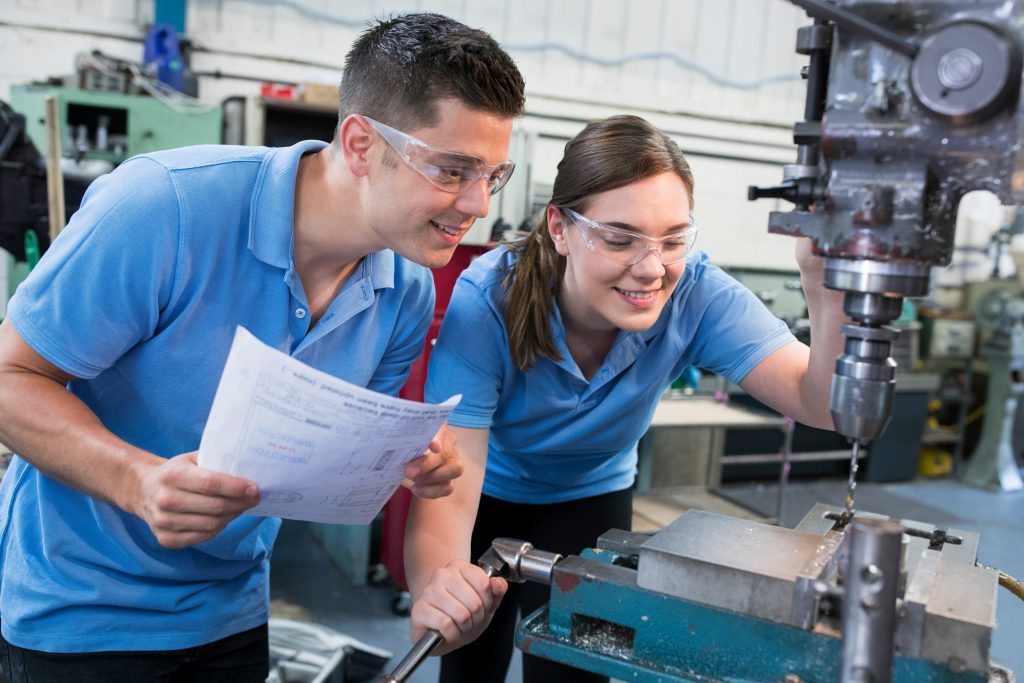
It all depends on where you work, what you do, and how much. Some of the highest paying companies include Apple, ConocoPhillips, Meta and Western Digital. Other places, like FedEx or Motorola Solutions, are also great places to work as a material engineer.
Materials engineers need to understand the relationship between materials and their processing methods. They must also be capable of identifying the causes and consequences of failures. Aside from being able to explain engineering concepts and ideas to non-engineers, they also need to be able to do so. They are also responsible for identifying and implementing cost-efficient operation strategies. They may also need communication with suppliers and professionals. They may also be required to travel abroad to obtain samples for testing. In some cases they may have to work for more than 40 hours per week.
Materials engineers might also be eligible for advanced degrees. They might be eligible to do a PhD in process engineer. They may also be able to find teaching positions or work in research. Senior material engineers can assume more management responsibilities. They might also have the opportunity for innovative research.
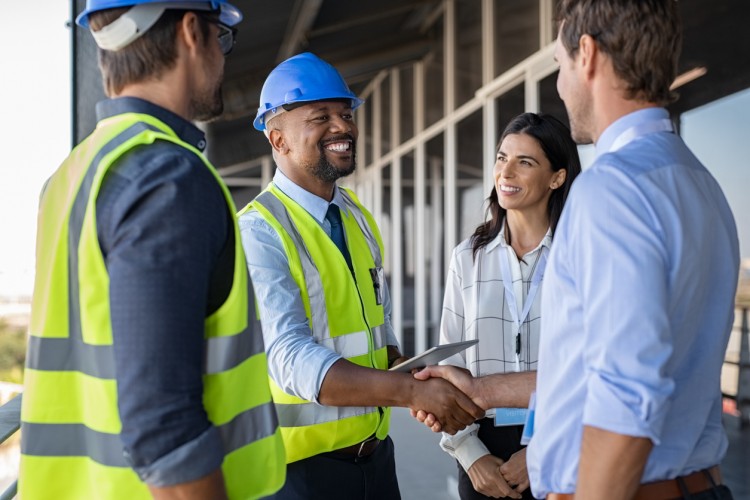
Materials engineers may work in manufacturing plants or offices, and may also travel to worksites to collect samples for testing. The field is very competitive and it is important that you stay up to date with industry innovations and trends. They might also need to maintain good relationships with customers. They can support product engineers with green practices, and even help improve their products. You may develop a strong reputation as a professional in your field.
