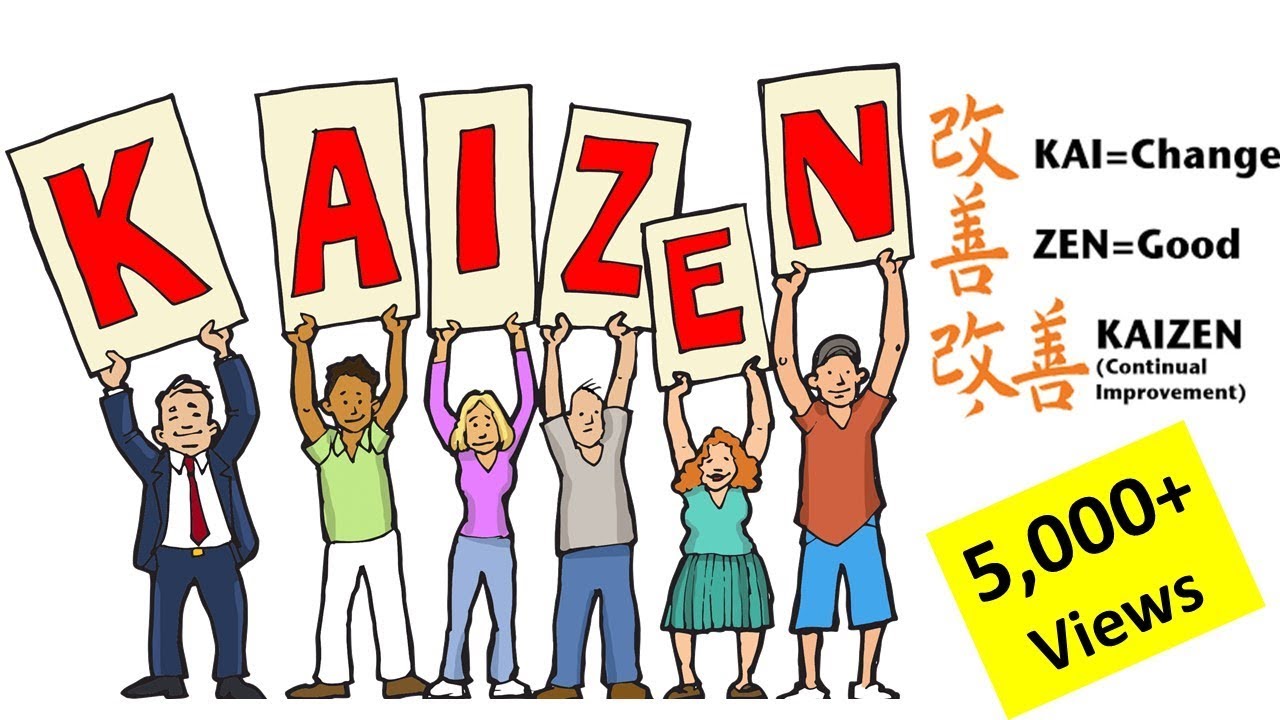
Lean 5 principles focus on eliminating waste. They also encourage value stream mapping to identify areas that can be performed more efficiently. It is crucial to identify the value-added and unnecessary wastes in order to eliminate them. By eliminating unnecessary steps, an efficient process is created that uses the least amount of time, energy, and materials. This ensures that customers are satisfied and high quality products are produced in the shortest time possible.
Value
You can improve the flow of manufacturing by eliminating waste using the Value of Lean 5 principles. By identifying and eliminating the steps that do not add value, you can create a smooth flow from production to shipping. This process helps reduce inventory, saves time and eliminates work in progress.
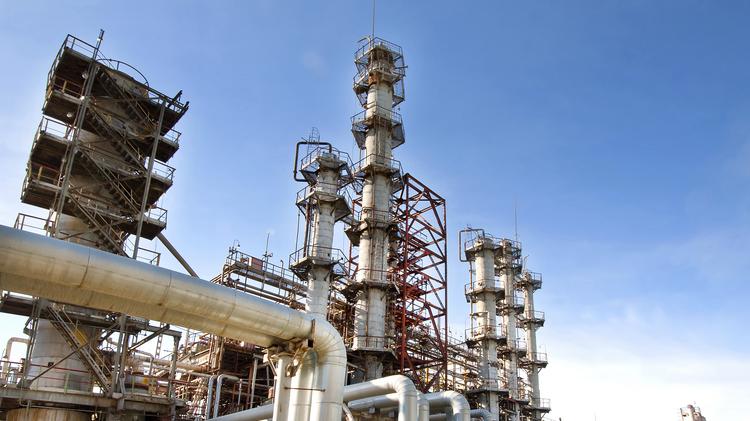
Value stream
Lean manufacturing's value stream is a method of eliminating waste in manufacturing processes. The process maps out every step in a process to identify and eliminate the necessary elements. The entire value stream is the product's entire life cycle, including its creation and use. This is how you eliminate waste. There are three types waste in a value stream.
