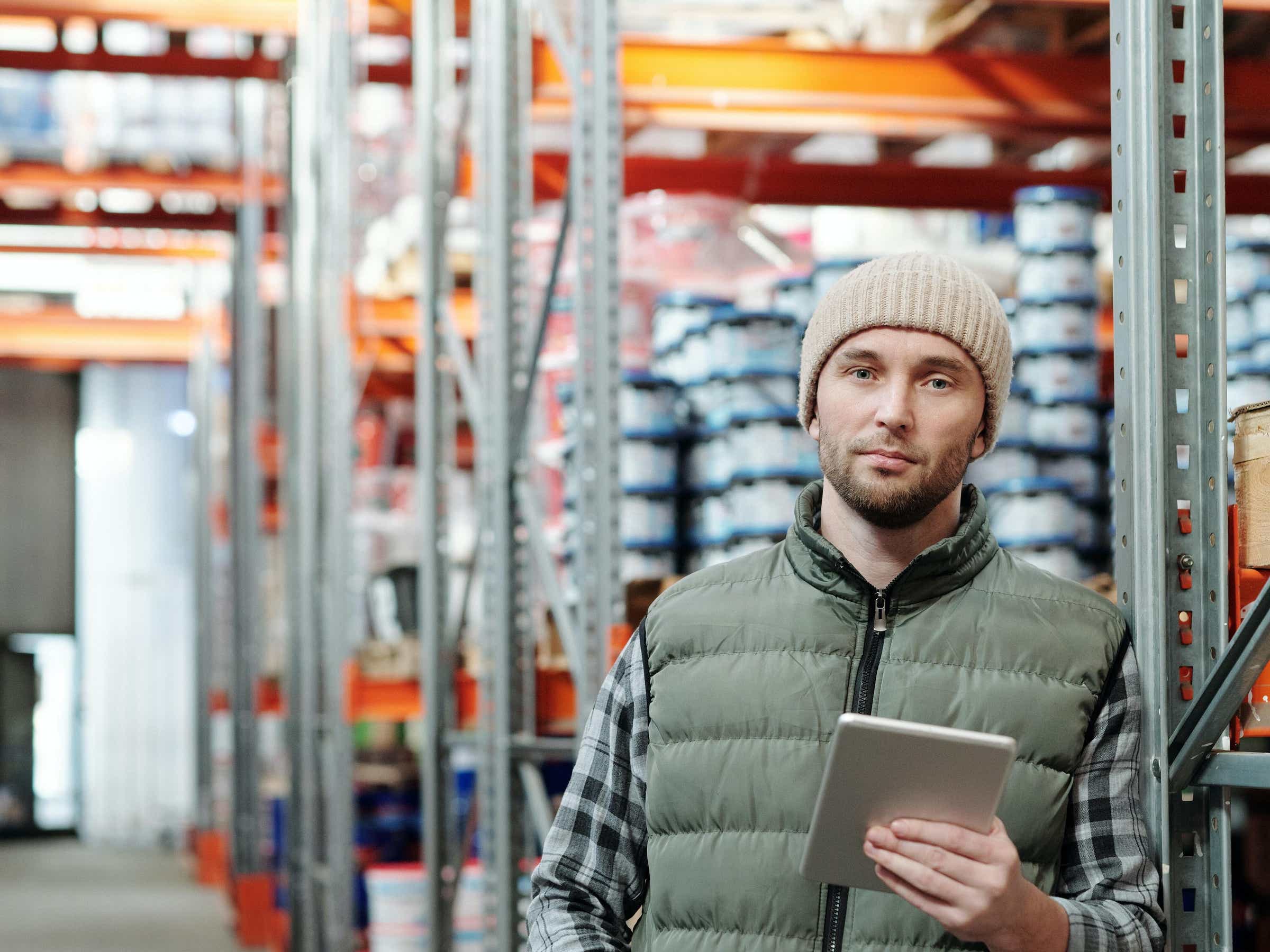
There are many types and styles of manufacturers. Which one is best for you business? Learn about Discrete, Process, Job shop, and Continuous manufacturing. Each type has their own advantages and drawbacks. This article will show you how the four types of manufacturing differ. You can choose the best model for your business based on your industry, location, and product type. Once you've decided on the right type, you should consider your sales, manufacturing, and quality control.
Discrete manufacturing
Discrete production is when distinct products are manufactured. Toys, cars, and aeroplanes are just a few examples of discrete manufacturing. Discrete manufacturing allows companies the freedom to concentrate on specific products rather than mass production. In other words, discrete manufacture allows for the creation of unique parts in an aeroplane using multiple manufacturing processes. Discrete manufacturing is a popular way to manufacture high-tech items.
