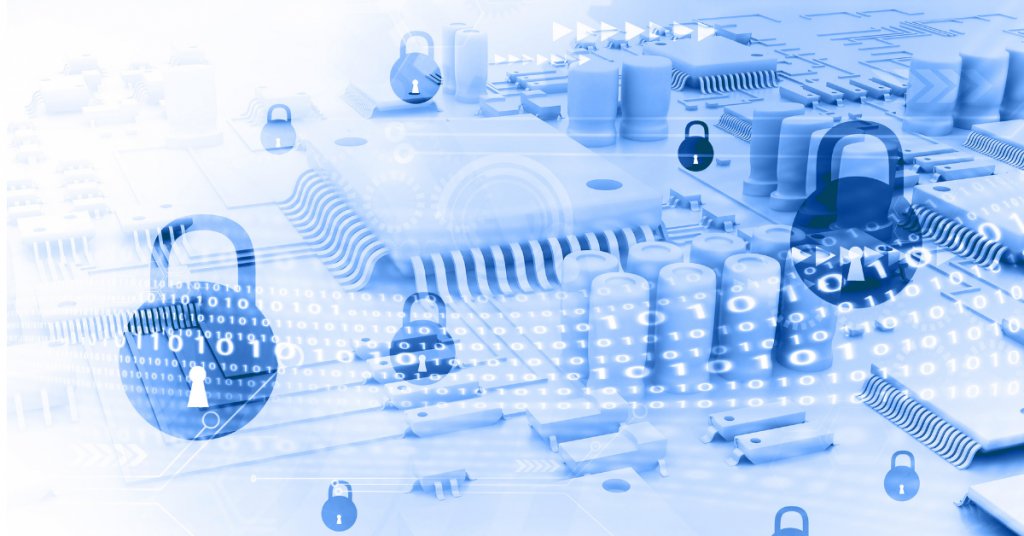
Today, apparel manufacturers face an unprecedented challenge to meet the demands of a diverse consumer base. These consumers differ in terms of physiographics as well as socioeconomics. They also have diverse preferences, which can be difficult to predict. Additionally, consumer awareness of different products is increasing, and they can access information readily. Consumers are more inclined to spend on high-fashion and expensive products.
Production efficiency
A key component of the overall strategy for apparel producers is to increase production efficiency. Because the apparel industry is dependent on human labor and changing fashion trends it is critical to ensure that production planning is in place. As a result, apparel manufacturers must ensure they can adapt to global requirements and meet a short product development cycle. In addition to planning for new products, apparel manufacturers should evaluate the efficiency of their existing lines and implement digital technologies, which can reduce the product development cycle from months to days. The planning process should include critical path analysis.
Increasing production efficiency is possible despite the labor-intensive nature of apparel manufacturing. However, achieving this goal requires a combination of the right tools and proper management. For example, an increase of just 10 to 15% in efficiency can lead to a 3-5% increase in EBITDA. Additionally, efficiency can help increase workers' wages and increase the country’s competitiveness on global markets.
Fabric layering
Fabric layering can be used in apparel production. It involves placing a pre-made pattern on top of a lay. You can either use a plotter or hand to create the pattern. The pattern components are placed in the markers. These are then cut using a straight or other method.
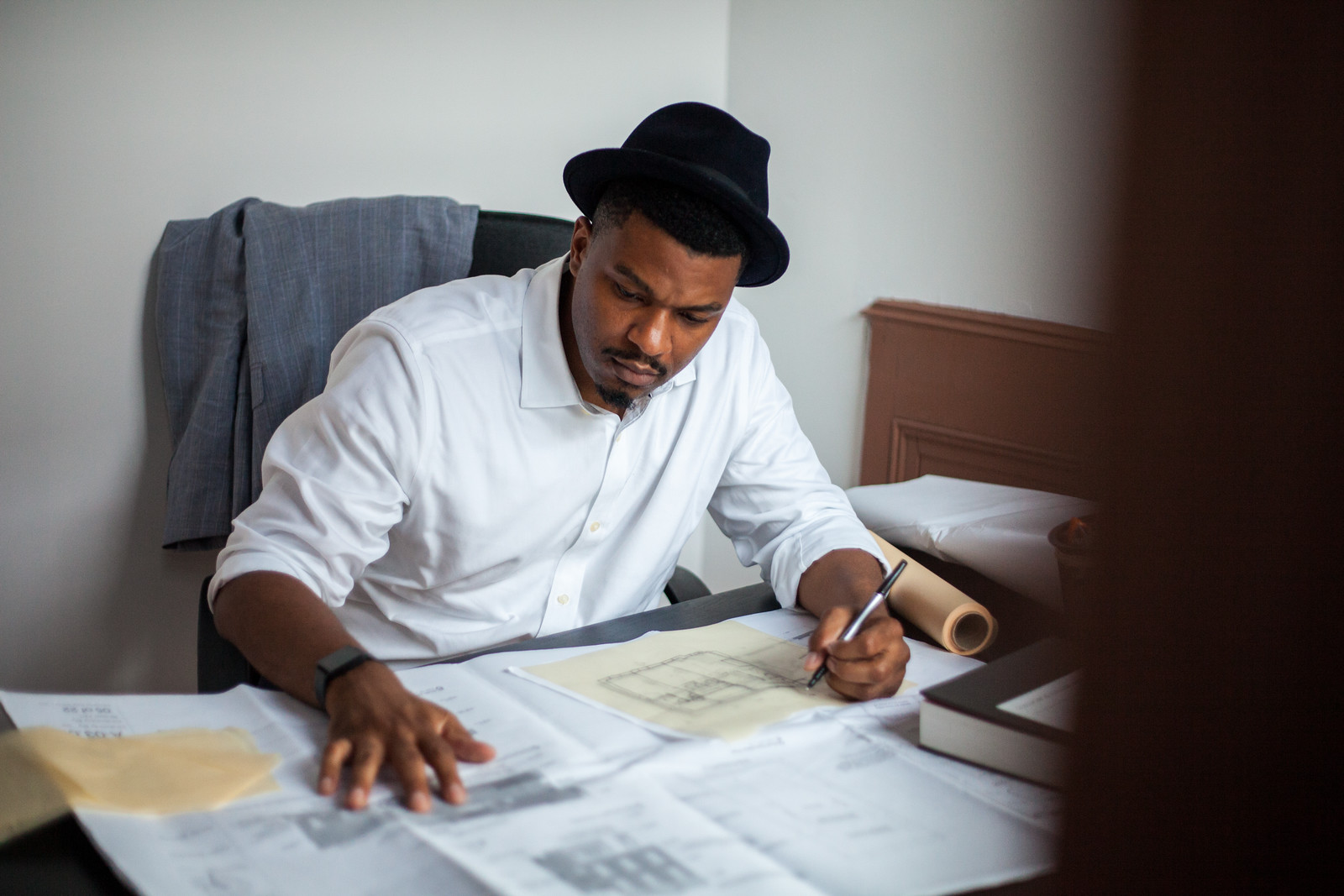
The fabric will be spread out evenly during this step. It can be laid out in a pile or laid out in superimposed layers with the cutting marker on top. The maximum fabric width, less the selvedge or needle marks, is the usable width. Fabric utilization is the area of fabric used. The layouts can be either half-garment or whole-garment. Half-garment laid fabric is placed on one side while whole-garment laid fabric covers both sides. Whole garment lay has the disadvantage that it uses more fabric.
