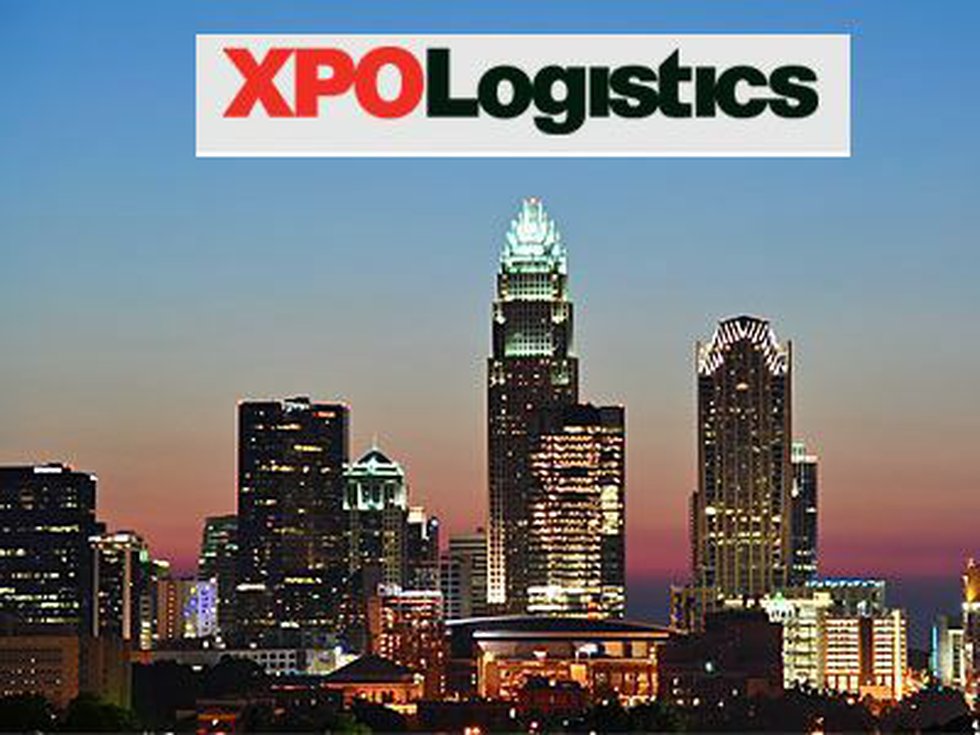
Every five years, for years ending in 2 and 7, the Census Bureau collects detailed statistics about businesses that are essential to understanding the economy. The Economic Census is the foundation for all business and industry statistics.
The Economic Census includes all business establishments. These are surveyed by their primary business activity. Based on their activities and geography, the establishments are classified by industries. This classification is derived by the North American Industry Classification System.
Business Owners and Firms
Business owners and firms can be surveyed on the basis of a firm or company rather than a business. The term "firm" or "company" is used to describe businesses that employ people and who have reported receipts in excess of $1,000 annually. This survey includes sole-proprietorships, nonfarm partnerships and reimbursable firms that are not employers.
Characteristics of business owners and firms
The Census Bureau is conducting the largest survey of small business owners in the country, including minorities and women. In 1969, it was created as a survey for women-owned and minority-owned business. It became part of the economic census of 1972.
The database contains information about over 6,000,000 establishments with a single unit and 1.8,000,000 establishments with multiple units. This information is used in all of the Bureau's programs that collect economic data, such as the Census Bureau Economic Census, County Business Patterns, special summary reports, and non-employer statistics.
Business Register and the Census Bureau's Statistical Abstract of Business Enterprises
SBO or the Statistical Abstract of Business Enterprises is the Census Bureau's principal source of non-employer firm information. This is an extensive multi-relational data base that contains records of each establishment with paid workers in the United States. The data collected are based on firm owners or firms. They are used in the compilation of statistics for programs such as the Economic Census.
SBO also includes statistical measures which are not available through other census programs. For example, the SBO covers establishment births or deaths, new firm launches and shut-downs, and changes in employment. SBO contains information about demographic characteristics, including age and education. It also gives details on home-based business participation and franchises.
SBO Data on Minority and Women-owned Businesses
The Survey of Minority and Women Owned Business, an annual survey of all non-farm businesses, includes those that are registered as partnerships, corporations and sole proprietorships and firms with a minimum of $1,000 in revenue per year. It is an important source of data about women- and minority-owned businesses and gives an annual estimate of the total revenue.
Researchers who study minority and woman-owned businesses will find this resource invaluable. It is also useful in studying the effects that discrimination has on the economy.
FAQ
What are the 7 Rs of logistics.
