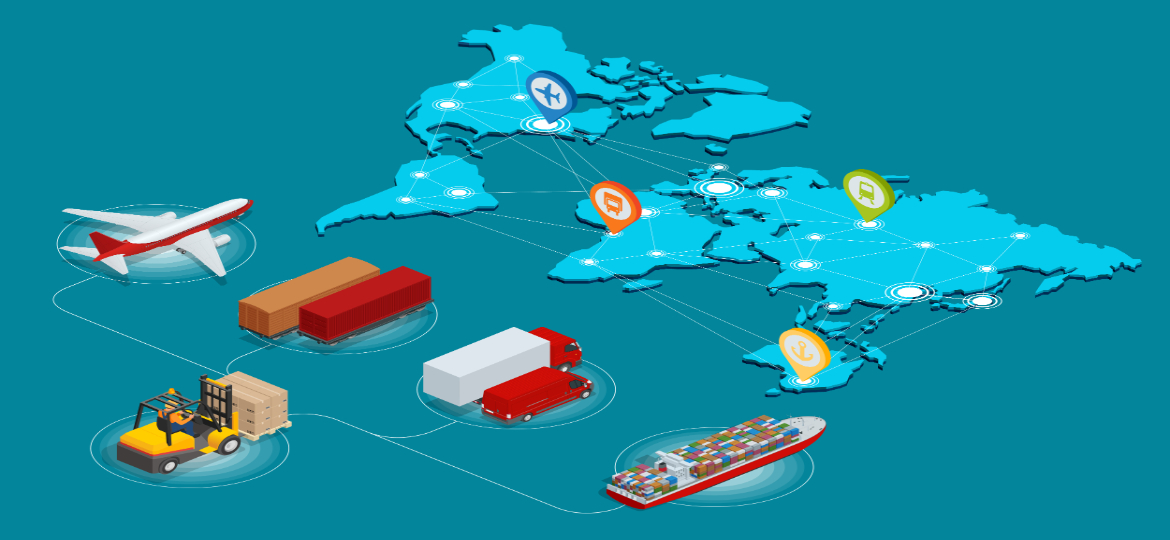
Andon in lean manufacturing is a visual signal that identifies and highlights problems with the goal of fixing them long-term. It's a tool to empower plant floor operators, and speed up teamwork.
Andon
) is a Japanese-derived word, which comes from the fixed paper lanterns used between the Edo period (17th century to 19th century). In Japanese it can also refer to the system of attaching light signals and sounds to specific processes in order to alert employees.
Toyota uses the term as a key principle for its Jidoka, or build-in quality, which is an important component of their TPS (Toyota Production System). It is often cited in the US as the origin of a concept which allows employees on the production line to stop it if there are safety or quality problems.
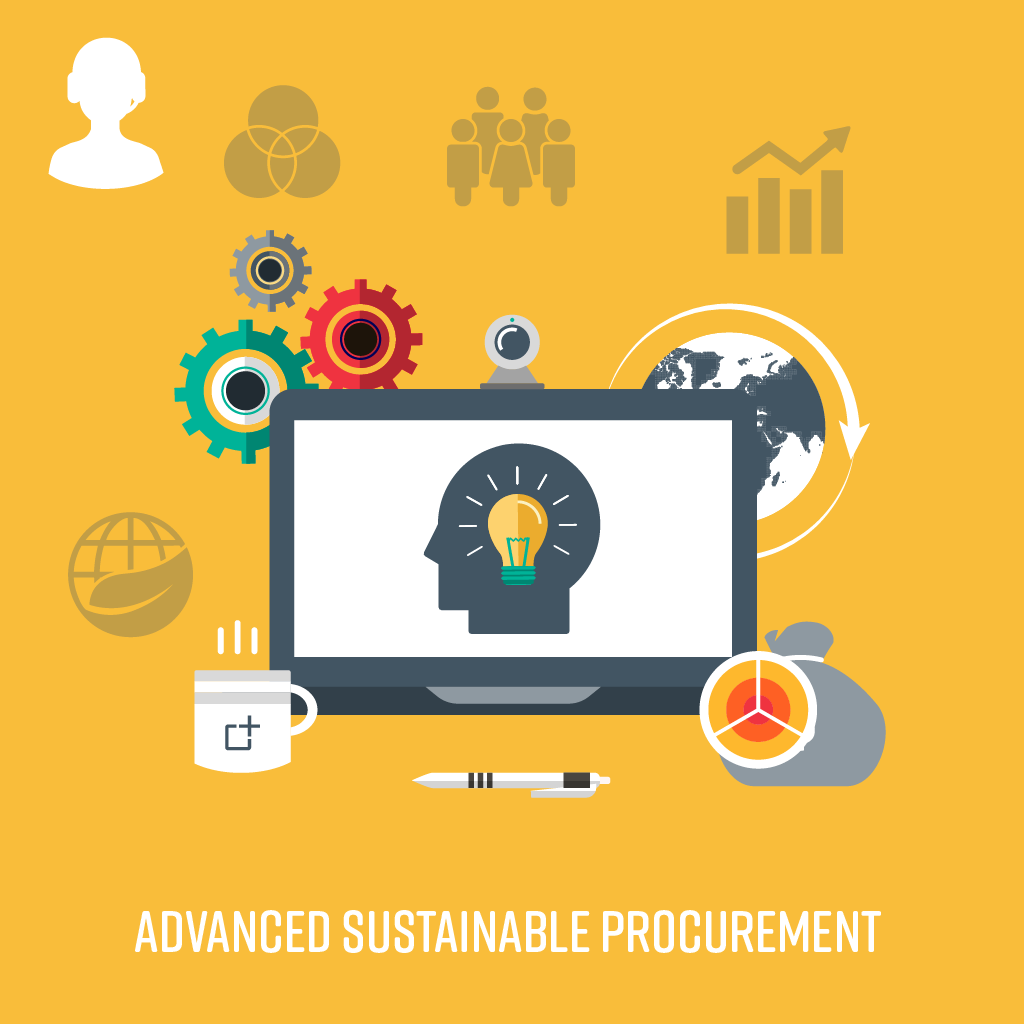
What is andon?
Andon is a lean manufacturing system that was pioneered by Toyota. It is a simple, straightforward system consisting of a board that has green, red and yellow lights. Each color signifies a specific state of production. When the green lights are on, the production is going smoothly. The yellow light means that the problem has been identified and is being dealt with. When the red light is lit, all production stops. Workers may take a short break, prepare spare parts, ask for help or even fill their bins.
The Andon Board is simple to use, and supervisors are able to immediately understand what has happened. The system is designed to provide immediate feedback and ensure all problems are resolved as soon as possible.
There are a variety of types of andons. But the most common is an alerting red light accompanied by a buzzer. These systems can be used to identify issues that may cause downtime or repeat problems.
An effective andon board can help to keep the production running in case of a malfunction. It is an easy-to-use tool that improves productivity, reduces downtimes, and increases product quality and safety.
