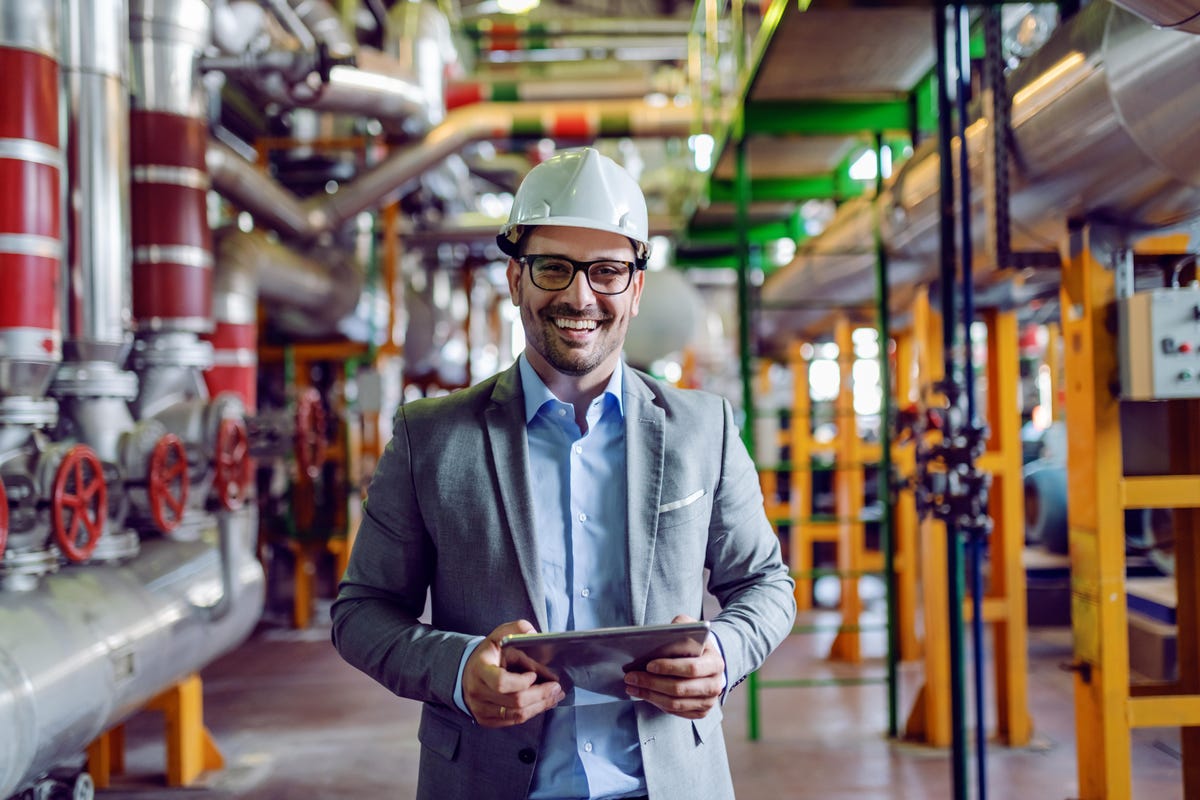
Alaska logistics services can be challenging. Alaska is a challenging place because of its unique climate and rugged terrain. This state is also one the least populous in the United States. Due to this, transportation options can be limited in certain months. Fortunately, Alaska is home to a wide array of logistics companies that can help to move your goods around the state. These services include freight forwarding and intermodal transport.
Port of Alaska is Alaska's largest logistics provider. This gateway serves approximately 85% state residents. It is the only reliable gateway to large-volume freight delivery to Anchorage or Fairbanks. Port of Alaska, in addition to being a major hub of cargo transportation, also supports the seafood business.
CP Logistics is another Alaska logistics provider with a significant impact. This company provides supply-chain management services across the United States as well as Canada and the Caribbean. The company relies on third-party audits for quality and safety. The company also has a strong SQF food safety program. The company has recently made a name for itself in the logistics industry by offering a mobile app that gives real-time shipment information.
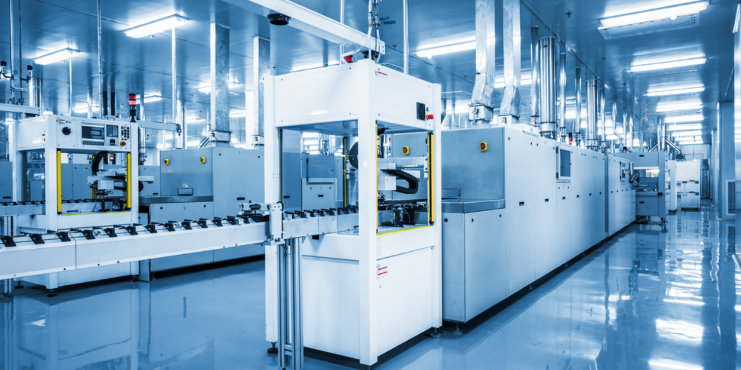
Carlile Logistics is another logistics company worth looking into. The company is a provider of truck cabs, fuel tanksers and cargo trailers. The company is part in the Saltchuk Resources network of companies. It places an emphasis on innovation and technology. The company is located in Alaska and supports many different projects, including oil exploration and building projects. The company also adapts to the changing needs of its clients.
