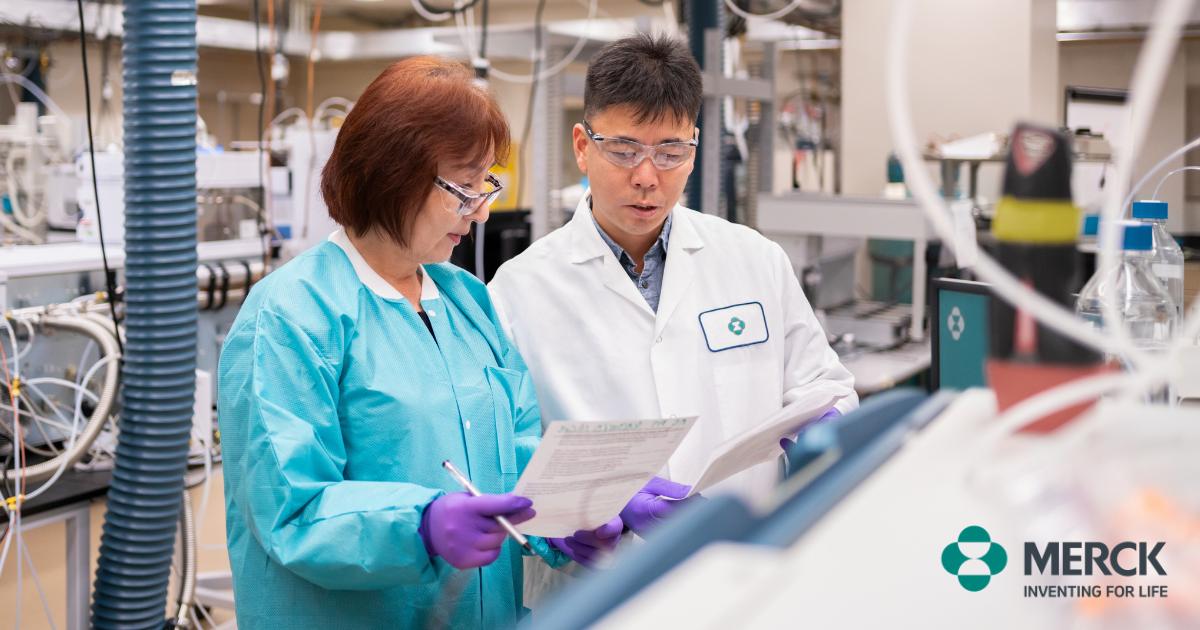
Managing your supply chain is essential to the success of your business. You want to improve your business' efficiency, lower costs, and increase customer satisfaction. The benefits of managing your supply network can be more than just a benefit. It can also increase revenues and help you gain competitive advantages in the marketplace. A strong supply chain management system can increase revenue by 8% of the ten largest companies.
To manage your supply chain, you need to keep track of the location of your inventory and monitor its status. It is also important to keep track of the availability and prices of your products as well as the lead times for your products.
The supply chain is an interdependent network of people, organizations, technologies, and resources that work together to produce, transport, and deliver goods and services. This network allows organizations to produce and deliver goods more quickly, better, and with greater efficiency. It also reduces production costs and increases purchasing efficiency. It is crucial for the production and distribution of electronic goods, health care products, and other items that are essential for daily living.
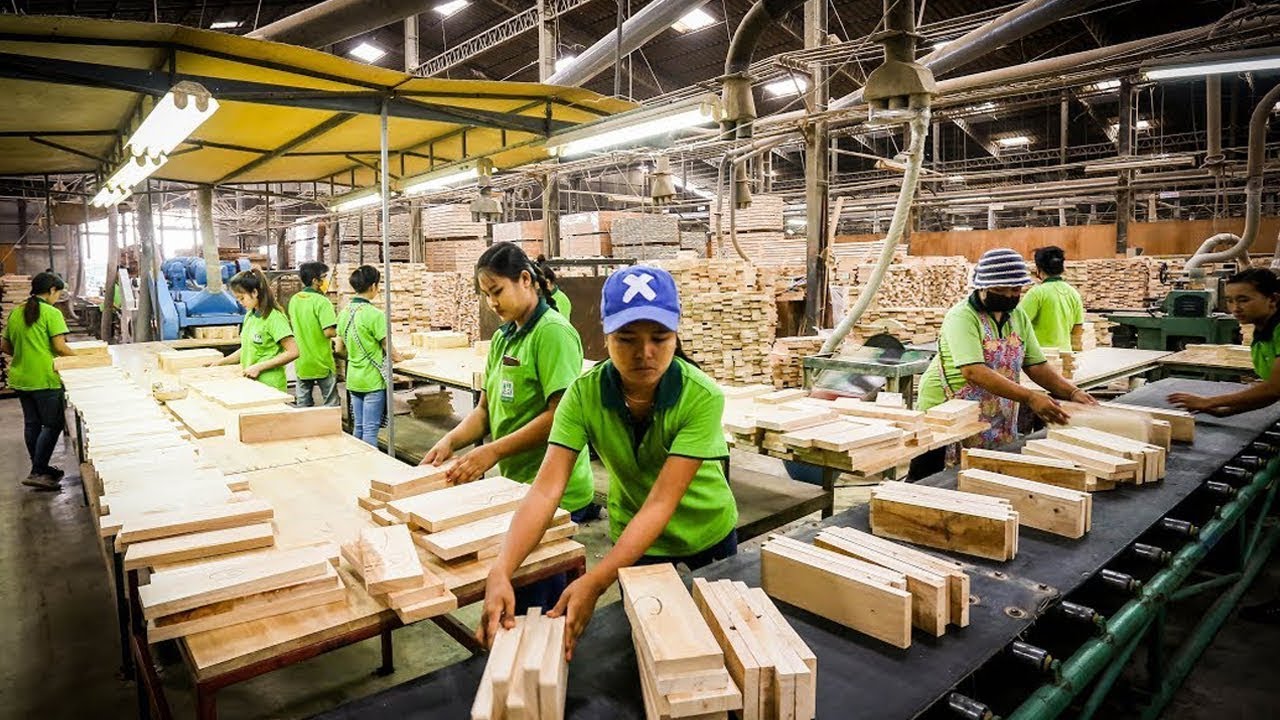
Supply chain management is about the design and implementation processes that get goods from raw materials up to the end consumer. It involves coordination of many different activities such as sales, marketing, production, and distribution. It also includes a system for managing returns on defective products.
