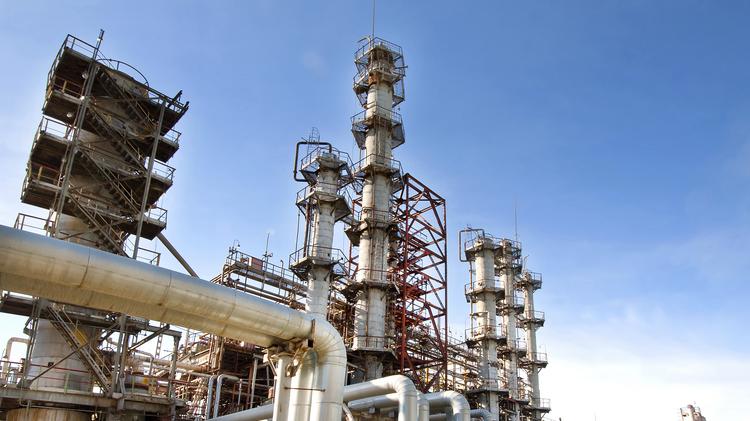
Lean to Agile can help reduce waste and improve team productivity. It emphasizes prioritizing work and eliminating waste. While empowering scrummasters and teams to do all the rest, it also focuses on prioritizing work. Also, agile teams should be empowered as product owners as well as servant leaders committed to the success and growth of their projects.
Time-to-market
The time it takes for a product to be fully released is one of its most important indicators of success. The faster you can capture market share, revenue and profits, the shorter it is. Companies need to know their development processes, and how they use them. They can then refine their processes to achieve their goals and use their capabilities to increase time-to-market.
Outsourcing can be used to speed up the time it takes to bring a product to market. It is possible to cut down on time by creating an ecosystem of reliable support partners. This will help you reduce risk and to share your resources.
Iteration
Iteration is an important element in agile software development. The concept emphasizes the importance of small, measurable steps that can be evaluated and tested sooner than a full process. The chances of success are greater for features that are more detailed. It is not always easy to do. An iteration's final product should be available and running. It must be integrated, tested and deployed on an internal server.
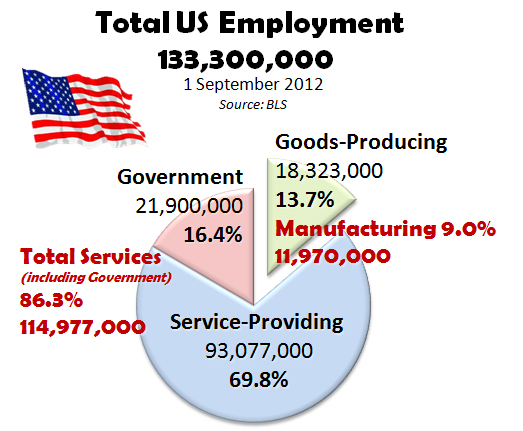
Iterations enable teams to review their backlog and resolve risks and issues that weren't previously discovered. The aim is to make each iteration better than the one before. Developers may refactor or add new features to existing features. This process is repeated until the product is ready to be released.
Collaborative processes
Agile Manifesto stresses the importance of collaboration between developers and business stakeholders. This allows teams prioritize work based off business goals. Lean processes also promote a value stream - the end-to-end list of actions that produce the product or service customers desire. Both approaches can be described as similar, but there are important differences.
Agile is more flexible that Lean. Lean UX teams don't use large, rigid tools for project management. Instead, they work as a team, scale up quickly and collaborate to achieve a goal. Agile is a system which consists of small-world networks, deliverables, and other elements. Agile also emphasizes autonomy and exploration as well as collaboration. An agile approach is required for scaling from one project to multiple projects.
Implementing user research into agile groups
Agile teams increasingly incorporate user research into their work processes. This mindset is becoming more common in product development. However, it's also spreading to other areas. Teams are realizing that flexible and rapid research is essential as usability and experience become more important. Agile teams employ agile mindsets to search for processes that can be connected to the product's backlog in order get user-centric, user-centric development.
