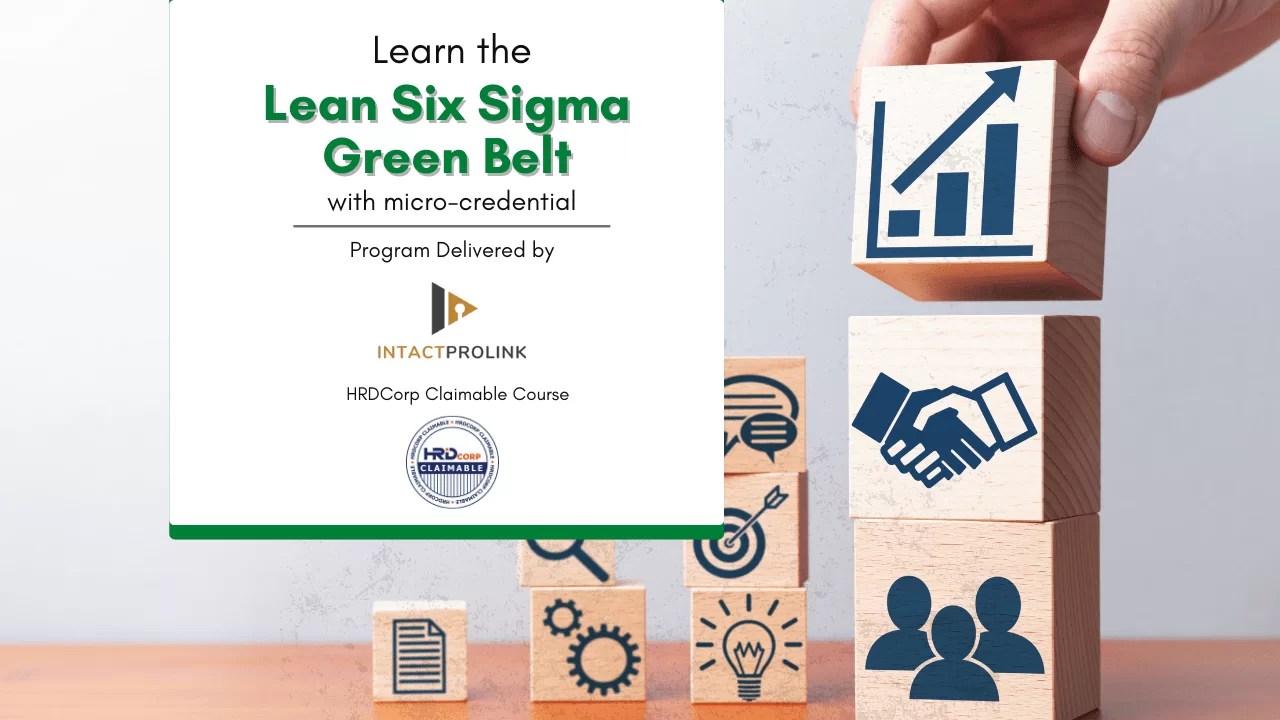
Several factors have caused a massive chip shortage in recent years. These include transportation issues and manufacturing problems. A number of disasters have led to the shut down of chip plants. This has affected consumer devices like gaming consoles, medical devices, and data centres. However, there are several efforts being made by the Chinese government to promote semiconductor manufacturing in the country. The government has even introduced an investment fund to help chip makers.
China's chip industry has seen remarkable improvements over the past several years as a result. According to IC Insights chip production in China will grow by 19.4% between 2025 and 2025, according to the company. The industry has much to do before it can reach its former heights. Despite these achievements, the number domestic chip companies remains small. Many of these companies do not yet have their own independent business.
Huawei, Oppo and Midea are some of China's most well-known chip manufacturers. Chinese companies are also growing in the market for mobile processors. These companies are also increasing their chip-making capabilities by creating their own chips. This has helped to make them more competitive in the industry.
