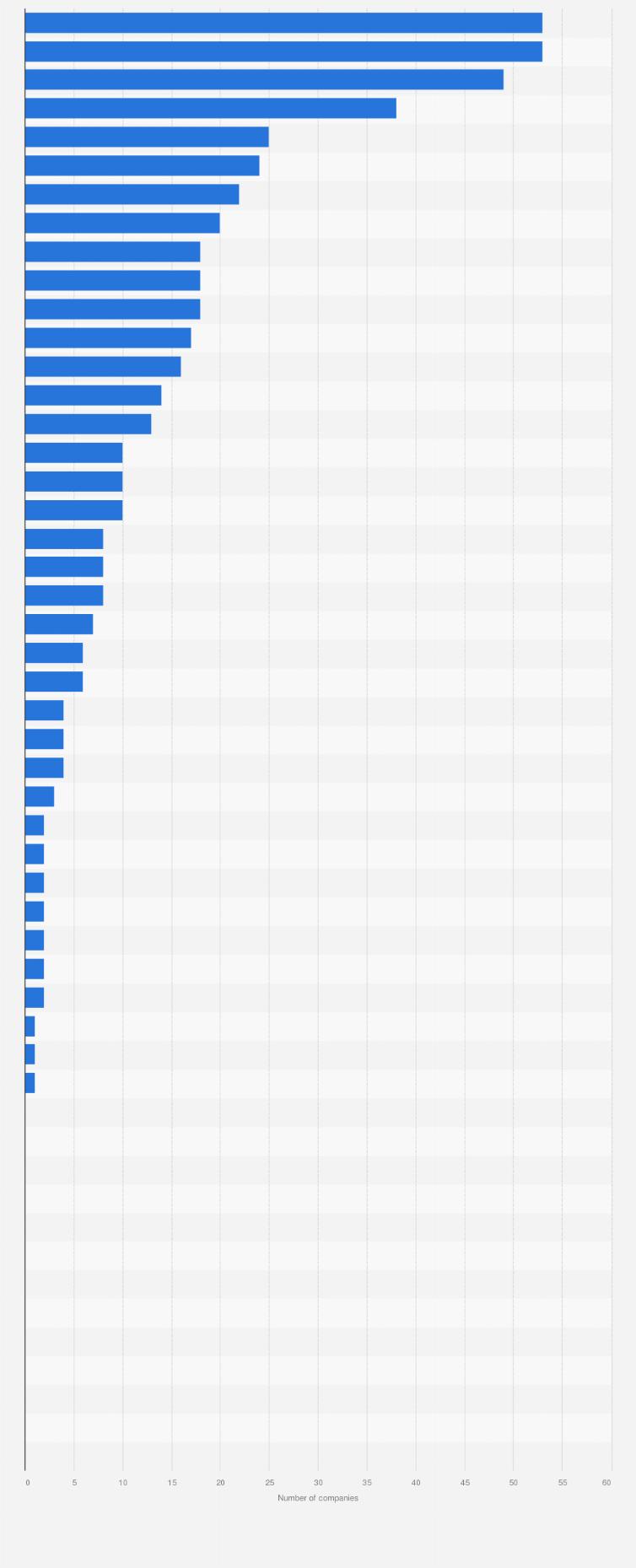
Facilities engineers, also called maintenance engineers, are professionals that provide engineering and construction support for buildings and operations. You will find their tasks include planning and implementing procedures, making recommendations for repairs and upgrades, and organizing routine and emergency maintenance. A wide range of engineering disciplines can play a part in their role, including electrical, mechanical, and plumbing. They have a strong understanding of safety standards, construction law, and other regulatory requirements.
Facilities engineers often start in the entry level of their career and can quickly rise to more senior positions. It is important to have a solid portfolio that includes research, articles, and engineering projects. Facilities engineers need to continue learning about their field. This will enable them to stand out in a job application.
Although it is not mandatory for all facilities engineers, a professional engineer certification can be a big advantage when applying for a new position. A professional engineer should possess a broad knowledge of engineering principles and concepts, as well as the ability to analyze data and make compelling presentations. Facility engineers should be familiar with asset reliability-centered maintenance strategies and predictive maintenance.
