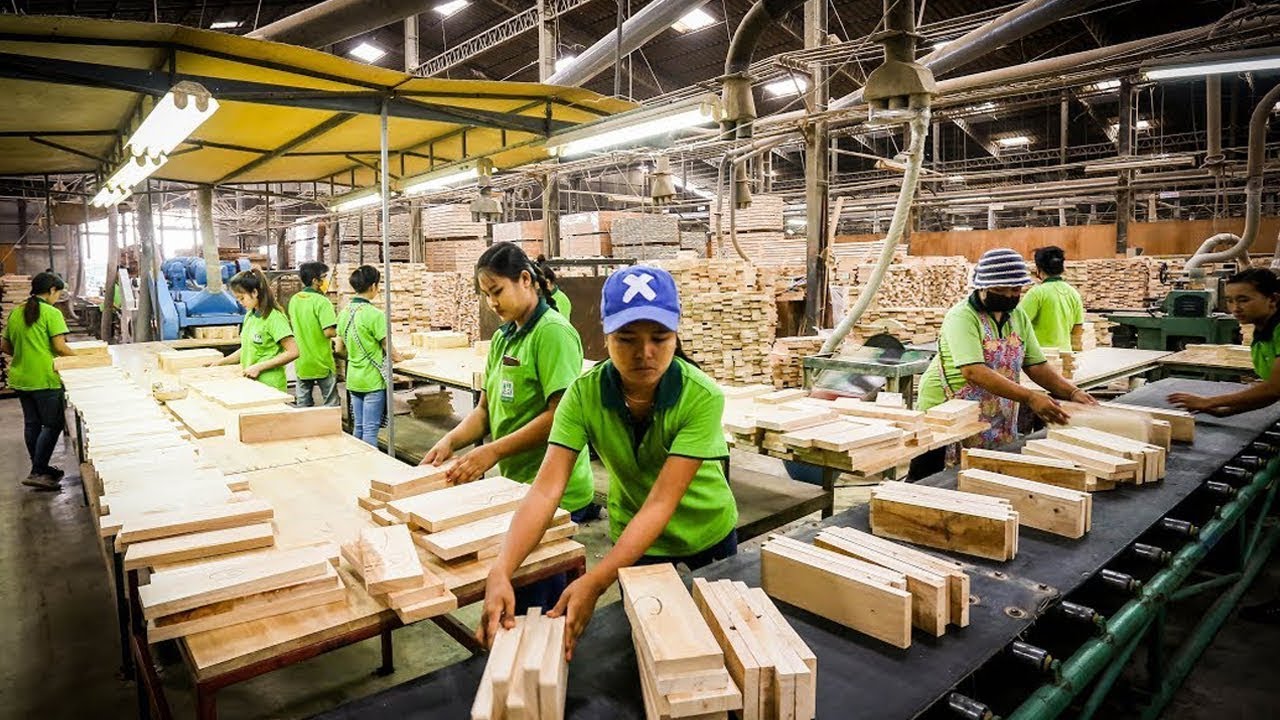
The duties of a manufacturing associate
Although the duties of a manufacturing associate are varied, they often involve repetitive motions and assembly line work. Associate must be able to use proper body mechanics and keep in good physical shape to avoid injury. They might also be required to lift heavy objects or stand for prolonged periods.
As a manufacturing associate, your duties could include reading engineering drawings and executing production documents. They need to coordinate with others on the team and produce reports. You will need to be organized, detail-oriented and good communicators.
Maintaining quality control over manufactured products is another major responsibility. They need to have an understanding of manufacturing processes and the ability to assess whether products meet company standards. They should also be able to inspect the finished product and spot any potential defects.
Qualifications required to become a job-director in manufacturing
Director of manufacturing is a job that requires you to manage all aspects of manufacturing operations, including scheduling and product production. In this role, you will need to maintain high standards of quality, as well as implementing and evaluating new ideas and techniques to cut costs. You will also have to evaluate the performance of your staff. You will need to have leadership skills and problem-solving abilities, as well as knowledge about manufacturing processes, in order to be a director of production.

You will be a manufacturing director and work closely with engineers and designers to create products and services. Excellent communication skills are essential to ensure that everyone in the company is on the right page and understands their respective roles. If you are able to communicate well, you will be able to effectively oversee the entire company. In addition, as a director of manufacturing, you will be expected to serve as a coach and mentor to employees under your supervision. For example, you will need to provide training to employees on safety protocols, risk mitigation, and new equipment.
