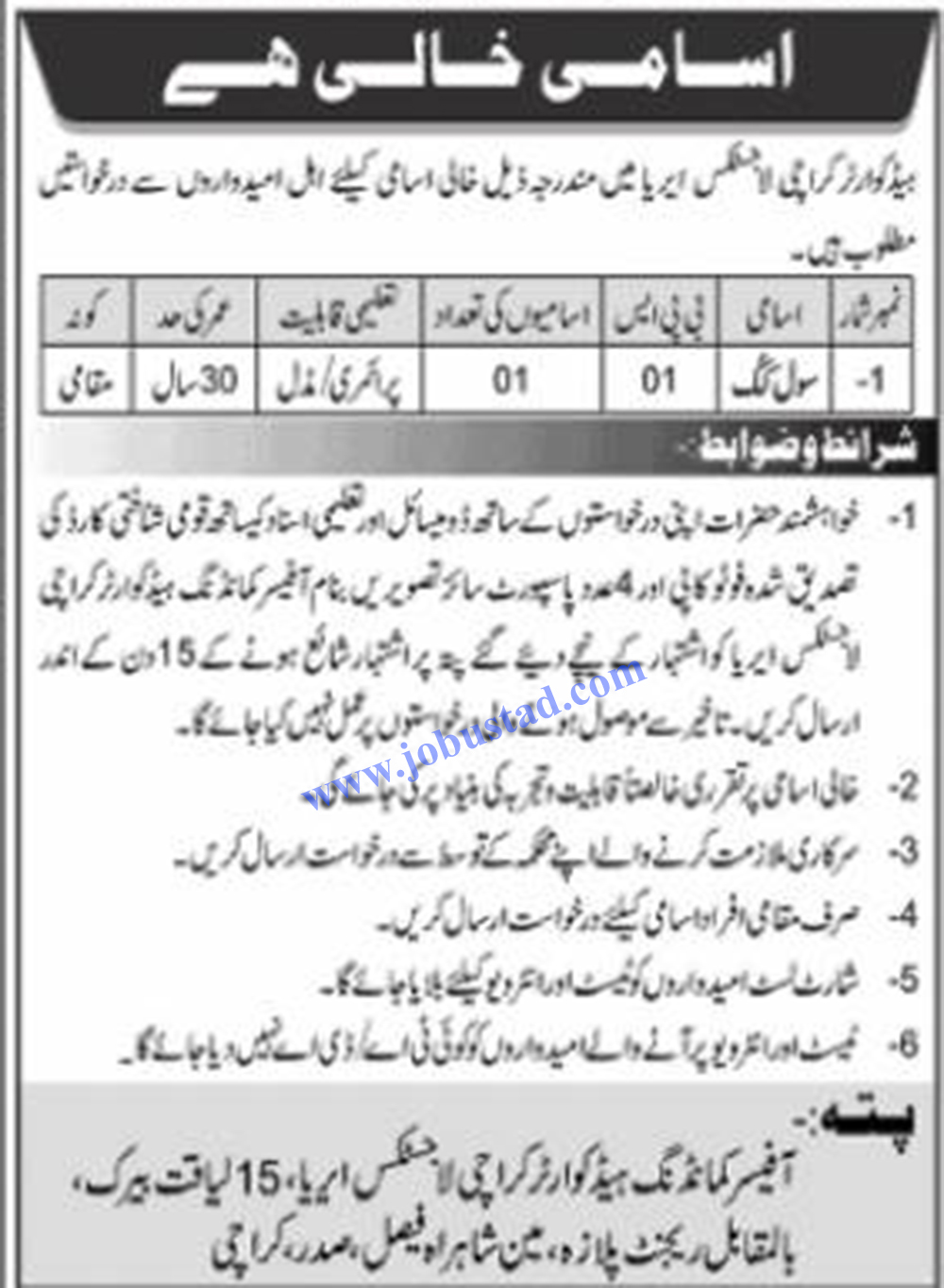
Industrial engineers use their expertise in mathematics and engineering to optimize the operation of a company. This includes the development of blueprints for machinery and the analysis of statistical data. An industrial engineer can help the management make better decisions and increase efficiency.
