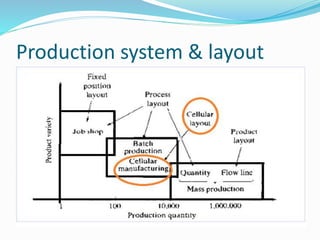
BLS Mechanical engineers are highly sought-after professionals who have extensive engineering knowledge and education. A BLS Mechanical Engineer is highly skilled and has a strong educational background. They are also highly qualified to serve as managers and team leaders. This career path has a positive outlook with a 7 percent increase in positions available by 2030. That equates to another 20,900 jobs on the job market. Candidats must have experience in computer-aided design and simulation software. They also need to be knowledgeable about specialized software and simulation.
Job duties
A mechanical engineer's job involves designing, developing, and planning equipment that produces or uses electricity. These engineers may also have to oversee the operation, maintenance and repair of machines. These professionals may work for large engineering firms or independently as consultants. They may also design refrigeration systems for frozen foods or air-conditioning systems for buildings. The data on the wages and employment of mechanical engineers is provided below.
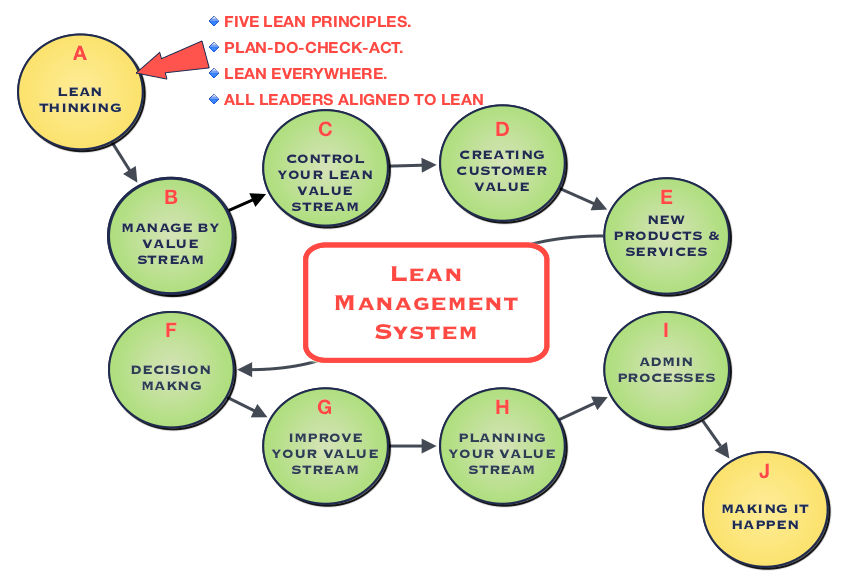
Entry-level mechanical engineers typically work in an office environment, but may also travel to the site of a construction project to work on an equipment problem. A strong grasp of basic business principles is essential for this entry-level job. Also, mechanical engineers will often use computers, so it is important to have an understanding of computer science. It is also advantageous to have strong tech skills for integrating sensors in machinery and analysing designs.
Education required
A Bachelor of Science in Mechanical Engineering degree (BSME), may be a great way of getting into mechanical engineering. This degree typically lasts four years and covers the fundamentals of design, testing, manufacturing, and other aspects. Computer software is also taught to students to create drawings and other designs. The BSME program will allow you to pursue a career in this field.
The BLS predicts a positive outlook in this field. BLS predicts that mechanical engineers will see a 4 percentage increase in employment between 2019-2029. Some engineers will be able take on higher management or become faculty in research and education programs. This job earns the average $84,190 salary. In the United States, mechanical engineers will see employment opportunities that are better than average in the next decade.
Salary
According to the U.S. Bureau of Labor Statistics (USBLS), the number of mechanical engineers is expected to grow by 5 percent between 2012-2022. This is a slower growth than the average of all occupations, but still very impressive. Those who stay on top of the latest technological advances will stand to benefit in a competitive job market. But, there are many factors that could affect the pay of a mechanical engineer.
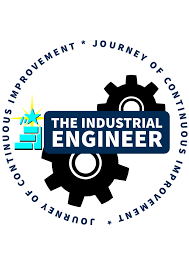
There are many factors that influence the salary of mechanical engineers, but mechanical engineers tend to make more than other engineers. The top 10 percent made more than $126,000.430 per annum. The highest salaries for mechanical engineers are not only possible but so is a career as a computer and electronic product manufacturer. California, New Mexico, and Alaska have the highest salaries currently for mechanical engineers. These states are ranked according to their wages, which vary depending on education and experience.
FAQ
What does warehouse refer to?
A warehouse is a place where goods are stored until they are sold. It can be an outdoor or indoor area. In some cases it could be both indoors and outdoors.
How can overproduction in manufacturing be reduced?