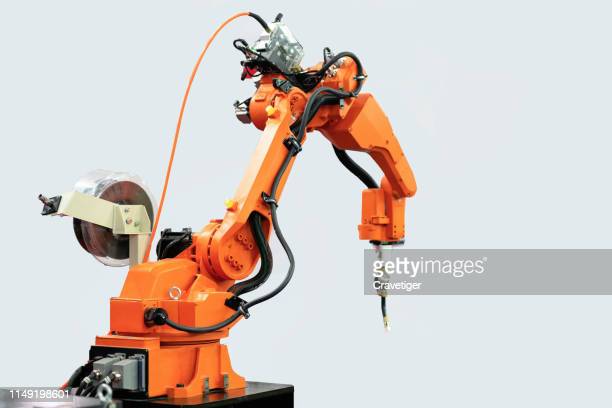
China is fast becoming a global hub for chip manufacturing. But there are still challenges. Chinese companies lack the resources necessary to mass-produce high-end microchips. These chips are used in smartphones, wearable devices, and servers. In addition, the country is not yet self-sufficient in the raw materials required for chip manufacturing. These include tantalum, enriched isotopes and neon. These raw materials undergo chemical processing to be refined.
The Chinese government also wants to reduce its dependence on imported chips. China plans to make 70% of its chip manufacturing in China by 2025. However, this will take years to achieve. China currently has 32 registered chips companies. Many more are still awaiting IPOs. The government is also actively marketing its industrial policy. It hopes to encourage companies to produce more chips in the country, which is a significant challenge given the limited resources available.
The US semiconductor market is experiencing an unprecedented shortage. Washington recently passed new rules restricting the ability of US citizens to support chip production.
TSMC, one of the world's largest chipmakers, has not yet made any announcements about a future plant in Europe. But it has not ruled out building an older-generation chip plant there. It has also partnered up with European automakers in order to buy less-advanced chip technology. The idea has been resisted by most European auto companies. The addition of a European plant to the supply chain would increase its complexity. This would mean that chips would need to be shipped back from Asia for processing. This could prolong the life of the chip by several more years.
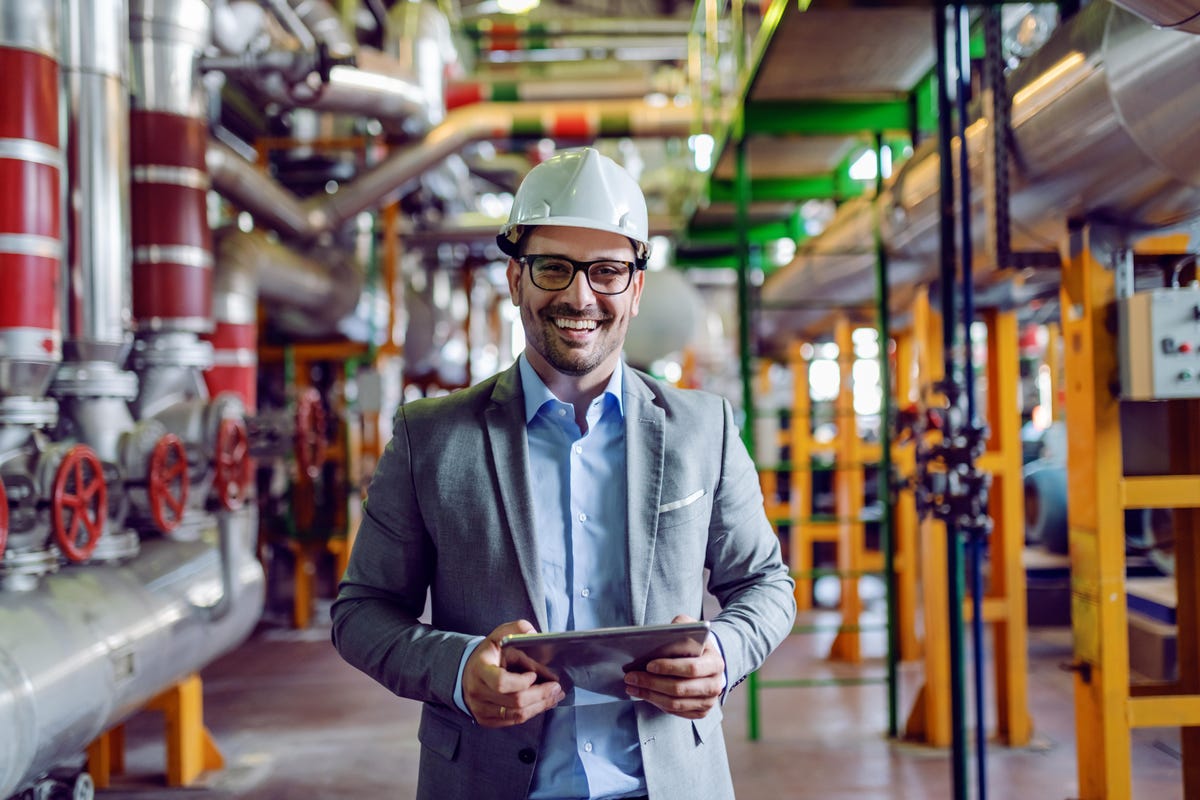
A report from the US Commerce Department states that the chip shortage could become severe in 2021. This has led to long delays for consumers. The shortage has also had a negative impact on transportation, healthcare, as well as gaming consoles. The US government will invest in reshoring chips production to create thousands of jobs and ensure a more resilient chip supply.
