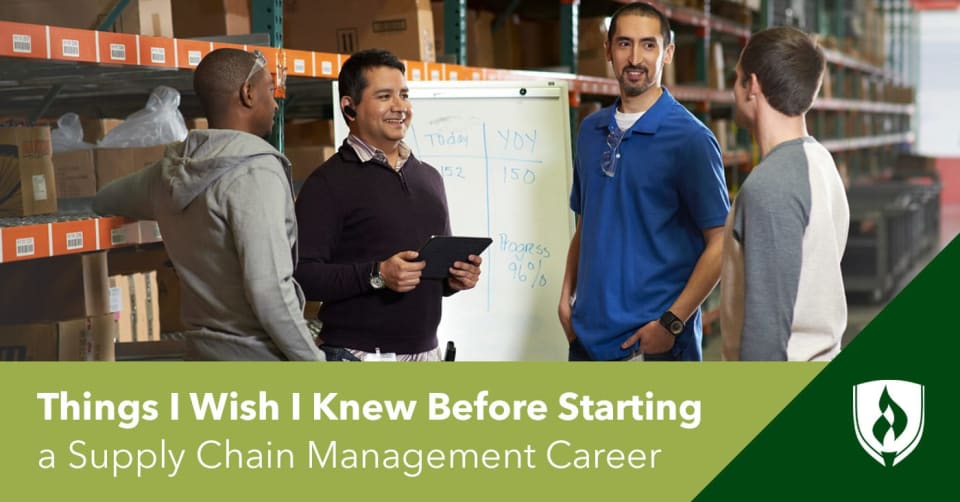
Diverse sources can cause disruptions in supply chains. Natural disasters, product recalls and delays in transportation are just a few examples. Price increases or margin losses can occur due to these interruptions. In order to continue production, some companies may have to modify their sourcing strategy. In many cases, companies will need to re-evaluate their supply networks, diversify their production, and audit their current inventories to prepare for the next disruption.
Supply chain disruptions have been experienced in many industries including electronics, pharmaceuticals, and transportation. Sometimes, disruptions occurred due to internal problems at a company. But in other cases, it was caused as a result of a global emergency. For example, a pandemic caused widespread health disruptions in several countries. It also impacted the retail industry. The pandemic forced governments and other government agencies to take measures to prevent its spread.
A pandemic can affect a company's workforce, distribution, and manufacturing processes. It can impact the production of critical products. Companies will have to re-evaluate their production and supply chains. Depending on the severity, the impact can last several weeks to months. If a pandemic occurs, businesses will need to re-evaluate their inventory, and reallocate capital if necessary.
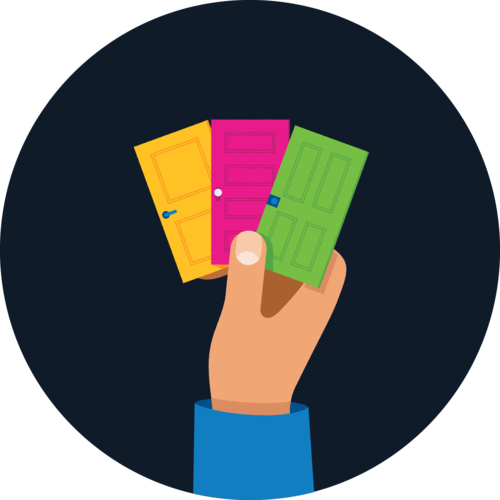
Disruption may occur at any stage in the supply chain and can impact both supply or demand. Most often, disruptions will affect the supply side more than the demand side. If the supply side of an epidemic is disrupted, however, the ripple effect will affect the whole economy.
Supply chain disruptions can have major consequences for a company and are often hard to predict. It is possible to spot seasonal fluctuations but it is much more difficult to predict rapid changes in consumer behavior. These risks can be mitigated by using predictive analytics to spot potential problems.
Another common cause of supply chain disruption is a labor shortage. Unreliable suppliers can cause companies to lose productivity. A machine failure can also disrupt an entire operation.
Natural disasters as well as market fluctuations and geopolitical instabilities are three of the most frequent causes of disruptions to supply chains. Natural disasters are very expensive and can disrupt the global supply chain. Other causes of supply chain disruption include a power outage, telecommunications blackout, and border closures. Moreover, companies may be forced to store large amounts of stock to protect their business.