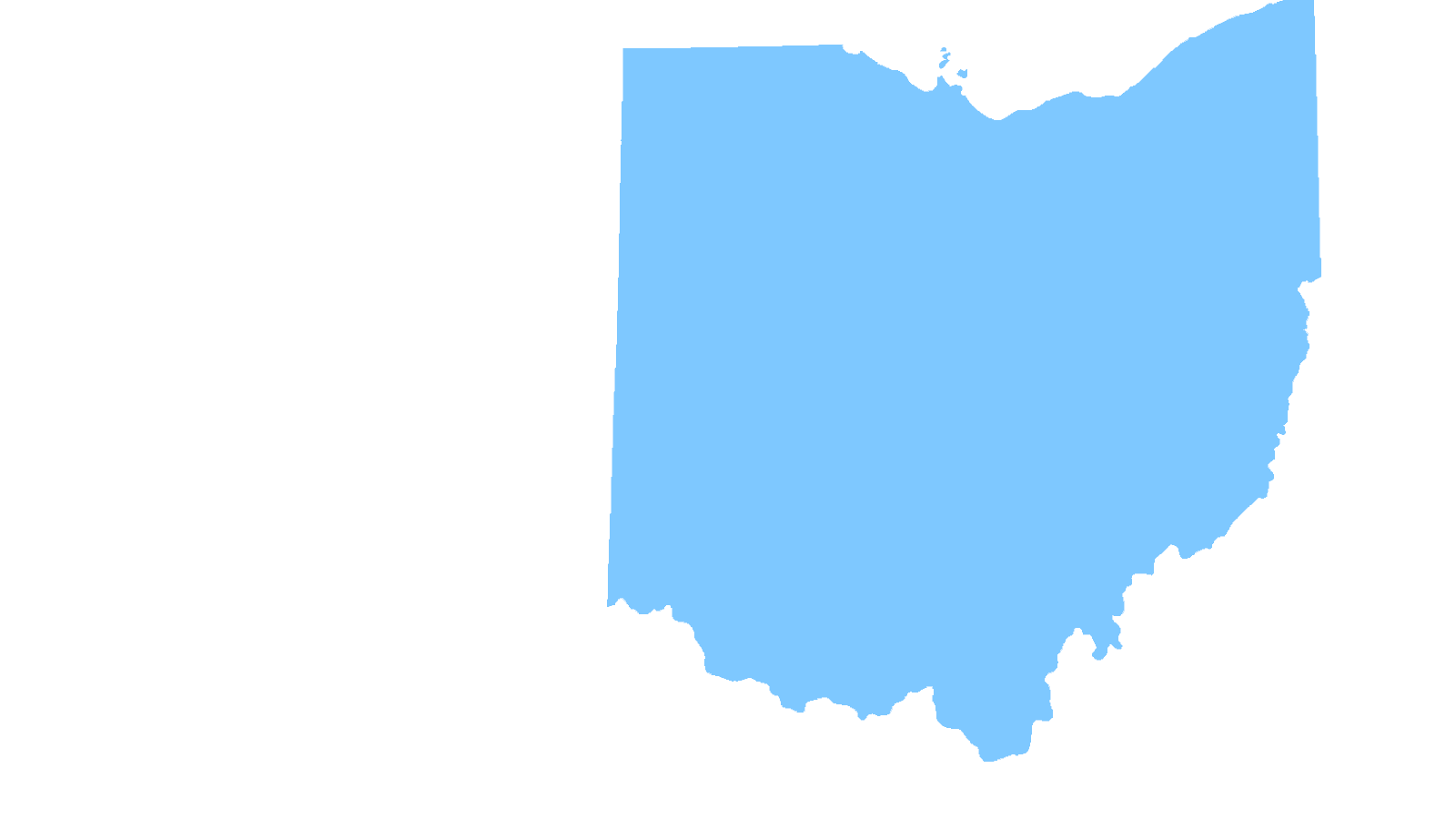
Facility engineers work in offices, construction, and manufacturing environments. They plan and execute processes to ensure that utilities are running safely and efficiently. Facilities engineers often work in close collaboration with management and other engineers to help create efficient work schedules, and handle any problems that may arise.
The duties of a facilities engineer vary depending on the size and type facility that he or she works in. The job requires good time management skills and problem-solving skills. It also requires the ability to work well in a team environment. A facilities engineer might perform hundreds of tasks in a day. The facilities engineer can be responsible for plumbing, electrical, and mechanical equipment. He or she must also be able to diagnose and correct malfunctions.
Many websites, including those of AFE, offer news and information about this profession. These websites contain information about the profession, including a sample resume.
Facilities engineers can also access these sites to read books, articles, take training courses and make connections with other engineers. In order to be a successful facilities engineer, you should have good organizational skills, a good understanding of various engineering and construction disciplines, and a solid understanding of building and safety codes.
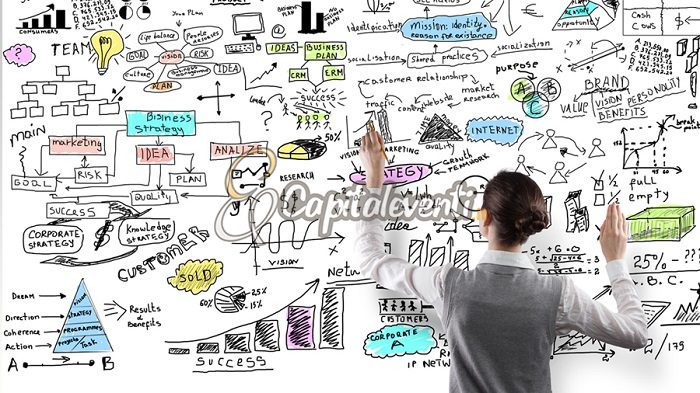
It is important for facilities engineers to be able to simultaneously perform many tasks and analyze data. To accomplish this, they need a working knowledge of design software, such as AutoCAD, as well as construction techniques, such as the CAM method. Other skills that are beneficial include project management, critical thinking, and problem-solving.