A typical job for an industrial engineer technician is to perform time and motion studies to improve productivity, evaluate performance, and implement changes. They might also be asked to analyze data related to an industrial safety and health program.
They also perform technical tasks, such as creating diagrams and schematics that illustrate the process. They also conduct a variety quality control tests on products in order to ensure they meet standards.
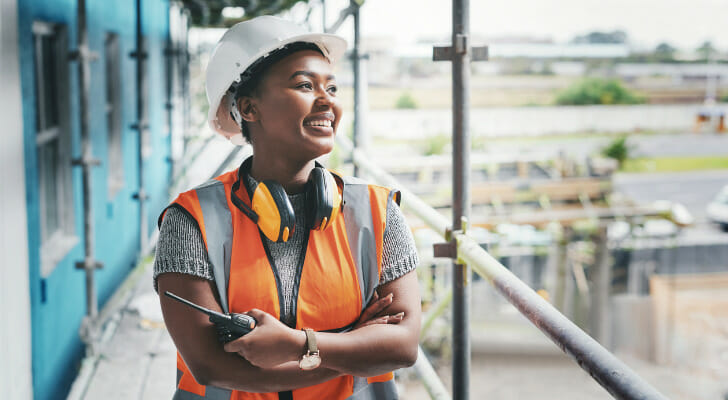
An industrial engineer's most common job duties include planning workflow, analyzing production costs and gauging prototypes. They also assess equipment capacities and develop efficient operating procedures. A variety of industries employ them, including aerospace engineering, pharmaceuticals electronics, food, and automobile. Most work full-time. The average annual salary for these workers is $53,000, although those with more education and experience might be able to make a better living.
Industrial engineers do not need any specific degrees. However, a strong math skills, critical thinking, and an eye for detail are vital. They must also be able talk with and interact with employees.
An industrial engineer technician who is skilled in recognizing the key factors will ensure the most efficient workflow. They must also be able recognize the importance of reducing waste materials and avoiding unproductive practices. They are able to identify ways to improve the workplace and save money over the long-term.
They are also likely to be the first people in their organization to try out new ideas. The best way to achieve this is by creating a strategic plan. It's like fitting together the pieces of a giant puzzle.
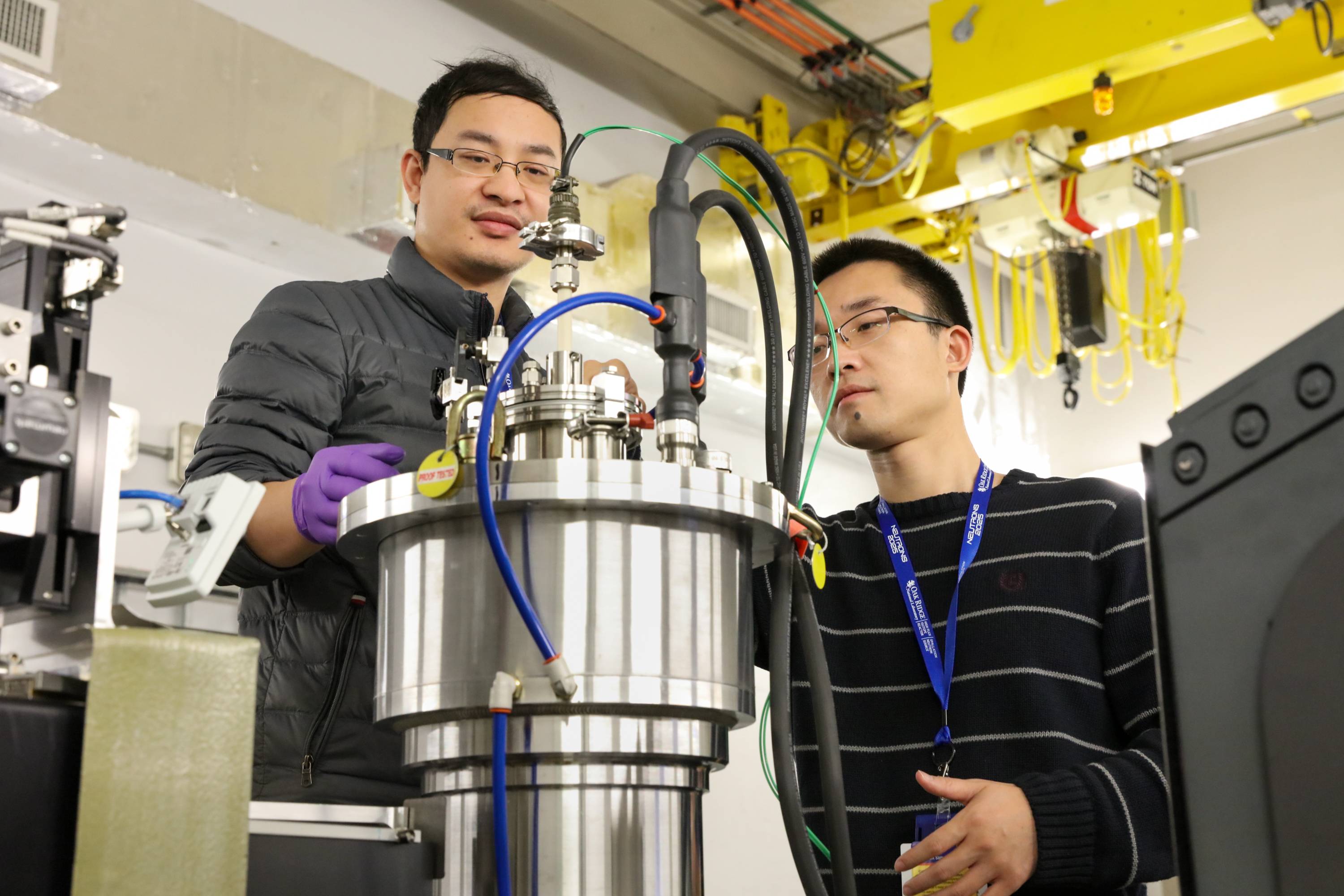
The quality control function is another important role of an industrial engineer. The automation of more industries will reduce the number jobs but it will not stop the growth of industrial engineering technicians.
An engineer might use a motion and time study to determine how long it takes for a task to be completed. This is the most accurate way to gauge the system's performance. This study could be used by engineers to establish a standard production level. These results will then be used to make improvements to the way an operation is run.
Many universities offer an industrial engineering technology program, including Liberty University. This program offers a variety of courses that range from motor controls and hydraulics to self-management skills. This program teaches students how to solve problems and work in teams to reach their goals.
FAQ
What are manufacturing & logistics?