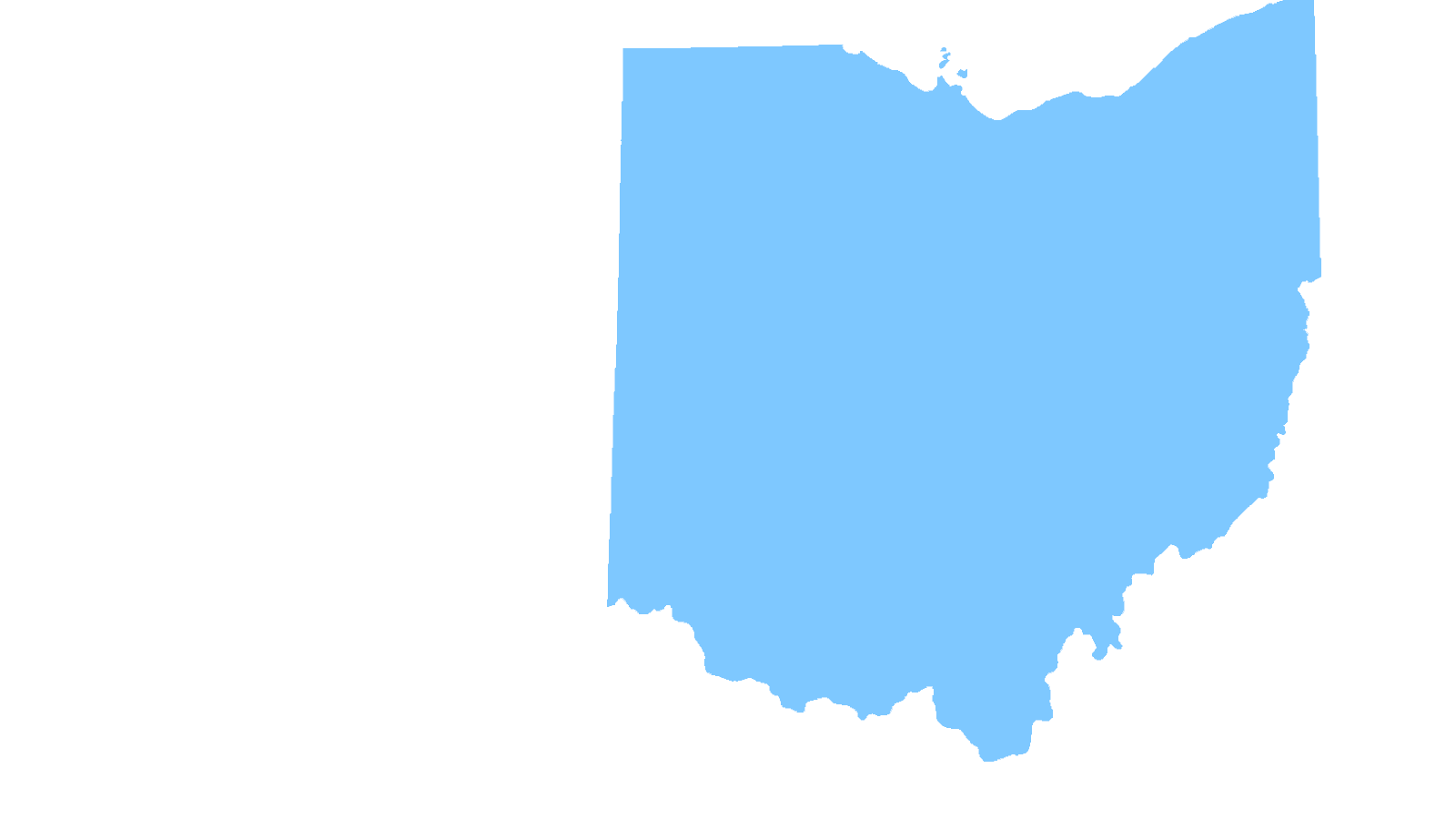
What is anon toyota?
Toyota has a special cord which any employee can pull when they see a possible issue with their car. If a worker felt the car was compromised, they could instantly stop the production line by pulling this cord.
Modern andon systems also use technology to curate information, which makes it easier to identify emerging problems, send notifications to stakeholders in real-time, and determine the root cause of a problem that requires a long term fix. Human touch is essential to interpret and act upon this information.
How to make andon work?
First, it's crucial to create an environment where employees and managers do not hesitate to identify or address problems. The more they are hesitant, the more they're likely to conceal problems and miss a chance to fix them. Line stops can help improve this by encouraging workers to press the button and pull out the cord when they detect a problem.
FAQ
What is the difference in Production Planning and Scheduling, you ask?