One of the biggest advantages of a facilities engineer job is the chance to work with a large array of people. Many engineers in this field are skilled at working with different materials and can coordinate the work of others.
FAQ
What does it take for a logistics enterprise to succeed?
To be a successful businessman in logistics, you will need many skills and knowledge. To communicate effectively with clients and suppliers, you must be able to communicate well. You need to understand how to analyze data and draw conclusions from it. You must be able manage stress and pressure under pressure. You need to be innovative and creative to come up with new ways to increase efficiency. To motivate and guide your team towards reaching organizational goals, you must have strong leadership skills.
You should also be organized and efficient to meet tight deadlines.
Is automation necessary in manufacturing?
Not only is automation important for manufacturers, but it's also vital for service providers. It allows them provide faster and more efficient services. In addition, it helps them reduce costs by reducing human errors and improving productivity.
How can manufacturing efficiency be improved?
First, we need to identify which factors are most critical in affecting production times. Next, we must find ways to improve those factors. If you don’t know where to begin, consider which factors have the largest impact on production times. Once you've identified them, try to find solutions for each of those factors.
How can manufacturing avoid production bottlenecks
To avoid production bottlenecks, ensure that all processes run smoothly from the moment you receive your order to the time the product ships.
This includes both planning for capacity and quality control.
Continuous improvement techniques such Six Sigma are the best method to accomplish this.
Six Sigma management is a system that improves quality and reduces waste within your organization.
It seeks to eliminate variation and create consistency in your work.
What is the responsibility of a logistics manager?
Logistics managers ensure that goods arrive on time and are unharmed. This is done using his/her knowledge of the company's products. He/she should make sure that enough stock is on hand to meet the demands.
Statistics
- In 2021, an estimated 12.1 million Americans work in the manufacturing sector.6 (investopedia.com)
- In the United States, for example, manufacturing makes up 15% of the economic output. (twi-global.com)
- (2:04) MTO is a production technique wherein products are customized according to customer specifications, and production only starts after an order is received. (oracle.com)
- You can multiply the result by 100 to get the total percent of monthly overhead. (investopedia.com)
- Many factories witnessed a 30% increase in output due to the shift to electric motors. (en.wikipedia.org)
External Links
How To
How to Use Lean Manufacturing for the Production of Goods
Lean manufacturing is a management style that aims to increase efficiency and reduce waste through continuous improvement. It was developed in Japan during the 1970s and 1980s by Taiichi Ohno, who received the Toyota Production System (TPS) award from TPS founder Kanji Toyoda. Michael L. Watkins published the book "The Machine That Changed the World", which was the first to be published about lean manufacturing.
Lean manufacturing is often defined as a set of principles used to improve the quality, speed, and cost of products and services. It emphasizes the elimination of defects and waste throughout the value stream. Lean manufacturing is called just-in-time (JIT), zero defect, total productive maintenance (TPM), or 5S. Lean manufacturing focuses on eliminating non-value-added activities such as rework, inspection, and waiting.
Lean manufacturing is a way for companies to achieve their goals faster, improve product quality, and lower costs. Lean manufacturing is a great way to manage the entire value chain including customers, suppliers, distributors and retailers as well as employees. Lean manufacturing practices are widespread in many industries. Toyota's philosophy is the foundation of its success in automotives, electronics and appliances, healthcare, chemical engineers, aerospace, paper and food, among other industries.
Lean manufacturing is based on five principles:
-
Define value - Find out what your business contributes to society, and what makes it different from other competitors.
-
Reduce Waste - Eliminate any activity that doesn't add value along the supply chain.
-
Create Flow. Ensure that your work is uninterrupted and flows seamlessly.
-
Standardize & simplify - Make processes consistent and repeatable.
-
Building Relationships – Establish personal relationships with both external and internal stakeholders.
Lean manufacturing is not a new concept, but it has been gaining popularity over the last few years due to a renewed interest in the economy following the global financial crisis of 2008. Many businesses have adopted lean production techniques to make them more competitive. According to some economists, lean manufacturing could be a significant factor in the economic recovery.
Lean manufacturing has many benefits in the automotive sector. These benefits include increased customer satisfaction, reduced inventory levels and lower operating costs.
It can be applied to any aspect of an organisation. Because it makes sure that all value chains are efficient and effectively managed, Lean Manufacturing is particularly helpful for organizations.
There are three main types of lean manufacturing:
-
Just-in Time Manufacturing, (JIT): This kind of lean manufacturing is also commonly known as "pull-systems." JIT refers to a system in which components are assembled at the point of use instead of being produced ahead of time. This approach aims to reduce lead times, increase the availability of parts, and reduce inventory.
-
Zero Defects Manufacturing, (ZDM): ZDM is focused on ensuring that no defective products leave the manufacturing facility. It is better to repair a part than have it removed from the production line if it needs to be fixed. This is also true for finished products that require minor repairs before shipping.
-
Continuous Improvement (CI), also known as Continuous Improvement, aims at improving the efficiency of operations through continuous identification and improvement to minimize or eliminate waste. Continuous improvement involves continuous improvement of processes and people as well as tools.