
Toyota has never lost sight, no matter how successful it is, of its primary goal to make high quality products. Toyota has been a top-selling automotive brand because of its unwavering dedication to excellence.
Toyota's strategy is based on staying true to its core values, focusing on incremental innovations, and promoting smart growth. It emphasizes the importance in building and maintaining relationships with dealers. Toyota places its customers first, whereas other companies might rely solely on stock prices. Because the automobile industry is competitive, innovation is key to success.
Toyota employees must be able to face challenges in order to continue to achieve success. Toyota encourages employees, to think outside the box and come up with new ideas. Open communication is encouraged and employees are challenged to reach out beyond differences and compromises. On-the-job training is a way to achieve this. Employees are also encouraged not to hide their mistakes or problems.
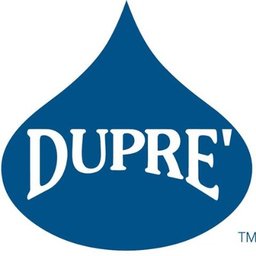
Toyota also uses continuous improvement, or kaizen, to achieve its success. This involves streamlining processes as well as testing new ideas. This process, known in Japanese as "genchi genbutsu", helps Toyota achieve its goals. It is also an essential part of Toyota's culture. It has been the foundation of Toyota's success for many decades.
Toyota was the first company to open a research facility. Kiichiro Tokyoda, the company's founder, believed that innovation was essential for automobile manufacturing to continue to thrive. He set up a research lab in the late 1930s. He envisaged a Japan with its own automobiles, and without any foreign technology.
Toyota made several strategic moves in the 1950s. Toyota began diversifying its product range and exporting cars to other countries. It also created a separate sales company, and established a network with dealers. It began to get a better understanding of the international car market. It saw that American and European automakers would outnumber Toyota if Toyota wanted to compete in global markets.
Toyota also launched an American division, a significant move in the 1950s. The move was made because the American workforce is nine times more productive that Japanese workers. It also realized that fuel-efficient cars were a must in the marketplace. It was required to convince the American public that Japanese cars were an excellent investment. It also had to overcome a massive strike that almost bankrupted it in the 1950s. It had to obtain loans and trim staff.
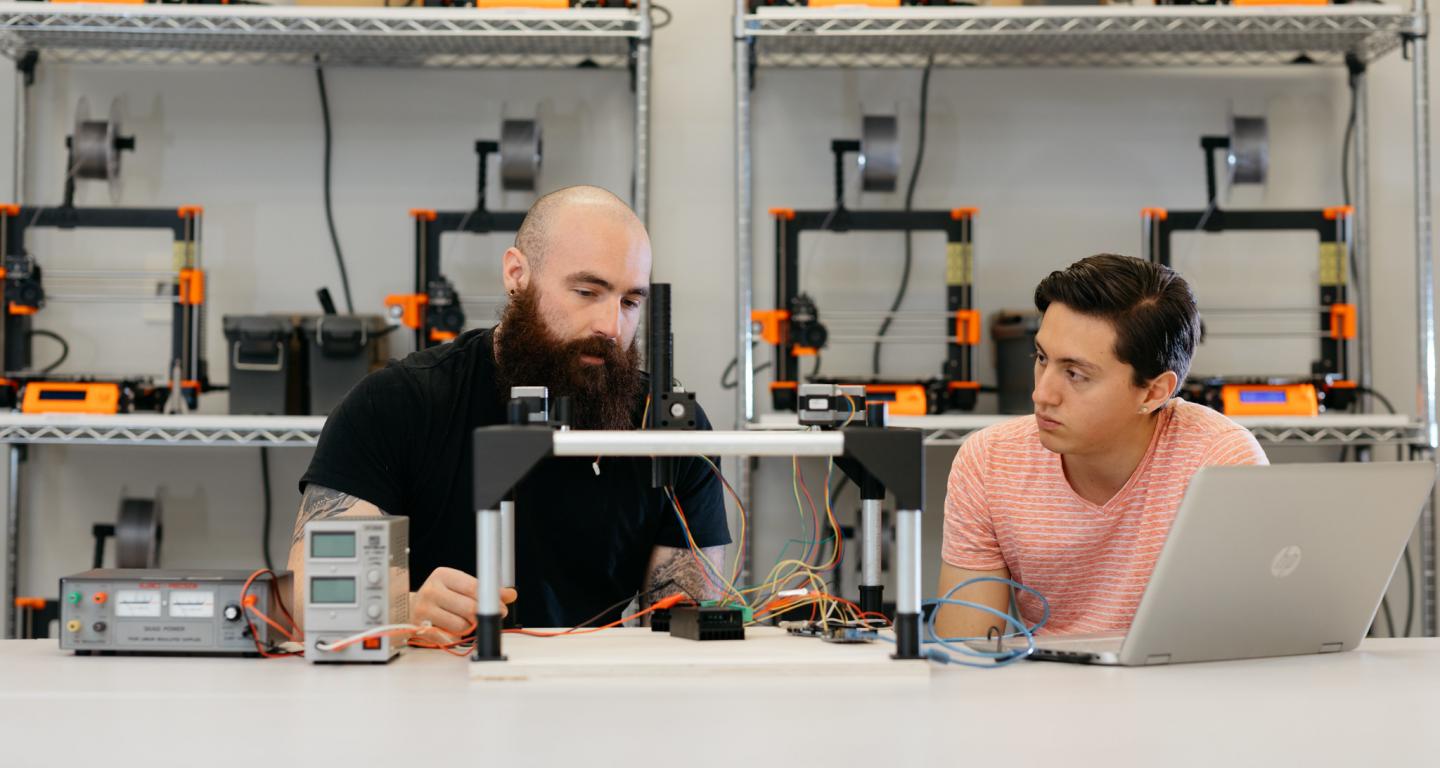
Toyota also launched a driver training school for citizens to help them get their licenses. It also produced a line of vehicles specifically for the U.S. These initiatives helped the company attract more customers to its dealerships.
