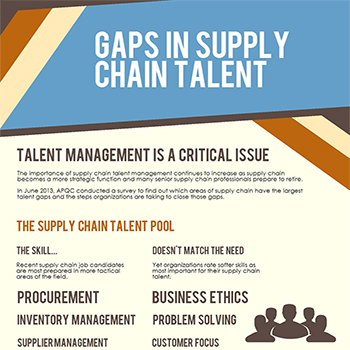
In recent years, there have been many factors that led to a huge shortage of chips. These include transportation issues and manufacturing problems. Many disasters have resulted in the closing of chip plant facilities. This has affected consumer devices such as gaming consoles, healthcare devices, and data centers. The Chinese government has made many efforts to promote the manufacturing of semiconductors in China. To support chip manufacturers, the government even created an investment fund.
This effort has resulted in China seeing remarkable progress in its chip production over the last few years. According to IC Insights by 2025, China's chip production is expected to increase by 19.4%. But, it still has a lot of work to do before the industry reaches its former level. Despite these advances, the number of domestic chip companies is still limited. Many of these companies aren't yet independent.
Some of the most prominent chip makers in China include Huawei, Midea, Oppo, and Xiaomi. Chinese companies are also gaining significant market share in the mobile processor space. They are also creating their own chips, which allows them to increase their chip making capabilities. This has allowed them to be more competitive in the market.
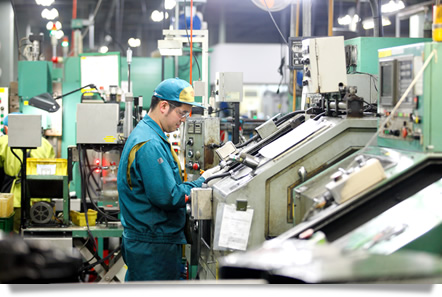
China is rapidly becoming a key chip manufacturing center, but there are still some limitations. Chinese companies have limited resources and are not able to mass-produce high end microchips. These chips are used in smartphones and other wearable devices as well as servers. The country isn't yet able produce all the raw materials needed for chip manufacturing. These include tantalum (enriched isotopes), and neon. These raw materials undergo chemical processing to be refined.
China wants to reduce its dependency on imported chips. China plans to produce 70% by 2025 of its chip production there. This will be difficult to achieve, however. China currently has 32 registered chips companies. Many more are still awaiting IPOs. The government is actively marketing its industrial strategy. It is trying to get more companies to produce chips in the country. This is a huge challenge due to the lack of resources.
The US semiconductor industry faces an unprecedented shortage of talent. Washington also recently adopted new rules to limit the US's ability to support chip production.
TSMC, the largest chipmaker in the world, has yet to make any announcements regarding a European plant. But it has not ruled out building an older-generation chip plant there. The company has also partnered with European automakers to purchase less-advanced chips. However, European auto companies have mostly opposed the idea. Adding a European plant would enhance the supply chain. Chips would then have to be shipped back into Asia for further processing. This could extend the chip's lifetime by several years.
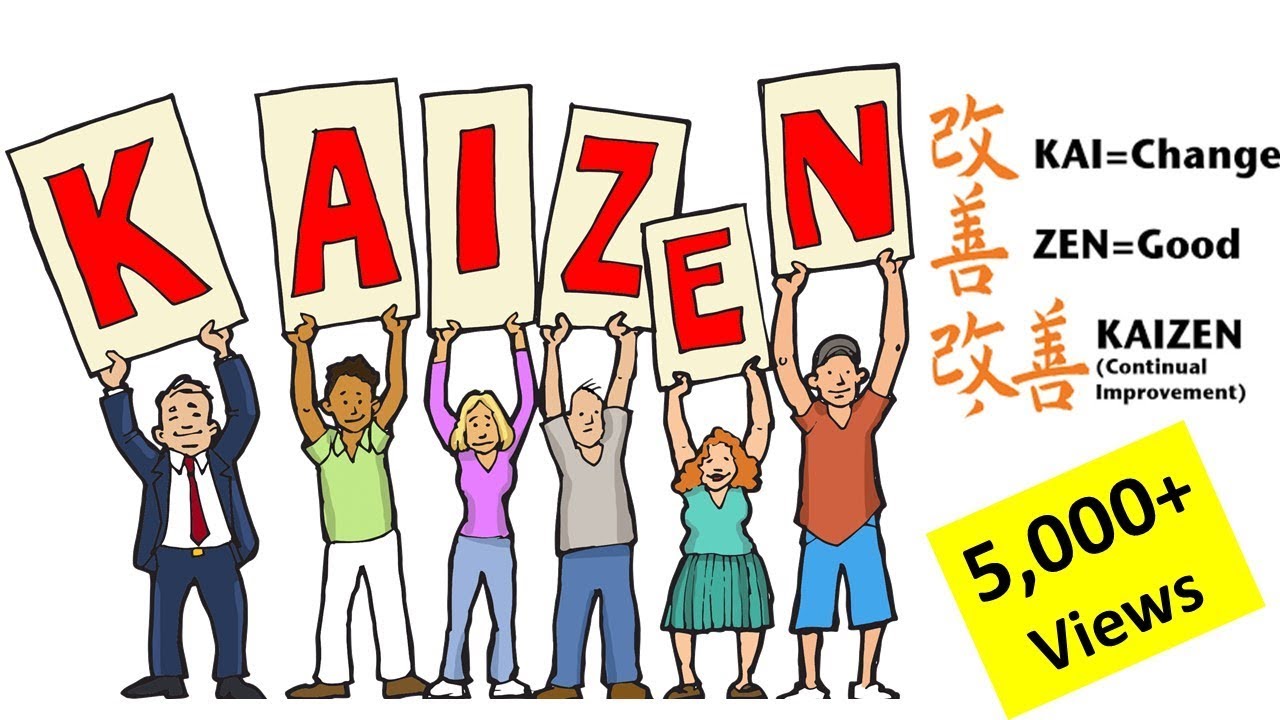
According to the US Commerce Department's report, the chip shortage would become serious in 2021. This has resulted in long delays for customers. The shortage has also affected transportation, healthcare, and gaming consoles. However, the government's investments in reshoring chip production will help create hundreds of thousands of jobs in the US, and ensure a more resilient chip supply chain.
FAQ
What skills should a production planner have?
You must be flexible and organized to become a productive production planner. You must also be able to communicate effectively with clients and colleagues.
What is production planning?