Discrete manufacturing produces distinct items. Instead of producing identical products, discrete Manufacturing produces items that can readily be identified by serial numbers or labels. For example, a smartphone may consist of different parts manufactured in multiple factories in different states, and the individual parts are assembled only once the finished product is ready to be sold. The bag of your smartphone is the same. It might contain different parts of several plants, including the Missouri plant and headquarters.
Manufacturing process
The term process manufacturing is a branch in manufacturing that involves formulas and recipe. The term process manufacturing contrasts with discrete manufacturing, which is concerned with individual units, bills of materials, and the assembly of components. The two manufacturing methods have very different goals. But each one is an important part of the manufacturing process. Here are three different ways to distinguish process manufacturing and discrete production. Let's have a look at them all.
Batch process manufacturing can be compared to continuous process production. It uses larger batches of raw materials, and works around the clock. Batch process manufacturing is common in pharmaceuticals, paper production, newspaper printing, bookbinding, and some food products. This method may not be the right fit for all industries. This method is often too complicated and expensive for small-scale businesses. This is why most companies resort to this method when producing large quantities of the same product.
Manufacturing job shop
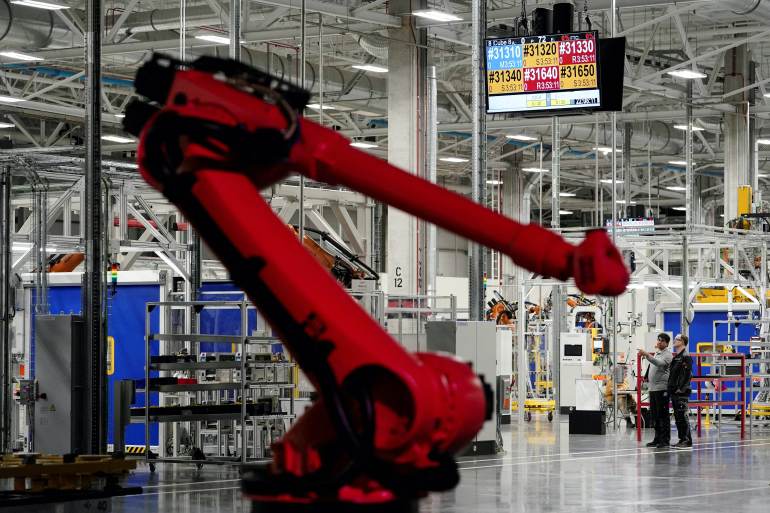
Job shop manufacturing is a small-scale system of production that specializes in custom, batch, and semi-custom manufacturing. Once each job has been completed, job shops can move on. This type of production is also known lean manufacturing. It is more efficient to use a single shift than many other methods. Here are some advantages of job shop production. You can read on to learn about this type of manufacturing. This method of manufacturing might be beneficial for your business.
First, job shops must be more efficient. Incorporating new manufacturing principles is key to achieving lean manufacturing systems. These principles emphasize total quality control and just-in-time production, and are highly relevant to high-volume operations. By adopting new manufacturing principles, a job shop can increase productivity while lowering costs at the same time. Each job must be done one at a given time. There should not be any waiting.
Continuous manufacturing
Continuous manufacturing's greatest benefit is its flexibility in tracking. This is especially useful when it comes down to product failure. Because the production lines can track the amount of raw materials and the time stamp, this information can be used to identify defective batches of drugs. The manufacturer can also reduce the risk of product shortages and waste by increasing their tracking. In the pharmaceutical industry, continuous manufacturing is also gaining popularity.
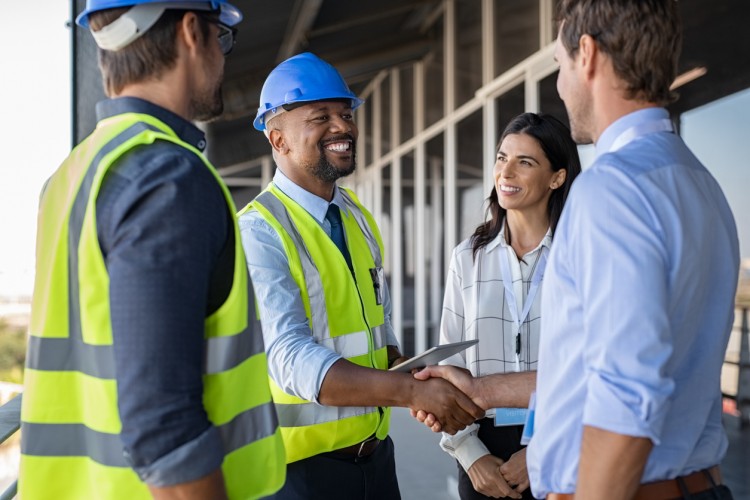
Although continuous manufacturing has many benefits, implementation can be difficult. The slow pace of implementation can make it difficult to integrate the manufacturing process with the rest. Continuous manufacturing has the potential of being a game changer in the pharmaceutical business, despite the limitations. Continuous manufacturing is only possible if the process integrates with end-to–end integration and continuous flow. The benefits of continuous manufacture have long been recognized by the pharmaceutical industries, but implementation has been slow.