Better inventory management is key to reducing excess production. This would reduce the time needed to manage inventory. By doing this, we could free up resources for other productive tasks.
This can be done by using a Kanban system. A Kanban board can be used to monitor work progress. In a Kanban system, work items move through a sequence of states until they reach their final destination. Each state represents a different priority level.
For instance, when work moves from one stage to another, the current task is complete enough to be moved to the next stage. However, if a task is still at the beginning stages, it will remain so until it reaches the end of the process.
This allows for work to continue moving forward, while also ensuring that there is no work left behind. With a Kanban board, managers can see exactly how much work is being done at any given moment. This allows them to adjust their workflows based on real-time information.
Lean manufacturing, another method to control inventory levels, is also an option. Lean manufacturing emphasizes eliminating waste in all phases of production. Any product that isn't adding value can be considered waste. Here are some examples of common types.
-
Overproduction
-
Inventory
-
Unnecessary packaging
-
Materials in excess
Manufacturers can reduce their costs and improve their efficiency by using these ideas.
How is a production manager different from a producer planner?
A production planner is more involved in the planning phase of the project than a project manger.
Statistics
- [54][55] These are the top 50 countries by the total value of manufacturing output in US dollars for its noted year according to World Bank.[56] (en.wikipedia.org)
- Many factories witnessed a 30% increase in output due to the shift to electric motors. (en.wikipedia.org)
- In the United States, for example, manufacturing makes up 15% of the economic output. (twi-global.com)
- (2:04) MTO is a production technique wherein products are customized according to customer specifications, and production only starts after an order is received. (oracle.com)
- According to a Statista study, U.S. businesses spent $1.63 trillion on logistics in 2019, moving goods from origin to end user through various supply chain network segments. (netsuite.com)
External Links
How To
How to Use Lean Manufacturing for the Production of Goods
Lean manufacturing (or lean manufacturing) is a style of management that aims to increase efficiency, reduce waste and improve performance through continuous improvement. It was developed by Taiichi Okono in Japan, during the 1970s & 1980s. TPS founder Kanji Takoda awarded him the Toyota Production System Award (TPS). The first book published on lean manufacturing was titled "The Machine That Changed the World" written by Michael L. Watkins and published in 1990.
Lean manufacturing refers to a set of principles that improve the quality, speed and costs of products and services. It is about eliminating defects and waste from all stages of the value stream. The five-steps of Lean Manufacturing are just-in time (JIT), zero defect and total productive maintenance (TPM), as well as 5S. Lean manufacturing focuses on eliminating non-value-added activities such as rework, inspection, and waiting.
Lean manufacturing improves product quality and costs. It also helps companies reach their goals quicker and decreases employee turnover. Lean manufacturing is a great way to manage the entire value chain including customers, suppliers, distributors and retailers as well as employees. Lean manufacturing is widely practiced in many industries around the world. Toyota's philosophy, for example, is what has enabled it to be successful in electronics, automobiles, medical devices, healthcare and chemical engineering as well as paper and food.
Five basic principles of Lean Manufacturing are included in lean manufacturing
-
Define Value: Identify the social value of your business and what sets you apart.
-
Reduce Waste - Eliminate any activity that doesn't add value along the supply chain.
-
Create Flow: Ensure that the work process flows without interruptions.
-
Standardize and Simplify – Make processes as consistent, repeatable, and as simple as possible.
-
Develop Relationships: Establish personal relationships both with internal and external stakeholders.
Lean manufacturing is not a new concept, but it has been gaining popularity over the last few years due to a renewed interest in the economy following the global financial crisis of 2008. To increase their competitiveness, many businesses have turned to lean manufacturing. In fact, some economists believe that lean manufacturing will be an important factor in economic recovery.
Lean manufacturing has many benefits in the automotive sector. These include improved customer satisfaction, reduced inventory levels, lower operating costs, increased productivity, and better overall safety.
Lean manufacturing can be applied to almost every aspect of an organization. However, it is particularly useful when applied to the production side of an organization because it ensures that all steps in the value chain are efficient and effective.
There are three types principally of lean manufacturing:
-
Just-in-Time Manufacturing: Also known as "pull systems", this type of lean manufacturing uses just-in-time manufacturing (JIT). JIT stands for a system where components are assembled on the spot rather than being made in advance. This method reduces lead times, increases availability, and decreases inventory.
-
Zero Defects Manufacturing, (ZDM): ZDM is focused on ensuring that no defective products leave the manufacturing facility. If a part needs to be fixed during the assembly line, it should be repaired rather than scrapped. This is true even for finished products that only require minor repairs prior to shipping.
-
Continuous Improvement: Continuous Improvement aims to improve efficiency by continually identifying problems and making adjustments to eliminate or minimize waste. It involves continuous improvement of processes, people, and tools.