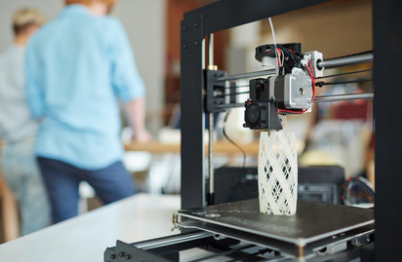
Supply Dynamics was founded in Loveland in Ohio in 2003. It is a multi-enterprise supply chains analytics suite. It offers technology solutions for manufacturers working in distributed manufacturing environments. Supply Dynamics works with the Defense Logistics Agency (DLA) and the Navy. It provides visibility and control of the organization's supply chains from beginning to end. It assists manufacturers in planning production and reducing the cost of raw material. Supply Dynamics works with a variety of industries including aerospace, defense, manufacturing, and transportation.
Dynamics 365 Supply Chain Management, a Microsoft Cloud-powered tool, enables organizations to increase operational efficiency, streamline production and create strong supply chains. It provides unparalleled visibility into the supply chain from beginning to end, with unrivalled flexibility and predictive analytics. Its modules enable customers to have complete product lifecycle functionality.
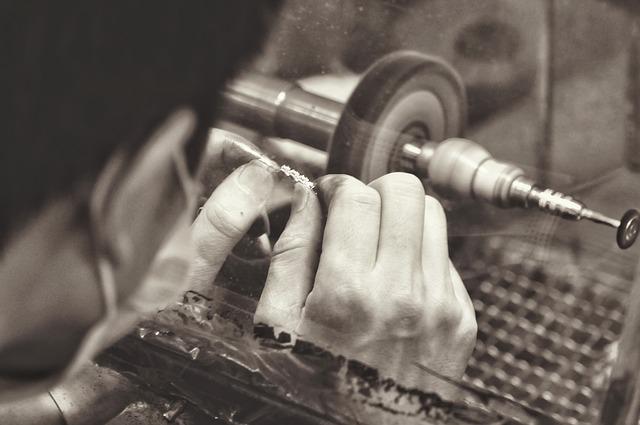
The Dynamics Supply Chain module includes features that allow users to configure items for process or discrete manufacturing, submit RFQs, test product quality, and submit purchase orders. You can also create Gantt charts that provide transparency for all operations. Visual Supply Schedule lets users see the forecast of inventory levels and anticipated demand. You can also modify the schedules if there are supply chain problems. It also provides managers with the ability to track progress of job functions in various areas of a production floor.
Microsoft Dynamics 365 Supply Chain Management allows organizations to use a single, predictive and unified way to manage customer demand. It also ensures that the right materials arrive at the right time. It is also useful for businesses in anticipating customer needs and changing capacity. It can be used at multiple locations and warehouses and integrates logistics, purchasing and production. It also supports vendor-specific pricing as well as multiple inventory costing options and transportation management. The solution supports inventory optimization, predictive analytics, and AI features.
Dynamics 365 also offers self-service for suppliers. Suppliers are able to accept or reject buy orders, issue POs with invoices, and enter shipment information. It supports multiple inventory costing methods such as vendor-specific pricing, item level, item group, and item-level pricing. It includes many inventory optimization features, such as the ability to create an order-specific inventory allocation plan.
Supply Dynamics offers unique solutions for benchmarking metals prices. With this technology, manufacturers can respond faster to changes in the market. They can also anticipate and predict fluctuations in production costs. This technology helps manufacturers lower the cost for raw materials which can lead to less waste. It also gives manufacturers a blueprint for data conversion to bill-ofmaterial.
