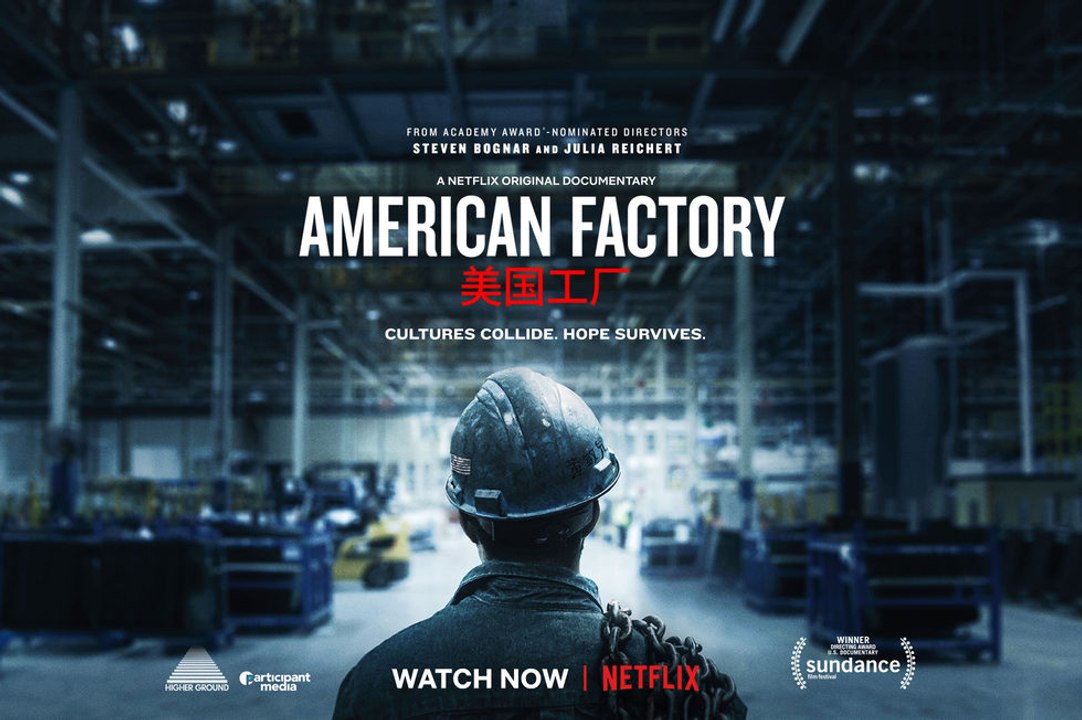
Kanban models in manufacturing can improve efficiency and lower costs. These principles aim to minimize downtime and inefficiencies. This results in faster manufacturing and delivery times, and better customer service. It allows for continuous improvement.
Kanban is a method to manage and organize work flow. It helps manufacturers and teams to better track and monitor the processes they perform, and to improve productivity. Kanban involves the creation of a visual representation of the steps involved in a particular process and the identification and minimization or inefficiencies.
You can either use a software program or manually to implement the kanban method. Software can be used to help teams determine what should be done and who should. The kanban method also allows for employees to adapt to feedback and make improvements to their processes. It is also useful in brainstorming.
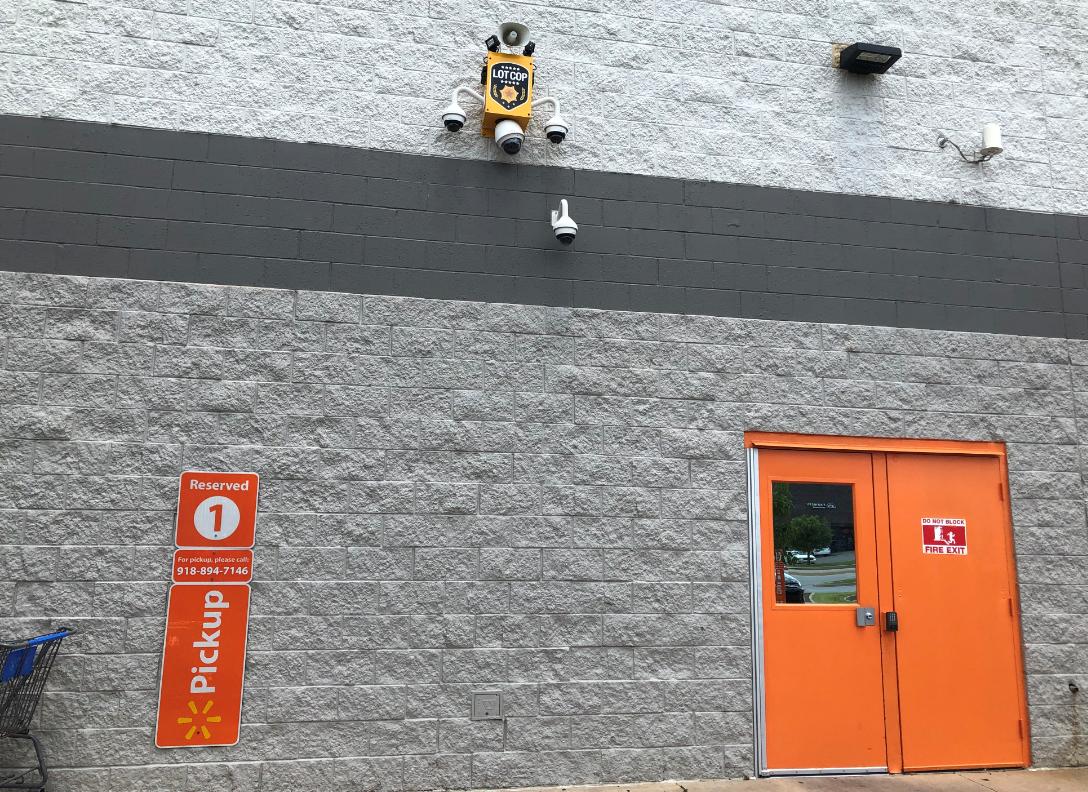
Kanban boards, which are boards that show a process, are one of the most well-known Kanban examples in manufacturing. The board lists the priority of each step in the process. Contacting a supplier is the first task. The second task will be to order the supplies required to complete your work. The third task is to begin manufacturing. The fourth task is testing and shipping the final product.