It is important that user research workflows be made easier and more accessible. This means creating repeatable user research templates that non-practitioners can easily use to run tests. These templates should include the most important questions as well as cover all stages of product creation. UX platforms, which offer preloaded templates or automated workflows, can help teams ensure consistent results.

Creation of value
The concept of value creation is somewhat odd, even if it makes sense. While creating value can be accomplished with a narrow scope or a larger one, it cannot be entirely binary. In some cases, a smaller scope produces less value and a greater scope generates more. Still, the concept of a full scope can be useful.
Lean and agile are two different ways to deliver a better product to customers. Combining both these methods can help companies deliver a superior product quicker. They also minimize process overhead by empowering employees to work together and focus on the needs of the customer.
FAQ
What does it mean to warehouse?
Warehouses and storage facilities are where goods are kept before being sold. It can be either an indoor or outdoor space. It may also be an indoor space or an outdoor area.
What does manufacturing mean?
Manufacturing Industries is a group of businesses that produce goods for sale. Consumers are people who purchase these goods. This is accomplished by using a variety of processes, including production, distribution and retailing. They create goods from raw materials, using machines and various other equipment. This includes all types of manufactured goods, including food items, clothing, building supplies, furniture, toys, electronics, tools, machinery, vehicles, pharmaceuticals, medical devices, chemicals, and many others.
How does manufacturing avoid bottlenecks in production?
You can avoid bottlenecks in production by making sure that everything runs smoothly throughout the production cycle, from the moment you receive an order to the moment the product is shipped.
This includes planning to meet capacity requirements and quality control.
Continuous improvement techniques like Six Sigma are the best way to achieve this.
Six Sigma Management System is a method to increase quality and reduce waste throughout your organization.
It focuses on eliminating variation and creating consistency in your work.
How can manufacturing efficiency be improved?
First, identify the factors that affect production time. We then need to figure out how to improve these variables. If you don’t know where to begin, consider which factors have the largest impact on production times. Once you've identified them, try to find solutions for each of those factors.
How does a production planner differ from a project manager?
The major difference between a Production Planner and a Project Manager is that a Project Manager is often the person responsible for organizing and planning the entire project. While a Production Planner is involved mainly in the planning stage,
What skills do production planners need?
A production planner must be organized, flexible, and able multitask to succeed. Also, you must be able and willing to communicate with clients and coworkers.
Statistics
- Many factories witnessed a 30% increase in output due to the shift to electric motors. (en.wikipedia.org)
- [54][55] These are the top 50 countries by the total value of manufacturing output in US dollars for its noted year according to World Bank.[56] (en.wikipedia.org)
- According to a Statista study, U.S. businesses spent $1.63 trillion on logistics in 2019, moving goods from origin to end user through various supply chain network segments. (netsuite.com)
- You can multiply the result by 100 to get the total percent of monthly overhead. (investopedia.com)
- Job #1 is delivering the ordered product according to specifications: color, size, brand, and quantity. (netsuite.com)
External Links
How To
How to Use 5S for Increasing Productivity in Manufacturing
5S stands as "Sort", Set In Order", Standardize", Separate" and "Store". Toyota Motor Corporation developed the 5S method in 1954. It improves the work environment and helps companies to achieve greater efficiency.
The basic idea behind this method is to standardize production processes, so they become repeatable, measurable, and predictable. It means tasks like cleaning, sorting or packing, labeling, and storing are done every day. Workers can be more productive by knowing what to expect.
Implementing 5S requires five steps. These are Sort, Set In Order, Standardize. Separate. And Store. Each step requires a different action to increase efficiency. For example, when you sort things, you make them easy to find later. You arrange items by placing them in an order. Once you have separated your inventory into groups and organized them, you will store these groups in easily accessible containers. Labeling your containers will ensure that everything is correctly labeled.
Employees need to reflect on how they do their jobs. Employees must understand why they do certain tasks and decide if there's another way to accomplish them without relying on the old ways of doing things. To implement the 5S system, employees must acquire new skills and techniques.
In addition to improving efficiency, the 5S system also increases morale and teamwork among employees. They are more motivated to achieve higher efficiency levels as they start to see improvement.