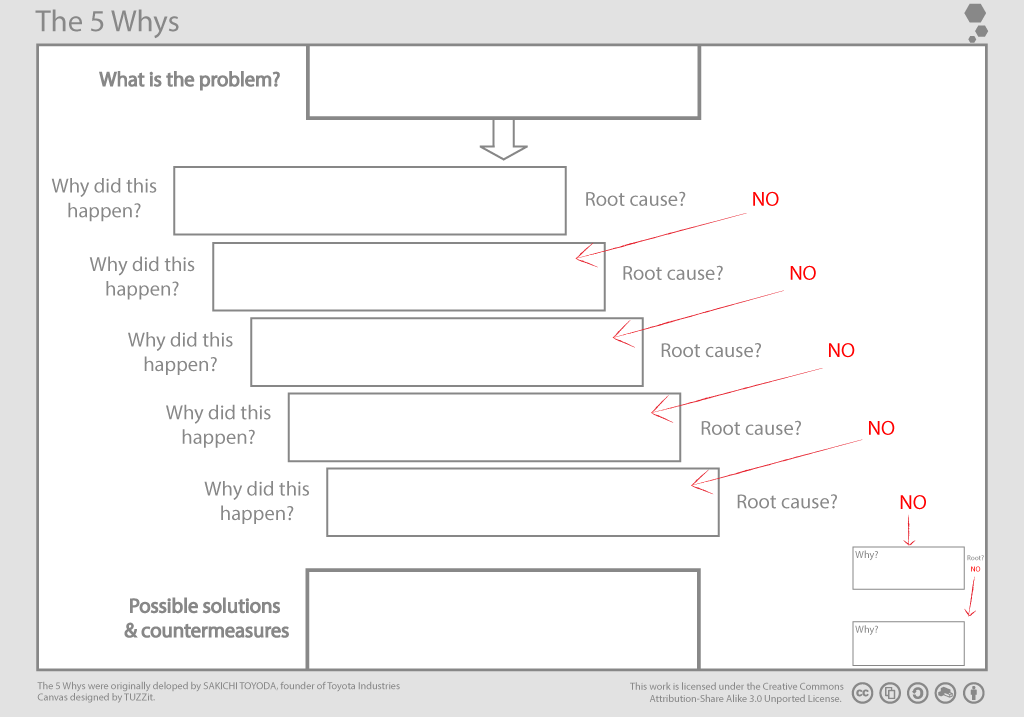
Tampa offers many different logistics jobs. Many of these jobs are in the manufacturing, construction or healthcare industries. However you can work in the wholesale trading industry, consulting firms, or other businesses that streamline supply chains.
A degree can provide a wide range of career options. Associate degrees can lead to entry-level jobs such as shipping clerks, but bachelor's degree holders are more likely to find higher paying positions. You may decide to specialize in one area of logistic, such as warehouse management or supply chain.
BLS statistics predict that jobs for logistics professionals will increase by 5 percent between 2018-2028. It is predicted that professionals focusing on business operations will see greater job growth.
A four-year college or community college can offer a degree in logistics. These programs usually offer a wide range of logistics specializations. This allows you to develop more specialized skills, and make you more employable when you advance up the ladder.
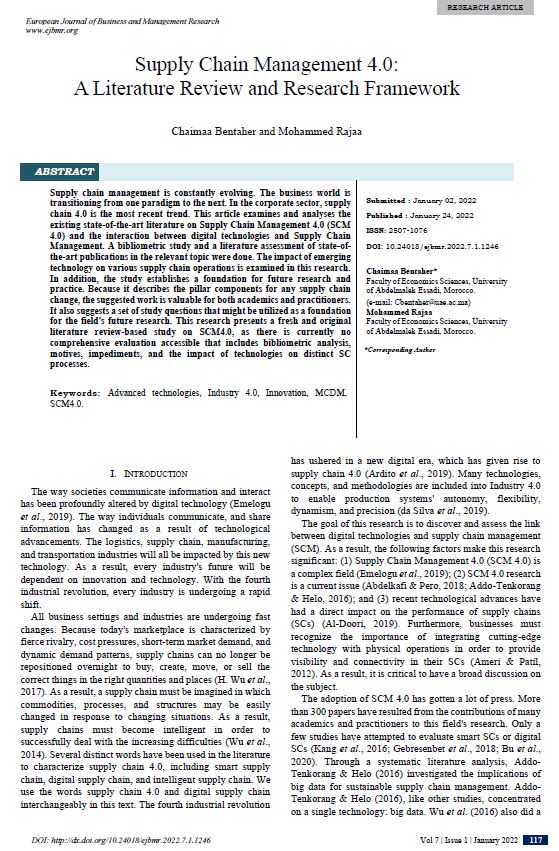
Students should also consider networking and internships in addition to earning a bachelor's. These opportunities can give you invaluable experience and help you land your first logistics position.
