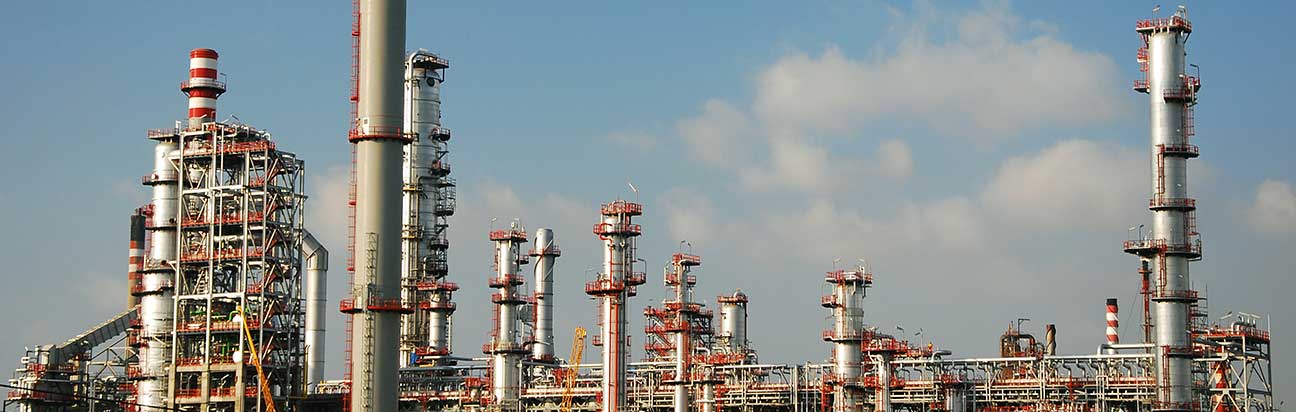
Considering the many articles published on supply chain management, the question is, what are the most cited? Given the amount of academic research on this topic, it is hard to answer. You can narrow down your field by using cocitation analysis. With the help of the Supply Chain Management Association's cocitation database, we were able to find the most-cited supply chain articles. The International Journal of Supply Chain Management has the highest number of citations at 25,476. The citations are organized into five categories based on their most cited article. The order of the citations is not very predictable, since the International Journal of Supply Chain Management has a much higher citation count than most other journals.
Amazon's supply-chain practices review is the most frequently cited article. This review links buyers and sellers. The objective of this review is to discover what works, and what doesn’t. The article discusses Amazon's many pitfalls, as well as the opportunities it offers. It also suggests several actionable ways to remedy these shortcomings.
Cross-sectional research on supply chain risks, and the performance that results is the most widely cited article. The study uses regression and panel data to test the effects of supply risks on performance, which is no small feat. The results are impressive. In particular, the study finds that supply chain risk management is the best way to improve performance in the long term. This finding has implications for all areas of corporate business life, including customer service and procurement.
The most cited article is not the only notable feat of the same caliber. Given the sheer number of publications available in the Supply Chain Management Association Database, it's no surprise that the most cited articles are in the same journal. The International Journal of Supply Chain Management (the flagship journal of Supply Chain Management Association) has the highest number of citations with 25,476. This is more than double the tally of the Supply Chain Management Association's sister journal, the International Journal of Logistics Research and Applications.
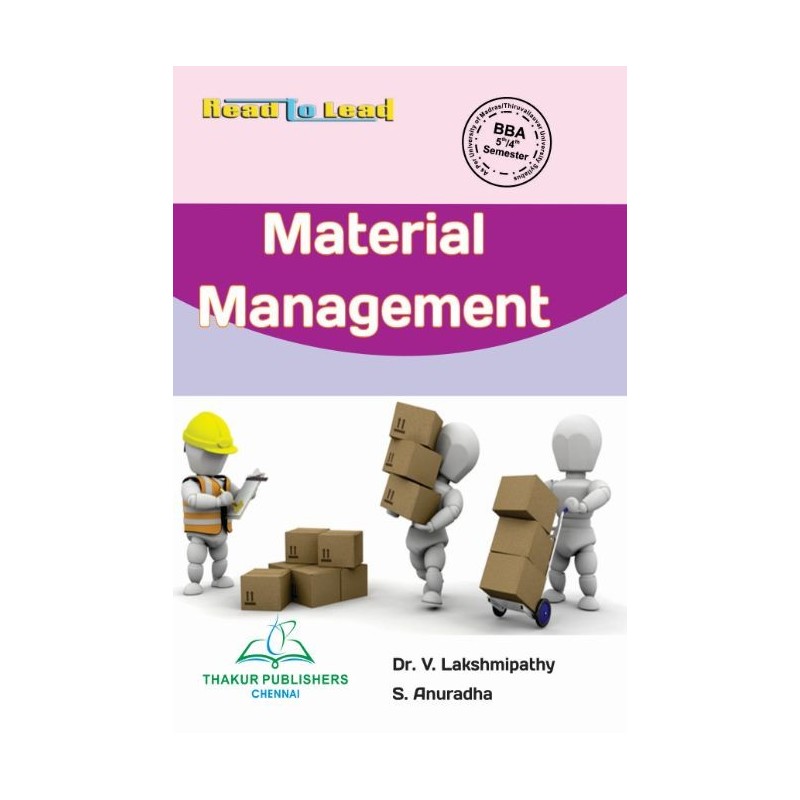
FAQ
What are manufacturing & logistics?
