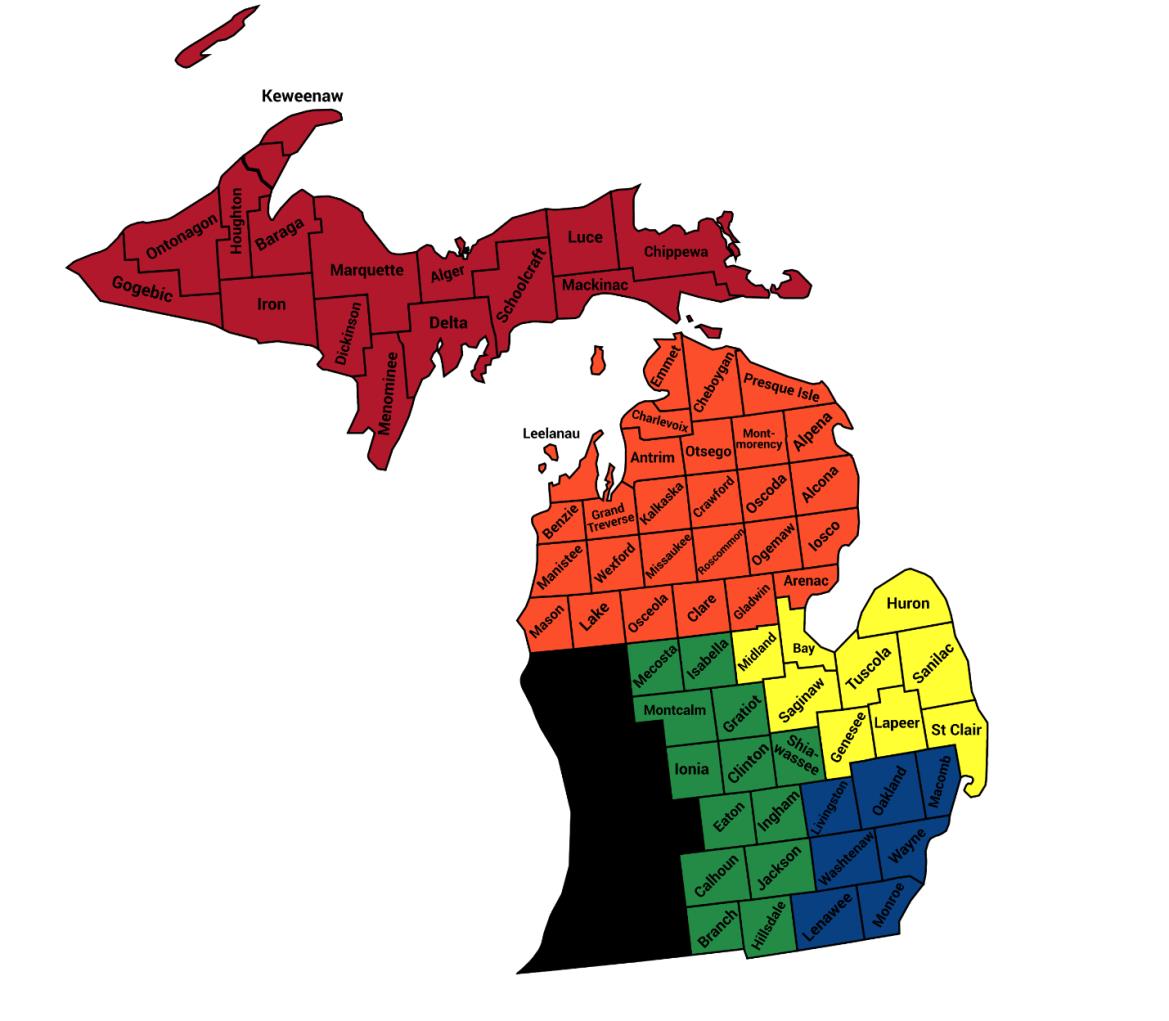
Both individuals and businesses can find a wide range of employment opportunities in the industry. Due to the fact that many employers prefer using outside agencies to screen prospective employees, the employment sector is expected to continue growing. Many of these agencies work online, which reduces their administrative overhead and staffing requirements. However, they are not immune to competition from job postings posted on employer Web sites and job-matching Internet sites operated by professional associations and educational institutions.
Jobs in the employment service industry
There are many occupations in the employment services industry. These professionals are specialized in different areas, such as recruiting, placement, and executive search. They also provide temporary workers for clients. These professionals are also able to provide human resources services. Companies located in different regions of the world dominate employment services.
Millions of people work in this industry, with many different educations, skills, and experience. Occupations range from secretary to computer systems analyst, and from general laborer to nurse. Some of the jobs in the industry are permanent, such as employment interviewers, marketing representatives, and office managers.
Labor market
The labor market is the place where supply and demand meet. Employees provide services to employers, and the employer pays them for these services. The worker could be an individual, or an organization. The employer could be anyone looking for a worker. In this way, workers and employers are like sellers and buyers.
The federal government has several statistical agencies that collect data on the labor market. For example, the Bureau of Labor Statistics collects and analyses data on unemployment, wages, and employment. It also analyzes data regarding industrial relations, occupational safety, family expenditure, and other related topics. These data are useful for economists to understand trends in labor markets.
Industry size
The number of workers in an industry defines its size. There are approximately 6.1 million employers in the United States. Large companies are the biggest employers. Small businesses employ fewer people. According to the U.S. Census Bureau 99.7% percent of total businesses are smaller than 500 employees. Even though smaller industries may not employ a lot of people, they could be able to create new jobs.