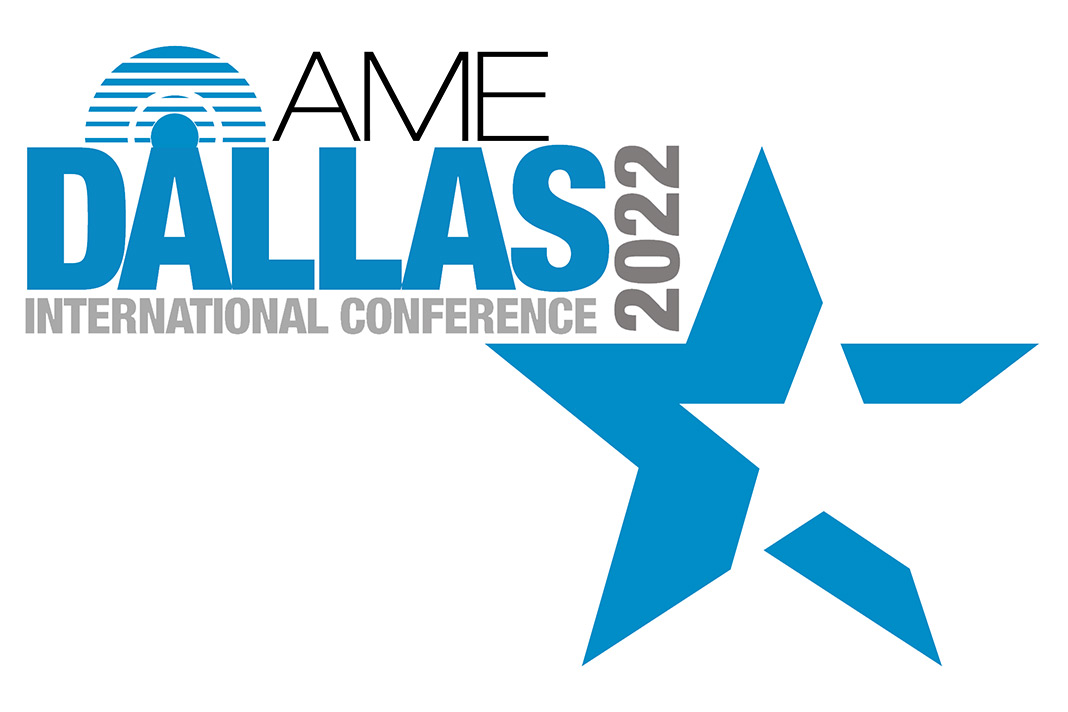
As a rule of thumb, the impact of supply chain disruptions is relatively low. Companies will need help if they discover a disruption. A majority of them will do so. Avoiding conflict by identifying issues early is a good idea.
Ernest & Young LLP surveyed 720 companies and found that 77% had experienced disruptions. 57% of those affected reported adverse consequences. Many of these problems can be addressed quickly, while others will require a more strategic approach.
FAQ
Is automation important for manufacturing?
Automation is important not only for manufacturers but also for service providers. It allows them to offer services faster and more efficiently. They can also reduce their costs by reducing human error and improving productivity.
How can excess manufacturing production be reduced?
The key to reducing overproduction lies in developing better ways to manage inventory. This would reduce time spent on activities such as purchasing, stocking, and maintaining excess stock. This could help us free up our time for other productive tasks.
Kanban systems are one way to achieve this. A Kanbanboard is a visual tool that allows you to keep track of the work being done. A Kanban system allows work items to move through several states before reaching their final destination. Each state represents a different priority.
When work is completed, it can be transferred to the next stage. If a task is still in its beginning stages, it will continue to be so until it reaches the end.
This allows you to keep work moving along while making sure that no work gets neglected. Managers can monitor the work being done by Kanban boards to see what is happening at any given time. This allows them to adjust their workflows based on real-time information.
Lean manufacturing is another way to manage inventory levels. Lean manufacturing focuses on eliminating waste throughout the entire production chain. Waste includes anything that does not add value to the product. Some common types of waste include:
-
Overproduction
-
Inventory
-
Unnecessary packaging
-
Excess materials
These ideas will help manufacturers increase efficiency and lower costs.
What are the responsibilities of a production planner
Production planners ensure that all project aspects are completed on time, within budget and within the scope. They make sure that the product and services meet client expectations.
How does manufacturing avoid bottlenecks in production?