FAQ
Why automate your warehouse
Modern warehouses are increasingly dependent on automation. The rise of e-commerce has led to increased demand for faster delivery times and more efficient processes.
Warehouses have to be flexible to meet changing requirements. They must invest heavily in technology to do this. Automating warehouses is a great way to save money. These are just a few reasons to invest in automation.
-
Increases throughput/productivity
-
Reduces errors
-
Improves accuracy
-
Safety increases
-
Eliminates bottlenecks
-
Allows companies scale more easily
-
Workers are more productive
-
It gives visibility to everything that happens inside the warehouse
-
Enhances customer experience
-
Improves employee satisfaction
-
Minimizes downtime and increases uptime
-
Ensures quality products are delivered on time
-
Eliminates human error
-
Assure compliance with regulations
What can I do to learn more about manufacturing?
You can learn the most about manufacturing by getting involved in it. You can read books, or watch instructional videos if you don't have the opportunity to do so.
What does it mean to warehouse?
A warehouse, or storage facility, is where goods are stored prior to being sold. It can be an outdoor or indoor area. In some cases, it may be a combination of both.
What does it take to run a logistics business?
To run a successful logistics company, you need a lot knowledge and skills. To communicate effectively with clients and suppliers, you must be able to communicate well. You need to understand how to analyze data and draw conclusions from it. You must be able to work well under pressure and handle stressful situations. You need to be innovative and creative to come up with new ways to increase efficiency. To motivate and guide your team towards reaching organizational goals, you must have strong leadership skills.
It is important to be organized and efficient in order to meet tight deadlines.
What is the role and responsibility of a Production Planner?
Production planners ensure all aspects of the project are delivered within time and budget. A production planner ensures that the service and product meet the client's expectations.
How can efficiency in manufacturing be improved?
First, we need to identify which factors are most critical in affecting production times. The next step is to identify the most important factors that affect production time. If you don’t know where to begin, consider which factors have the largest impact on production times. Once you identify them, look for solutions.
Why is logistics important in manufacturing?
Logistics are essential to any business. They enable you to achieve outstanding results by helping manage product flow from raw materials through to finished goods.
Logistics also play a major role in reducing costs and increasing efficiency.
Statistics
- According to the United Nations Industrial Development Organization (UNIDO), China is the top manufacturer worldwide by 2019 output, producing 28.7% of the total global manufacturing output, followed by the United States, Japan, Germany, and India.[52][53] (en.wikipedia.org)
- In 2021, an estimated 12.1 million Americans work in the manufacturing sector.6 (investopedia.com)
- Many factories witnessed a 30% increase in output due to the shift to electric motors. (en.wikipedia.org)
- In the United States, for example, manufacturing makes up 15% of the economic output. (twi-global.com)
- According to a Statista study, U.S. businesses spent $1.63 trillion on logistics in 2019, moving goods from origin to end user through various supply chain network segments. (netsuite.com)
External Links
How To
How to Use the 5S to Increase Productivity In Manufacturing
5S stands as "Sort", Set In Order", Standardize", Separate" and "Store". Toyota Motor Corporation invented the 5S strategy in 1954. It allows companies to improve their work environment, thereby achieving greater efficiency.
The basic idea behind this method is to standardize production processes, so they become repeatable, measurable, and predictable. It means tasks like cleaning, sorting or packing, labeling, and storing are done every day. These actions allow workers to perform their job more efficiently, knowing what to expect.
There are five steps that you need to follow in order to implement 5S. Each step has a different action and leads to higher efficiency. If you sort items, it makes them easier to find later. You arrange items by placing them in an order. Next, organize your inventory into categories and store them in containers that are easily accessible. You can also label your containers to ensure everything is properly labeled.
Employees must be able to critically examine their work practices. Employees must understand why they do certain tasks and decide if there's another way to accomplish them without relying on the old ways of doing things. They must learn new skills and techniques in order to implement the 5S system.
In addition to improving efficiency, the 5S system also increases morale and teamwork among employees. Once they start to notice improvements, they are motivated to keep working towards their goal of increasing efficiency.