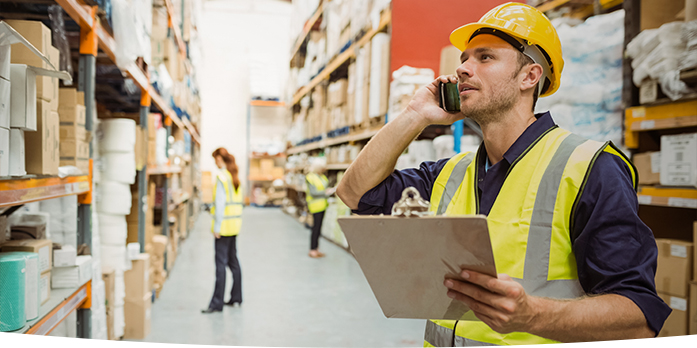
Many machines are used by Machinists. These machines make repairs on metal products such as a car. They can also create precision metal parts or new alloys. Machine operators are frequently exposed to toxic chemicals. A good machinist has excellent communication skills and is detail-oriented.
Machinists typically work full-time or part-time. Many of them begin working right out of high school. Some machinists take an apprenticeship before they move on to a fulltime position. Others may pursue associate degrees. Many machinists choose to earn a degree in engineering (CAD) or computer-aided development (Eng.
Machine operators often work in factories and specialty shops. These positions can be noisy and exposed to dangerous materials, but they provide excellent opportunities for problem-solving. A machinist can use either manual or automatically. For those with more experience, it is possible to rise up to managerial and supervisory roles. The need for machinists is increasing as baby boomers retire. Machine shops are retooling for automation also increases job security.
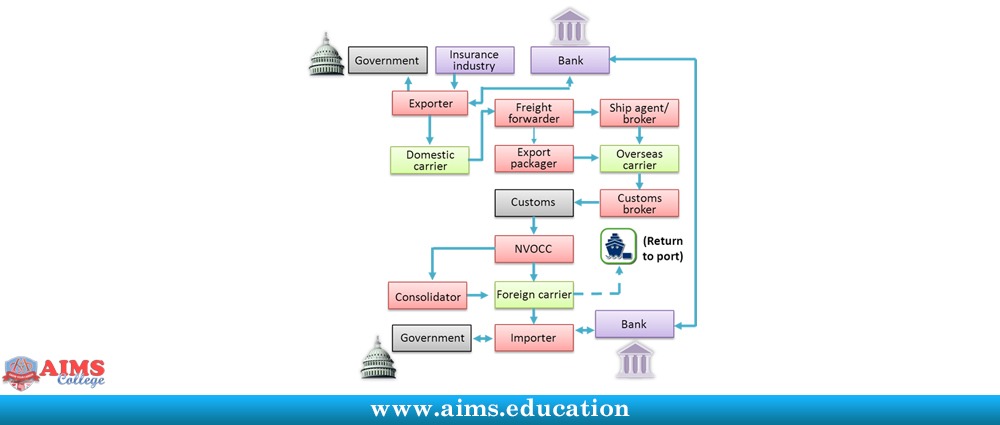
Depending upon the employer, machinists are often assigned specific duties. These include setting up machines and maintaining them. You can also work with assembly lines. These machines are operated by humans and robots. Other responsibilities include programming and monitoring machines, as well as interpreting blueprints.
Machinists can work with many materials such as steel and aluminum, as well brass, copper and other metals. Machine machinists are most often required to work on metal parts.
A high school diploma is the norm for machinists, but some employers may require an associate's or higher degree. The training program can last for up to four years if you are interested. You may also have the opportunity to learn from a mentor in your work environment. Ask your mentor for information about apprenticeships or other training opportunities.
No matter what company they work for, machinists have to collaborate with others. They can either work as part of a larger team or individually, but they must always follow safety procedures. It includes proper safety equipment such earplugs. Machinists are often exposed to chemicals and fumes. Machinists aren't always under constant pressure.
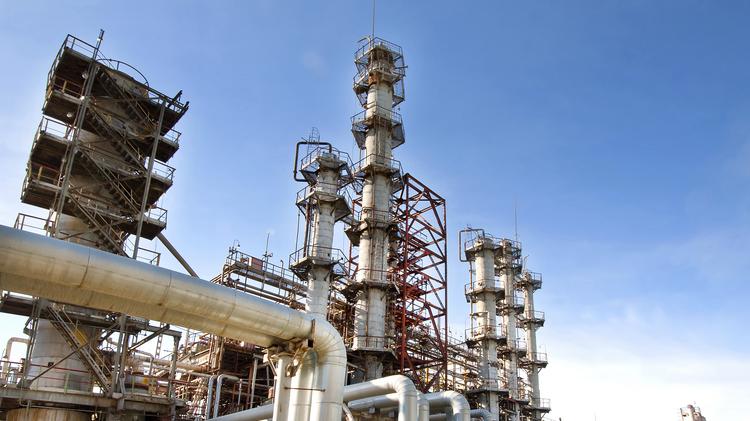
Besides on-the-job training, machinists can enroll in college courses or join trade unions. Machinists with union membership enjoy better benefits and greater job security. Many union members have health insurance and retirement plans. Numerous colleges offer two year machining associates programs.
You can climb up the corporate ladder with a degree as a machinist. As demand for auto parts grows, machinists are more in-demand. Between 2020-2030, there will be a 7% increase in employment. With the increasing use artificial intelligence and retooling to automate, machinists are expected to be in high demand over these next two decades.
