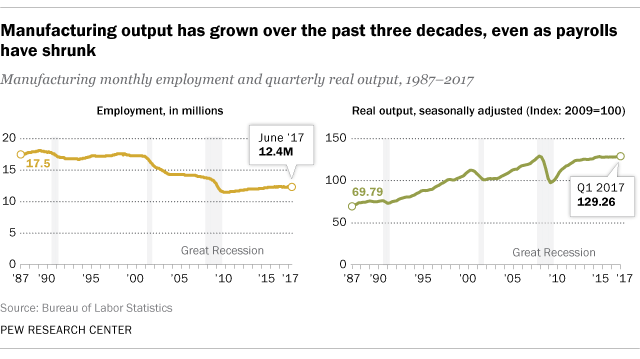
Industrial Engineering Managers play a vital role in the team, no matter if it's for a new project or routine work. They are responsible for directing staff and improving production output. This includes coordinating the layout and design of the factory floor and overseeing the implementation of processes and procedures. They also provide technical expertise and knowledge to assist organizations in developing new products and processes.
They are responsible in developing and maintaining effective manufacturing processes. This requires knowledge about the most recent trends in robotics and automation. They need to ensure safety and health compliance, as well as monitor and maintain industrial operations. They also supervise the use of raw materials and consumables. They also conduct studies to improve workflow and space usage. The manager oversees all work projects, including reductions in cycle time, cost reductions and improvement of processes. They also manage preventative maintenance.
In collaboration with other teams, the manager develops new processes, streamlines operations, and improves efficiency. He or she also oversees the redesign and installation of equipment and facility renovations. As part of the project management process, the manager communicates technical information to non-technical stakeholders. In addition, the manager secures resources for teams and makes site visits to suppliers' facilities. He or she is a champion for members of the team and ensures they adhere to quality standards.
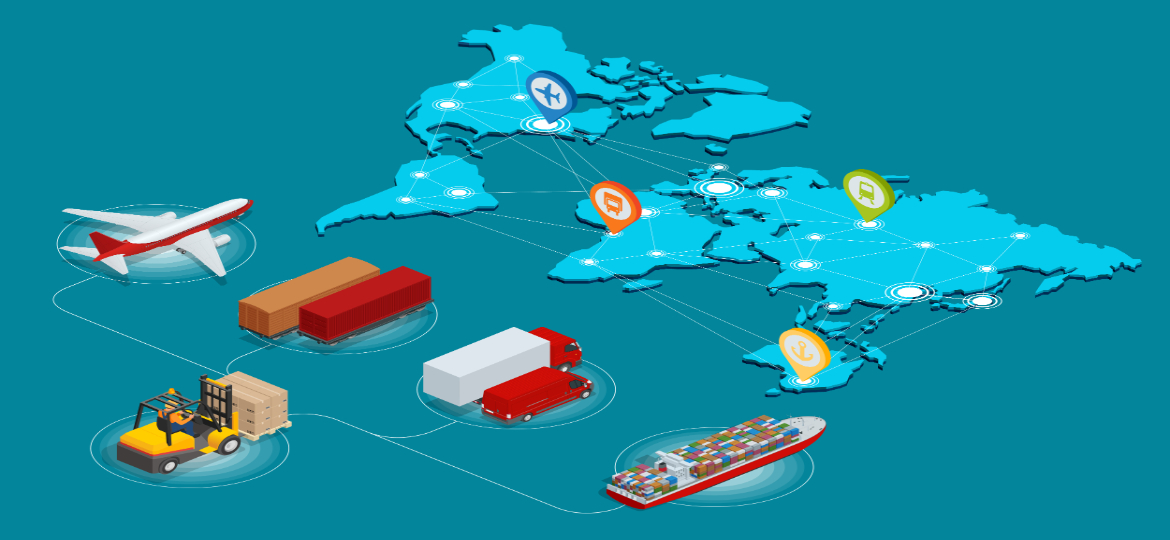
Industrial engineers managers are expected to be creative and highly motivated. They must be able to work in hot and cold environments, be physically fit, and climb and walk for 8 to 12 hours a day. Aside from that, they need to be able and able to communicate well with all levels.
The degree required to become an Industrial Engineering Manager is in engineering or a closely related field. They must also have at minimum five years of relevant experience. Employers prefer candidates who have completed postgraduate studies. You may also need specific skills like project management or logistics.
Managers in Industrial Engineering oversee the development and design of new products and processes. They are skilled in problem solving and quality improvement. They are also able to work in a team setting. Managers are more successful when they are able to encourage employee growth.
Industrial engineers excel in streamlining operations. They are well-versed in manufacturing processes and love meeting deadlines. They have expertise in recruitment, human resources and logistics as well vendor and supplier relations. They are skilled at managing budgets, setting goals and administering procedures. They can also create strategies to increase efficiency in engineering projects.

Industrial engineering managers may be responsible in designing and implementing new manufacturing techniques or operating equipment. They are responsible for developing plans to implement new equipment or operating methods according to established standards and guidelines. They are responsible for overseeing the implementation of waste elimination plans. In addition, they are responsible for analyzing labor productivity in the factory.
Industrial Engineering Managers are able to share their knowledge and help develop strategies for increasing productivity, developing new products, managing human resources, and other tasks. They can also contribute to the improvement and development of existing processes.
FAQ
How does manufacturing avoid bottlenecks in production?
The key to avoiding bottlenecks in production is to keep all processes running smoothly throughout the entire production cycle, from the time you receive an order until the time when the product ships.
