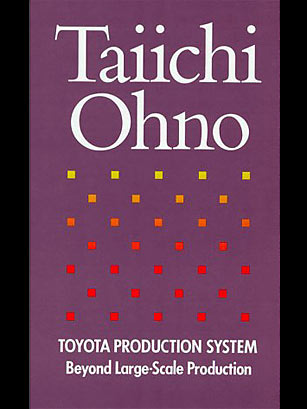
As a logistics coordinator, you will ensure that the goods arrive at the destination they are supposed to be. In this field, you'll ensure that goods are delivered efficiently to your customer's door. This article will provide more information about logistics. Learn about the roles of a customer service specialist and inventory analyst as well as a supply chain manager. Here are some of the most important jobs you will find in logistics.
Logistics coordinator
Monster offers thousands of opportunities to find logistics coordinator jobs. This type of job requires a lot of hands-on training. Candidates with minimal experience can usually take up training through an internship or apprenticeship, although they may also need to have some industry experience. A job as a logistic coordinator is a good option if you have extensive experience in logistics.
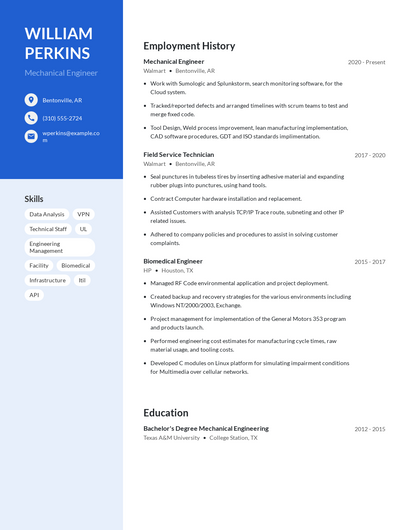
Customer service specialist
The customer service specialist manages and delivers customer service. They interact with customers on a daily basis, coordinate inland transportation, resolve customer complaints, and help them to resolve any issues. They manage customer relationships and also coordinate appointments, record special service requirements, and schedule transportation, warehousing and other activities. As a customer support specialist, you will also coordinate all necessary documents and documentation to ensure timely and affordable delivery.
Inventory analyst
An Inventory Analyst oversees overall inventory productivity and maintenance of service level. Their primary responsibilities include order fulfillment for TSC Feed programmes, as well managing the day to day activities of inventory replenishment. They manage inventory levels for their respective product categories to support assortment and merchandise planning. They monitor trends and make plans for article-site replenishment. They may also assist with marketing and promotional activities. They are often in charge of analyzing sales data and creating new strategies to enhance business efficiency.
Supply chain manager
A supply chain manager is responsible for managing the movement of materials and goods between suppliers and customers. This role requires a broad range of skills. Typically, a bachelor's degree in business administration is required. Employers prefer candidates with master's degrees. There are various ways to qualify for a supply chain manager job. Find out more about this career field. A business administration associate's degree is a good starting point if you want to work in supply chain management.
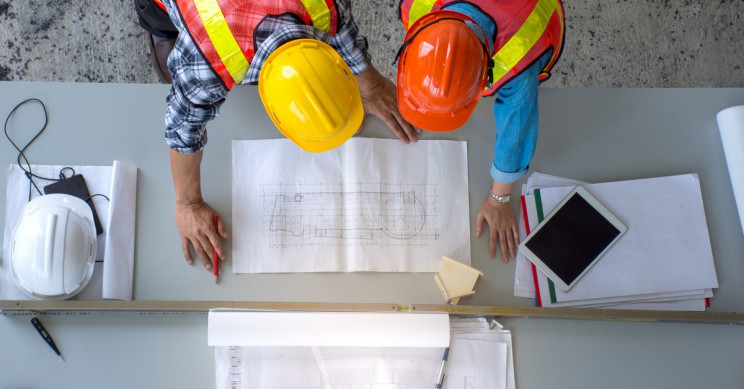
Freight agent
While you're creating your job description, make sure to include a section on your cargo and freight agent responsibilities. The job description should contain a list of the key responsibilities of this position, so that potential applicants can easily see what they need to do on a daily basis. Make sure to use strong action verbs in your description to get the attention of qualified applicants. It is important to include in the job description a list detailing all qualifications needed for this position.