The acronym 7R's for Logistics stands to represent the seven basic principles in logistics management. It was published in 2004 by the International Association of Business Logisticians as part of their "Seven Principles of Logistics Management" series.
The acronym is composed of the following letters.
-
Responsive - ensure all actions are legal and not harmful to others.
-
Reliable - You can have confidence that you will fulfill your promises.
-
Be responsible - Use resources efficiently and avoid wasting them.
-
Realistic - Consider all aspects of operations, including environmental impact and cost effectiveness.
-
Respectful - Treat people fairly and equitably
-
Resourceful - look for opportunities to save money and increase productivity.
-
Recognizable: Provide customers with value-added service
What are the differences between these four types?
Manufacturing is the process of transforming raw materials into useful products using machines and processes. It can involve many activities like designing, manufacturing, testing packaging, shipping, selling and servicing.
What is production management?
Production Planning refers to the development of a plan for every aspect of production. This document ensures that everything is prepared and available when you are ready for shooting. This document should also include information on how to get the best result on set. This information includes locations, crew details and equipment requirements.
First, you need to plan what you want to film. You may already know where you want the film to be shot, or perhaps you have specific locations and sets you wish to use. Once you have identified your locations and scenes, you can start working out which elements you require for each scene. You might decide you need a car, but not sure what make or model. This is where you can look up car models online and narrow down your options by choosing from different makes and models.
After you have chosen the right car, you will be able to begin thinking about accessories. Are you looking for people to sit in the front seats? You might also need someone to help you get around the back. You might want to change your interior color from black and white. These questions will help you determine the exact look and feel of your car. Another thing you can do is think about what type of shots are desired. You will be filming close-ups and wide angles. Maybe you want the engine or the steering wheels to be shown. These details will help identify the exact car you wish to film.
Once you've determined the above, it is time to start creating a calendar. You can create a schedule that will outline when you must start and finish your shoots. You will need to know when you have to be there, what time you have to leave and when your return home. Everyone will know what they need and when. If you need to hire extra staff, you can make sure you book them in advance. You don't want to hire someone who won't show up because he didn't know.
When creating your schedule, you will also need to consider the number of days you need to film. Some projects take only a few days while others can last several weeks. While creating your schedule, it is important to remember whether you will require more than one shot per day. Shooting multiple takes over the same location will increase costs and take longer to complete. You can't be certain if you will need multiple takes so it is better not to shoot too many.
Another important aspect of production planning is setting budgets. Setting a realistic budget is essential as it will allow you to work within your means. If you have to reduce your budget due to unexpected circumstances, you can always lower it later. It is important to not overestimate how much you will spend. If you underestimate the cost of something, you will have less money left after paying for other items.
Production planning is a very detailed process, but once you understand how everything works together, it becomes easier to plan future projects.
What do we need to know about Manufacturing Processes in order to learn more about Logistics?
No. No. Knowing about manufacturing processes will help you understand how logistics works.
Statistics
- In 2021, an estimated 12.1 million Americans work in the manufacturing sector.6 (investopedia.com)
- In the United States, for example, manufacturing makes up 15% of the economic output. (twi-global.com)
- (2:04) MTO is a production technique wherein products are customized according to customer specifications, and production only starts after an order is received. (oracle.com)
- According to a Statista study, U.S. businesses spent $1.63 trillion on logistics in 2019, moving goods from origin to end user through various supply chain network segments. (netsuite.com)
- [54][55] These are the top 50 countries by the total value of manufacturing output in US dollars for its noted year according to World Bank.[56] (en.wikipedia.org)
External Links
How To
How to use 5S to increase Productivity in Manufacturing
5S stands to stand for "Sort", “Set In Order", “Standardize", and "Store". Toyota Motor Corporation was the first to develop the 5S approach in 1954. It allows companies to improve their work environment, thereby achieving greater efficiency.
This method has the basic goal of standardizing production processes to make them repeatable. This means that tasks such as cleaning, sorting, storing, packing, and labeling are performed daily. These actions allow workers to perform their job more efficiently, knowing what to expect.
Five steps are required to implement 5S: Sort, Set In Order, Standardize. Separate. Each step involves a different action which leads to increased efficiency. If you sort items, it makes them easier to find later. Once you have placed items in an ordered fashion, you will put them together. After you have divided your inventory into groups you can store them in easy-to-reach containers. You can also label your containers to ensure everything is properly labeled.
Employees must be able to critically examine their work practices. Employees should understand why they do the tasks they do, and then decide if there are better ways to accomplish them. They must learn new skills and techniques in order to implement the 5S system.
In addition to improving efficiency, the 5S system also increases morale and teamwork among employees. As they begin to see improvements, they feel motivated to continue working towards the goal of achieving higher levels of efficiency.