Toyota's success as an automobile manufacturer depends on its ability and willingness to innovate and create value. It depends on its ability develop relationships and partnerships with suppliers.
FAQ
How can efficiency in manufacturing be improved?
First, we need to identify which factors are most critical in affecting production times. The next step is to identify the most important factors that affect production time. You can start by identifying the most important factors that impact production time. Once you have identified the factors, then try to find solutions.
What are manufacturing and logistics?
Manufacturing refers to the process of making goods using raw materials and machines. Logistics is the management of all aspects of supply chain activities, including procurement, production planning, distribution, warehousing, inventory control, transportation, and customer service. As a broad term, manufacturing and logistics often refer to both the creation and delivery of products.
Why is logistics important in manufacturing?
Logistics are essential to any business. They help you achieve great results by helping you manage all aspects of product flow, from raw materials to finished goods.
Logistics plays a significant role in reducing cost and increasing efficiency.
How can excess manufacturing production be reduced?
The key to reducing overproduction lies in developing better ways to manage inventory. This would reduce the amount of time spent on unnecessary activities such as purchasing, storing, and maintaining excess stock. By doing this, we could free up resources for other productive tasks.
One way to do this is to adopt a Kanban system. A Kanban board, a visual display to show the progress of work, is called a Kanban board. Kanban systems are where work items travel through a series of states until reaching their final destination. Each state represents an individual priority level.
As an example, if work is progressing from one stage of the process to another, then the current task is complete and can be transferred to the next. It is possible to keep a task in the beginning stages until it gets to the end.
This allows for work to continue moving forward, while also ensuring that there is no work left behind. With a Kanban board, managers can see exactly how much work is being done at any given moment. This allows them to adjust their workflows based on real-time information.
Lean manufacturing, another method to control inventory levels, is also an option. Lean manufacturing is about eliminating waste from all stages of the production process. Waste includes anything that does not add value to the product. There are several types of waste that you might encounter:
-
Overproduction
-
Inventory
-
Unnecessary packaging
-
Material surplus
By implementing these ideas, manufacturers can improve efficiency and cut costs.
Statistics
- It's estimated that 10.8% of the U.S. GDP in 2020 was contributed to manufacturing. (investopedia.com)
- [54][55] These are the top 50 countries by the total value of manufacturing output in US dollars for its noted year according to World Bank.[56] (en.wikipedia.org)
- In 2021, an estimated 12.1 million Americans work in the manufacturing sector.6 (investopedia.com)
- (2:04) MTO is a production technique wherein products are customized according to customer specifications, and production only starts after an order is received. (oracle.com)
- In the United States, for example, manufacturing makes up 15% of the economic output. (twi-global.com)
External Links
How To
How to use the Just-In Time Method in Production
Just-in-time is a way to cut costs and increase efficiency in business processes. It's the process of obtaining the right amount and timing of resources when you need them. This means that only what you use is charged to your account. Frederick Taylor, a 1900s foreman, first coined the term. He noticed that workers were often paid overtime when they had to work late. He decided to ensure workers have enough time to do their jobs before starting work to improve productivity.
JIT is a way to plan ahead and make sure you don't waste any money. Also, you should look at the whole project from start-to-finish and make sure you have the resources necessary to address any issues. You can anticipate problems and have enough equipment and people available to fix them. This way, you won't end up paying extra money for things that weren't really necessary.
There are different types of JIT methods:
-
Demand-driven: This is a type of JIT where you order the parts/materials needed for your project regularly. This will allow you to track how much material you have left over after using it. It will also allow you to predict how long it takes to produce more.
-
Inventory-based : You can stock the materials you need in advance. This allows you to predict how much you can expect to sell.
-
Project-driven: This is an approach where you set aside enough funds to cover the cost of your project. If you know the amount you require, you can buy the materials you need.
-
Resource-based JIT: This type of JIT is most commonly used. You assign certain resources based off demand. You will, for example, assign more staff to deal with large orders. If you don't have many orders, you'll assign fewer people to handle the workload.
-
Cost-based: This approach is very similar to resource-based. However, you don't just care about the number of people you have; you also need to consider how much each person will cost.
-
Price-based: This is very similar to cost-based, except that instead of looking at how much each individual worker costs, you look at the overall price of the company.
-
Material-based is an alternative to cost-based. Instead of looking at the total cost in the company, this method focuses on the average amount of raw materials that you consume.
-
Time-based: Another variation of resource-based JIT. Instead of focusing only on how much each employee is costing, you should focus on how long it takes to complete your project.
-
Quality-based JIT: This is another variation of resource based JIT. Instead of focusing on the cost of each worker or how long it takes, think about how high quality your product is.
-
Value-based JIT: This is the latest form of JIT. This is where you don't care about how the products perform or whether they meet customers' expectations. Instead, you are focused on adding value to the marketplace.
-
Stock-based: This stock-based method focuses on the actual quantity of products being made at any given time. It's useful when you want maximum production and minimal inventory.
-
Just-intime (JIT), planning is a combination JIT management and supply chain management. It is the process that schedules the delivery of components within a short time of their order. This is important as it reduces lead time and increases throughput.