The kanban board allows teams to visualise their process and make small changes as necessary. Kanban boards are also useful for improving communication between teams as well as identifying and addressing any bottlenecks.
Kanban can also be used to reduce waste and increase information sharing. This is especially important when a company is trying to implement Lean principles. It is possible to accumulate waste over the course of a manufacturing operation in many ways. The manufacturer can add value to every stage of the manufacturing process by removing waste. You can also use the kanban method to manage inventory. It can help to control inventory overstocking.
Kanban is a great method to visualize and reduce costs. Kanban can help improve efficiency and reduce the number of items required to complete a job. It improves communication and minimizes downtime. The kanban technique is a great example how technology can be used for a complex task.
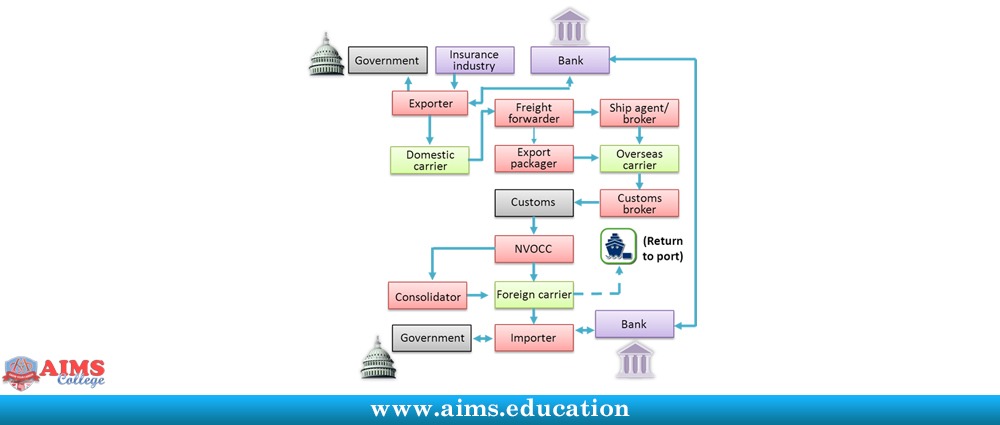
The Kanban method can be used as a brainstorming tool and to increase productivity. It can be used to connect companies to suppliers, and to improve communication. It is also useful in improving quality and streamlining the production process.
One of the most well-known Kanban methods in manufacturing is the board. Tasks are organized according to priority and time needed to complete them. The board also displays the steps involved in a process, such as design, manufacturing, and testing.
FAQ
What is the role of a logistics manager
A logistics manager makes sure that all goods are delivered on-time and in good condition. This is done by using his/her experience and knowledge of the company's products. He/she must also ensure sufficient stock to meet the demand.
What are manufacturing and logistics?
Manufacturing is the process of creating goods from raw materials by using machines and processes. Logistics encompasses the management of all aspects associated with supply chain activities such as procurement, production planning, distribution and inventory control. It also includes customer service. As a broad term, manufacturing and logistics often refer to both the creation and delivery of products.
What is the responsibility of a production planner?
Production planners ensure that all project aspects are completed on time, within budget and within the scope. They make sure that the product and services meet client expectations.
What is production management?
Production Planning refers to the development of a plan for every aspect of production. This document is designed to make sure everything is ready for when you're ready to shoot. This document should also include information on how to get the best result on set. This information includes locations, crew details and equipment requirements.
The first step in filming is to define what you want. You may have decided where to shoot or even specific locations you want to use. Once you have determined your scenes and locations, it is time to start figuring out the elements that you will need for each scene. If you decide you need a car and don't know what model to choose, this could be an example. You could look online for cars to see what options are available, and then narrow down your choices by selecting between different makes or models.