Supply chain complexity rises as global competition grows. Part price fluctuations, offshoring and talent attrition all contribute to this increase in complexity. Your supply chain may also be affected by the presence of multiple suppliers.
Supply chain management is a complex process that involves many departments in your organization. These include finance, sales and operations.
It is essential to have knowledge in all five aspects of supply chain management in order to successfully manage your supply chains. These elements include design and management of your supply network, selection of suppliers, management of supplier relationships, design of inventory management, coordination of supply chain logistics, and coordination.
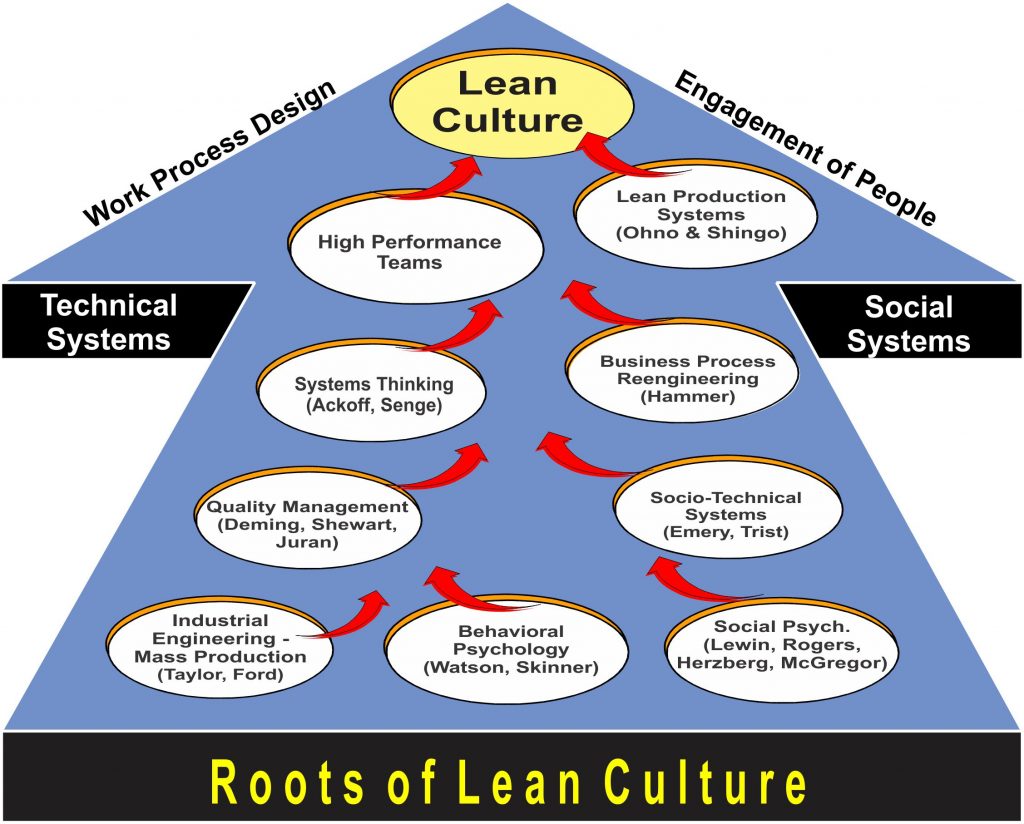
A supply chain planning plan is a plan that describes how your organization will implement the strategy. It also provides details about the steps required for achieving the plan. For example, you may decide to outsource manufacturing, which includes packaging and distribution. You might also have to inspect finished products and collect payments from your customers.
Management of supplier relationships should be considered when creating your supply chain strategy. You might choose to work with vendors who have a track record of delivering products on time. A vendor who is flexible may be a good choice, as you will have the ability to purchase emergency supplies in an emergency.