Production Planning (PP) refers to the process of determining how much production is needed at any given moment. This can be done by forecasting demand and identifying production capabilities.
Scheduling involves the assignment of dates and times to tasks in order to complete them within the timeframe.
Why automate your warehouse
Modern warehousing is becoming more automated. The rise of e-commerce has led to increased demand for faster delivery times and more efficient processes.
Warehouses should be able adapt quickly to new needs. Technology investment is necessary to enable warehouses to respond quickly to changing demands. Automation of warehouses offers many benefits. Here are some of the reasons automation is worth your investment:
-
Increases throughput/productivity
-
Reduces errors
-
Increases accuracy
-
Safety Boosts
-
Eliminates bottlenecks
-
Companies can scale up more easily
-
Increases efficiency of workers
-
It gives visibility to everything that happens inside the warehouse
-
Enhances customer experience
-
Improves employee satisfaction
-
Reducing downtime and increasing uptime
-
Quality products delivered on time
-
Removes human error
-
This helps to ensure compliance with regulations
What does "warehouse" mean?
A warehouse or storage facility is where goods are stored before they are sold. It can be indoors or out. It may also be an indoor space or an outdoor area.
Is there anything we should know about Manufacturing Processes prior to learning about Logistics.
No. It doesn't matter if you don't know anything about manufacturing before you learn about logistics. But, being familiar with manufacturing processes will give you a better understanding about how logistics works.
What skills should a production planner have?
Production planners must be flexible, organized, and able handle multiple tasks. Effective communication with clients and colleagues is essential.
What is the importance of automation in manufacturing?
Automation is essential for both manufacturers and service providers. It allows them provide faster and more efficient services. They can also reduce their costs by reducing human error and improving productivity.
What is meant by manufacturing industries?
Manufacturing Industries refers to businesses that manufacture products. These products are sold to consumers. These companies employ many processes to achieve this purpose, such as production and distribution, retailing, management and so on. They produce goods from raw materials by using machines and other machinery. This includes all types manufactured goods such as clothing, building materials, furniture, electronics, tools and machinery.
Statistics
- [54][55] These are the top 50 countries by the total value of manufacturing output in US dollars for its noted year according to World Bank.[56] (en.wikipedia.org)
- According to a Statista study, U.S. businesses spent $1.63 trillion on logistics in 2019, moving goods from origin to end user through various supply chain network segments. (netsuite.com)
- According to the United Nations Industrial Development Organization (UNIDO), China is the top manufacturer worldwide by 2019 output, producing 28.7% of the total global manufacturing output, followed by the United States, Japan, Germany, and India.[52][53] (en.wikipedia.org)
- You can multiply the result by 100 to get the total percent of monthly overhead. (investopedia.com)
- Many factories witnessed a 30% increase in output due to the shift to electric motors. (en.wikipedia.org)
External Links
How To
How to use 5S to increase Productivity in Manufacturing
5S stands to stand for "Sort", “Set In Order", “Standardize", and "Store". Toyota Motor Corporation was the first to develop the 5S approach in 1954. It allows companies to improve their work environment, thereby achieving greater efficiency.
This method aims to standardize production processes so that they are repeatable, measurable and predictable. This means that every day tasks such cleaning, sorting/storing, packing, and labeling can be performed. This knowledge allows workers to be more efficient in their work because they are aware of what to expect.
Implementing 5S involves five steps: Sort, Set in Order, Standardize Separate, Store, and Each step requires a different action, which increases efficiency. Sorting things makes it easier to find them later. When items are ordered, they are put together. Once you have separated your inventory into groups and organized them, you will store these groups in easily accessible containers. Finally, label all containers correctly.
Employees must be able to critically examine their work practices. Employees should understand why they do the tasks they do, and then decide if there are better ways to accomplish them. In order to use the 5S system effectively, they must be able to learn new skills.
The 5S method increases efficiency and morale among employees. As they begin to see improvements, they feel motivated to continue working towards the goal of achieving higher levels of efficiency.