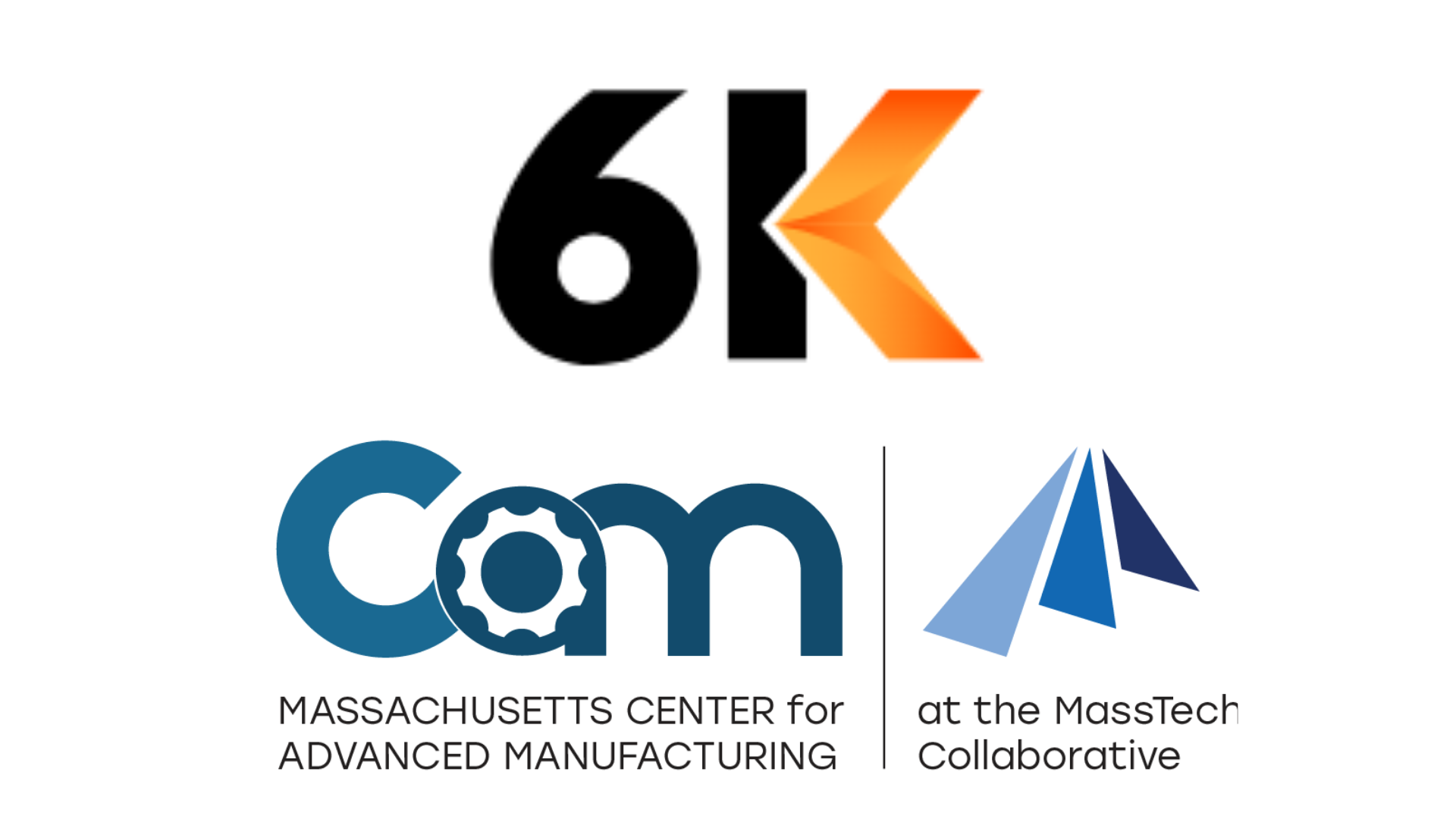
The United States' manufacturing sector is growing. The US is currently the third-largest country to produce goods. The total manufacturing output hit a record high in Q1 2018, exceeding $1.95 trillion, and is on course to exceed that high by 2022. This is due a variety of factors, including automation growth and productivity growth.
Institutes of High Wage America
High wage America is an initiative to create high-wage jobs and improve the economy. The slow recovery of the United States from the Great Recession has been accompanied by high levels and low wages. But, there are ways out of the current low-wage crisis. State and local stakeholders can create an agenda to promote high-wage jobs in order to improve the American workforce's current situation.