Production Planning includes planning for all aspects related to production. This document will ensure everything is in order and ready to go when you need it. It should also contain information on achieving the best results on set. This information includes locations, crew details and equipment requirements.
The first step is to outline what you want to film. You may have already chosen the location you want, or there are locations or sets you prefer. Once you have determined your scenes and locations, it is time to start figuring out the elements that you will need for each scene. Perhaps you have decided that you need to buy a car but aren't sure which model. If this is the case, you might start searching online for car models and then narrow your options by selecting from different makes.
Once you have found the right vehicle, you can think about adding accessories. Do you need people sitting in the front seats? Or maybe you just need someone to push the car around. Perhaps you would like to change the interior colour from black to white. These questions will help guide you in determining the ideal look and feel for your car. You can also think about the type of shots you want to get. Do you want to film close-ups, or wider angles? Perhaps you want to show the engine or the steering wheel? This will allow you to determine the type of car you want.
Once you have determined all of the above, you can move on to creating a schedule. The schedule will show you when to begin shooting and when to stop. A schedule for each day will detail when you should arrive at the location and when you need leave. This way, everyone knows what they need to do and when. Hire extra staff by booking them ahead of time. It is not worth hiring someone who won’t show up because you didn’t tell him.
Also, consider how many days you will be filming your schedule. Some projects can be completed in a matter of days or weeks. Others may take several days. You should consider whether you will need more than one shot per week when creating your schedule. Multiplying takes in the same area will result both in increased costs and a longer time. It is better to be cautious and take fewer shots than you risk losing money if you are not sure if multiple takes are necessary.
Budgeting is another crucial aspect of production plan. As it will allow you and your team to work within your financial means, setting a realistic budget is crucial. Keep in mind that you can always reduce your budget if you face unexpected difficulties. However, it is important not to overestimate the amount that you will spend. You'll end up with less money after paying for other things if the cost is underestimated.
Planning production is a tedious process. Once you have a good understanding of how everything works together, planning future projects becomes easy.
How can manufacturing overproduction be reduced?
The key to reducing overproduction lies in developing better ways to manage inventory. This would reduce the amount of time spent on unnecessary activities such as purchasing, storing, and maintaining excess stock. This would allow us to use our resources for more productive tasks.
Kanban systems are one way to achieve this. A Kanbanboard is a visual tool that allows you to keep track of the work being done. Kanban systems are where work items travel through a series of states until reaching their final destination. Each state represents an individual priority level.
If work is moving from one stage to the other, then the current task can be completed and moved on to the next. But if a task remains in the beginning stages it will stay that way until it reaches its end.