Materials engineers could also work in laboratories. Advanced math topics may be used for troubleshooting and design. They may need to communicate engineering concepts clearly. They may also be required travel to other countries in order to obtain samples or observe the manufacturing process.
Technology companies such Apple and FedEx often employ materials engineers. Raytheon Technologies, which manufactures metals and other material, may employ them. It is possible to get a job in this field, but it can be very competitive. Engineer consulting firms may also offer opportunities to become material engineers. They might also open their own businesses that can help them stay ahead of the curve in their industry.
Material engineers might also need to work long hours. They may travel to worksites to collect samples for testing, or to observe the use of materials in manufacturing plants. If they work as material engineers in factories, they might be required to work longer hours. Because of this, they will need to be able to work hard.
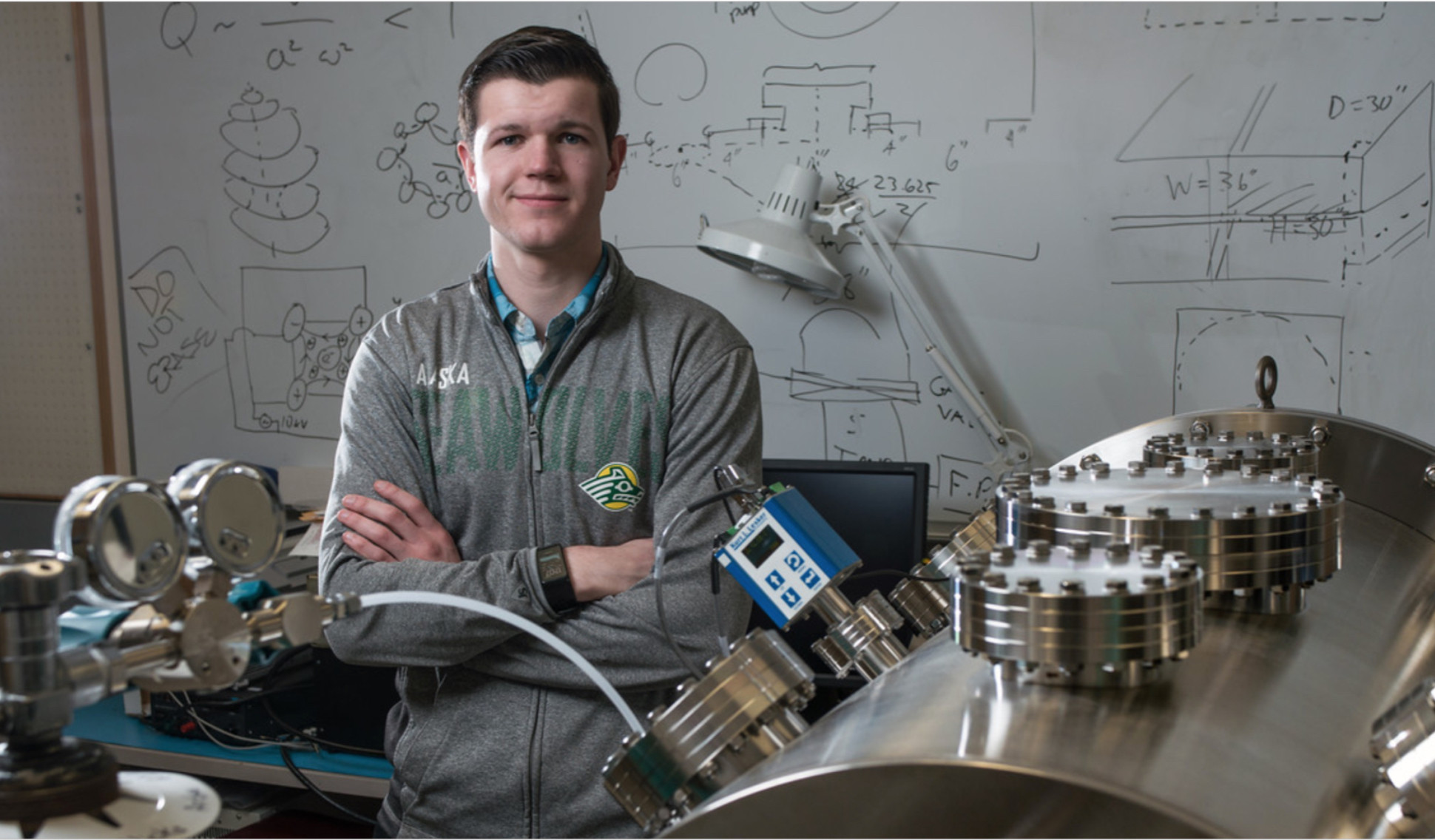
Material engineers often have to work in groups. They may need to communicate with other professionals, communicate with clients, and communicate with suppliers. They may also be responsible in ensuring that deadlines and budgets get met.