Another noteworthy logistics company in Alaska is PRL Logistics Inc. This company provides logistical support for Gallagher Marine Systems. They have a long history of providing logistics support in Alaska. They have worked alongside companies like PenAir, Bristow Aviation, DHL, and Bristow Aviation. Their team has even worked in the Aleutians and Southeast.
Alaska Logistics, LLC, another logistics company has made a huge splash in Alaska. Alaska Logistics, LLC provides container and barge transportation for customers in Alaska. Additionally, they now offer transportation of other cargo types. They can transport bulk commodities, containers and sanitary bulk commodities. They provide service to Western Alaska ports and surrounding villages.
A strong reputation for quality service is the most important thing about any Alaska logistics company. It is essential to be prepared for any eventuality. Alaska is home of some of most extreme weather. It is susceptible to flooding and volcanic eruptions that can cause serious damage. A limited highway system is another problem. As a result, logistics providers need to be prepared to handle all of the state's logistical challenges.
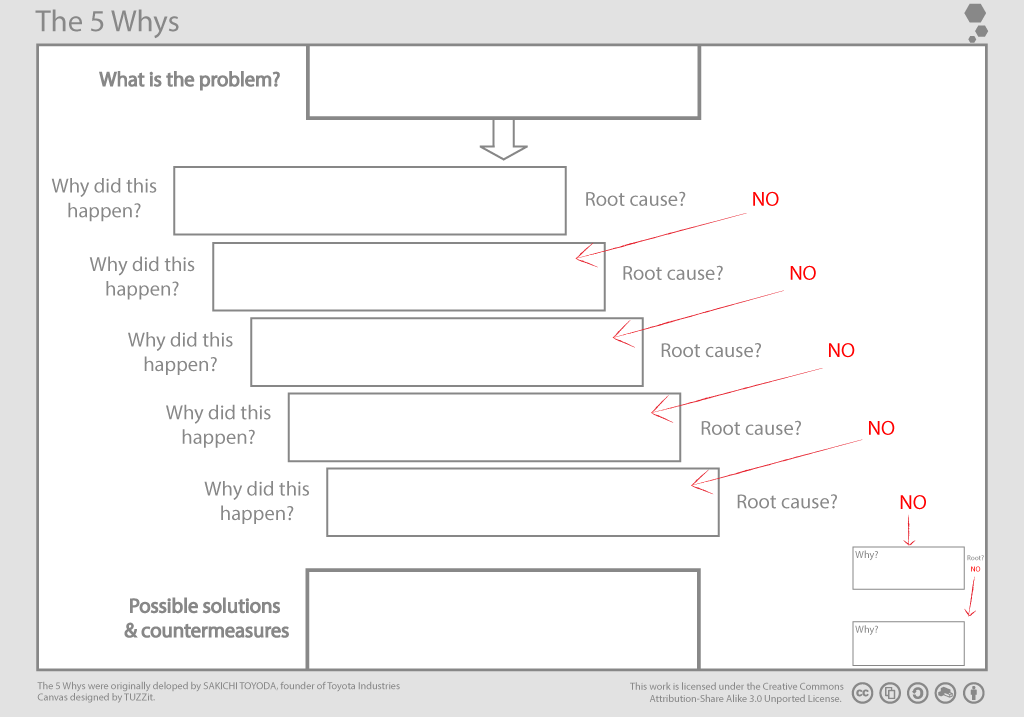
Finally, moving cement in Alaska is one of the most difficult logistical problems. Cement is essential for construction projects and must be transported by air. It is necessary to plan ahead, but you must be able to complete the task.
FAQ
How can efficiency in manufacturing be improved?
First, determine which factors have the greatest impact on production time. Next, we must find ways to improve those factors. You can start by identifying the most important factors that impact production time. Once you have identified them, it is time to identify solutions.
What skills is required for a production planner?
You must be flexible and organized to become a productive production planner. Effective communication with clients and colleagues is essential.
Why automate your warehouse
Automation has become increasingly important in modern warehousing. With the rise of ecommerce, there is a greater demand for faster delivery times as well as more efficient processes.
Warehouses should be able adapt quickly to new needs. They must invest heavily in technology to do this. Automation of warehouses offers many benefits. These are some of the benefits that automation can bring to warehouses:
-
Increases throughput/productivity
-
Reduces errors
-
Increases accuracy
-
Safety Boosts
-
Eliminates bottlenecks
-
Companies can scale up more easily
-
It makes workers more efficient
-
The warehouse can be viewed from all angles.
-
Enhances customer experience
-
Improves employee satisfaction
-
Reduces downtime and improves uptime
-
You can be sure that high-quality products will arrive on time
-
Removes human error
-
It helps ensure compliance with regulations
What does it take to run a logistics business?