Flow
The first principle, flow, of the 5 lean principles, involves identifying and evaluating the customer's needs. This step is critical in designing new products and services. Customers don't always clearly communicate their needs. The second step involves defining the value stream or the sequence of activities that will complete a project. This step is crucial to lean project management. It requires close collaboration between all project participants.
Pull
In a pull system, the process begins only when there is an order from a customer. A pizza shop would not produce extra pizzas if they had received a customer order. If they didn't, they would waste time and resources as well as their ingredients.
Perfection
One of the five lean principles is perfection. Perfection is a state of being complete, exact, consistent. Perfection is a difficult goal. The idea behind this concept is to promote continuous improvement. The result is a better performance for organizations.
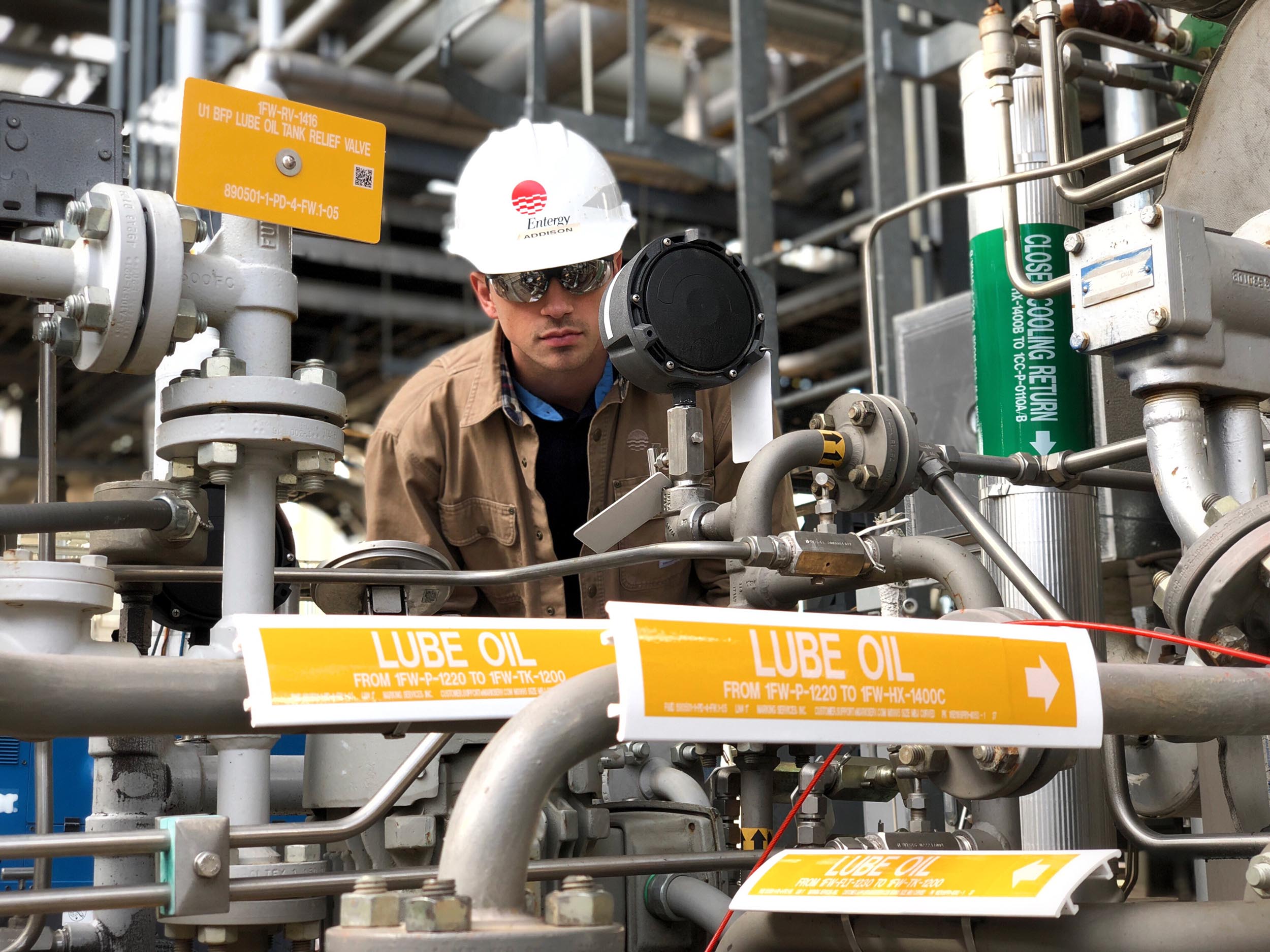
Stakeholder collaboration
Stakeholder collaboration is a crucial element in lean project administration. This involves collaboration among project team members to solve problems, and increase the project's value. Teams must identify the problems and areas that need improvement in order to plan. The doing phase involves gathering data to help them find solutions. Execution is not the main focus. It is important that the team considers the organizational structure in order to collaborate.
FAQ
What does the term manufacturing industries mean?
Manufacturing Industries are businesses that produce products for sale. Consumers are people who purchase these goods. These companies use various processes such as production, distribution, retailing, management, etc., to fulfill this purpose. They make goods from raw materials with machines and other equipment. This includes all types if manufactured goods.
Why is logistics important in manufacturing
Logistics are essential to any business. They help you achieve great results by helping you manage all aspects of product flow, from raw materials to finished goods.
Logistics play a key role in reducing expenses and increasing efficiency.
How can manufacturing efficiency improved?
First, determine which factors have the greatest impact on production time. We must then find ways that we can improve these factors. If you don’t know how to start, look at which factors have the greatest impact upon production time. Once you have identified them, it is time to identify solutions.
What is the difference in Production Planning and Scheduling, you ask?
Production Planning (PP) is the process of determining what needs to be produced at any given point in time. This is done through forecasting demand and identifying production capacities.
