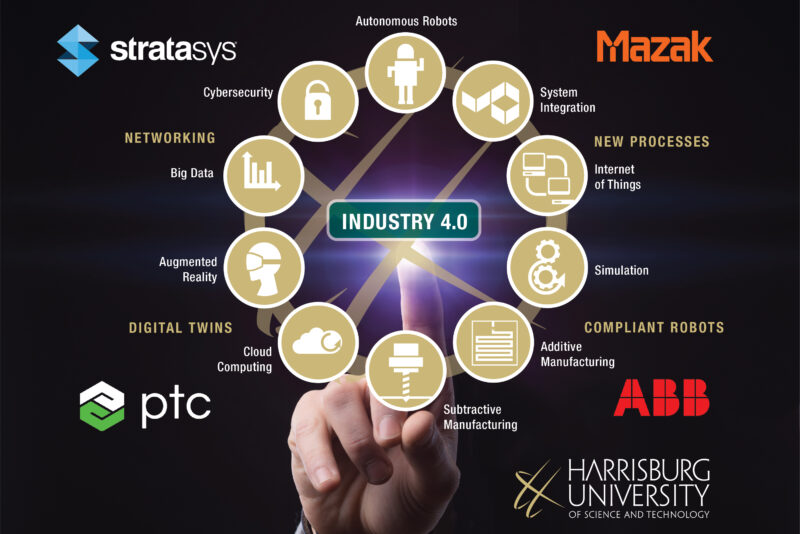
The field of industrial management is engineering in which various engineering processes are combined to create an effective management structure. These engineering processes are integrated into an integrated management system by the industrial manager. Here are some details about the job. These are some of the benefits and requirements to become an industrial manager. If you have the required qualifications and are looking for a challenging and rewarding job, this is the career for you. Continue reading to find out more.
Job description
An industrial manager is responsible for overseeing the production and manufacturing of goods and services. Although the job is broad, it may also cover specific aspects such as how to source raw materials and use equipment. Computer literacy is essential for industrial production managers, who must be able to use computers to coordinate the work of different departments, suppliers, clients, and other parties. Industrial production managers should also be conversant in the most recent production technologies and management procedures. Many managers take part in professional organizations, attend tradeshows and conferences in the industry, and enroll in courses to earn certification.
Industrial managers coordinate all activities within a company, in addition to supervising production processes. They make sure that production lines run smoothly and meet customer demands in terms of quality, time and delivery. They also oversee the staffing levels and make changes to production levels if necessary to reduce inventory. They may coordinate communication with suppliers or other departments, and supervise quality control programs. Majority of their responsibilities involve managing people. This involves identifying, training, motivating and motivating employees.
Education is necessary
For industrial managers, a bachelor's level in business administration, management, engineering or other related fields is not enough. Employers will prefer candidates who have a background in one or more of these fields. Also, industrial managers must be computer-literate. Computers are becoming increasingly essential in the manufacturing process. They help coordinate production between departments, suppliers, clients, and other parties. To excel in this field, interested individuals need to have the right education and experience.
Many industrial production managers started their careers as production workers before moving up to the first-line supervisory position. To advance to an industrial manager position, most professionals must earn a college degree in business management. However, there are some workers who can get this education on the jobs. Or they might choose to go to classes sponsored and paid by their company. Managers are expected to have at least two to five years' experience in the relevant field before they can become managers.
Earning potential
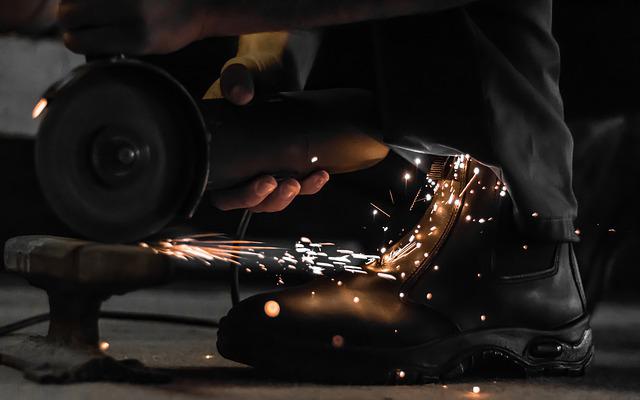
In manufacturing plants, industrial managers oversee the smooth running of the entire operation. They decide how to best utilize employees and equipment, meet production standards, and make strategic decisions. These people are responsible for evaluating and hiring workers. They also set production schedules and ensure safety. They supervise the day-today activities of a workforce and monitor the entire production process to ensure it operates efficiently and at peak efficiency.