A successful logistics business requires a lot more than just knowledge. For clients and suppliers to be successful, you need to have excellent communication skills. It is important to be able to analyse data and draw conclusions. You will need to be able handle pressure well and work in stressful situations. In order to innovate and create new ways to improve efficiency, creativity is essential. To motivate and guide your team towards reaching organizational goals, you must have strong leadership skills.
You must be organized to meet tight deadlines.
What kind of jobs are there in logistics?
Logistics can offer many different jobs. These are some of the jobs available in logistics:
-
Warehouse workers – They load and unload pallets and trucks.
-
Transportation drivers – They drive trucks or trailers to transport goods and perform pick-ups.
-
Freight handlers, - They sort out and pack freight in warehouses.
-
Inventory managers – These people oversee inventory at warehouses.
-
Sales reps are people who sell products to customers.
-
Logistics coordinators - They plan and organize logistics operations.
-
Purchasing agents: They are responsible for purchasing goods and services to support company operations.
-
Customer service representatives are available to answer customer calls and emails.
-
Shipping clerks – They process shipping orders, and issue bills.
-
Order fillers - These people fill orders based on what has been ordered.
-
Quality control inspectors (QCI) - They inspect all incoming and departing products for potential defects.
-
Others – There are many other types available in logistics. They include transport supervisors, cargo specialists and others.
What is the difference in Production Planning and Scheduling, you ask?
Production Planning (PP), or production planning, is the process by which you determine what products are needed at any given time. Forecasting and identifying production capacity are two key elements to this process.
Scheduling refers to the process of allocating specific dates to tasks in order that they can be completed within a specified timeframe.
Statistics
- In 2021, an estimated 12.1 million Americans work in the manufacturing sector.6 (investopedia.com)
- In the United States, for example, manufacturing makes up 15% of the economic output. (twi-global.com)
- Job #1 is delivering the ordered product according to specifications: color, size, brand, and quantity. (netsuite.com)
- According to a Statista study, U.S. businesses spent $1.63 trillion on logistics in 2019, moving goods from origin to end user through various supply chain network segments. (netsuite.com)
- It's estimated that 10.8% of the U.S. GDP in 2020 was contributed to manufacturing. (investopedia.com)
External Links
How To
How to use lean manufacturing in the production of goods
Lean manufacturing refers to a method of managing that seeks to improve efficiency and decrease waste. It was developed in Japan during the 1970s and 1980s by Taiichi Ohno, who received the Toyota Production System (TPS) award from TPS founder Kanji Toyoda. Michael L. Watkins published the "The Machine That Changed the World", the first book about lean manufacturing. It was published in 1990.
Lean manufacturing is often described as a set if principles that help improve the quality and speed of products and services. It emphasizes reducing defects and eliminating waste throughout the value chain. Lean manufacturing is also known as just in time (JIT), zero defect total productive maintenance(TPM), and five-star (S). Lean manufacturing is about eliminating activities that do not add value, such as inspection, rework, and waiting.
Lean manufacturing not only improves product quality but also reduces costs. Companies can also achieve their goals faster by reducing employee turnover. Lean manufacturing can be used to manage all aspects of the value chain. Customers, suppliers, distributors, retailers and employees are all included. Lean manufacturing practices are widespread in many industries. Toyota's philosophy is the foundation of its success in automotives, electronics and appliances, healthcare, chemical engineers, aerospace, paper and food, among other industries.
Five principles are the basis of lean manufacturing:
-
Define Value- Identify the added value your company brings to society. What makes you stand out from your competitors?
-
Reduce Waste - Eliminate any activity that doesn't add value along the supply chain.
-
Create Flow. Ensure that your work is uninterrupted and flows seamlessly.
-
Standardize & Simplify - Make processes as consistent and repeatable as possible.
-
Build Relationships- Develop personal relationships with both internal as well as external stakeholders.
Lean manufacturing, although not new, has seen renewed interest in the economic sector since 2008. Many businesses are now using lean manufacturing to improve their competitiveness. Many economists believe lean manufacturing will play a major role in economic recovery.
Lean manufacturing, which has many benefits, is now a standard practice in the automotive industry. These include better customer satisfaction and lower inventory levels. They also result in lower operating costs.
You can apply Lean Manufacturing to virtually any aspect of your organization. It is especially useful for the production aspect of an organization, as it ensures that every step in the value chain is efficient and effective.
There are three main types in lean manufacturing
-
Just-in-Time Manufacturing (JIT): This type of lean manufacturing is commonly referred to as "pull systems." JIT means that components are assembled at the time of use and not manufactured in advance. This method reduces lead times, increases availability, and decreases inventory.
-
Zero Defects Manufacturing (ZDM),: ZDM is a system that ensures no defective units are left the manufacturing facility. You should repair any part that needs to be repaired during an assembly line. This also applies to finished products that need minor repairs before being shipped.
-
Continuous Improvement (CI), also known as Continuous Improvement, aims at improving the efficiency of operations through continuous identification and improvement to minimize or eliminate waste. Continuous improvement involves continuous improvement of processes and people as well as tools.