Scheduling involves the assignment of dates and times to tasks in order to complete them within the timeframe.
Statistics
- You can multiply the result by 100 to get the total percent of monthly overhead. (investopedia.com)
- [54][55] These are the top 50 countries by the total value of manufacturing output in US dollars for its noted year according to World Bank.[56] (en.wikipedia.org)
- In 2021, an estimated 12.1 million Americans work in the manufacturing sector.6 (investopedia.com)
- It's estimated that 10.8% of the U.S. GDP in 2020 was contributed to manufacturing. (investopedia.com)
- According to a Statista study, U.S. businesses spent $1.63 trillion on logistics in 2019, moving goods from origin to end user through various supply chain network segments. (netsuite.com)
External Links
How To
Six Sigma: How to Use it in Manufacturing
Six Sigma is defined by "the application SPC (statistical process control) techniques to achieve continuous improvements." It was developed by Motorola's Quality Improvement Department at their plant in Tokyo, Japan, in 1986. The basic idea behind Six Sigma is to improve quality by improving processes through standardization and eliminating defects. In recent years, many companies have adopted this method because they believe there is no such thing as perfect products or services. Six Sigma's primary goal is to reduce variation from the average value of production. This means that if you take a sample of your product, then measure its performance against the average, you can find out what percentage of the time the process deviates from the norm. If there is a significant deviation from the norm, you will know that something needs to change.
Understanding how your business' variability is a key step towards Six Sigma implementation is the first. Once you have a good understanding of the basics, you can identify potential sources of variation. This will allow you to decide if these variations are random and systematic. Random variations are caused when people make mistakes. While systematic variations are caused outside of the process, they can occur. For example, if you're making widgets, and some of them fall off the assembly line, those would be considered random variations. But if you notice that every widget you make falls apart at the exact same place each time, this would indicate that there is a problem.
Once you have identified the problem, you can design solutions. The solution could involve changing how you do things, or redesigning your entire process. Once you have implemented the changes, it is important to test them again to ensure they work. If they don't work, you will need to go back to the drawing boards and create a new plan.