Manufacturing refers the process of producing goods from raw materials through machines and processes. Logistics encompasses the management of all aspects associated with supply chain activities such as procurement, production planning, distribution and inventory control. It also includes customer service. Logistics and manufacturing are often referred to as one thing. It encompasses both the creation of products and their delivery to customers.
What kind of jobs are there in logistics?
There are different kinds of jobs available in logistics. These are some of the jobs available in logistics:
-
Warehouse workers – They load, unload and transport pallets and trucks.
-
Transportation drivers: They drive trucks and trailers and deliver goods and make pick-ups.
-
Freight handlers are people who sort and pack freight into warehouses.
-
Inventory managers: They are responsible for the inventory and management of warehouses.
-
Sales representatives: They sell products to customers.
-
Logistics coordinators are responsible for organizing and planning logistics operations.
-
Purchasing agents - They buy goods and services that are necessary for company operations.
-
Customer service representatives are available to answer customer calls and emails.
-
Ship clerks - They issue bills and process shipping orders.
-
Order fillers are people who fill orders based only on what was ordered.
-
Quality control inspectors: They inspect outgoing and incoming products for any defects.
-
Others – There are many other types available in logistics. They include transport supervisors, cargo specialists and others.
How can manufacturing efficiency be improved?
First, identify the factors that affect production time. We then need to figure out how to improve these variables. If you don't know where to start, then think about which factor(s) have the biggest impact on production time. Once you have identified the factors, then try to find solutions.
What is it like to manage a logistics company?
To run a successful logistics company, you need a lot knowledge and skills. For clients and suppliers to be successful, you need to have excellent communication skills. You need to understand how to analyze data and draw conclusions from it. You need to be able work under pressure and manage stressful situations. In order to innovate and create new ways to improve efficiency, creativity is essential. Strong leadership qualities are essential to motivate your team and help them achieve their organizational goals.
It is also important to be efficient and well organized in order meet deadlines.
What are the products of logistics?
Logistics involves the transportation of goods from point A and point B.
They include all aspects associated with transport including packaging, loading transporting, unloading storage, warehousing inventory management customer service, distribution returns and recycling.
Logisticians ensure that the right product reaches the right place at the right time and under safe conditions. They assist companies with their supply chain efficiency through information on demand forecasts. Stock levels, production times, and availability.
They also keep track of shipments in transit, monitor quality standards, perform inventories and order replenishment, coordinate with suppliers and vendors, and provide support services for sales and marketing.
Statistics
- Job #1 is delivering the ordered product according to specifications: color, size, brand, and quantity. (netsuite.com)
- In the United States, for example, manufacturing makes up 15% of the economic output. (twi-global.com)
- (2:04) MTO is a production technique wherein products are customized according to customer specifications, and production only starts after an order is received. (oracle.com)
- According to the United Nations Industrial Development Organization (UNIDO), China is the top manufacturer worldwide by 2019 output, producing 28.7% of the total global manufacturing output, followed by the United States, Japan, Germany, and India.[52][53] (en.wikipedia.org)
- It's estimated that 10.8% of the U.S. GDP in 2020 was contributed to manufacturing. (investopedia.com)
External Links
How To
How to use 5S in Manufacturing to Increase Productivity
5S stands in for "Sort", the "Set In Order", "Standardize", or "Separate". The 5S methodology was developed at Toyota Motor Corporation in 1954. It assists companies in improving their work environments and achieving higher efficiency.
This method aims to standardize production processes so that they are repeatable, measurable and predictable. This means that every day tasks such cleaning, sorting/storing, packing, and labeling can be performed. Workers can be more productive by knowing what to expect.
Five steps are required to implement 5S: Sort, Set In Order, Standardize. Separate. Each step requires a different action, which increases efficiency. Sorting things makes it easier to find them later. When you arrange items, you place them together. After you have divided your inventory into groups you can store them in easy-to-reach containers. Labeling your containers will ensure that everything is correctly labeled.
Employees must be able to critically examine their work practices. Employees need to be able understand their motivations and discover alternative ways to do them. To be successful in the 5S system, employees will need to acquire new skills and techniques.
The 5S method not only increases efficiency but also boosts morale and teamwork. As they begin to see improvements, they feel motivated to continue working towards the goal of achieving higher levels of efficiency.