FAQ
Why is logistics important in manufacturing?
Logistics are an integral part any business. They are essential to any business's success.
Logistics play a key role in reducing expenses and increasing efficiency.
Is automation necessary in manufacturing?
Not only are service providers and manufacturers important, but so is automation. Automation allows them to deliver services quicker and more efficiently. It also helps to reduce costs and improve productivity.
What does manufacturing mean?
Manufacturing Industries are those businesses that make products for sale. The people who buy these products are called consumers. These companies use a variety processes such as distribution, retailing and management to accomplish their purpose. They manufacture goods from raw materials using machines and other equipment. This covers all types of manufactured goods including clothing, food, building supplies and furniture, as well as electronics, tools, machinery, vehicles and pharmaceuticals.
What are the responsibilities of a logistic manager?
Logistics managers make sure all goods are delivered on schedule and without damage. This is done by using his/her experience and knowledge of the company's products. He/she should ensure that sufficient stock is available in order to meet customer demand.
What is the difference between a production planner and a project manager?
The main difference between a production planner and a project manager is that a project manager is usually the person who plans and organizes the entire project, whereas a production planner is mainly involved in the planning stage of the project.
What is the role of a manager in manufacturing?
A manufacturing manager has to ensure that all manufacturing processes work efficiently and effectively. They must also be alert to any potential problems and take appropriate action.
They should also be able and comfortable communicating with other departments like sales and marketing.
They should also be knowledgeable about the latest trends in the industry so they can use this information for productivity and efficiency improvements.
Statistics
- According to a Statista study, U.S. businesses spent $1.63 trillion on logistics in 2019, moving goods from origin to end user through various supply chain network segments. (netsuite.com)
- It's estimated that 10.8% of the U.S. GDP in 2020 was contributed to manufacturing. (investopedia.com)
- According to the United Nations Industrial Development Organization (UNIDO), China is the top manufacturer worldwide by 2019 output, producing 28.7% of the total global manufacturing output, followed by the United States, Japan, Germany, and India.[52][53] (en.wikipedia.org)
- In 2021, an estimated 12.1 million Americans work in the manufacturing sector.6 (investopedia.com)
- Many factories witnessed a 30% increase in output due to the shift to electric motors. (en.wikipedia.org)
External Links
How To
How to use 5S to increase Productivity in Manufacturing
5S stands for "Sort", 'Set In Order", 'Standardize', & Separate>. Toyota Motor Corporation invented the 5S strategy in 1954. It helps companies achieve higher levels of efficiency by improving their work environment.
This approach aims to standardize production procedures, making them predictable, repeatable, and easily measurable. This means that daily tasks such as cleaning and sorting, storage, packing, labeling, and packaging are possible. Through these actions, workers can perform their jobs more efficiently because they know what to expect from them.
Implementing 5S requires five steps. These are Sort, Set In Order, Standardize. Separate. And Store. Each step requires a different action to increase efficiency. You can make it easy for people to find things later by sorting them. You arrange items by placing them in an order. Next, organize your inventory into categories and store them in containers that are easily accessible. You can also label your containers to ensure everything is properly labeled.
Employees must be able to critically examine their work practices. Employees should understand why they do the tasks they do, and then decide if there are better ways to accomplish them. They will need to develop new skills and techniques in order for the 5S system to be implemented.
In addition to increasing efficiency, the 5S method also improves morale and teamwork among employees. They feel more motivated to work towards achieving greater efficiency as they see the results.