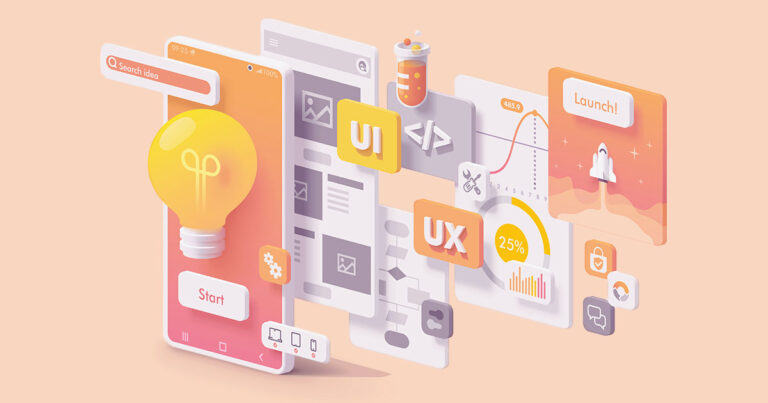
During the industrial revolution, manufacturing engineers have been in demand. They are responsible to design manufacturing processes which improve production efficiency. Manufacturing engineers must be commercially-aware in addition to their technical knowledge. They must have a strong background in mathematics and science. They should also have leadership skills.
The education and skills of a manufacturing engineering engineer will determine their salary. They can expect to earn between $70960 and $126,000 per annum in the United States. They can get a master’s degree to help them advance their careers. They can then enjoy a better salary. A master's can allow them to learn new technologies, and improve their skills.
To contribute as researchers, they may also be eligible to pursue a PhD. They may also work for the local and central government. They may also work in the capacity of consultants. They may work in various manufacturing areas.
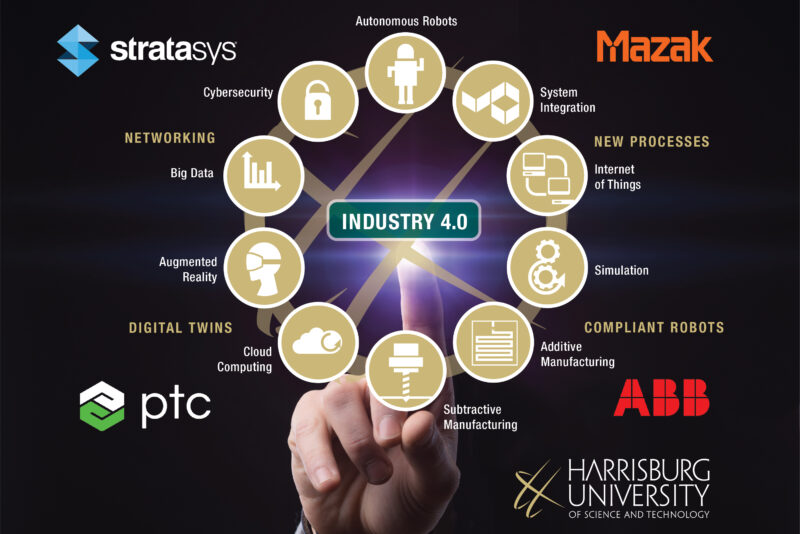
Manufacturing engineers typically earn more if they are experienced. They will become more experienced and can move up to managerial roles. This position allows them to design and implement manufacturing processes. They will also be responsible for overseeing the day to day operations of the factory. They may also be required to work on weekends and evenings.
Most manufacturing engineers start as interns or apprentices. They can work anywhere in manufacturing. They can also work in industrial or commercial design. They may become consultants after gaining some experience. This position will allow them to manage the factory floor as well as guide engineers. They will also be responsible in maintaining the company’s best practices. They will also be expected to identify and resolve any errors in the manufacturing process.
Manufacturing engineers have to keep up with the latest manufacturing trends and technologies. They need to be able work in a fast-paced environment, and solve any problems that might arise. They also need to demonstrate leadership qualities and IT skills. They will receive a salary of a minimum wage during their first year in the industry. They can earn a slightly higher salary after they have been in the industry for a few years.
The average salary for manufacturing engineers is between $28,500-126,000 per annum. This includes bonuses and taxable earnings. The state where the job is situated can affect the salary. Manufacturing Engineers can make as much at $34 an hr in some states.
