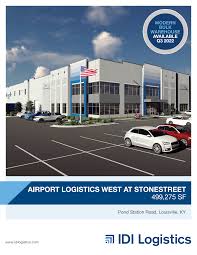
The United States' manufacturing sector has been a key contributor to the country's economy and employment. It is important that the United States, while still the third largest manufacturer in the world remains heavily dependent on other countries for most of its production needs. The United States now faces many challenges, including a dearth of manufacturing capacity, and a highly competitive manufacturing environment. The United States must expand its innovation system in order strengthen our economy.
The United States has one of the highest manufacturing salaries in the country. The United States' largest economic contributor is its manufacturing sector, which accounts for more than 12 % of gross domestic product (GDP), as well as about 6 percent of all jobs. Many people believe that manufacturing is dying. However, this sector is actually thriving.
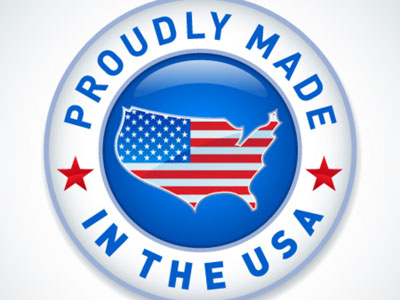
The United States manufacturing industry is a major beneficiary of technology. There has been an explosion in new production technology over the past several years that has allowed companies to make more efficient and faster products. The technology allows for lower costs through more efficient processes. American manufacturers can also increase their competitiveness by improving the efficiency of their production processes.
Technology has also provided a boost to the manufacturing industry in other areas such as automation. Automation has made manufacturing more efficient, which helps keep costs down.
It is important to preserve American manufacturing because it helps protect our financial system. The American-made products are appreciated by consumers who pay attention to environmental standards when buying goods. Companies that invest in their local communities and help them hire their people are valued by many customers.
Another reason to maintain manufacturing in the United States is that it is more environmentally friendly. The United States’ manufacturing industry uses less energy that manufacturing in other countries. This has several benefits including lower emissions and the ability ship goods more efficiently to customers. This helps to lower costs in other areas such as logistics, shipping and manufacturing. The United States' manufacturing sector can lower shipping costs and increase customer satisfaction.
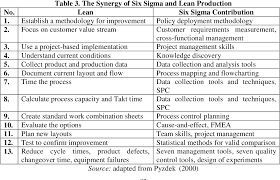
Finally, American manufacturing is a great way of supporting workers not located along the coasts. Many people in this country have been negatively affected by the recession and many are now unemployed. This has also led the U.S. to be more interested in manufacturing capabilities. More than 22,000 jobs were created in manufacturing in the United States in the last year. The future will see the American economy grow.
FAQ
Is it possible to automate certain parts of manufacturing
Yes! Yes. The Egyptians created the wheel thousands years ago. Nowadays, we use robots for assembly lines.
There are many uses of robotics today in manufacturing. These include:
-
Robots for assembly line
-
Robot welding
-
Robot painting
-
Robotics inspection
-
Robots that produce products
Automation could also be used to improve manufacturing. 3D printing makes it possible to produce custom products in a matter of days or weeks.
What are the responsibilities of a manufacturing manager
The manufacturing manager should ensure that every manufacturing process is efficient and effective. They should also be aware and responsive to any company problems.
They should also learn how to communicate effectively with other departments, including sales and marketing.
They should also be knowledgeable about the latest trends in the industry so they can use this information for productivity and efficiency improvements.
What is the role of a logistics manager
Logistics managers ensure that goods arrive on time and are unharmed. This is done through his/her expertise and knowledge about the company's product range. He/she should ensure that sufficient stock is available in order to meet customer demand.
Is automation important in manufacturing?
Automation is essential for both manufacturers and service providers. It enables them to provide services faster and more efficiently. It reduces human errors and improves productivity, which in turn helps them lower their costs.
What makes a production planner different from a project manger?
The difference between a product planner and project manager is that a planer is typically the one who organizes and plans the entire project. A production planner, however, is mostly involved in the planning stages.
What are the 7 R's of logistics?
The 7R's of Logistics is an acronym for the seven basic principles of logistics management. It was developed by the International Association of Business Logisticians (IABL) and published in 2004 as part of its "Seven Principles of Logistics Management" series.
The acronym consists of the following letters:
-
Responsive - ensure all actions are legal and not harmful to others.
-
Reliable - have confidence in the ability to deliver on commitments made.
-
Reasonable - make sure you use your resources well and don't waste them.
-
Realistic - Consider all aspects of operations, including environmental impact and cost effectiveness.
-
Respectful: Treat others with fairness and equity
-
You are resourceful and look for ways to save money while increasing productivity.
-
Recognizable - Provide value-added services to customers
Is there anything we should know about Manufacturing Processes prior to learning about Logistics.
No. No. But, being familiar with manufacturing processes will give you a better understanding about how logistics works.
Statistics
- According to the United Nations Industrial Development Organization (UNIDO), China is the top manufacturer worldwide by 2019 output, producing 28.7% of the total global manufacturing output, followed by the United States, Japan, Germany, and India.[52][53] (en.wikipedia.org)
- Job #1 is delivering the ordered product according to specifications: color, size, brand, and quantity. (netsuite.com)
- According to a Statista study, U.S. businesses spent $1.63 trillion on logistics in 2019, moving goods from origin to end user through various supply chain network segments. (netsuite.com)
- You can multiply the result by 100 to get the total percent of monthly overhead. (investopedia.com)
- (2:04) MTO is a production technique wherein products are customized according to customer specifications, and production only starts after an order is received. (oracle.com)
External Links
How To
How to Use Six Sigma in Manufacturing
Six Sigma is "the application statistical process control (SPC), techniques for continuous improvement." Motorola's Quality Improvement Department created Six Sigma at their Tokyo plant, Japan in 1986. Six Sigma's core idea is to improve the quality of processes by standardizing and eliminating defects. Since there are no perfect products, or services, this approach has been adopted by many companies over the years. Six Sigma aims to reduce variation in the production's mean value. This means that if you take a sample of your product, then measure its performance against the average, you can find out what percentage of the time the process deviates from the norm. If you notice a large deviation, then it is time to fix it.
Understanding how your business' variability is a key step towards Six Sigma implementation is the first. Once you understand this, you can then identify the causes of variation. These variations can also be classified as random or systematic. Random variations occur when people do mistakes. Symmetrical variations are caused due to factors beyond the process. If you make widgets and some of them end up on the assembly line, then those are considered random variations. It would be considered a systematic problem if every widget that you build falls apart at the same location each time.
Once you've identified the problem areas you need to find solutions. It might mean changing the way you do business or redesigning it entirely. You should then test the changes again after they have been implemented. If they don’t work, you’ll need to go back and rework the plan.