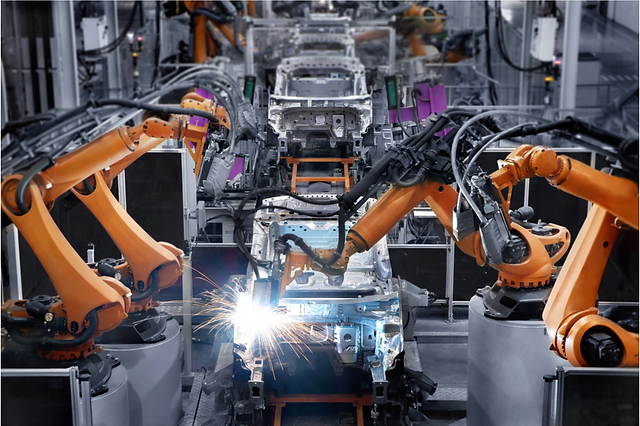
Its master planning feature automates the creation of Production Orders based on open Purchase Orders. It also has an optimization addin that allows users predict changes in customer requirements. It also uses AI capabilities to increase the flow and distribution of goods. Microsoft has certified Dynamics Supply Chain Management, making it an excellent solution for companies looking to create a strong supply network.
FAQ
How can manufacturing efficiency improved?
First, determine which factors have the greatest impact on production time. Next, we must find ways to improve those factors. If you aren't sure where to begin, think about the factors that have the greatest impact on production time. Once you have identified them, it is time to identify solutions.
What does warehouse mean?
A warehouse is an area where goods are stored before being sold. It can be indoors or out. It may also be an indoor space or an outdoor area.
How can manufacturing avoid production bottlenecks
The key to avoiding bottlenecks in production is to keep all processes running smoothly throughout the entire production cycle, from the time you receive an order until the time when the product ships.
This includes planning for both capacity requirements and quality control measures.
Continuous improvement techniques such Six Sigma can help you achieve this.
Six Sigma management is a system that improves quality and reduces waste within your organization.
It emphasizes consistency and eliminating variance in your work.
What are the 7 R's of logistics?
The 7R's of Logistics is an acronym for the seven basic principles of logistics management. It was developed and published by the International Association of Business Logisticians in 2004 as part of the "Seven Principles of Logistics Management".
The acronym is made up of the following letters:
-
Responsible – ensure that all actions are legal and don't cause harm to anyone else.
-
Reliable - You can have confidence that you will fulfill your promises.
-
Be responsible - Use resources efficiently and avoid wasting them.
-
Realistic - Consider all aspects of operations, including environmental impact and cost effectiveness.
-
Respectful - Treat people fairly and equitably
-
Responsive - Look for ways to save time and increase productivity.
-
Recognizable provides value-added products and services to customers
Statistics
- Job #1 is delivering the ordered product according to specifications: color, size, brand, and quantity. (netsuite.com)
- You can multiply the result by 100 to get the total percent of monthly overhead. (investopedia.com)
- It's estimated that 10.8% of the U.S. GDP in 2020 was contributed to manufacturing. (investopedia.com)
- [54][55] These are the top 50 countries by the total value of manufacturing output in US dollars for its noted year according to World Bank.[56] (en.wikipedia.org)
- Many factories witnessed a 30% increase in output due to the shift to electric motors. (en.wikipedia.org)
External Links
How To
How to Use 5S to Increase Productivity in Manufacturing
5S stands as "Sort", Set In Order", Standardize", Separate" and "Store". Toyota Motor Corporation created the 5S methodology in 1954. It assists companies in improving their work environments and achieving higher efficiency.
This approach aims to standardize production procedures, making them predictable, repeatable, and easily measurable. Cleaning, sorting and packing are all done daily. Because workers know what they can expect, this helps them perform their jobs more efficiently.
There are five steps to implementing 5S, including Sort, Set In Order, Standardize, Separate and Store. Each step is a different action that leads to greater efficiency. If you sort items, it makes them easier to find later. You arrange items by placing them in an order. Once you have separated your inventory into groups and organized them, you will store these groups in easily accessible containers. Make sure everything is correctly labeled when you label your containers.
Employees must be able to critically examine their work practices. Employees should understand why they do the tasks they do, and then decide if there are better ways to accomplish them. They will need to develop new skills and techniques in order for the 5S system to be implemented.
In addition to improving efficiency, the 5S system also increases morale and teamwork among employees. They feel more motivated to work towards achieving greater efficiency as they see the results.