Cutting
Cutting involves using cutting blades that cut a particular piece of fabric into smaller pieces. Fabric can cost between 60 and 70 percent of a garment's price. It is crucial that every inch be used. Apparel manufacturing should have a strict control system to ensure that every inch is used.
Spreading fabric onto a large surface is the first step to cutting fabric. Usually, in mass production, a number of layers is used to spread the fabric. The cutting master determines how many layers should be spread on a specific garment, based on the number of garments to be made and the thickness of the fabric. After the fabric is spread, it must be measured and a maximum width of cutting is determined.
Pressing
The process of pressing is crucial in the production of apparel. It improves the appearance and comfort of garments. This is done in a factory. You can either automate or manually operate a press. Software can be used for controlling the automation level. Software can also program a press to follow a set of instructions. The possibility of human error can be reduced by automating the pressing process in an apparel manufacturing plant. The increasing number of fibers and fabric varieties will require more precise control of temperature and pressure during the process.
The process of pressing involves heating the fibers of the garment. The shape of the garment is stabilized with the softened fibres. It is important to choose the correct temperature in order not to damage the yarns and fibres.
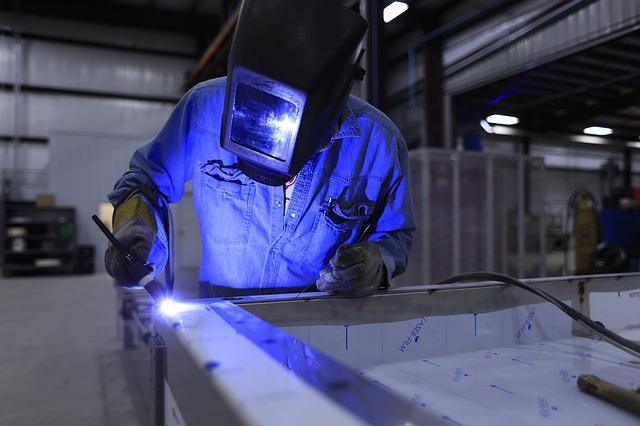
Minimum order quantity
It is essential to know the Minimum Order Quantity (or MOQ), of each clothing manufacturer when searching for one. Many garment factories will not produce your garments without a minimum order amount. The MOQ will vary from one factory to the next depending on your technical specifications. Some factories are able to accept orders up to 100 items. Others require orders over a thousand.