FAQ
What do we need to know about Manufacturing Processes in order to learn more about Logistics?
No. You don't have to know about manufacturing processes before learning about logistics. It is important to know about the manufacturing processes in order to understand how logistics works.
What is the difference between manufacturing and logistics
Manufacturing is the act of producing goods from raw materials using machines and processes. Logistics covers all aspects involved in managing supply chains, including procurement and production planning. Manufacturing and logistics can often be grouped together to describe a larger term that covers both the creation of products, and the delivery of them to customers.
How can efficiency in manufacturing be improved?
First, we need to identify which factors are most critical in affecting production times. The next step is to identify the most important factors that affect production time. If you don’t know how to start, look at which factors have the greatest impact upon production time. Once you have identified the factors, then try to find solutions.
What are the main products of logistics?
Logistics refers to the movement of goods from one place to another.
They include all aspects of transport, including packaging, loading, transporting, unloading, storing, warehousing, inventory management, customer service, distribution, returns, and recycling.
Logisticians ensure that the product is delivered to the correct place, at the right time, and under safe conditions. They help companies manage their supply chain efficiency by providing information on demand forecasts, stock levels, production schedules, and availability of raw materials.
They keep track and monitor the transit of shipments, maintain quality standards, order replenishment and inventories, coordinate with suppliers, vendors, and provide support for sales and marketing.
Are there ways to automate parts of manufacturing?
Yes! Yes. Automation has been around since ancient time. The Egyptians discovered the wheel thousands and years ago. Today, robots assist in the assembly of lines.
There are many applications for robotics in manufacturing today. These include:
-
Line robots
-
Robot welding
-
Robot painting
-
Robotics inspection
-
Robots that create products
Manufacturing can also be automated in many other ways. 3D printing makes it possible to produce custom products in a matter of days or weeks.
Statistics
- Many factories witnessed a 30% increase in output due to the shift to electric motors. (en.wikipedia.org)
- According to a Statista study, U.S. businesses spent $1.63 trillion on logistics in 2019, moving goods from origin to end user through various supply chain network segments. (netsuite.com)
- You can multiply the result by 100 to get the total percent of monthly overhead. (investopedia.com)
- [54][55] These are the top 50 countries by the total value of manufacturing output in US dollars for its noted year according to World Bank.[56] (en.wikipedia.org)
- In the United States, for example, manufacturing makes up 15% of the economic output. (twi-global.com)
External Links
How To
Six Sigma and Manufacturing
Six Sigma is defined by "the application SPC (statistical process control) techniques to achieve continuous improvements." It was developed by Motorola's Quality Improvement Department at their plant in Tokyo, Japan, in 1986. Six Sigma's main goal is to improve process quality by standardizing processes and eliminating defects. Many companies have adopted this method in recent years. They believe there is no such thing a perfect product or service. Six Sigma seeks to reduce variation between the mean production value. This means that if you take a sample of your product, then measure its performance against the average, you can find out what percentage of the time the process deviates from the norm. If the deviation is excessive, it's likely that something needs to be fixed.
Understanding how your business' variability is a key step towards Six Sigma implementation is the first. Once you've understood that, you'll want to identify sources of variation. These variations can also be classified as random or systematic. Random variations are caused by human errors. Systematic variations can be caused by outside factors. You could consider random variations if some widgets fall off the assembly lines. It would be considered a systematic problem if every widget that you build falls apart at the same location each time.
Once you've identified the problem areas you need to find solutions. The solution could involve changing how you do things, or redesigning your entire process. After implementing the new changes, you should test them again to see if they worked. If they don't work you need to rework them and come up a better plan.