The first step is to develop a sustainable manufacturing approach. A plan must be developed to combat wage stagnation, poor working conditions and lack of training. To make this happen, the United States must combat unfair trade practices and adopt policies that will support manufacturing communities.
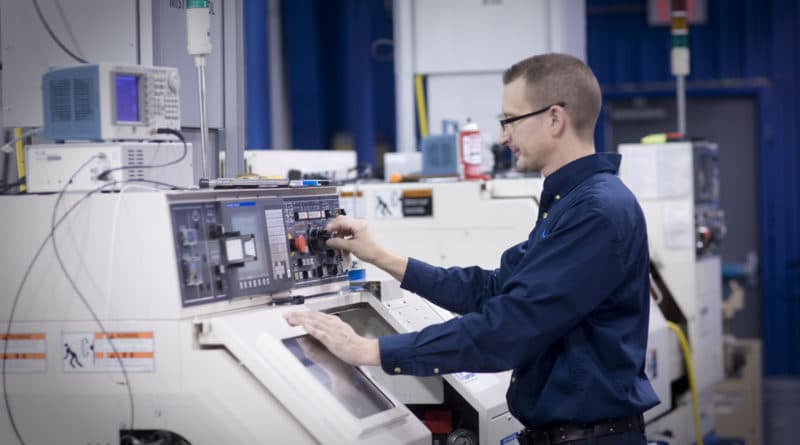
Automated manufacturing technologies
It is clear that automation technologies have revolutionized the way we produce products. Automation has dramatically reduced costs and increased profits for both workers and companies. The US government has a positive impact on the development of new technology through its policy. In fact, government policies can help businesses grow by encouraging the development of new technologies, and creating jobs in the process.
The US's first introduction of automated manufacturing was in the early 1900s when Ford Motor Company built its first car assembly line. This was the first of its kind in the world and greatly improved Ford's production rate. This reduced the time it took to build a car from 12 hours to around one and a quarter hours.
Productivity growth
There are many factors that point to manufacturing productivity growth. Across many industries, large gaps between the best run companies and the rest of the industry indicate that productivity growth can be achieved. As is the availability of technology and mobility that allows production to be moved from one location to another, it is vital to increase infrastructure investment. The output divided by the inputs (most commonly labor hours) is how productivity is measured. Outputs can also be measured by units sold, produced, or both.
The most commonly used way to measure productivity is labor productivity. This measure compares output to hours worked. The labor productivity measure can be broken down into different sectors, wages, or technological advancement. Increased productivity directly impacts company profits. Companies that are more efficient in their production processes produce more output per hour of employee labor.
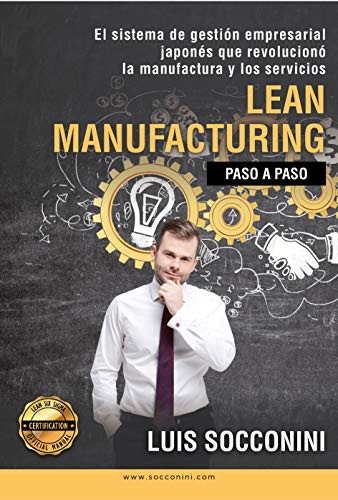
Outsourcing impacts
There are multiple ways that outsourcing can impact manufacturing in the United States. Some outsourcing can be advantageous, as it allows the country's labor costs to be lower and allows them to compete with other countries. In other cases, outsourcing has the opposite effect, causing the loss of American jobs. Sometimes, outsourcing can result in American jobs being replaced with foreign workers. Other times, it can lead American workers to earn lower wages.
Outsourcing began with American companies. It then spread to other countries. In order to cut costs, some companies decided to eliminate all of their "core" activities. Companies like Sodexo (which provides food service), IBM and UPS were all affected. Companies like Foxconn, which manufactures computers, also started outsourcing. Apple is just one of many companies that outsource their entire manufacturing.
FAQ
Is it possible to automate certain parts of manufacturing
Yes! Yes. The Egyptians discovered the wheel thousands and years ago. We now use robots to help us with assembly lines.
There are many applications for robotics in manufacturing today. They include:
-
Robots for assembly line
-
Robot welding
-
Robot painting
-
Robotics inspection
-
Robots create products
Manufacturing could also benefit from automation in other ways. 3D printing, for example, allows us to create custom products without waiting for them to be made.