The ability to earn an industrial production manager's salary depends on the experience of the worker and the employer. Although it's hard for anyone to predict what the future earnings will be, the median industrial manager salary was $103,380 as of May 2016. The highest paid industrial production workers earned $172,000. High-skilled industrial production managers may earn more if they have been certified and received additional training. According to the U.S. Bureau of Labor Statistics, industrial production managers who have earned a bachelor's degree or higher may earn more.
Environment for work
An industrial production manager divides her or his time between the production area and the office. When they work in a production zone, industrial production managers need to adhere to safety and health guidelines and use appropriate protective equipment. They spend a lot of time meeting with their subordinates and analysing production data. These managers might also create reports. Industrial production managers often work in dynamic environments.
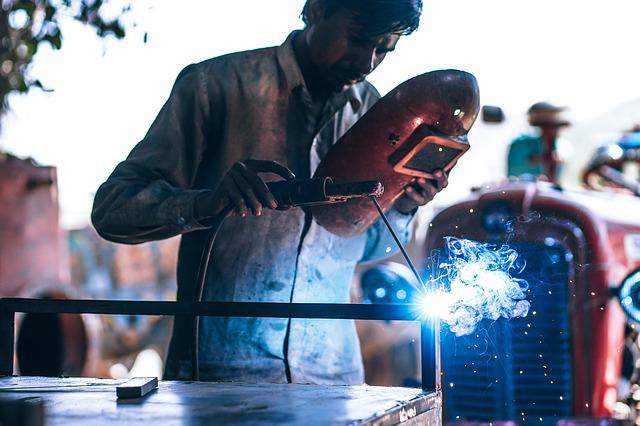
Industrial production managers play a key role in a company's overall management structure. They are responsible for coordinating the activities of workers and increasing productivity. A primary responsibility of an industrial production manager is increasing productivity and ensuring safety. Corporate restructuring has seen many levels of management eliminated and support staff cut, which means that production managers have more to do. This is a serious challenge for any manager and can make the job of a production manager difficult.
FAQ
What are my options for learning more about manufacturing
Hands-on experience is the best way to learn more about manufacturing. If that is not possible, you could always read books or view educational videos.
How can we increase manufacturing efficiency?
The first step is to determine the key factors that impact production time. We then need to figure out how to improve these variables. You can start by identifying the most important factors that impact production time. Once you have identified the factors, then try to find solutions.
How can we reduce manufacturing overproduction?
In order to reduce excess production, you need to develop better inventory management methods. This would reduce the time needed to manage inventory. We could use these resources to do other productive tasks.
This can be done by using a Kanban system. A Kanban Board is a visual display that tracks work progress. Work items are moved through various states to reach their destination in a Kanban system. Each state represents a different priority level.
When work is completed, it can be transferred to the next stage. A task that is still in the initial stages of a process will be considered complete until it moves on to the next stage.
This allows work to move forward and ensures that no work is missed. A Kanban board allows managers to monitor how much work is being completed at any given moment. This data allows them adjust their workflow based upon real-time data.
Lean manufacturing is another option to control inventory levels. Lean manufacturing works to eliminate waste throughout every stage of the production chain. Anything that does nothing to add value to a product is waste. Here are some examples of common types.
-
Overproduction
-
Inventory
-
Packaging not required
-
Materials in excess
These ideas will help manufacturers increase efficiency and lower costs.
