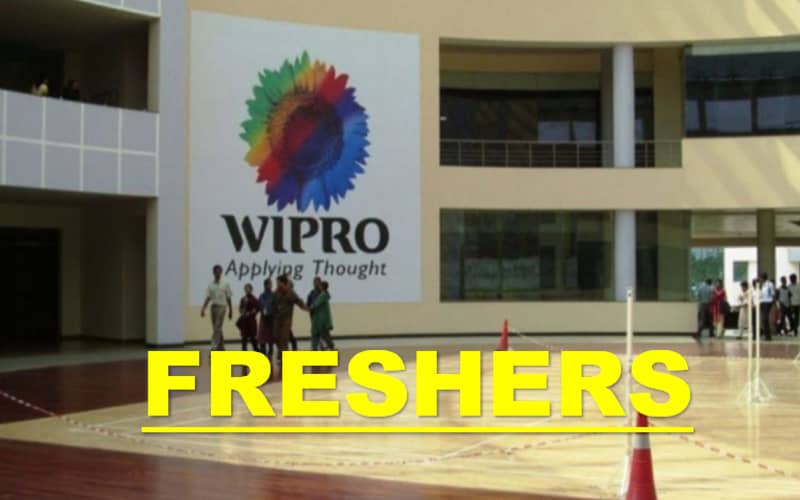
In classical economics, there are three basic sectors. These categories can be broken down into manufacturing, services, or financial activities. The characteristics and risks that businesses face are what determine how they are classified. You will find out more about each sector below. This is a brief overview of the types of businesses in each sector. If you're interested, you can continue to explore this information. But, these categories should not be viewed as mutually exclusive.
Economic activity
The factors that affect production, inputs and outputs have a significant impact on the country's economic activities. A region's economic activity is often determined by the demand for a specific good or service. There are two types of economic activity: primary and secondary. Primary economic activities provide goods or services to satisfy daily human needs, while secondary economic activities add value to raw materials and combine them to make a more valuable product. Manufacturing and processing are two examples of secondary activities.
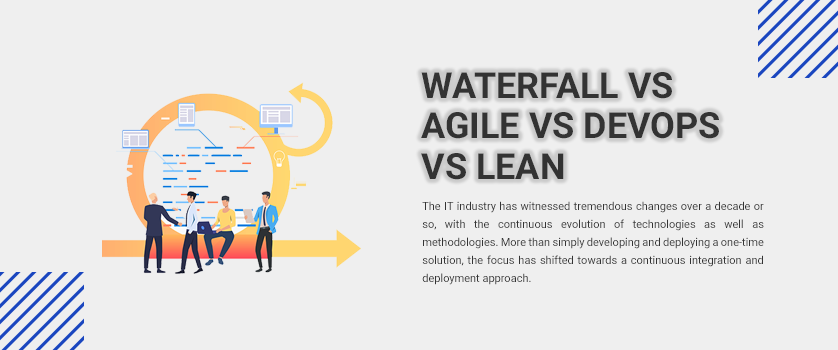
Classification of businesses
Business classification is the process by which businesses are divided into groups based upon the activities they engage in. There are two main types: primary or secondary. Primary businesses are those that use natural resources to extract them and then exchange them. The second type of business processes and transforms raw materials into products that are ready for consumption. There are many distinctions between these two types. Listed below are some of the major differences between the two types. This article can help you choose the right type of business for your company.
Characteristics
The following discussion explains the differences between the primary, secondary, and tertiary sectors and focuses on how each type of sector affects the economy. First, let's define sectors. Sectors are unique economic entities, and they respond differently to various factors. These conditions could be repeated, such business cycles, or they might be one-off events, such improvements in technology. These characteristics can help identify the most viable sector and determine their relative importance to an economy.
There are risks
Industry risk is the variance in performance between different industries and their companies. It is measured by the variation in return on equity and profitability. This can be adjusted depending on industry to reflect the performance stock markets. For example, a company that manufactures steel is considered to be high risk because of the potential for a major earthquake in the region. An analysis of these risks can help investors identify volatile sectors.
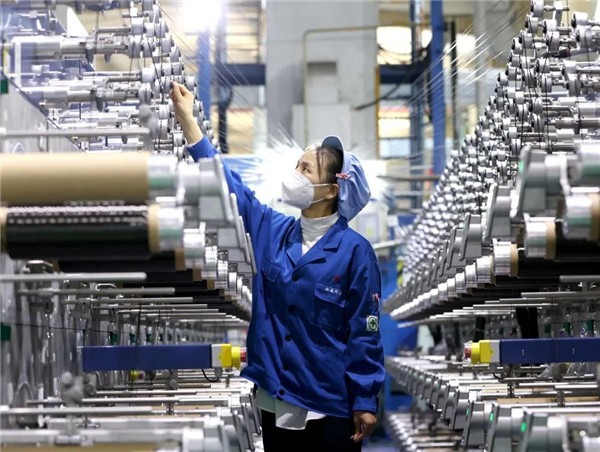
Investments
While investors often invest in certain companies, sector investing can be a great option for the more cautious investor. Sectors offer lower risks and can be found in mutual funds and exchange-traded funds. Additionally, sector investing has become a very popular investment strategy. This article will help you identify the best investments. Read on to learn more. And don't forget to check out our free resource section for more information.
