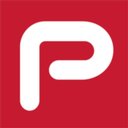
A surprising trend emerged when the list of states with manufacturers revealed that the usual suspects (such as the southeastern ones) are at the top. But this trend is changing and many states show that you can trade off cost and quality of labor to get the best deals. This trend shows that many factors affect a state's ability attract manufacturing jobs. So how do you choose the best place for your business?
Group Five
The following list contains a listing of all Group Five manufacturers, organized by state. The Group Five portfolio includes steel pipes and structural components as well as industrial engineering products. The company offers pipe design services. They offer the best price to quality ratio in steel thickness and grade. The company utilizes the latest CAD systems, computer finite analysis programs, and other advanced software to ensure that your pipe design is perfect.
Group Three
The United States Census Bureau estimates that there are about 50,000 manufacturers within Group Three. The group has low unemployment and high rates of economic growth. However, its GDP growth rate is low. This is because the majority of manufacturers in this group have small businesses. These limitations aside, the data can still serve as a guide. Here are the top companies in each state. Continue reading to find out more.
Three of the largest European manufacturers are Audi and Mercedes-Benz. Honda and Toyota fall to fifth and fifth, respectively. But, the Big Three has been reclaimed from Honda and Toyota by the Detroit Three. The following table lists these carmakers as well as their sales in each respective state. The link below will take you to the list of top-selling cars in each state. There are many models for these manufacturers, including SUVs, minivans, and midsize sedans.
FAQ
What skills should a production planner have?
To become a successful production planner, you need to be organized, flexible, and able to multitask. It is also important to be able communicate with colleagues and clients.
How can overproduction in manufacturing be reduced?
Better inventory management is key to reducing excess production. This would reduce the time spent on unproductive activities like purchasing, storing and maintaining excess stock. This will allow us to free up resources for more productive tasks.
One way to do this is to adopt a Kanban system. A Kanban board is a visual display used to track work in progress. A Kanban system allows work items to move through several states before reaching their final destination. Each state is assigned a different priority.
When work is completed, it can be transferred to the next stage. It is possible to keep a task in the beginning stages until it gets to the end.
This helps to keep work moving forward while ensuring that no work is left behind. Managers can view the Kanban board to see how much work they have done. This allows them the ability to adjust their workflow using real-time data.
Lean manufacturing can also be used to reduce inventory levels. Lean manufacturing emphasizes eliminating waste in all phases of production. Waste includes anything that does not add value to the product. There are several types of waste that you might encounter:
-
Overproduction
-
Inventory
-
Packaging that is not necessary
-
Overstock materials
Manufacturers can increase efficiency and decrease costs by implementing these ideas.
What does warehouse mean?
A warehouse or storage facility is where goods are stored before they are sold. It can be an indoor space or an outdoor area. It could be one or both.
What jobs are available in logistics?
There are many types of jobs in logistics. Here are some:
-
Warehouse workers - They load trucks and pallets.
-
Transportation drivers – They drive trucks or trailers to transport goods and perform pick-ups.
-
Freight handlers, - They sort out and pack freight in warehouses.
-
Inventory managers – They manage the inventory in warehouses.
-
Sales representatives: They sell products to customers.
-
Logistics coordinators - They organize and plan logistics operations.
-
Purchasing agents - They buy goods and services that are necessary for company operations.
-
Customer service representatives – They answer emails and phone calls from customers.
-
Ship clerks - They issue bills and process shipping orders.
-
Order fillers – They fill orders based upon what was ordered and shipped.
-
Quality control inspectors are responsible for inspecting incoming and outgoing products looking for defects.
-
Others – There are many other types available in logistics. They include transport supervisors, cargo specialists and others.
Statistics
- According to the United Nations Industrial Development Organization (UNIDO), China is the top manufacturer worldwide by 2019 output, producing 28.7% of the total global manufacturing output, followed by the United States, Japan, Germany, and India.[52][53] (en.wikipedia.org)
- Many factories witnessed a 30% increase in output due to the shift to electric motors. (en.wikipedia.org)
- It's estimated that 10.8% of the U.S. GDP in 2020 was contributed to manufacturing. (investopedia.com)
- Job #1 is delivering the ordered product according to specifications: color, size, brand, and quantity. (netsuite.com)
- In 2021, an estimated 12.1 million Americans work in the manufacturing sector.6 (investopedia.com)
External Links
How To
Six Sigma and Manufacturing
Six Sigma is defined by "the application SPC (statistical process control) techniques to achieve continuous improvements." Motorola's Quality Improvement Department developed it at their Tokyo plant in Japan in 1986. Six Sigma's core idea is to improve the quality of processes by standardizing and eliminating defects. Many companies have adopted Six Sigma in recent years because they believe that there are no perfect products and services. Six Sigma's primary goal is to reduce variation from the average value of production. It is possible to measure the performance of your product against an average and find the percentage of time that it differs from the norm. If it is too large, it means that there are problems.
Understanding the dynamics of variability within your business is the first step in Six Sigma. Once you understand that, it is time to identify the sources of variation. This will allow you to decide if these variations are random and systematic. Random variations occur when people make mistakes; systematic ones are caused by factors outside the process itself. For example, if you're making widgets, and some of them fall off the assembly line, those would be considered random variations. If however, you notice that each time you assemble a widget it falls apart in exactly the same spot, that is a problem.
After identifying the problem areas, you will need to devise solutions. It might mean changing the way you do business or redesigning it entirely. You should then test the changes again after they have been implemented. If they fail, you can go back to the drawing board to come up with a different plan.