This includes both quality control and capacity planning.
Continuous improvement techniques such Six Sigma can help you achieve this.
Six Sigma Management System is a method to increase quality and reduce waste throughout your organization.
It focuses on eliminating variation and creating consistency in your work.
How can manufacturing excess production be decreased?
Better inventory management is key to reducing excess production. This would reduce the time spent on unproductive activities like purchasing, storing and maintaining excess stock. This could help us free up our time for other productive tasks.
A Kanban system is one way to achieve this. A Kanban board, a visual display to show the progress of work, is called a Kanban board. Kanban systems are where work items travel through a series of states until reaching their final destination. Each state represents a different priority.
To illustrate, work can move from one stage or another when it is complete enough for it to be moved to a new stage. A task that is still in the initial stages of a process will be considered complete until it moves on to the next stage.
This helps to keep work moving forward while ensuring that no work is left behind. A Kanban board allows managers to monitor how much work is being completed at any given moment. This information allows them to adjust their workflow based on real-time data.
Lean manufacturing can also be used to reduce inventory levels. Lean manufacturing is about eliminating waste from all stages of the production process. Waste includes anything that does not add value to the product. These are some of the most common types.
-
Overproduction
-
Inventory
-
Packaging not required
-
Material surplus
Manufacturers can reduce their costs and improve their efficiency by using these ideas.
What is the difference between Production Planning, Scheduling and Production Planning?
Production Planning (PP), or production planning, is the process by which you determine what products are needed at any given time. Forecasting demand is one way to do this.
Scheduling is the process that assigns dates to tasks so they can get completed within a given timeframe.
How can efficiency in manufacturing be improved?
The first step is to determine the key factors that impact production time. Then we need to find ways to improve these factors. If you don’t know where to begin, consider which factors have the largest impact on production times. Once you have identified the factors, then try to find solutions.
Statistics
- (2:04) MTO is a production technique wherein products are customized according to customer specifications, and production only starts after an order is received. (oracle.com)
- Many factories witnessed a 30% increase in output due to the shift to electric motors. (en.wikipedia.org)
- [54][55] These are the top 50 countries by the total value of manufacturing output in US dollars for its noted year according to World Bank.[56] (en.wikipedia.org)
- According to a Statista study, U.S. businesses spent $1.63 trillion on logistics in 2019, moving goods from origin to end user through various supply chain network segments. (netsuite.com)
- It's estimated that 10.8% of the U.S. GDP in 2020 was contributed to manufacturing. (investopedia.com)
External Links
How To
How to Use Lean Manufacturing for the Production of Goods
Lean manufacturing (or lean manufacturing) is a style of management that aims to increase efficiency, reduce waste and improve performance through continuous improvement. It was first developed in Japan in the 1970s/80s by Taiichi Ahno, who was awarded the Toyota Production System (TPS), award from KanjiToyoda, the founder of TPS. Michael L. Watkins published the original book on lean manufacturing, "The Machine That Changed the World," in 1990.
Lean manufacturing is often described as a set if principles that help improve the quality and speed of products and services. It emphasizes the elimination and minimization of waste in the value stream. Lean manufacturing is also known as just in time (JIT), zero defect total productive maintenance(TPM), and five-star (S). Lean manufacturing is about eliminating activities that do not add value, such as inspection, rework, and waiting.
Lean manufacturing not only improves product quality but also reduces costs. Companies can also achieve their goals faster by reducing employee turnover. Lean manufacturing is considered one of the most effective ways to manage the entire value chain, including suppliers, customers, distributors, retailers, and employees. Lean manufacturing is widely used in many industries. Toyota's philosophy is the foundation of its success in automotives, electronics and appliances, healthcare, chemical engineers, aerospace, paper and food, among other industries.
Lean manufacturing includes five basic principles:
-
Define Value - Identify the value your business adds to society and what makes you different from competitors.
-
Reduce Waste - Remove any activity which doesn't add value to your supply chain.
-
Create Flow. Ensure that your work is uninterrupted and flows seamlessly.
-
Standardize & Simplify - Make processes as consistent and repeatable as possible.
-
Build Relationships- Develop personal relationships with both internal as well as external stakeholders.
Although lean manufacturing isn't a new concept in business, it has gained popularity due to renewed interest in the economy after the 2008 global financial crisis. To increase their competitiveness, many businesses have turned to lean manufacturing. In fact, some economists believe that lean manufacturing will be an important factor in economic recovery.
Lean manufacturing is now becoming a common practice in the automotive industry, with many benefits. These include improved customer satisfaction, reduced inventory levels, lower operating costs, increased productivity, and better overall safety.
You can apply Lean Manufacturing to virtually any aspect of your organization. However, it is particularly useful when applied to the production side of an organization because it ensures that all steps in the value chain are efficient and effective.
There are three main types of lean manufacturing:
-
Just-in Time Manufacturing, (JIT): This kind of lean manufacturing is also commonly known as "pull-systems." JIT stands for a system where components are assembled on the spot rather than being made in advance. This strategy aims to decrease lead times, increase availability of parts and reduce inventory.
-
Zero Defects Manufacturing (ZDM): ZDM focuses on ensuring that no defective units leave the manufacturing facility. You should repair any part that needs to be repaired during an assembly line. This applies to finished products, which may need minor repairs before they are shipped.
-
Continuous Improvement (CI): CI aims to improve the efficiency of operations by continuously identifying problems and making changes in order to eliminate or minimize waste. Continuous Improvement (CI) involves continuous improvement in processes, people, tools, and infrastructure.