FAQ
What is the role of a logistics manager
Logistics managers ensure that goods arrive on time and are unharmed. This is done using his/her knowledge of the company's products. He/she should ensure that sufficient stock is available in order to meet customer demand.
What is the job of a production plan?
Production planners ensure all aspects of the project are delivered within time and budget. They ensure that the product or service is of high quality and meets client requirements.
What does "warehouse" mean?
A warehouse, or storage facility, is where goods are stored prior to being sold. It can be indoors or out. It may also be an indoor space or an outdoor area.
What are the four types of manufacturing?
Manufacturing refers the process of turning raw materials into useful products with machines and processes. It can involve many activities like designing, manufacturing, testing packaging, shipping, selling and servicing.
What is production planning?
Production Planning includes planning for all aspects related to production. This document is designed to make sure everything is ready for when you're ready to shoot. It should also contain information on achieving the best results on set. This includes location information, crew details, equipment specifications, and casting lists.
It is important to first outline the type of film you would like to make. You may have already decided where you would like to shoot, or maybe there are specific locations or sets that you want to use. Once you have identified your locations and scenes, you can start working out which elements you require for each scene. For example, you might decide that you need a car but don't know exactly what model you want. If this is the case, you might start searching online for car models and then narrow your options by selecting from different makes.
After you have chosen the right car, you will be able to begin thinking about accessories. Do you have people who need to be seated in the front seat? Or maybe you just need someone to push the car around. You might want to change your interior color from black and white. These questions can help you decide the right look for your car. You can also think about the type of shots you want to get. You will be filming close-ups and wide angles. Maybe you want to show your engine or the steering wheel. These details will help identify the exact car you wish to film.
Once you've determined the above, it is time to start creating a calendar. You can create a schedule that will outline when you must start and finish your shoots. Every day will have a time for you to arrive at the location, leave when you are leaving and return home when you are done. So everyone is clear about what they need to do. Hire extra staff by booking them ahead of time. You should not hire anyone who doesn't show up because of your inaction.
Also, consider how many days you will be filming your schedule. Some projects are quick and easy, while others take weeks. When you are creating your schedule, you should always keep in mind whether you need more than one shot per day or not. Multiplying takes in the same area will result both in increased costs and a longer time. It is better to be cautious and take fewer shots than you risk losing money if you are not sure if multiple takes are necessary.
Budgeting is another crucial aspect of production plan. A realistic budget will help you work within your means. It is possible to reduce the budget at any time if you experience unexpected problems. However, you shouldn't overestimate the amount of money you will spend. If you underestimate how much something costs, you'll have less money to pay for other items.
Production planning is a complicated process. But once you understand how everything works together, it becomes much easier to plan future project.
How can we increase manufacturing efficiency?
The first step is to identify the most important factors affecting production time. Then we need to find ways to improve these factors. If you aren't sure where to begin, think about the factors that have the greatest impact on production time. Once you identify them, look for solutions.
Are there any Manufacturing Processes that we should know before we can learn about Logistics?
No. You don't have to know about manufacturing processes before learning about logistics. However, knowing about manufacturing processes will definitely give you a better understanding of how logistics works.
Statistics
- According to a Statista study, U.S. businesses spent $1.63 trillion on logistics in 2019, moving goods from origin to end user through various supply chain network segments. (netsuite.com)
- In 2021, an estimated 12.1 million Americans work in the manufacturing sector.6 (investopedia.com)
- In the United States, for example, manufacturing makes up 15% of the economic output. (twi-global.com)
- (2:04) MTO is a production technique wherein products are customized according to customer specifications, and production only starts after an order is received. (oracle.com)
- Many factories witnessed a 30% increase in output due to the shift to electric motors. (en.wikipedia.org)
External Links
How To
How to use 5S in Manufacturing to Increase Productivity
5S stands in for "Sort", the "Set In Order", "Standardize", or "Separate". Toyota Motor Corporation invented the 5S strategy in 1954. It helps companies achieve higher levels of efficiency by improving their work environment.
The idea behind standardizing production processes is to make them repeatable and measurable. It means tasks like cleaning, sorting or packing, labeling, and storing are done every day. Workers can be more productive by knowing what to expect.
Implementing 5S involves five steps: Sort, Set in Order, Standardize Separate, Store, and Each step requires a different action to increase efficiency. Sorting things makes it easier to find them later. When items are ordered, they are put together. Once you have separated your inventory into groups and organized them, you will store these groups in easily accessible containers. Finally, label all containers correctly.
Employees will need to be more critical about their work. Employees must understand why they do certain tasks and decide if there's another way to accomplish them without relying on the old ways of doing things. To be successful in the 5S system, employees will need to acquire new skills and techniques.
The 5S method increases efficiency and morale among employees. As they begin to see improvements, they feel motivated to continue working towards the goal of achieving higher levels of efficiency.