What does it mean to be a manufacturer?
Manufacturing Industries is a group of businesses that produce goods for sale. Consumers are the people who purchase these products. This is accomplished by using a variety of processes, including production, distribution and retailing. They make goods from raw materials with machines and other equipment. This covers all types of manufactured goods including clothing, food, building supplies and furniture, as well as electronics, tools, machinery, vehicles and pharmaceuticals.
What is the job of a production plan?
A production planner makes sure all project elements are delivered on schedule, within budget, as well as within the agreed scope. They make sure that the product and services meet client expectations.
What are the responsibilities of a manufacturing manager
The manufacturing manager should ensure that every manufacturing process is efficient and effective. They should also be aware and responsive to any company problems.
They must also be able to communicate with sales and marketing departments.
They should also be aware of the latest trends in their industry and be able to use this information to help improve productivity and efficiency.
Statistics
- In the United States, for example, manufacturing makes up 15% of the economic output. (twi-global.com)
- You can multiply the result by 100 to get the total percent of monthly overhead. (investopedia.com)
- Job #1 is delivering the ordered product according to specifications: color, size, brand, and quantity. (netsuite.com)
- It's estimated that 10.8% of the U.S. GDP in 2020 was contributed to manufacturing. (investopedia.com)
- According to a Statista study, U.S. businesses spent $1.63 trillion on logistics in 2019, moving goods from origin to end user through various supply chain network segments. (netsuite.com)
External Links
How To
How to use the Just-In Time Method in Production
Just-intime (JIT), a method used to lower costs and improve efficiency in business processes, is called just-in-time. It allows you to get the right amount resources at the right time. This means that you only pay the amount you actually use. The term was first coined by Frederick Taylor, who developed his theory while working as a foreman in the early 1900s. Taylor observed that overtime was paid to workers if they were late in working. He decided that workers would be more productive if they had enough time to complete their work before they started to work.
JIT is an acronym that means you need to plan ahead so you don’t waste your money. The entire project should be looked at from start to finish. You need to ensure you have enough resources to tackle any issues that might arise. You can anticipate problems and have enough equipment and people available to fix them. You won't have to pay more for unnecessary items.
There are many types of JIT methods.
-
Demand-driven JIT: This is a JIT that allows you to regularly order the parts/materials necessary for your project. This will let you track the amount of material left over after you've used it. This will allow you to calculate how long it will take to make more.
-
Inventory-based: This is a type where you stock the materials required for your projects in advance. This allows for you to anticipate how much you can sell.
-
Project-driven : This is a method where you make sure that enough money is set aside to pay the project's cost. When you know how much you need, you'll purchase the appropriate amount of materials.
-
Resource-based: This is the most common form of JIT. Here, you allocate certain resources based on demand. For example, if there is a lot of work coming in, you will have more people assigned to them. You'll have fewer orders if you have fewer.
-
Cost-based: This is the same as resource-based except that you don't care how many people there are but how much each one of them costs.
-
Price-based: This is very similar to cost-based, except that instead of looking at how much each individual worker costs, you look at the overall price of the company.
-
Material-based: This approach is similar to cost-based. However, instead of looking at the total cost for the company, you look at how much you spend on average on raw materials.
-
Time-based JIT is another form of resource-based JIT. Instead of worrying about how much each worker costs, you can focus on how long the project takes.
-
Quality-based JIT - This is another form of resource-based JIT. Instead of thinking about how much each employee costs or how long it takes to manufacture something, you think about how good the quality of your product is.
-
Value-based JIT: One of the most recent forms of JIT. In this case, you're not concerned with how well the products perform or whether they meet customer expectations. Instead, you're focused on how much value you add to the market.
-
Stock-based. This method is inventory-based and focuses only on the actual production at any given point. It's useful when you want maximum production and minimal inventory.
-
Just-in-time (JIT) planning: This is a combination of JIT and supply chain management. It refers to the process of scheduling the delivery of components as soon as they are ordered. This is important as it reduces lead time and increases throughput.