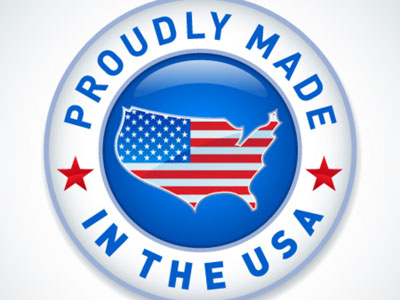
Additive manufacture is a technique for manufacturing which uses digital files. It creates parts, objects, and whole systems. It allows firms to produce complex machinery or other devices at relatively low cost. This process can also be used to reduce production costs and speed up the time to market. Casting, forging, and any other traditional production methods are not required.
In additive manufacturing, the benefits go far beyond suppliers, manufacturers, and communities. Customers who can afford innovative products also reap the benefits of additive manufacturing. Several Fortune 500 companies have adopted 3D printing technologies. Biden Administration announced a new initiative to support small- and medium-sized manufacturing firms in adopting additive manufacture.
AM Forward is a public-private initiative that aims to encourage the use of additive manufacturing by developing standards and common practices, establishing an open-market for additive-manufactured parts, and addressing supply chain issues. It is led by five large U.S. manufacturers: General Electric Aviation, Honeywell, Lockheed Martin, Raytheon, and Siemens Energy. These firms are partnering with the DOE Manufacturing Demonstration Facility at Oak Ridge National Laboratory, which is a national facility that provides access to a range of additive-manufacturing technologies.
OEMs will use the AM Forward agreement to find technical solutions to industry problems, collaborate with other firms and create standard specifications, as well as offer technical support to U.S.-based suppliers. The initiative is expected to be extended to other large companies in the coming years.
One of the major players involved in AM Forward is the NEO Additive Manufacturing Cluster of Ohio, which works to accelerate the adoption of additive-manufacturing technologies. Ohio has a solid base of skilled engineers and scientists making it an ideal place for additive manufacturing businesses.
The America Makes national accelerator is another important player. This program partners with academia, industry, economic development resources, and workforce training programs to encourage the adoption of additive-manufacturing by a wide range of sectors. Many university programs now exist for additive-manufacturing.
Other government programs are available to help with the adoption of additive production, such as the Manufacturing Extension Partnership. Programs offered by the Department of Labor to support small manufacturers include technical support, financing, and even financial assistance.
These programs often help overcome market failures. It is difficult for small businesses to access affordable financing and industry-standard technology because of a variety of obstacles. Similarly, some customers may not be willing to commit to purchasing from companies that invest in additive-manufacturing technologies.
Some of the most innovative additive-manufacturing firms in the country are located in Ohio. Desktop Metal is an industrial additive-manufacturing company that offers metal 3-D printing and machining services to manufacturers and designers. Jonco Industries, Inc. offers several fabrication services, which include rapid prototyping, prototyping design, and high-volume finishing. PostPro3D specializes in automated surface finishing.
Besides collaborating with the Federal Government, other industry organizations are working to increase the adoption of additive-manufacturing. The Fraunhofer Institute is a leading institution for the development of additive-manufacturing technology.
FAQ
How important is automation in manufacturing?
Automation is important not only for manufacturers but also for service providers. It enables them to provide services faster and more efficiently. It reduces human errors and improves productivity, which in turn helps them lower their costs.
Why is logistics important for manufacturing?
Logistics are an integral part any business. They help you achieve great results by helping you manage all aspects of product flow, from raw materials to finished goods.
Logistics play a key role in reducing expenses and increasing efficiency.
What is the difference between Production Planning, Scheduling and Production Planning?
Production Planning (PP), also known as forecasting and identifying production capacities, is the process that determines what product needs to be produced at any particular time. This is accomplished by forecasting the demand and identifying production resources.
Scheduling involves the assignment of dates and times to tasks in order to complete them within the timeframe.
How can manufacturing reduce production bottlenecks?
The key to avoiding bottlenecks in production is to keep all processes running smoothly throughout the entire production cycle, from the time you receive an order until the time when the product ships.
This includes planning to meet capacity requirements and quality control.
The best way to do this is to use continuous improvement techniques such as Six Sigma.