The supply chain management process can help reduce the wear on your equipment. This can help you and your company stay more connected to your customers and decrease quality issues.
FAQ
What do you mean by warehouse?
A warehouse is a place where goods are stored until they are sold. You can have it indoors or outdoors. It may also be an indoor space or an outdoor area.
What is the job of a manufacturer manager?
A manufacturing manager must ensure that all manufacturing processes are efficient and effective. They must also be alert to any potential problems and take appropriate action.
They should also learn how to communicate effectively with other departments, including sales and marketing.
They should be up to date on the latest trends and be able apply this knowledge to increase productivity and efficiency.
What are the essential elements of running a logistics firm?
To be a successful businessman in logistics, you will need many skills and knowledge. To communicate effectively with clients and suppliers, you must be able to communicate well. You will need to know how to interpret data and draw conclusions. You must be able manage stress and pressure under pressure. You must be creative and innovative to develop new ideas to improve efficiency. You need to have strong leadership qualities to motivate team members and direct them towards achieving organizational goals.
It is also important to be efficient and well organized in order meet deadlines.
What are the responsibilities of a production planner
Production planners make sure that every aspect of the project is delivered on-time, within budget, and within schedule. They also ensure that the product/service meets the client’s needs.
Is automation important for manufacturing?
Automating is not just important for manufacturers, but also for service providers. It allows them provide faster and more efficient services. It reduces human errors and improves productivity, which in turn helps them lower their costs.
Is it necessary to be familiar with Manufacturing Processes before we learn about Logistics.
No. No. However, knowing about manufacturing processes will definitely give you a better understanding of how logistics works.
How can manufacturing avoid production bottlenecks
Production bottlenecks can be avoided by ensuring that processes are running smoothly during the entire production process, starting with the receipt of an order and ending when the product ships.
This includes both planning for capacity and quality control.
This can be done by using continuous improvement techniques, such as Six Sigma.
Six Sigma is a management method that helps to improve quality and reduce waste.
It emphasizes consistency and eliminating variance in your work.
Statistics
- In 2021, an estimated 12.1 million Americans work in the manufacturing sector.6 (investopedia.com)
- According to a Statista study, U.S. businesses spent $1.63 trillion on logistics in 2019, moving goods from origin to end user through various supply chain network segments. (netsuite.com)
- In the United States, for example, manufacturing makes up 15% of the economic output. (twi-global.com)
- It's estimated that 10.8% of the U.S. GDP in 2020 was contributed to manufacturing. (investopedia.com)
- [54][55] These are the top 50 countries by the total value of manufacturing output in US dollars for its noted year according to World Bank.[56] (en.wikipedia.org)
External Links
How To
How to Use Just-In-Time Production
Just-in-time is a way to cut costs and increase efficiency in business processes. It is a process where you get the right amount of resources at the right moment when they are needed. This means that your only pay for the resources you actually use. Frederick Taylor first coined this term while working in the early 1900s as a foreman. He noticed that workers were often paid overtime when they had to work late. He decided to ensure workers have enough time to do their jobs before starting work to improve productivity.
JIT is an acronym that means you need to plan ahead so you don’t waste your money. Look at your entire project, from start to end. Make sure you have enough resources in place to deal with any unexpected problems. You can anticipate problems and have enough equipment and people available to fix them. This will ensure that you don't spend more money on things that aren't necessary.
There are different types of JIT methods:
-
Demand-driven: This type of JIT allows you to order the parts/materials required for your project on a regular basis. This will allow for you to track the material that you have left after using it. This will allow you to calculate how long it will take to make more.
-
Inventory-based: This allows you to store the materials necessary for your projects in advance. This allows for you to anticipate how much you can sell.
-
Project-driven: This means that you have enough money to pay for your project. You will be able to purchase the right amount of materials if you know what you need.
-
Resource-based JIT: This type of JIT is most commonly used. You allocate resources based on the demand. You might assign more people to help with orders if there are many. If there aren't many orders, you will assign fewer people.
-
Cost-based : This is similar in concept to resource-based. But here, you aren't concerned about how many people your company has but how much each individual costs.
-
Price-based: This is very similar to cost-based, except that instead of looking at how much each individual worker costs, you look at the overall price of the company.
-
Material-based: This approach is similar to cost-based. However, instead of looking at the total cost for the company, you look at how much you spend on average on raw materials.
-
Time-based: Another variation of resource-based JIT. Instead of focusing on the cost of each employee, you will focus on the time it takes to complete a project.
-
Quality-based JIT: Another variation on resource-based JIT. Instead of focusing on the cost of each worker or how long it takes, think about how high quality your product is.
-
Value-based JIT : This is the newest type of JIT. In this instance, you are not concerned about the product's performance or meeting customer expectations. Instead, your goal is to add value to the market.
-
Stock-based is an inventory-based system that measures the number of items produced at any given moment. It's used when you want to maximize production while minimizing inventory.
-
Just-in time (JIT), planning: This is a combination JIT/supply chain management. This refers to the scheduling of the delivery of components as soon after they are ordered. It is essential because it reduces lead-times and increases throughput.