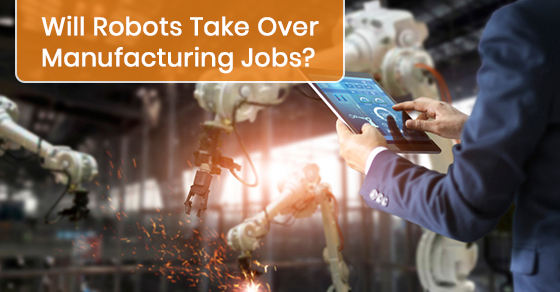
A manufacturing engineer may work in any of the many manufacturing industries such as paper manufacturing, aerospace manufacturing, and pharmaceutical manufacturing. They can work for large multinational organizations or smaller local operations. You can also find manufacturing engineers working for the central and local governments.
They can also work for new industrial estates. General Motors and Tesla are some of the most prominent American manufacturing companies. A graduate degree is also a great way for engineers to learn about new technologies.
FAQ
What is the role of a manager in manufacturing?
The manufacturing manager should ensure that every manufacturing process is efficient and effective. They should also be aware and responsive to any company problems.
They should also know how to communicate with other departments such as sales and marketing.
They should be informed about industry trends and be able make use of this information to improve their productivity and efficiency.
How can excess manufacturing production be reduced?
In order to reduce excess production, you need to develop better inventory management methods. This would reduce time spent on activities such as purchasing, stocking, and maintaining excess stock. This will allow us to free up resources for more productive tasks.
Kanban systems are one way to achieve this. A Kanban board can be used to monitor work progress. Kanban systems are where work items travel through a series of states until reaching their final destination. Each state represents an individual priority level.
When work is completed, it can be transferred to the next stage. It is possible to keep a task in the beginning stages until it gets to the end.
This keeps work moving and ensures no work is lost. With a Kanban board, managers can see exactly how much work is being done at any given moment. This allows them the ability to adjust their workflow using real-time data.
Lean manufacturing is another option to control inventory levels. Lean manufacturing is about eliminating waste from all stages of the production process. Anything that does nothing to add value to a product is waste. These are some of the most common types.
-
Overproduction
-
Inventory
-
Unnecessary packaging
-
Exceed materials
By implementing these ideas, manufacturers can improve efficiency and cut costs.
Is automation important for manufacturing?
Not only are service providers and manufacturers important, but so is automation. It allows them provide faster and more efficient services. It also helps to reduce costs and improve productivity.
What skills is required for a production planner?
Production planners must be flexible, organized, and able handle multiple tasks. Communication skills are essential to ensure that you can communicate effectively with clients, colleagues, and customers.
Statistics
- Job #1 is delivering the ordered product according to specifications: color, size, brand, and quantity. (netsuite.com)
- Many factories witnessed a 30% increase in output due to the shift to electric motors. (en.wikipedia.org)
- In the United States, for example, manufacturing makes up 15% of the economic output. (twi-global.com)
- It's estimated that 10.8% of the U.S. GDP in 2020 was contributed to manufacturing. (investopedia.com)
- According to the United Nations Industrial Development Organization (UNIDO), China is the top manufacturer worldwide by 2019 output, producing 28.7% of the total global manufacturing output, followed by the United States, Japan, Germany, and India.[52][53] (en.wikipedia.org)
External Links
How To
Six Sigma and Manufacturing
Six Sigma refers to "the application and control of statistical processes (SPC) techniques in order to achieve continuous improvement." Motorola's Quality Improvement Department developed it at their Tokyo plant in Japan in 1986. Six Sigma is a method to improve quality through standardization and elimination of defects. This method has been adopted by many companies in recent years as they believe there are no perfect products or services. Six Sigma seeks to reduce variation between the mean production value. This means that if you take a sample of your product, then measure its performance against the average, you can find out what percentage of the time the process deviates from the norm. If this deviation is too big, you know something needs fixing.
Understanding how your business' variability is a key step towards Six Sigma implementation is the first. Once you've understood that, you'll want to identify sources of variation. It is important to identify whether the variations are random or systemic. Random variations happen when people make errors; systematic variations are caused externally. You could consider random variations if some widgets fall off the assembly lines. If however, you notice that each time you assemble a widget it falls apart in exactly the same spot, that is a problem.
Once you have identified the problem, you can design solutions. This could mean changing your approach or redesigning the entire process. You should then test the changes again after they have been implemented. If they don't work, you will need to go back to the drawing boards and create a new plan.