Most manufacturers need to have a minimum order quantity (MOQ), especially if they deal in bulk products. This quantity allows them to stay profitable and helps to weed out businesses that only want small orders but don't need large quantities. This is especially important for custom orders.
FAQ
What does it mean to warehouse?
A warehouse, or storage facility, is where goods are stored prior to being sold. It can be an outdoor or indoor area. Sometimes, it can be both an indoor and outdoor space.
How can manufacturing prevent production bottlenecks?
The key to avoiding bottlenecks in production is to keep all processes running smoothly throughout the entire production cycle, from the time you receive an order until the time when the product ships.
This includes planning for capacity requirements as well as quality control measures.
The best way to do this is to use continuous improvement techniques such as Six Sigma.
Six Sigma management is a system that improves quality and reduces waste within your organization.
It's all about eliminating variation and creating consistency in work.
Why automate your factory?
Modern warehouses are increasingly dependent on automation. With the rise of ecommerce, there is a greater demand for faster delivery times as well as more efficient processes.
Warehouses must adapt quickly to meet changing customer needs. They must invest heavily in technology to do this. Automation warehouses can bring many benefits. These are just a few reasons to invest in automation.
-
Increases throughput/productivity
-
Reduces errors
-
Increases accuracy
-
Safety is boosted
-
Eliminates bottlenecks
-
Companies can scale more easily
-
This makes workers more productive
-
It gives visibility to everything that happens inside the warehouse
-
Enhances customer experience
-
Improves employee satisfaction
-
Minimizes downtime and increases uptime
-
Quality products delivered on time
-
Eliminates human error
-
Helps ensure compliance with regulations
Statistics
- Job #1 is delivering the ordered product according to specifications: color, size, brand, and quantity. (netsuite.com)
- In the United States, for example, manufacturing makes up 15% of the economic output. (twi-global.com)
- According to the United Nations Industrial Development Organization (UNIDO), China is the top manufacturer worldwide by 2019 output, producing 28.7% of the total global manufacturing output, followed by the United States, Japan, Germany, and India.[52][53] (en.wikipedia.org)
- Many factories witnessed a 30% increase in output due to the shift to electric motors. (en.wikipedia.org)
- In 2021, an estimated 12.1 million Americans work in the manufacturing sector.6 (investopedia.com)
External Links
How To
How to Use the Just In Time Method in Production
Just-in-time is a way to cut costs and increase efficiency in business processes. It allows you to get the right amount resources at the right time. This means that you only pay for what you actually use. Frederick Taylor was the first to coin this term. He developed it while working as a foreman during the early 1900s. He observed how workers were paid overtime if there were delays in their work. He concluded that if workers were given enough time before they start work, productivity would increase.
JIT is an acronym that means you need to plan ahead so you don’t waste your money. You should also look at the entire project from start to finish and make sure that you have sufficient resources available to deal with any problems that arise during the course of your project. You will have the resources and people to solve any problems you anticipate. This way, you won't end up paying extra money for things that weren't really necessary.
There are several types of JIT techniques:
-
Demand-driven JIT: You order the parts and materials you need for your project every other day. This will let you track the amount of material left over after you've used it. It will also allow you to predict how long it takes to produce more.
-
Inventory-based : You can stock the materials you need in advance. This allows for you to anticipate how much you can sell.
-
Project-driven: This approach involves setting aside sufficient funds to cover your project's costs. You will be able to purchase the right amount of materials if you know what you need.
-
Resource-based JIT: This is the most popular form of JIT. Here you can allocate certain resources based purely on demand. If you have many orders, you will assign more people to manage them. You'll have fewer orders if you have fewer.
-
Cost-based: This is similar to resource-based, except that here you're not just concerned about how many people you have but how much each person costs.
-
Price-based: This approach is very similar to the cost-based method except that you don't look at individual workers costs but the total cost of the company.
-
Material-based: This is quite similar to cost-based, but instead of looking at the total cost of the company, you're concerned with how much raw materials you spend on average.
-
Time-based: Another variation of resource-based JIT. Instead of worrying about how much each worker costs, you can focus on how long the project takes.
-
Quality-based JIT - This is another form of resource-based JIT. Instead of worrying about the costs of each employee or how long it takes for something to be made, you should think about how quality your product is.
-
Value-based: This is one of the newest forms of JIT. This is where you don't care about how the products perform or whether they meet customers' expectations. Instead, your goal is to add value to the market.
-
Stock-based. This method is inventory-based and focuses only on the actual production at any given point. This is used to increase production and minimize inventory.
-
Just-in time (JIT), planning: This is a combination JIT/supply chain management. It refers to the process of scheduling the delivery of components as soon as they are ordered. It reduces lead times and improves throughput.