Production bottlenecks can be avoided by ensuring that processes are running smoothly during the entire production process, starting with the receipt of an order and ending when the product ships.
This includes planning to meet capacity requirements and quality control.
The best way to do this is to use continuous improvement techniques such as Six Sigma.
Six Sigma management is a system that improves quality and reduces waste within your organization.
It focuses on eliminating variation and creating consistency in your work.
What are the essential elements of running a logistics firm?
It takes a lot of skills and knowledge to run a successful logistics business. Good communication skills are essential to effectively communicate with your suppliers and clients. You need to understand how to analyze data and draw conclusions from it. You must be able manage stress and pressure under pressure. You need to be innovative and creative to come up with new ways to increase efficiency. You must be a strong leader to motivate others and direct them to achieve organizational goals.
It is also important to be efficient and well organized in order meet deadlines.
What is the job of a logistics manger?
Logistics managers ensure that goods arrive on time and are unharmed. This is done using his/her knowledge of the company's products. He/she should ensure that sufficient stock is available in order to meet customer demand.
What skills are required to be a production manager?
You must be flexible and organized to become a productive production planner. Also, you must be able and willing to communicate with clients and coworkers.
Statistics
- (2:04) MTO is a production technique wherein products are customized according to customer specifications, and production only starts after an order is received. (oracle.com)
- According to the United Nations Industrial Development Organization (UNIDO), China is the top manufacturer worldwide by 2019 output, producing 28.7% of the total global manufacturing output, followed by the United States, Japan, Germany, and India.[52][53] (en.wikipedia.org)
- Many factories witnessed a 30% increase in output due to the shift to electric motors. (en.wikipedia.org)
- It's estimated that 10.8% of the U.S. GDP in 2020 was contributed to manufacturing. (investopedia.com)
- According to a Statista study, U.S. businesses spent $1.63 trillion on logistics in 2019, moving goods from origin to end user through various supply chain network segments. (netsuite.com)
External Links
How To
How to use the Just In-Time Production Method
Just-in-time (JIT) is a method that is used to reduce costs and maximize efficiency in business processes. This is where you have the right resources at the right time. This means that you only pay for what you actually use. Frederick Taylor, a 1900s foreman, first coined the term. He observed how workers were paid overtime if there were delays in their work. He realized that workers should have enough time to complete their jobs before they begin work. This would help increase productivity.
JIT is an acronym that means you need to plan ahead so you don’t waste your money. Look at your entire project, from start to end. Make sure you have enough resources in place to deal with any unexpected problems. You can anticipate problems and have enough equipment and people available to fix them. This way you won't be spending more on things that aren’t really needed.
There are many JIT methods.
-
Demand-driven: This type of JIT allows you to order the parts/materials required for your project on a regular basis. This will allow for you to track the material that you have left after using it. This will allow you to calculate how long it will take to make more.
-
Inventory-based: This type allows you to stock the materials needed for your projects ahead of time. This allows you to predict how much you can expect to sell.
-
Project-driven: This method allows you to set aside enough funds for your project. If you know the amount you require, you can buy the materials you need.
-
Resource-based JIT: This type of JIT is most commonly used. Here, you allocate certain resources based on demand. You might assign more people to help with orders if there are many. If there aren't many orders, you will assign fewer people.
-
Cost-based: This approach is very similar to resource-based. However, you don't just care about the number of people you have; you also need to consider how much each person will cost.
-
Price-based: This is a variant of cost-based. However, instead of focusing on the individual workers' costs, this looks at the total price of the company.
-
Material-based: This approach is similar to cost-based. However, instead of looking at the total cost for the company, you look at how much you spend on average on raw materials.
-
Time-based JIT is another form of resource-based JIT. Instead of focusing solely on the amount each employee costs, focus on how long it takes for the project to be completed.
-
Quality-based JIT: Another variation on resource-based JIT. Instead of looking at the labor costs and time it takes to make a product, think about its quality.
-
Value-based JIT : This is the newest type of JIT. In this instance, you are not concerned about the product's performance or meeting customer expectations. Instead, you're focused on how much value you add to the market.
-
Stock-based. This method is inventory-based and focuses only on the actual production at any given point. This is used to increase production and minimize inventory.
-
Just-in-time (JIT) planning: This is a combination of JIT and supply chain management. It is the process that schedules the delivery of components within a short time of their order. It's important as it reduces leadtimes and increases throughput.