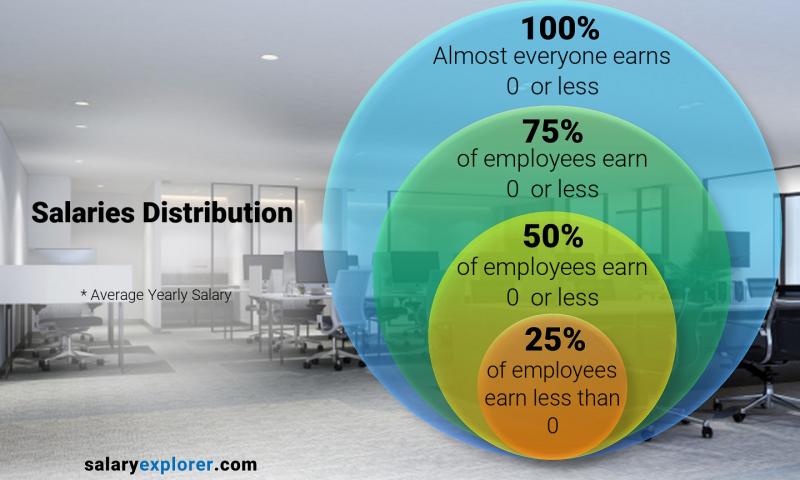
The term advanced manufacturing refers to the use of innovative technology to enhance processes and products. The technology used in this process can be classified either as "innovative," "advanced" or "cutting edge". As the number of companies that use advanced manufacturing increases, these industries are increasingly integrating new and innovative technologies into their manufacturing processes. Below are some examples of advanced manufacturing. These are the most popular technologies in advanced manufacturing.
Continuous manufacturing
Continuous manufacturing was first described in the 1700s, when it was used for making pig iron in blast furnaces. Since then, the idea has spread to other industries, such as automotive, food, oil, refining, chemicals and pulp & paper. Continuous manufacturing has captured the attention of CMOs from top pharma and other big players in the biopharmaceutical market.
In a recent commentary, the FDA and its partners discussed the benefits of using continuous manufacturing to produce therapeutic proteins. This legislation would establish national centers to help companies develop standards and advance the field. This legislation is intended to improve the creation and use of medical products. Further, it would also encourage companies to use continuous manufacturing to develop and improve products. But it is essential to ensure that continuous manufacture processes are safe.
Automated processes
It is hard to overstate the benefits of automation in advanced manufacturing. Automating processes in advanced manufacturing is the best way to maximize production efficiency and make the most of your floor space. In order to reduce costs and increase production efficiency, manufacturers can collect data and leverage automation technologies. Automation in the process industry also helps to save time and money. The initial investment is not cheap, but it will ultimately increase the bottom line for a manufacturing company.
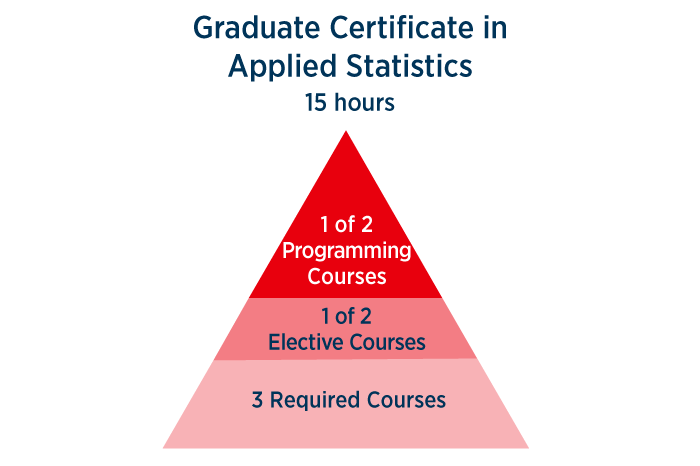
Modern companies combine advanced manufacturing processes and automated processes. Audi, for example, uses automated welding and bonding to reduce production times and save energy and weight. They also employ advanced manufacturing methods such as regenerativebraking in conveyors. The biggest advancement in manufacturing is 3D printing, which has been around since the 1980s, but has only recently reached mainstream adoption. What makes 3D printing so appealing to manufacturers?
Internet of Things
Manufacturing is being transformed by the IIoT revolution. This revolution uses sensors to monitor machinery and processes. These sensors gather data from many parts of manufacturing and feed this data to a central center station. Data is then analysed to aid in optimizing processes and eliminating waste. Advanced manufacturers already utilize IIoT sensors to monitor their processes and optimize production. The IIoT can be described as the industrial equivalent of key fobs.
