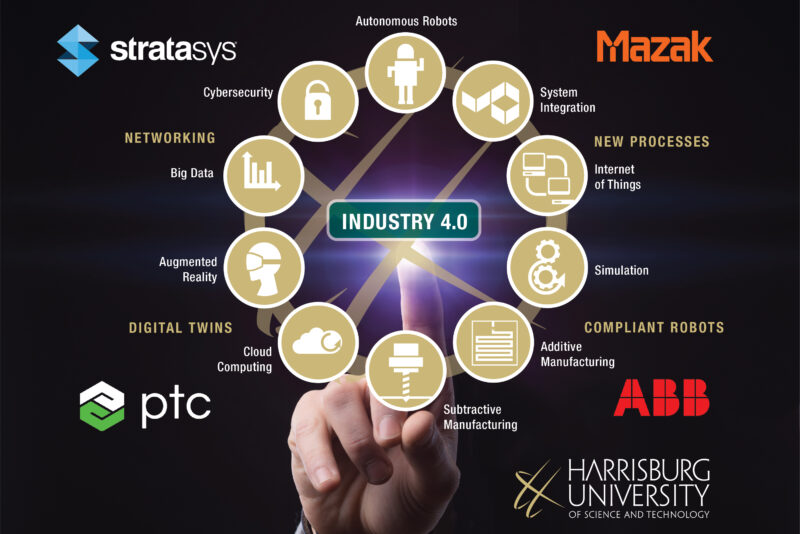
You will be an industrial designer and create innovative products for your home, office, or industry. This article will discuss your job duties and how to get the education and training that you need. It also discusses the salary range you can expect. You'll also learn how to get started and the different career options. You'll also find out about the career benefits, as well as potential opportunities for advancement. Once you've completed your education, you'll be well on your way to a lucrative career in the design field.
Your job duties
The Industrial designer is responsible for generating new products and services through the integration of art, business, and engineering skills. They must ensure that brand strategies are aligned with their designs. You must have experience as an Industrial Designer and a solid portfolio of design concepts. Industrial Designers should be skilled in computer-aided designs software and creative in incorporating new technology to products.
As a part of their job, Industrial Designers work to develop design concepts and regulations. They should be able solve problems and communicate design ideas to cross-functional teams. They must be able collaborate with engineers and to create CAD models. Industrial Designers must also be familiar with Microsoft Office, Solidworks, Keyshot, and other computer-aided design software.
Education Required
An educational background in an industrial design program is helpful for job seekers seeking a career in this field. These programs offer students the opportunity to create a portfolio online to showcase their design abilities. Likewise, some industrial designers also have a Master of Business Administration degree, which helps them enhance their business acumen and better understand the limitations of products. Industrial designers use their analytical skills and reasoning to create innovative products and services.
The kind of work you are interested in is a factor in the education that an industrial designer needs. An industrial designer must hold at least an associate's degree. Some schools offer degrees in industrial design, while others do not. Candidates should take courses in business and design, as well as courses in engineering and mathematics. To show potential employers, it is important that you have a portfolio. You have many opportunities for career growth and advancement, as there are with all jobs in design.
Opportunities for career advancement
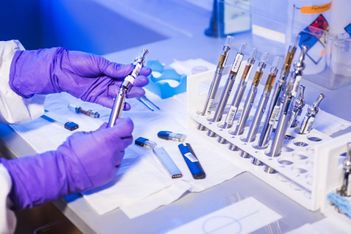
If you're interested in becoming an industrial designer, you can find a range of entry-level positions at design firms, manufacturing companies, or in-house design departments. Then, you can progress to more senior roles by applying for jobs as a chief designer or design department head. Whatever job you choose to pursue, any chance to develop your design skills will prove beneficial. These are just a few of many entry-level positions that industrial designers can take.
An industrial designer usually has a bachelor's degree or related qualifications, and many employers look for candidates who have a background in graphics or sketching, as these skills can enhance their applications for jobs. Employers may choose to hire candidates who are proficient in 3D modeling or CADD. A skilled industrial designer, whether you're an architect, civil engineer or engineer, will be needed to be able to draw, render, and present their work to decision makers.
Salary
The salary of an industrial designer depends on their education and experience. A person with a Masters' or Doctorate degree generally earns more than 75,019 annually. A Bachelor's degree is less. Many industrial designers make it to management positions. Here are some tips for increasing your salary. To begin, make sure to read the job description carefully and know your exact salary expectations.
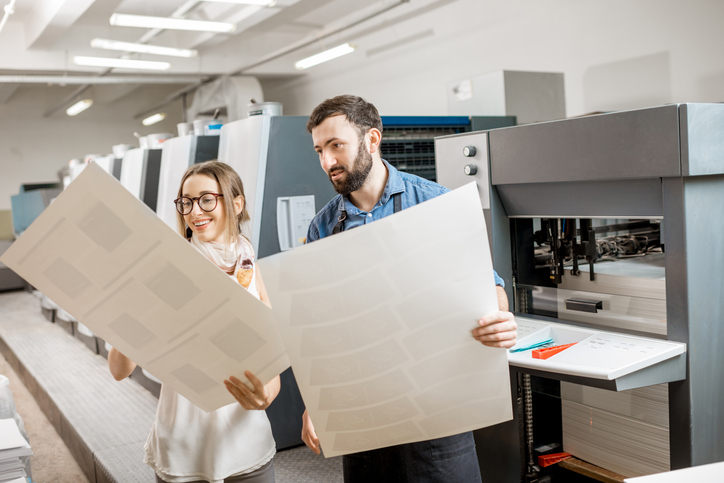
Industrial Designers earn an average annual salary of $62,315, though the actual amount can be much higher. According to the U.S. Bureau of Labor Statistics (USBoLS), the highest earners in this profession make $106,000 a YEAR. But, this is only an estimate. Your industry experience, where you work, and your location all will impact the salary you receive. Once you've established your skillset and geographic location, you can begin to evaluate the compensation available in your field.
