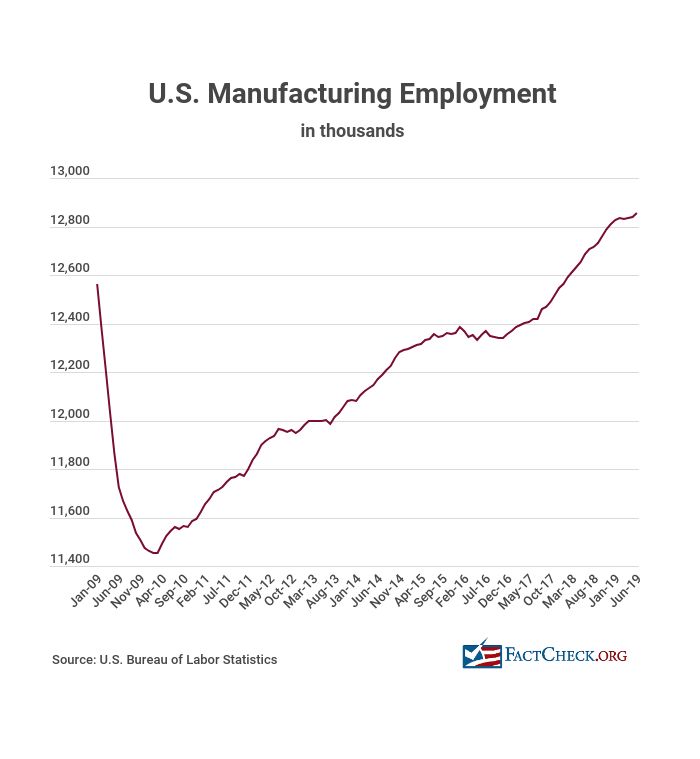
The location you work and the area you specialize will determine how much you can make as a material engineer. Apple, ConocoPhillips Meta, Western Digital, and Meta are among the top-paying companies. Others, such as FedEx and Motorola Solutions, can also be excellent places for a material engineer to work.
Materials engineers must understand the relationships between materials and processing methods. They must be able find the root causes of failures. In addition, they must be able to communicate engineering concepts to non-engineers. They also identify and implement cost-efficient operating strategies. They might also be required to communicate with suppliers or other professionals. Sometimes, they may be required to travel to foreign countries in order to collect samples for testing. In some cases, they may work more than 40 hours a week.
Materials engineers could also obtain advanced degrees. They may be able pursue a PhD degree in process engineering. They might also be eligible to teach or do research. Senior material engineers could be responsible for more management responsibilities. They may be eligible to conduct innovative research.
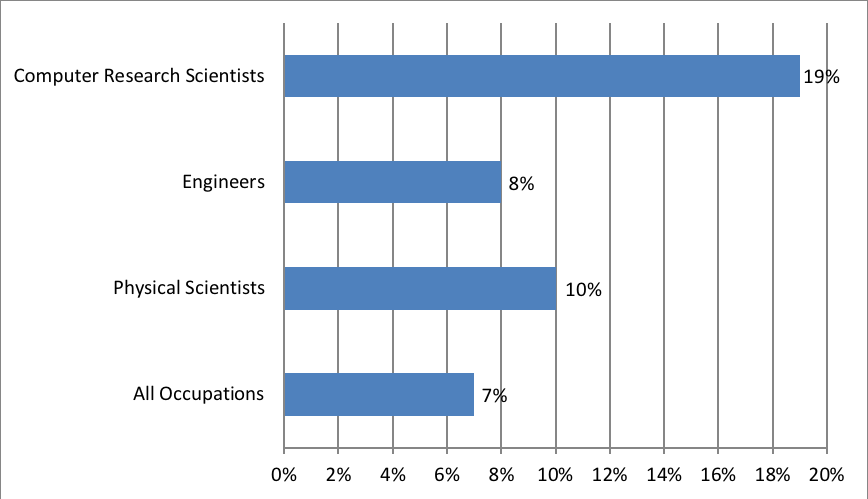
Materials engineers can work in offices or manufacturing plants. They may also travel to sites to collect samples for testing. The field is also very competitive, so it is important to stay on top of industry trends and innovations. They may also need to establish relationships with clients. They can support product engineers with green practices, and even help improve their products. This could lead to a strong reputation for their industry.
Materials engineers can also work in labs. They might use advanced math topics to design and troubleshoot. They might need to communicate engineering concepts clearly. They might also need to travel abroad to collect samples or observe how materials are used in manufacturing plants.
Technology companies such Apple and FedEx often employ materials engineers. They may also be employed by companies that manufacture metals and other materials, such as Raytheon Technologies. This field is extremely competitive and it may prove difficult to land a job at these companies. Engineer consulting firms may also offer opportunities to become material engineers. You may also have the opportunity to start your own business, which will allow you to stay at the forefront of your industry.
Material engineers might also need to work long hours. They might travel to work sites to collect samples or observe how materials are used in manufacturing plants. In addition, they may work more than 40 hours if they are working as a material engineer in a factory. Because of this, they will need to be able to work hard.