To deploy IIoT effectively and efficiently, you need a roadmap and the development capabilities to create use cases. The following roadmap is provided by an automaker. It shows three phases of deployment.
Cost-effectiveness
Costs of advanced manufacturing may not be directly comparable to traditional production systems. The traditional cost-benefit analysis, however, is not sufficient to evaluate economic benefits. A holistic model that incorporates both benefits and costs can be used to identify new advantages and speed decision-making. Munker and Schroer present a cost-benefit analysis that addresses the most important issues related to AMS implementation.
Information technology is rapidly changing the face and cost of manufacturing. The production systems are becoming more intelligent and networked. The cost pressure is increasing, putting more emphasis on productivity and company's ability respond to customer demands. Rapid adoption of advanced manufacturing technology will likely speed up the implementation of these technologies as well as their cost-effectiveness. As the industry digitizes, this will likely lead to a rapid adoption of such technologies.
Human error reduction
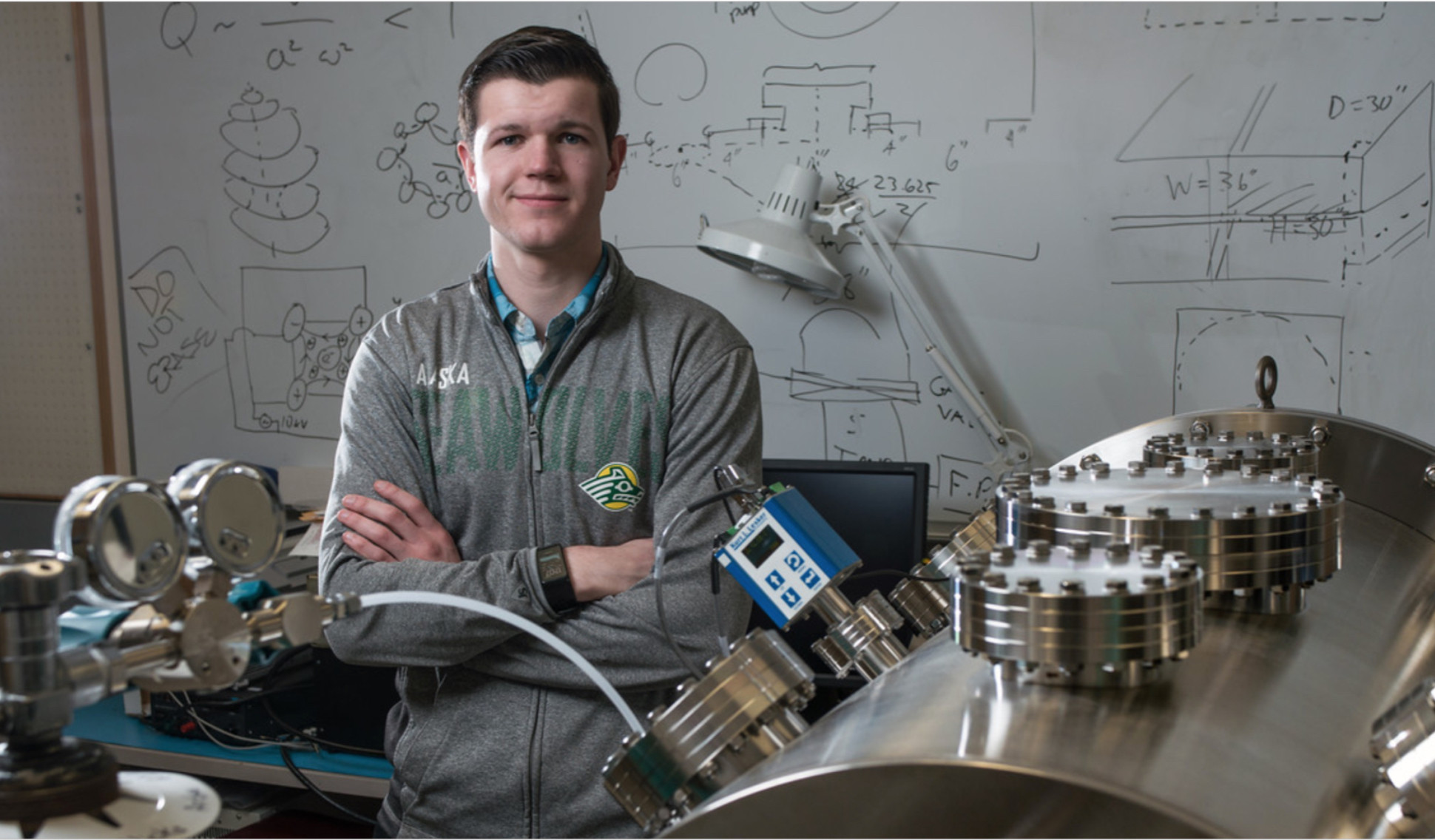
Although humans can make mistakes, the manufacturing process used to create a product is designed to minimize them. Human error can occur when employees fail to follow the written process or misunderstand instructions. When making drugs, pharmaceutical labs, for instance, must adhere to very strict procedures. An employee might think they understand the process, and so proceed to make the drug mixture without reading the written instructions.