How can manufacturing avoid production bottlenecks
Avoiding production bottlenecks is as simple as keeping all processes running smoothly, from the time an order is received until the product ships.
This includes planning for capacity requirements as well as quality control measures.
Continuous improvement techniques such Six Sigma can help you achieve this.
Six Sigma is a management method that helps to improve quality and reduce waste.
It focuses on eliminating variation and creating consistency in your work.
What are the 4 types of manufacturing?
Manufacturing is the process of transforming raw materials into useful products using machines and processes. It involves many different activities such as designing, building, testing, packaging, shipping, selling, servicing, etc.
Statistics
- [54][55] These are the top 50 countries by the total value of manufacturing output in US dollars for its noted year according to World Bank.[56] (en.wikipedia.org)
- Many factories witnessed a 30% increase in output due to the shift to electric motors. (en.wikipedia.org)
- (2:04) MTO is a production technique wherein products are customized according to customer specifications, and production only starts after an order is received. (oracle.com)
- Job #1 is delivering the ordered product according to specifications: color, size, brand, and quantity. (netsuite.com)
- According to the United Nations Industrial Development Organization (UNIDO), China is the top manufacturer worldwide by 2019 output, producing 28.7% of the total global manufacturing output, followed by the United States, Japan, Germany, and India.[52][53] (en.wikipedia.org)
External Links
How To
How to Use Lean Manufacturing for the Production of Goods
Lean manufacturing is an approach to management that aims for efficiency and waste reduction. It was first developed in Japan in the 1970s/80s by Taiichi Ahno, who was awarded the Toyota Production System (TPS), award from KanjiToyoda, the founder of TPS. Michael L. Watkins published the book "The Machine That Changed the World", which was the first to be published about lean manufacturing.
Lean manufacturing is often defined as a set of principles used to improve the quality, speed, and cost of products and services. It emphasizes the elimination of defects and waste throughout the value stream. Lean manufacturing is called just-in-time (JIT), zero defect, total productive maintenance (TPM), or 5S. Lean manufacturing focuses on eliminating non-value-added activities such as rework, inspection, and waiting.
Lean manufacturing can help companies improve their product quality and reduce costs. Additionally, it helps them achieve their goals more quickly and reduces employee turnover. Lean manufacturing is a great way to manage the entire value chain including customers, suppliers, distributors and retailers as well as employees. Lean manufacturing is widely practiced in many industries around the world. Toyota's philosophy has been a key driver of success in many industries, including automobiles and electronics.
Lean manufacturing is based on five principles:
-
Define Value - Identify the value your business adds to society and what makes you different from competitors.
-
Reduce waste - Get rid of any activity that does not add value to the supply chain.
-
Create Flow - Ensure work moves smoothly through the process without interruption.
-
Standardize & simplify - Make processes consistent and repeatable.
-
Develop Relationships: Establish personal relationships both with internal and external stakeholders.
Although lean manufacturing has always been around, it is gaining popularity in recent years because of a renewed interest for the economy after 2008's global financial crisis. Many businesses have adopted lean manufacturing techniques to help them become more competitive. Economists think that lean manufacturing is a crucial factor in economic recovery.
With many benefits, lean manufacturing is becoming more common in the automotive industry. These include higher customer satisfaction levels, reduced inventory levels as well as lower operating costs.
Any aspect of an enterprise can benefit from Lean manufacturing. Because it makes sure that all value chains are efficient and effectively managed, Lean Manufacturing is particularly helpful for organizations.
There are three types principally of lean manufacturing:
-
Just-in-Time Manufacturing: Also known as "pull systems", this type of lean manufacturing uses just-in-time manufacturing (JIT). JIT is a method in which components are assembled right at the moment of use, rather than being manufactured ahead of time. This approach aims to reduce lead times, increase the availability of parts, and reduce inventory.
-
Zero Defects Manufacturing (ZDM): ZDM focuses on ensuring that no defective units leave the manufacturing facility. You should repair any part that needs to be repaired during an assembly line. This also applies to finished products that need minor repairs before being shipped.
-
Continuous Improvement: Continuous Improvement aims to improve efficiency by continually identifying problems and making adjustments to eliminate or minimize waste. Continuous Improvement (CI) involves continuous improvement in processes, people, tools, and infrastructure.