Manufacturing is the act of producing goods from raw materials using machines and processes. Logistics includes all aspects related to supply chain management, such as procurement, distribution planning, inventory control and transportation. As a broad term, manufacturing and logistics often refer to both the creation and delivery of products.
What is production planning?
Production Planning includes planning for all aspects related to production. This document ensures that everything is prepared and available when you are ready for shooting. It should also contain information on achieving the best results on set. This information includes locations, crew details and equipment requirements.
The first step is to decide what you want. You might have an idea of where you want to film, or you may have specific locations or sets in mind. Once you have identified your locations and scenes, you can start working out which elements you require for each scene. Perhaps you have decided that you need to buy a car but aren't sure which model. In this case, you could start looking up cars online to find out what models are available and then narrow your choices by choosing between different makes and models.
Once you have found the right vehicle, you can think about adding accessories. Are you looking for people to sit in the front seats? Or perhaps you need someone walking around the back of the car? You may want to change the interior's color from black or white. These questions can help you decide the right look for your car. Another thing you can do is think about what type of shots are desired. Do you want to film close-ups, or wider angles? Maybe you want the engine or the steering wheels to be shown. These details will help identify the exact car you wish to film.
Once you have made all the necessary decisions, you can start to create a schedule. You will know when you should start and when you should finish shooting. You will need to know when you have to be there, what time you have to leave and when your return home. This way, everyone knows what they need to do and when. Hire extra staff by booking them ahead of time. It's not worth paying someone to show up if you haven't told him.
You will need to factor in the days that you have to film when creating your schedule. Some projects may only take a couple of days, while others could last for weeks. When you are creating your schedule, you should always keep in mind whether you need more than one shot per day or not. Multiple shots at the same location can increase costs and make it more difficult to complete. You can't be certain if you will need multiple takes so it is better not to shoot too many.