The logistics industry has a diverse workforce, and job prospects are generally good. There are many logistics jobs available across the nation, especially in large, growing states like California and Texas. Careers are available in several specific sectors, including aerospace and oil & gas.
When choosing a logistics company, you should consider their size and capabilities. Ideally, you should select a 3PL that understands your business and can offer you a customized solution to meet your specific needs. It will help you reduce costs and improve efficiency.
The success of your company is dependent on the supply chain. You must have the right people and the right tools to ensure that your products arrive at the correct time and in perfect condition. You can improve the efficiency of your supply chain by selecting a third-party logistics provider that has expertise in your industry and can deliver the goods on time, every time.
Sheer is a Tampa-based, full-service 3PL that can improve the speed and efficiency of your supply chain while lowering your costs. We provide a range of services to our customers, including transportation, inventory management, and shipping.
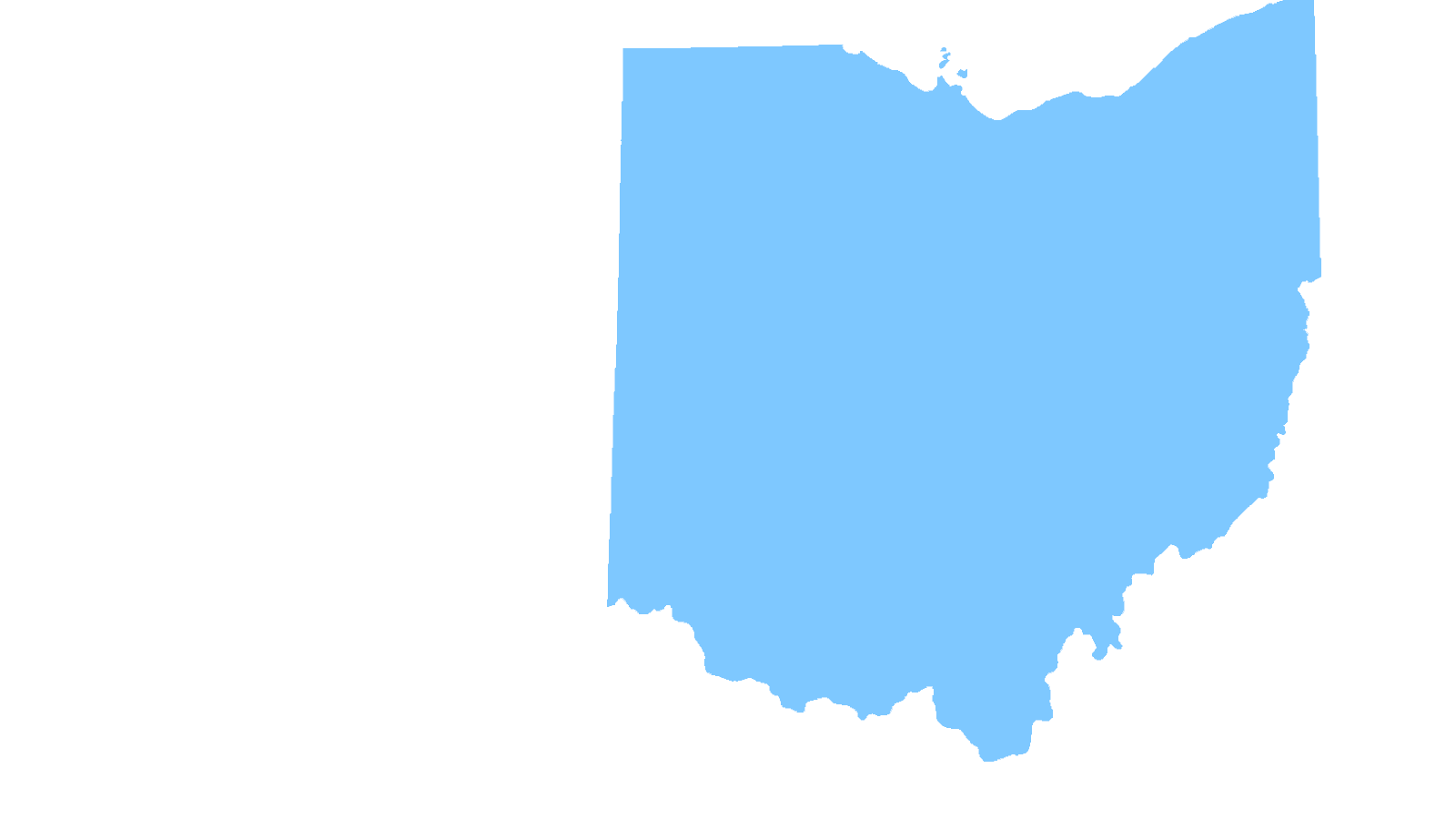
We offer a range of technology tools that will help you manage and track your supply chain. Our suite of cloud-based software integrates seamlessly with your ERP system. This allows you to manage and monitor your entire business.