This helps to keep work moving forward while ensuring that no work is left behind. Managers can monitor the work being done by Kanban boards to see what is happening at any given time. This information allows them to adjust their workflow based on real-time data.
Lean manufacturing is another way to manage inventory levels. Lean manufacturing is about eliminating waste from all stages of the production process. Waste includes anything that does not add value to the product. These are some of the most common types.
-
Overproduction
-
Inventory
-
Unnecessary packaging
-
Material surplus
Manufacturers can reduce their costs and improve their efficiency by using these ideas.
What are my options for learning more about manufacturing
Practical experience is the best way of learning about manufacturing. You can also read educational videos or take classes if this isn't possible.
What do we need to know about Manufacturing Processes in order to learn more about Logistics?
No. It doesn't matter if you don't know anything about manufacturing before you learn about logistics. However, knowing about manufacturing processes will definitely give you a better understanding of how logistics works.
Statistics
- It's estimated that 10.8% of the U.S. GDP in 2020 was contributed to manufacturing. (investopedia.com)
- You can multiply the result by 100 to get the total percent of monthly overhead. (investopedia.com)
- Many factories witnessed a 30% increase in output due to the shift to electric motors. (en.wikipedia.org)
- According to the United Nations Industrial Development Organization (UNIDO), China is the top manufacturer worldwide by 2019 output, producing 28.7% of the total global manufacturing output, followed by the United States, Japan, Germany, and India.[52][53] (en.wikipedia.org)
- According to a Statista study, U.S. businesses spent $1.63 trillion on logistics in 2019, moving goods from origin to end user through various supply chain network segments. (netsuite.com)
External Links
How To
How to Use Lean Manufacturing in the Production of Goods
Lean manufacturing is a management system that aims at increasing efficiency and reducing waste. It was developed in Japan during the 1970s and 1980s by Taiichi Ohno, who received the Toyota Production System (TPS) award from TPS founder Kanji Toyoda. Michael L. Watkins published the original book on lean manufacturing, "The Machine That Changed the World," in 1990.
Lean manufacturing can be described as a set or principles that are used to improve quality, speed and cost of products or services. It emphasizes the elimination of defects and waste throughout the value stream. Lean manufacturing is also known as just in time (JIT), zero defect total productive maintenance(TPM), and five-star (S). Lean manufacturing is about eliminating activities that do not add value, such as inspection, rework, and waiting.
Lean manufacturing not only improves product quality but also reduces costs. Companies can also achieve their goals faster by reducing employee turnover. Lean Manufacturing is one of the most efficient ways to manage the entire value chains, including suppliers and customers as well distributors and retailers. Many industries worldwide use lean manufacturing. Toyota's philosophy is the foundation of its success in automotives, electronics and appliances, healthcare, chemical engineers, aerospace, paper and food, among other industries.
Lean manufacturing is based on five principles:
-
Define Value: Identify the social value of your business and what sets you apart.
-
Reduce waste - Get rid of any activity that does not add value to the supply chain.
-
Create Flow – Ensure that work flows smoothly throughout the process.
-
Standardize & Simplify - Make processes as consistent and repeatable as possible.
-
Build Relationships - Establish personal relationships with both internal and external stakeholders.
Lean manufacturing, although not new, has seen renewed interest in the economic sector since 2008. Many companies have adopted lean manufacturing methods to increase their marketability. According to some economists, lean manufacturing could be a significant factor in the economic recovery.
Lean manufacturing is now becoming a common practice in the automotive industry, with many benefits. These include higher customer satisfaction levels, reduced inventory levels as well as lower operating costs.
You can apply Lean Manufacturing to virtually any aspect of your organization. Lean manufacturing is most useful in the production sector of an organisation because it ensures that each step in the value-chain is efficient and productive.
There are three types of lean manufacturing.
-
Just-in Time Manufacturing (JIT), also known as "pull system": This form of lean manufacturing is often referred to simply as "pull". JIT refers to a system in which components are assembled at the point of use instead of being produced ahead of time. This method reduces lead times, increases availability, and decreases inventory.
-
Zero Defects Manufacturing - ZDM: ZDM focuses its efforts on making sure that no defective units leave a manufacturing facility. It is better to repair a part than have it removed from the production line if it needs to be fixed. This is true even for finished products that only require minor repairs prior to shipping.
-
Continuous Improvement (CI), also known as Continuous Improvement, aims at improving the efficiency of operations through continuous identification and improvement to minimize or eliminate waste. Continuous improvement involves continuous improvement of processes and people as well as tools.