Budgeting is another important aspect of production planning. Setting a realistic budget is essential as it will allow you to work within your means. It is possible to reduce the budget at any time if you experience unexpected problems. It is important to not overestimate how much you will spend. If you underestimate how much something costs, you'll have less money to pay for other items.
Production planning is a very detailed process, but once you understand how everything works together, it becomes easier to plan future projects.
Do we need to know about Manufacturing Processes before learning about Logistics?
No. No. But, being familiar with manufacturing processes will give you a better understanding about how logistics works.
What are the 4 types of manufacturing?
Manufacturing refers the process of turning raw materials into useful products with machines and processes. Manufacturing can include many activities such as designing and building, testing, packaging shipping, selling, servicing, and other related activities.
What makes a production planner different from a project manger?
The main difference between a production planner and a project manager is that a project manager is usually the person who plans and organizes the entire project, whereas a production planner is mainly involved in the planning stage of the project.
What jobs are available in logistics?
There are many jobs available in logistics. These are some of the jobs available in logistics:
-
Warehouse workers – They load and unload pallets and trucks.
-
Transport drivers - These are people who drive trucks and trailers to transport goods or perform pick-ups.
-
Freight handlers are people who sort and pack freight into warehouses.
-
Inventory managers – These people oversee inventory at warehouses.
-
Sales representatives - They sell products.
-
Logistics coordinators – They plan and coordinate logistics operations.
-
Purchasing agents – They buy goods or services necessary to run a company.
-
Customer service representatives - Answer calls and email from customers.
-
Shippers clerks - They process shipping order and issue bills.
-
Order fillers - These people fill orders based on what has been ordered.
-
Quality control inspectors (QCI) - They inspect all incoming and departing products for potential defects.
-
Others - There are many other types of jobs available in logistics, such as transportation supervisors, cargo specialists, etc.
What is meant by manufacturing industries?
Manufacturing Industries are those businesses that make products for sale. The people who buy these products are called consumers. To accomplish this goal, these companies employ a range of processes including distribution, sales, management, and production. They produce goods from raw materials by using machines and other machinery. This includes all types and varieties of manufactured goods, such as food items, clothings, building supplies, furnitures, toys, electronics tools, machinery vehicles, pharmaceuticals medical devices, chemicals, among others.
Statistics
- According to a Statista study, U.S. businesses spent $1.63 trillion on logistics in 2019, moving goods from origin to end user through various supply chain network segments. (netsuite.com)
- According to the United Nations Industrial Development Organization (UNIDO), China is the top manufacturer worldwide by 2019 output, producing 28.7% of the total global manufacturing output, followed by the United States, Japan, Germany, and India.[52][53] (en.wikipedia.org)
- [54][55] These are the top 50 countries by the total value of manufacturing output in US dollars for its noted year according to World Bank.[56] (en.wikipedia.org)
- You can multiply the result by 100 to get the total percent of monthly overhead. (investopedia.com)
- In 2021, an estimated 12.1 million Americans work in the manufacturing sector.6 (investopedia.com)
External Links
How To
Six Sigma in Manufacturing
Six Sigma is defined by "the application SPC (statistical process control) techniques to achieve continuous improvements." Motorola's Quality Improvement Department created Six Sigma at their Tokyo plant, Japan in 1986. Six Sigma's basic concept is to improve quality and eliminate defects through standardization. In recent years, many companies have adopted this method because they believe there is no such thing as perfect products or services. Six Sigma's primary goal is to reduce variation from the average value of production. This means that you can take a sample from your product and then compare its performance to the average to find out how often the process differs from the norm. If there is a significant deviation from the norm, you will know that something needs to change.
Understanding how variability works in your company is the first step to Six Sigma. Once you understand this, you can then identify the causes of variation. These variations can also be classified as random or systematic. Random variations occur when people make mistakes; systematic ones are caused by factors outside the process itself. For example, if you're making widgets, and some of them fall off the assembly line, those would be considered random variations. If however, you notice that each time you assemble a widget it falls apart in exactly the same spot, that is a problem.
Once you've identified the problem areas you need to find solutions. This could mean changing your approach or redesigning the entire process. To verify that the changes have worked, you need to test them again. If they don't work you need to rework them and come up a better plan.