FAQ
What does it mean to warehouse?
Warehouses and storage facilities are where goods are kept before being sold. It can be an outdoor or indoor area. Sometimes, it can be both an indoor and outdoor space.
What are the requirements to start a logistics business?
To be a successful businessman in logistics, you will need many skills and knowledge. For clients and suppliers to be successful, you need to have excellent communication skills. You need to understand how to analyze data and draw conclusions from it. You will need to be able handle pressure well and work in stressful situations. To increase efficiency and creativity, you need to be creative. You will need strong leadership skills to motivate and direct your team members towards achieving their organizational goals.
It is important to be organized and efficient in order to meet tight deadlines.
What are the goods of logistics?
Logistics is the process of moving goods from one point to another.
They encompass all aspects transport, including packaging and loading, transporting, storage, unloading.
Logisticians make sure that the right product arrives at the right place at the correct time and in safe conditions. They provide information on demand forecasts as well stock levels, production schedules and availability of raw material.
They can also track shipments in transit and monitor quality standards.
Statistics
- You can multiply the result by 100 to get the total percent of monthly overhead. (investopedia.com)
- According to a Statista study, U.S. businesses spent $1.63 trillion on logistics in 2019, moving goods from origin to end user through various supply chain network segments. (netsuite.com)
- In the United States, for example, manufacturing makes up 15% of the economic output. (twi-global.com)
- In 2021, an estimated 12.1 million Americans work in the manufacturing sector.6 (investopedia.com)
- [54][55] These are the top 50 countries by the total value of manufacturing output in US dollars for its noted year according to World Bank.[56] (en.wikipedia.org)
External Links
How To
How to use the Just In-Time Production Method
Just-in-time (JIT) is a method that is used to reduce costs and maximize efficiency in business processes. This is where you have the right resources at the right time. This means you only pay what you use. Frederick Taylor first coined this term while working in the early 1900s as a foreman. He observed how workers were paid overtime if there were delays in their work. He decided to ensure workers have enough time to do their jobs before starting work to improve productivity.
JIT is a way to plan ahead and make sure you don't waste any money. The entire project should be looked at from start to finish. You need to ensure you have enough resources to tackle any issues that might arise. You'll be prepared to handle any potential problems if you know in advance. This way, you won't end up paying extra money for things that weren't really necessary.
There are many JIT methods.
-
Demand-driven: This JIT is where you place regular orders for the parts/materials that are needed for your project. This will enable you to keep track of how much material is left after you use it. This will allow you to calculate how long it will take to make more.
-
Inventory-based : You can stock the materials you need in advance. This allows you predict the amount you can expect to sell.
-
Project-driven: This is an approach where you set aside enough funds to cover the cost of your project. When you know how much you need, you'll purchase the appropriate amount of materials.
-
Resource-based JIT : This is probably the most popular type of JIT. You assign certain resources based off demand. You might assign more people to help with orders if there are many. If you don't receive many orders, then you'll assign fewer employees to handle the load.
-
Cost-based : This is similar in concept to resource-based. But here, you aren't concerned about how many people your company has but how much each individual costs.
-
Price-based: This is a variant of cost-based. However, instead of focusing on the individual workers' costs, this looks at the total price of the company.
-
Material-based: This approach is similar to cost-based. However, instead of looking at the total cost for the company, you look at how much you spend on average on raw materials.
-
Time-based: Another variation of resource-based JIT. Instead of focusing on how much each employee costs, you focus on how long it takes to complete the project.
-
Quality-based JIT is another variant of resource-based JIT. Instead of worrying about the costs of each employee or how long it takes for something to be made, you should think about how quality your product is.
-
Value-based JIT is the newest form of JIT. In this scenario, you're not concerned about how products perform or whether customers expect them to meet their expectations. Instead, your goal is to add value to the market.
-
Stock-based: This is an inventory-based method that focuses on the actual number of items being produced at any given time. This method is useful when you want to increase production while decreasing inventory.
-
Just-in-time planning (JIT): This is a combination JIT and supply-chain management. It's the process of scheduling delivery of components immediately after they are ordered. This is important as it reduces lead time and increases throughput.