Six Sigma is a management system used to improve quality and reduce waste in every aspect of your organization.
It emphasizes consistency and eliminating variance in your work.
What does it take for a logistics enterprise to succeed?
To be a successful businessman in logistics, you will need many skills and knowledge. Good communication skills are essential to effectively communicate with your suppliers and clients. You will need to know how to interpret data and draw conclusions. You will need to be able handle pressure well and work in stressful situations. To improve efficiency, you must be innovative and creative. Strong leadership qualities are essential to motivate your team and help them achieve their organizational goals.
It is important to be organized and efficient in order to meet tight deadlines.
Statistics
- According to the United Nations Industrial Development Organization (UNIDO), China is the top manufacturer worldwide by 2019 output, producing 28.7% of the total global manufacturing output, followed by the United States, Japan, Germany, and India.[52][53] (en.wikipedia.org)
- You can multiply the result by 100 to get the total percent of monthly overhead. (investopedia.com)
- (2:04) MTO is a production technique wherein products are customized according to customer specifications, and production only starts after an order is received. (oracle.com)
- Many factories witnessed a 30% increase in output due to the shift to electric motors. (en.wikipedia.org)
- In the United States, for example, manufacturing makes up 15% of the economic output. (twi-global.com)
External Links
How To
How to Use Lean Manufacturing for the Production of Goods
Lean manufacturing is a management style that aims to increase efficiency and reduce waste through continuous improvement. It was developed by Taiichi Okono in Japan, during the 1970s & 1980s. TPS founder Kanji Takoda awarded him the Toyota Production System Award (TPS). Michael L. Watkins published the original book on lean manufacturing, "The Machine That Changed the World," in 1990.
Lean manufacturing is often defined as a set of principles used to improve the quality, speed, and cost of products and services. It emphasizes the elimination and minimization of waste in the value stream. Lean manufacturing is called just-in-time (JIT), zero defect, total productive maintenance (TPM), or 5S. Lean manufacturing focuses on eliminating non-value-added activities such as rework, inspection, and waiting.
In addition to improving product quality and reducing costs, lean manufacturing helps companies achieve their goals faster and reduces employee turnover. Lean Manufacturing is one of the most efficient ways to manage the entire value chains, including suppliers and customers as well distributors and retailers. Lean manufacturing is widely practiced in many industries around the world. Toyota's philosophy has been a key driver of success in many industries, including automobiles and electronics.
Lean manufacturing includes five basic principles:
-
Define Value - Determine the value that your business brings to society. Also, identify what sets you apart from your competitors.
-
Reduce Waste - Eliminate any activity that doesn't add value along the supply chain.
-
Create Flow - Ensure work moves smoothly through the process without interruption.
-
Standardize and Simplify – Make processes as consistent, repeatable, and as simple as possible.
-
Develop Relationships: Establish personal relationships both with internal and external stakeholders.
Although lean manufacturing has always been around, it is gaining popularity in recent years because of a renewed interest for the economy after 2008's global financial crisis. Many businesses have adopted lean production techniques to make them more competitive. Many economists believe lean manufacturing will play a major role in economic recovery.
Lean manufacturing, which has many benefits, is now a standard practice in the automotive industry. These include higher customer satisfaction levels, reduced inventory levels as well as lower operating costs.
Lean manufacturing can be applied to almost every aspect of an organization. It is especially useful for the production aspect of an organization, as it ensures that every step in the value chain is efficient and effective.
There are three types principally of lean manufacturing:
-
Just-in Time Manufacturing: This lean manufacturing method is commonly called "pull systems." JIT is a process in which components can be assembled at the point they are needed, instead of being made ahead of time. This strategy aims to decrease lead times, increase availability of parts and reduce inventory.
-
Zero Defects Manufacturing: ZDM ensures that no defective units leave the manufacturing plant. It is better to repair a part than have it removed from the production line if it needs to be fixed. This applies to finished goods that may require minor repairs before shipment.
-
Continuous Improvement: Continuous Improvement aims to improve efficiency by continually identifying problems and making adjustments to eliminate or minimize waste. Continuous improvement involves continuous improvement of processes and people as well as tools.