FAQ
What types of jobs can you find in logistics
Logistics can offer many different jobs. These are some of the jobs available in logistics:
-
Warehouse workers - They load trucks and pallets.
-
Transportation drivers: They drive trucks and trailers and deliver goods and make pick-ups.
-
Freight handlers - They sort and pack freight in warehouses.
-
Inventory managers – They manage the inventory in warehouses.
-
Sales representatives: They sell products to customers.
-
Logistics coordinators – They plan and coordinate logistics operations.
-
Purchasing agents are those who purchase goods and services for the company.
-
Customer service representatives are available to answer customer calls and emails.
-
Shipping clerks - They process shipping orders and issue bills.
-
Order fillers - These people fill orders based on what has been ordered.
-
Quality control inspectors - They check incoming and outgoing products for defects.
-
Others - There are many other types of jobs available in logistics, such as transportation supervisors, cargo specialists, etc.
What is the role and responsibility of a Production Planner?
A production planner makes sure all project elements are delivered on schedule, within budget, as well as within the agreed scope. They ensure that the product or service is of high quality and meets client requirements.
What are the responsibilities of a manufacturing manager
A manufacturing manager must make sure that all manufacturing processes run smoothly and effectively. They should also be aware and responsive to any company problems.
They should also be able communicate with other departments, such as sales or marketing.
They should also be aware of the latest trends in their industry and be able to use this information to help improve productivity and efficiency.
What are the 7 Rs of logistics?
The 7R's of Logistics is an acronym for the seven basic principles of logistics management. It was developed by the International Association of Business Logisticians (IABL) and published in 2004 as part of its "Seven Principles of Logistics Management" series.
The acronym is made up of the following letters:
-
Responsive - ensure all actions are legal and not harmful to others.
-
Reliable - You can have confidence that you will fulfill your promises.
-
Reasonable - make sure you use your resources well and don't waste them.
-
Realistic – Consider all aspects, including cost-effectiveness as well as environmental impact.
-
Respectful – Treat others fairly and equitably.
-
Be resourceful: Look for opportunities to save money or increase productivity.
-
Recognizable - Provide value-added services to customers
How is a production manager different from a producer planner?
A production planner is more involved in the planning phase of the project than a project manger.
What is the difference between Production Planning, Scheduling and Production Planning?
Production Planning (PP) is the process of determining what needs to be produced at any given point in time. This is done through forecasting demand and identifying production capacities.
Scheduling refers the process by which tasks are assigned dates so that they can all be completed within the given timeframe.
Statistics
- According to the United Nations Industrial Development Organization (UNIDO), China is the top manufacturer worldwide by 2019 output, producing 28.7% of the total global manufacturing output, followed by the United States, Japan, Germany, and India.[52][53] (en.wikipedia.org)
- Job #1 is delivering the ordered product according to specifications: color, size, brand, and quantity. (netsuite.com)
- In 2021, an estimated 12.1 million Americans work in the manufacturing sector.6 (investopedia.com)
- [54][55] These are the top 50 countries by the total value of manufacturing output in US dollars for its noted year according to World Bank.[56] (en.wikipedia.org)
- According to a Statista study, U.S. businesses spent $1.63 trillion on logistics in 2019, moving goods from origin to end user through various supply chain network segments. (netsuite.com)
External Links
How To
Six Sigma and Manufacturing
Six Sigma is defined by "the application SPC (statistical process control) techniques to achieve continuous improvements." Motorola's Quality Improvement Department in Tokyo, Japan developed Six Sigma in 1986. Six Sigma's core idea is to improve the quality of processes by standardizing and eliminating defects. Since there are no perfect products, or services, this approach has been adopted by many companies over the years. Six Sigma's primary goal is to reduce variation from the average value of production. If you take a sample and compare it with the average, you will be able to determine how much of the production process is different from the norm. If you notice a large deviation, then it is time to fix it.
Understanding the nature of variability in your business is the first step to Six Sigma. Once you have a good understanding of the basics, you can identify potential sources of variation. This will allow you to decide if these variations are random and systematic. Random variations occur when people make mistakes; systematic ones are caused by factors outside the process itself. For example, if you're making widgets, and some of them fall off the assembly line, those would be considered random variations. However, if you notice that every time you assemble a widget, it always falls apart at exactly the same place, then that would be a systematic problem.
Once you've identified where the problems lie, you'll want to design solutions to eliminate those problems. You might need to change the way you work or completely redesign the process. Once you have implemented the changes, it is important to test them again to ensure they work. If they don't work, you will need to go back to the drawing boards and create a new plan.