Industry's impact on recession
When the economy is in recession, the employment industry will experience a decline in numbers of workers. As a result, unemployment rates will increase. In turn, unemployment rates will rise. Although every sector will see job losses, the extent of those losses will vary. Throughout the Great Recession, every sector lost jobs, but the magnitudes of job losses were different for different sectors.
The resulting reductions in payroll will be reflected in the premium. This will cause a 1% rise in premiums in the Mild recession scenario. In the case of the Severe recession, the increase will be larger. The decline in payrolls for Goods & Services has been about half that of other industries. As a result, the premiums for Goods & Services will increase.
Impact of COVID-19 pandemic (coronavirus), on the industrial sector
Most of the COVID-19 coronavirus pandemic's impact on the employment market was felt in industries with a large older workforce. Professional and commercial services were home to the greatest number of job losses. They were followed closely by healthcare and social assistance. Job losses were higher among younger workers, but not by a disproportionately large amount. Younger workers were likely to be in industries with more face-to-face contact.
Both high- and low-paying industries were affected by the pandemic. While many workers lost their jobs as a result of the virus's spread, the number of those in these industries was lower than other sectors. Many information and management workers were able to work remotely, which allowed them to recover the majority of their jobs. Higher-paying jobs suffered the most from the recession. In the second quarter of 2019, the number of people working in those sectors was 15% lower than in the same period in 2018.
FAQ
What are the main products of logistics?
Logistics is the process of moving goods from one point to another.
They encompass all aspects transport, including packaging and loading, transporting, storage, unloading.
Logisticians ensure that the product is delivered to the correct place, at the right time, and under safe conditions. Logisticians help companies improve their supply chain efficiency by providing information about demand forecasts and stock levels, production schedules, as well as availability of raw materials.
They also keep track of shipments in transit, monitor quality standards, perform inventories and order replenishment, coordinate with suppliers and vendors, and provide support services for sales and marketing.
What is the responsibility for a logistics manager
Logistics managers make sure all goods are delivered on schedule and without damage. This is done through his/her expertise and knowledge about the company's product range. He/she should make sure that enough stock is on hand to meet the demands.
What is the difference between Production Planning and Scheduling?
Production Planning (PP) is the process of determining what needs to be produced at any given point in time. This is done through forecasting demand and identifying production capacities.
Scheduling refers to the process of allocating specific dates to tasks in order that they can be completed within a specified timeframe.
What jobs are available in logistics?
There are different kinds of jobs available in logistics. Here are some examples:
-
Warehouse workers - They load and unload trucks and pallets.
-
Transportation drivers - They drive trucks and trailers to deliver goods and carry out pick-ups.
-
Freight handlers - They sort and pack freight in warehouses.
-
Inventory managers - These are responsible for overseeing the stock of goods in warehouses.
-
Sales representatives: They sell products to customers.
-
Logistics coordinators are responsible for organizing and planning logistics operations.
-
Purchasing agents: They are responsible for purchasing goods and services to support company operations.
-
Customer service representatives - They answer calls and emails from customers.
-
Shippers clerks - They process shipping order and issue bills.
-
Order fillers – They fill orders based upon what was ordered and shipped.
-
Quality control inspectors (QCI) - They inspect all incoming and departing products for potential defects.
-
Other - Logistics has many other job opportunities, including transportation supervisors, logistics specialists, and cargo specialists.
What skills should a production planner have?
Being a production planner is not easy. You need to be organized and flexible. Also, you must be able and willing to communicate with clients and coworkers.
Do we need to know about Manufacturing Processes before learning about Logistics?
No. It doesn't matter if you don't know anything about manufacturing before you learn about logistics. But, being familiar with manufacturing processes will give you a better understanding about how logistics works.
What are the four types of manufacturing?
Manufacturing is the process by which raw materials are transformed into useful products through machines and processes. Manufacturing can include many activities such as designing and building, testing, packaging shipping, selling, servicing, and other related activities.
Statistics
- (2:04) MTO is a production technique wherein products are customized according to customer specifications, and production only starts after an order is received. (oracle.com)
- According to the United Nations Industrial Development Organization (UNIDO), China is the top manufacturer worldwide by 2019 output, producing 28.7% of the total global manufacturing output, followed by the United States, Japan, Germany, and India.[52][53] (en.wikipedia.org)
- Many factories witnessed a 30% increase in output due to the shift to electric motors. (en.wikipedia.org)
- [54][55] These are the top 50 countries by the total value of manufacturing output in US dollars for its noted year according to World Bank.[56] (en.wikipedia.org)
- According to a Statista study, U.S. businesses spent $1.63 trillion on logistics in 2019, moving goods from origin to end user through various supply chain network segments. (netsuite.com)
External Links
How To
How to use 5S to increase Productivity in Manufacturing
5S stands as "Sort", Set In Order", Standardize", Separate" and "Store". Toyota Motor Corporation invented the 5S strategy in 1954. This methodology helps companies improve their work environment to increase efficiency.
This method aims to standardize production processes so that they are repeatable, measurable and predictable. This means that tasks such as cleaning, sorting, storing, packing, and labeling are performed daily. These actions allow workers to perform their job more efficiently, knowing what to expect.
There are five steps to implementing 5S, including Sort, Set In Order, Standardize, Separate and Store. Each step requires a different action, which increases efficiency. Sorting things makes it easier to find them later. You arrange items by placing them in an order. After you have divided your inventory into groups you can store them in easy-to-reach containers. Make sure everything is correctly labeled when you label your containers.
Employees need to reflect on how they do their jobs. Employees need to be able understand their motivations and discover alternative ways to do them. They will need to develop new skills and techniques in order for the 5S system to be implemented.
In addition to increasing efficiency, the 5S method also improves morale and teamwork among employees. Once they start to notice improvements, they are motivated to keep working towards their goal of increasing efficiency.