Effective communication between senior and junior employees is another way to reduce human error. People will make mistakes if they are treated badly. Managers must not punish employees for asking questions. Employees should feel at ease asking questions. If they don't feel comfortable asking questions they won't be inclined to take corrective action. Maintain a healthy dialog between junior and senior employees and resolve communication problems in a professional and courteous manner.
FAQ
How does a production planner differ from a project manager?
The difference between a product planner and project manager is that a planer is typically the one who organizes and plans the entire project. A production planner, however, is mostly involved in the planning stages.
What is the role of a logistics manager
Logistics managers ensure that goods arrive on time and are unharmed. This is done using his/her knowledge of the company's products. He/she should also ensure enough stock is available to meet demand.
What types of jobs can you find in logistics
There are many types of jobs in logistics. These are some of the jobs available in logistics:
-
Warehouse workers – They load, unload and transport pallets and trucks.
-
Transport drivers - These are people who drive trucks and trailers to transport goods or perform pick-ups.
-
Freight handlers, - They sort out and pack freight in warehouses.
-
Inventory managers – They manage the inventory in warehouses.
-
Sales reps - They sell products and services to customers.
-
Logistics coordinators - They plan and organize logistics operations.
-
Purchasing agents - They purchase goods and services needed for company operations.
-
Customer service agents - They answer phone calls and respond to emails.
-
Shippers clerks - They process shipping order and issue bills.
-
Order fillers are people who fill orders based only on what was ordered.
-
Quality control inspectors (QCI) - They inspect all incoming and departing products for potential defects.
-
Others – There are many other types available in logistics. They include transport supervisors, cargo specialists and others.
What are the four types in manufacturing?
Manufacturing refers to the transformation of raw materials into useful products by using machines and processes. Manufacturing can include many activities such as designing and building, testing, packaging shipping, selling, servicing, and other related activities.
Statistics
- In the United States, for example, manufacturing makes up 15% of the economic output. (twi-global.com)
- [54][55] These are the top 50 countries by the total value of manufacturing output in US dollars for its noted year according to World Bank.[56] (en.wikipedia.org)
- In 2021, an estimated 12.1 million Americans work in the manufacturing sector.6 (investopedia.com)
- (2:04) MTO is a production technique wherein products are customized according to customer specifications, and production only starts after an order is received. (oracle.com)
- Many factories witnessed a 30% increase in output due to the shift to electric motors. (en.wikipedia.org)
External Links
How To
Six Sigma: How to Use it in Manufacturing
Six Sigma refers to "the application and control of statistical processes (SPC) techniques in order to achieve continuous improvement." Motorola's Quality Improvement Department, Tokyo, Japan, developed it in 1986. Six Sigma's basic concept is to improve quality and eliminate defects through standardization. Many companies have adopted Six Sigma in recent years because they believe that there are no perfect products and services. The main goal of Six Sigma is to reduce variation from the mean value of production. You can calculate the percentage of deviation from the norm by taking a sample of your product and comparing it to the average. If there is a significant deviation from the norm, you will know that something needs to change.
Understanding the nature of variability in your business is the first step to Six Sigma. Once you understand that, it is time to identify the sources of variation. Also, you will need to identify the sources of variation. Random variations occur when people do mistakes. Symmetrical variations are caused due to factors beyond the process. You could consider random variations if some widgets fall off the assembly lines. But if you notice that every widget you make falls apart at the exact same place each time, this would indicate that there is a problem.
Once you identify the problem areas, it is time to create solutions. It might mean changing the way you do business or redesigning it entirely. After implementing the new changes, you should test them again to see if they worked. If they fail, you can go back to the drawing board to come up with a different plan.