Sheer’s multimodal freight networks can turn your supply chain around from a liability into an asset. You can count us to ensure that all of your products arrive safely and on schedule, every time.
FAQ
How can manufacturing prevent production bottlenecks?
The key to avoiding bottlenecks in production is to keep all processes running smoothly throughout the entire production cycle, from the time you receive an order until the time when the product ships.
This includes both planning for capacity and quality control.
The best way to do this is to use continuous improvement techniques such as Six Sigma.
Six Sigma is a management method that helps to improve quality and reduce waste.
It seeks to eliminate variation and create consistency in your work.
How can I learn about manufacturing?
Experience is the best way for you to learn about manufacturing. You can also read educational videos or take classes if this isn't possible.
What are the 7 Rs of logistics.
The 7R's of Logistics is an acronym for the seven basic principles of logistics management. It was developed by the International Association of Business Logisticians (IABL) and published in 2004 as part of its "Seven Principles of Logistics Management" series.
The following letters form the acronym:
-
Responsible - ensure that actions are in compliance with legal requirements and do not cause harm to others.
-
Reliable: Have faith in your ability or the ability to honor any promises made.
-
It is reasonable to use resources efficiently and not waste them.
-
Realistic - Take into consideration all aspects of operations including cost-effectiveness, environmental impact, and other factors.
-
Respectful – Treat others fairly and equitably.
-
You are resourceful and look for ways to save money while increasing productivity.
-
Recognizable is a company that provides customers with value-added solutions.
What makes a production planner different from a project manger?
A production planner is more involved in the planning phase of the project than a project manger.
What are manufacturing and logistic?
Manufacturing refers to the process of making goods using raw materials and machines. Logistics is the management of all aspects of supply chain activities, including procurement, production planning, distribution, warehousing, inventory control, transportation, and customer service. As a broad term, manufacturing and logistics often refer to both the creation and delivery of products.
Statistics
- You can multiply the result by 100 to get the total percent of monthly overhead. (investopedia.com)
- It's estimated that 10.8% of the U.S. GDP in 2020 was contributed to manufacturing. (investopedia.com)
- [54][55] These are the top 50 countries by the total value of manufacturing output in US dollars for its noted year according to World Bank.[56] (en.wikipedia.org)
- In the United States, for example, manufacturing makes up 15% of the economic output. (twi-global.com)
- According to the United Nations Industrial Development Organization (UNIDO), China is the top manufacturer worldwide by 2019 output, producing 28.7% of the total global manufacturing output, followed by the United States, Japan, Germany, and India.[52][53] (en.wikipedia.org)
External Links
How To
How to Use Six Sigma in Manufacturing
Six Sigma refers to "the application and control of statistical processes (SPC) techniques in order to achieve continuous improvement." Motorola's Quality Improvement Department in Tokyo, Japan developed Six Sigma in 1986. Six Sigma's main goal is to improve process quality by standardizing processes and eliminating defects. In recent years, many companies have adopted this method because they believe there is no such thing as perfect products or services. Six Sigma aims to reduce variation in the production's mean value. This means that you can take a sample from your product and then compare its performance to the average to find out how often the process differs from the norm. If this deviation is too big, you know something needs fixing.
Understanding the dynamics of variability within your business is the first step in Six Sigma. Once you have this understanding, you will need to identify sources and causes of variation. This will allow you to decide if these variations are random and systematic. Random variations are caused by human errors. Systematic variations can be caused by outside factors. If you make widgets and some of them end up on the assembly line, then those are considered random variations. You might notice that your widgets always fall apart at the same place every time you put them together.
Once you have identified the problem, you can design solutions. That solution might involve changing the way you do things or redesigning the process altogether. After implementing the new changes, you should test them again to see if they worked. If they didn't work, then you'll need to go back to the drawing board and come up with another plan.