FAQ
What skills are required to be a production manager?
Production planners must be flexible, organized, and able handle multiple tasks. Communication skills are essential to ensure that you can communicate effectively with clients, colleagues, and customers.
What are the 7 Rs of logistics?
The acronym 7R's of Logistic is an acronym that stands for seven fundamental principles of logistics management. It was developed and published by the International Association of Business Logisticians in 2004 as part of the "Seven Principles of Logistics Management".
The acronym is composed of the following letters.
-
Responsible - ensure that all actions taken are within legal requirements and are not harmful to others.
-
Reliable - have confidence in the ability to deliver on commitments made.
-
It is reasonable to use resources efficiently and not waste them.
-
Realistic – Consider all aspects, including cost-effectiveness as well as environmental impact.
-
Respectful - Treat people fairly and equitably
-
Resourceful - look for opportunities to save money and increase productivity.
-
Recognizable is a company that provides customers with value-added solutions.
Why should you automate your warehouse?
Automation has become increasingly important in modern warehousing. E-commerce has increased the demand for quicker delivery times and more efficient processes.
Warehouses have to be flexible to meet changing requirements. They must invest heavily in technology to do this. Automating warehouses is a great way to save money. Here are some of the reasons automation is worth your investment:
-
Increases throughput/productivity
-
Reduces errors
-
Improves accuracy
-
Boosts safety
-
Eliminates bottlenecks
-
Allows companies to scale more easily
-
Increases efficiency of workers
-
It gives visibility to everything that happens inside the warehouse
-
Enhances customer experience
-
Improves employee satisfaction
-
Minimizes downtime and increases uptime
-
Quality products delivered on time
-
Removing human error
-
This helps to ensure compliance with regulations
How important is automation in manufacturing?
Not only is automation important for manufacturers, but it's also vital for service providers. They can provide services more quickly and efficiently thanks to automation. In addition, it helps them reduce costs by reducing human errors and improving productivity.
What does warehouse refer to?
A warehouse is a place where goods are stored until they are sold. It can be either an indoor or outdoor space. It may also be an indoor space or an outdoor area.
What are the responsibilities of a logistic manager?
A logistics manager makes sure that all goods are delivered on-time and in good condition. This is done using his/her knowledge of the company's products. He/she must also ensure sufficient stock to meet the demand.
Statistics
- According to a Statista study, U.S. businesses spent $1.63 trillion on logistics in 2019, moving goods from origin to end user through various supply chain network segments. (netsuite.com)
- Job #1 is delivering the ordered product according to specifications: color, size, brand, and quantity. (netsuite.com)
- (2:04) MTO is a production technique wherein products are customized according to customer specifications, and production only starts after an order is received. (oracle.com)
- You can multiply the result by 100 to get the total percent of monthly overhead. (investopedia.com)
- Many factories witnessed a 30% increase in output due to the shift to electric motors. (en.wikipedia.org)
External Links
How To
How to Use the Just-In-Time Method in Production
Just-in time (JIT), is a process that reduces costs and increases efficiency in business operations. It's a way to ensure that you get the right resources at just the right time. This means that only what you use is charged to your account. Frederick Taylor, a 1900s foreman, first coined the term. He observed how workers were paid overtime if there were delays in their work. He realized that workers should have enough time to complete their jobs before they begin work. This would help increase productivity.
JIT is a way to plan ahead and make sure you don't waste any money. The entire project should be looked at from start to finish. You need to ensure you have enough resources to tackle any issues that might arise. If you expect problems to arise, you will be able to provide the necessary equipment and personnel to address them. This will prevent you from spending extra money on unnecessary things.
There are several types of JIT techniques:
-
Demand-driven JIT: This is a JIT that allows you to regularly order the parts/materials necessary for your project. This will allow for you to track the material that you have left after using it. This will allow you to calculate how long it will take to make more.
-
Inventory-based : You can stock the materials you need in advance. This allows you predict the amount you can expect to sell.
-
Project-driven : This is a method where you make sure that enough money is set aside to pay the project's cost. Once you have an idea of how much material you will need, you can purchase the necessary materials.
-
Resource-based JIT is the most widespread form. This is where you assign resources based upon demand. If you have many orders, you will assign more people to manage them. If you don't receive many orders, then you'll assign fewer employees to handle the load.
-
Cost-based: This is the same as resource-based except that you don't care how many people there are but how much each one of them costs.
-
Price-based: This approach is very similar to the cost-based method except that you don't look at individual workers costs but the total cost of the company.
-
Material-based: This is quite similar to cost-based, but instead of looking at the total cost of the company, you're concerned with how much raw materials you spend on average.
-
Time-based JIT: This is another variant of resource-based JIT. Instead of worrying about how much each worker costs, you can focus on how long the project takes.
-
Quality-based JIT: Another variation on resource-based JIT. Instead of thinking about the cost of each employee or the time it takes to produce something, you focus on how good your product quality.
-
Value-based JIT is the newest form of JIT. In this instance, you are not concerned about the product's performance or meeting customer expectations. Instead, you are focused on adding value to the marketplace.
-
Stock-based: This stock-based method focuses on the actual quantity of products being made at any given time. This method is useful when you want to increase production while decreasing inventory.
-
Just-in time (JIT), planning: This is a combination JIT/supply chain management. It's the process of scheduling delivery of components immediately after they are ordered. It reduces lead times and improves throughput.