FAQ
How can manufacturing reduce production bottlenecks?
The key to avoiding bottlenecks in production is to keep all processes running smoothly throughout the entire production cycle, from the time you receive an order until the time when the product ships.
This includes planning to meet capacity requirements and quality control.
This can be done by using continuous improvement techniques, such as Six Sigma.
Six Sigma is a management system used to improve quality and reduce waste in every aspect of your organization.
It's all about eliminating variation and creating consistency in work.
What is the difference between Production Planning and Scheduling?
Production Planning (PP), or production planning, is the process by which you determine what products are needed at any given time. Forecasting and identifying production capacity are two key elements to this process.
Scheduling is the process of assigning specific dates to tasks so they can be completed within the specified timeframe.
What jobs are available in logistics?
There are different kinds of jobs available in logistics. Some examples are:
-
Warehouse workers: They load and unload trucks, pallets, and other cargo.
-
Transportation drivers – These drivers drive trucks and wagons to transport goods and pick up the goods.
-
Freight handlers - They sort and pack freight in warehouses.
-
Inventory managers - They oversee the inventory of goods in warehouses.
-
Sales representatives - They sell products.
-
Logistics coordinators - They plan and organize logistics operations.
-
Purchasing agents – They buy goods or services necessary to run a company.
-
Customer service agents - They answer phone calls and respond to emails.
-
Shippers clerks - They process shipping order and issue bills.
-
Order fillers - These people fill orders based on what has been ordered.
-
Quality control inspectors: They inspect outgoing and incoming products for any defects.
-
Others - There are many types of jobs in logistics such as transport supervisors and cargo specialists.
Why automate your warehouse
Modern warehousing is becoming more automated. E-commerce has brought increased demand for more efficient and quicker delivery times.
Warehouses must adapt quickly to meet changing customer needs. In order to do this, they need to invest in technology. Automating warehouses is a great way to save money. These are some of the benefits that automation can bring to warehouses:
-
Increases throughput/productivity
-
Reduces errors
-
Improves accuracy
-
Safety enhancements
-
Eliminates bottlenecks
-
Allows companies scale more easily
-
It makes workers more efficient
-
This gives you visibility into what happens in the warehouse
-
Enhances customer experience
-
Improves employee satisfaction
-
Reducing downtime and increasing uptime
-
Quality products delivered on time
-
Eliminates human error
-
It helps ensure compliance with regulations
What does it take for a logistics enterprise to succeed?
You need to have a lot of knowledge and skills to manage a successful logistic business. Effective communication skills are necessary to work with suppliers and clients. It is important to be able to analyse data and draw conclusions. You must be able to work well under pressure and handle stressful situations. In order to innovate and create new ways to improve efficiency, creativity is essential. You will need strong leadership skills to motivate and direct your team members towards achieving their organizational goals.
You must be organized to meet tight deadlines.
Statistics
- You can multiply the result by 100 to get the total percent of monthly overhead. (investopedia.com)
- Job #1 is delivering the ordered product according to specifications: color, size, brand, and quantity. (netsuite.com)
- In the United States, for example, manufacturing makes up 15% of the economic output. (twi-global.com)
- Many factories witnessed a 30% increase in output due to the shift to electric motors. (en.wikipedia.org)
- It's estimated that 10.8% of the U.S. GDP in 2020 was contributed to manufacturing. (investopedia.com)
External Links
How To
How to Use the 5S to Increase Productivity In Manufacturing
5S stands for "Sort", 'Set In Order", 'Standardize', & Separate>. Toyota Motor Corporation invented the 5S strategy in 1954. It improves the work environment and helps companies to achieve greater efficiency.
The idea behind standardizing production processes is to make them repeatable and measurable. Cleaning, sorting and packing are all done daily. This knowledge allows workers to be more efficient in their work because they are aware of what to expect.
Implementing 5S involves five steps: Sort, Set in Order, Standardize Separate, Store, and Each step is a different action that leads to greater efficiency. By sorting, for example, you make it easy to find the items later. When items are ordered, they are put together. After you have divided your inventory into groups you can store them in easy-to-reach containers. Make sure everything is correctly labeled when you label your containers.
Employees will need to be more critical about their work. Employees need to understand the reasons they do certain jobs and determine if there is a better way. To implement the 5S system, employees must acquire new skills and techniques.
In addition to increasing efficiency, the 5S method also improves morale and teamwork among employees. Once they start to notice improvements, they are motivated to keep working towards their goal of increasing efficiency.