After you have chosen the right car, you will be able to begin thinking about accessories. Do you have people who need to be seated in the front seat? You might also need someone to help you get around the back. You may want to change the interior's color from black or white. These questions will help to determine the style and feel of your car. The type of shots that you are looking for is another thing to consider. You will be filming close-ups and wide angles. Maybe you want to show the engine and the steering wheel. These things will help you to identify the car that you are looking for.
Once you have established all the details, you can create a schedule. A schedule will tell you when you need to start shooting and when you need to finish. Every day will have a time for you to arrive at the location, leave when you are leaving and return home when you are done. This way, everyone knows what they need to do and when. You can also make sure to book extra staff in advance if you have to hire them. It is not worth hiring someone who won’t show up because you didn’t tell him.
Your schedule will also have to be adjusted to reflect the number of days required to film. Some projects may only take a couple of days, while others could last for weeks. When you are creating your schedule, you should always keep in mind whether you need more than one shot per day or not. Multiple takes at the same place will result in higher costs and longer completion times. You can't be certain if you will need multiple takes so it is better not to shoot too many.
Budget setting is an important part of production planning. It is important to set a realistic budget so you can work within your budget. Keep in mind that you can always reduce your budget if you face unexpected difficulties. However, it is important not to overestimate the amount that you will spend. If you underestimate the cost of something, you will have less money left after paying for other items.
Production planning is a detailed process. But, once you understand the workings of everything, it becomes easier for future projects to be planned.
How can manufacturing efficiency improved?
First, determine which factors have the greatest impact on production time. We must then find ways that we can improve these factors. If you don’t know how to start, look at which factors have the greatest impact upon production time. Once you have identified them, it is time to identify solutions.
What's the difference between Production Planning & Scheduling?
Production Planning (PP) refers to the process of determining how much production is needed at any given moment. This can be done by forecasting demand and identifying production capabilities.
Scheduling involves the assignment of dates and times to tasks in order to complete them within the timeframe.
Statistics
- Job #1 is delivering the ordered product according to specifications: color, size, brand, and quantity. (netsuite.com)
- It's estimated that 10.8% of the U.S. GDP in 2020 was contributed to manufacturing. (investopedia.com)
- In the United States, for example, manufacturing makes up 15% of the economic output. (twi-global.com)
- (2:04) MTO is a production technique wherein products are customized according to customer specifications, and production only starts after an order is received. (oracle.com)
- According to a Statista study, U.S. businesses spent $1.63 trillion on logistics in 2019, moving goods from origin to end user through various supply chain network segments. (netsuite.com)
External Links
How To
How to use the Just In-Time Production Method
Just-intime (JIT), which is a method to minimize costs and maximize efficiency in business process, is one way. It's the process of obtaining the right amount and timing of resources when you need them. This means that you only pay the amount you actually use. Frederick Taylor developed the concept while working as foreman in early 1900s. He saw how overtime was paid to workers for work that was delayed. He realized that workers should have enough time to complete their jobs before they begin work. This would help increase productivity.
The idea behind JIT is that you should plan ahead and have everything ready so you don't waste money. The entire project should be looked at from start to finish. You need to ensure you have enough resources to tackle any issues that might arise. If you anticipate that there might be problems, you'll have enough people and equipment to fix them. This way, you won't end up paying extra money for things that weren't really necessary.
There are many JIT methods.
-
Demand-driven JIT: This is a JIT that allows you to regularly order the parts/materials necessary for your project. This will let you track the amount of material left over after you've used it. This will allow you to calculate how long it will take to make more.
-
Inventory-based : You can stock the materials you need in advance. This allows for you to anticipate how much you can sell.
-
Project-driven: This means that you have enough money to pay for your project. When you know how much you need, you'll purchase the appropriate amount of materials.
-
Resource-based JIT : This is probably the most popular type of JIT. You allocate resources based on the demand. You might assign more people to help with orders if there are many. If you don't receive many orders, then you'll assign fewer employees to handle the load.
-
Cost-based : This is similar in concept to resource-based. But here, you aren't concerned about how many people your company has but how much each individual costs.
-
Price-based pricing: This is similar in concept to cost-based but instead you look at how much each worker costs, it looks at the overall company's price.
-
Material-based: This approach is similar to cost-based. However, instead of looking at the total cost for the company, you look at how much you spend on average on raw materials.
-
Time-based JIT is another form of resource-based JIT. Instead of worrying about how much each worker costs, you can focus on how long the project takes.
-
Quality-based: This is yet another variation of resource-based JIT. Instead of looking at the labor costs and time it takes to make a product, think about its quality.
-
Value-based JIT: One of the most recent forms of JIT. In this scenario, you're not concerned about how products perform or whether customers expect them to meet their expectations. Instead, your goal is to add value to the market.
-
Stock-based: This is an inventory-based method that focuses on the actual number of items being produced at any given time. It is used when production goals are met while inventory is kept to a minimum.
-
Just-in-time planning (JIT): This is a combination JIT and supply-chain management. It is the process of scheduling components' delivery as soon as they have been ordered. It's important because it reduces lead times and increases throughput.