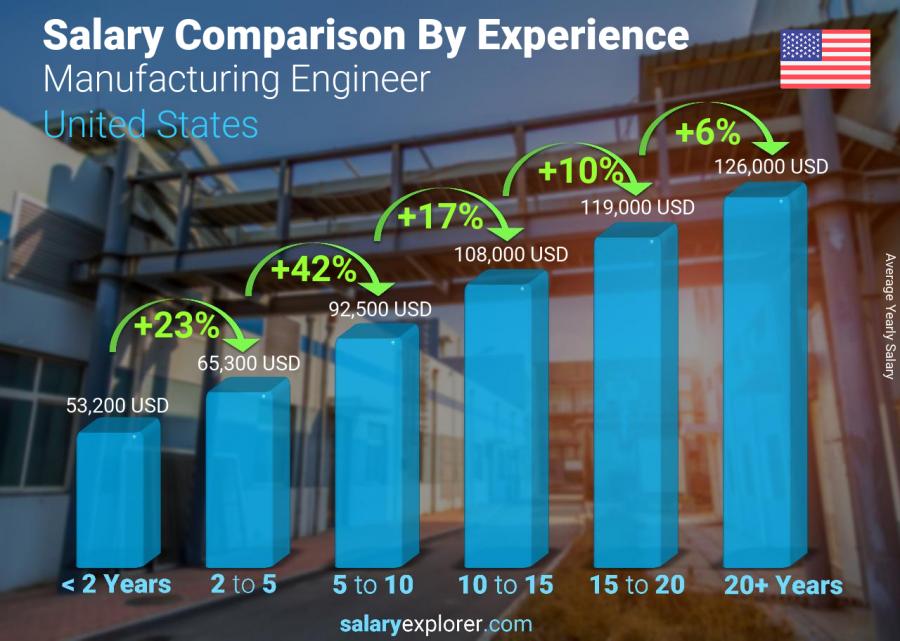
As a result, material engineers may need to work with a team. They may be required to communicate with suppliers, clients, and other professionals. In addition, they may be responsible for ensuring that budgets are met and that deadlines are met.
FAQ
Can we automate some parts of manufacturing?
Yes! Yes! Automation has existed since ancient times. The Egyptians invent the wheel thousands of year ago. Nowadays, we use robots for assembly lines.
There are many uses of robotics today in manufacturing. They include:
-
Robots for assembly line
-
Robot welding
-
Robot painting
-
Robotics inspection
-
Robots that create products
Manufacturing could also benefit from automation in other ways. 3D printing makes it possible to produce custom products in a matter of days or weeks.
What are the 7 Rs of logistics management?
The acronym 7Rs of Logistics refers to the seven core principles of logistics management. It was created by the International Association of Business Logisticians and published in 2004 under its "Seven Principles of Logistics Management".
The following letters form the acronym:
-
Responsible – ensure that all actions are legal and don't cause harm to anyone else.
-
Reliable - Have confidence in your ability to fulfill all of your commitments.
-
Reasonable - use resources efficiently and don't waste them.
-
Realistic – consider all aspects of operations, from cost-effectiveness to environmental impact.
-
Respectful - treat people fairly and equitably.
-
You are resourceful and look for ways to save money while increasing productivity.
-
Recognizable - Provide value-added services to customers
What are the four types of manufacturing?
Manufacturing is the process that transforms raw materials into useful products. It can involve many activities like designing, manufacturing, testing packaging, shipping, selling and servicing.
What is the responsibility for a logistics manager
Logistics managers ensure that goods arrive on time and are unharmed. This is done through his/her expertise and knowledge about the company's product range. He/she also needs to ensure adequate stock to meet demand.
Statistics
- According to the United Nations Industrial Development Organization (UNIDO), China is the top manufacturer worldwide by 2019 output, producing 28.7% of the total global manufacturing output, followed by the United States, Japan, Germany, and India.[52][53] (en.wikipedia.org)
- (2:04) MTO is a production technique wherein products are customized according to customer specifications, and production only starts after an order is received. (oracle.com)
- [54][55] These are the top 50 countries by the total value of manufacturing output in US dollars for its noted year according to World Bank.[56] (en.wikipedia.org)
- Many factories witnessed a 30% increase in output due to the shift to electric motors. (en.wikipedia.org)
- It's estimated that 10.8% of the U.S. GDP in 2020 was contributed to manufacturing. (investopedia.com)
External Links
How To
How to Use 5S to Increase Productivity in Manufacturing
5S stands for "Sort", 'Set In Order", 'Standardize', & Separate>. The 5S methodology was developed at Toyota Motor Corporation in 1954. It improves the work environment and helps companies to achieve greater efficiency.
The idea behind standardizing production processes is to make them repeatable and measurable. Cleaning, sorting and packing are all done daily. This knowledge allows workers to be more efficient in their work because they are aware of what to expect.
Five steps are required to implement 5S: Sort, Set In Order, Standardize. Separate. Each step involves a different action which leads to increased efficiency. By sorting, for example, you make it easy to find the items later. When you set items in an order, you put items together. You then organize your inventory in groups. Make sure everything is correctly labeled when you label your containers.
Employees will need to be more critical about their work. Employees need to be able understand their motivations and discover alternative ways to do them. In order to use the 5S system effectively, they must be able to learn new skills.
In addition to increasing efficiency, the 5S method also improves morale and teamwork among employees. As they begin to see improvements, they feel motivated to continue working towards the goal of achieving higher levels of efficiency.