
There are thousands of Connecticut manufacturing jobs waiting to be filled. There are 411 manufacturers in Connecticut that employ 159,000 people. Manufacturing contributes the most to the state's gross state product and pays a better-than-average salary. Recent surveys by the Connecticut Business and Industry Association revealed that there are a lot of needs in the manufacturing sector. The survey found that 13,000 jobs in manufacturing are vacant in Connecticut, and many companies struggle to find younger workers.
Connecticut's manufacturing workforce is older. A third of those workers are over 55. Many companies moved their manufacturing facilities to reduce labor costs. In turn, other operations adopted new machinery and automation. Although manufacturing used to be considered hazardous and dirty in the past it has gained a better reputation. Companies offer entry-level positions, internships, apprenticeships. Manufacturing is Connecticut’s third largest employment sector. Its high tech operations are a key competitive advantage.
Connecticut has many public and private education programs that are designed to prepare people for manufacturing jobs. The Manufacturing Innovation Fund is a program that supports high schools, universities, vocational high schools, and comprehensive high schools. It also supports online training, pre-apprenticeships, career activities, and career activities, for K-12 students.
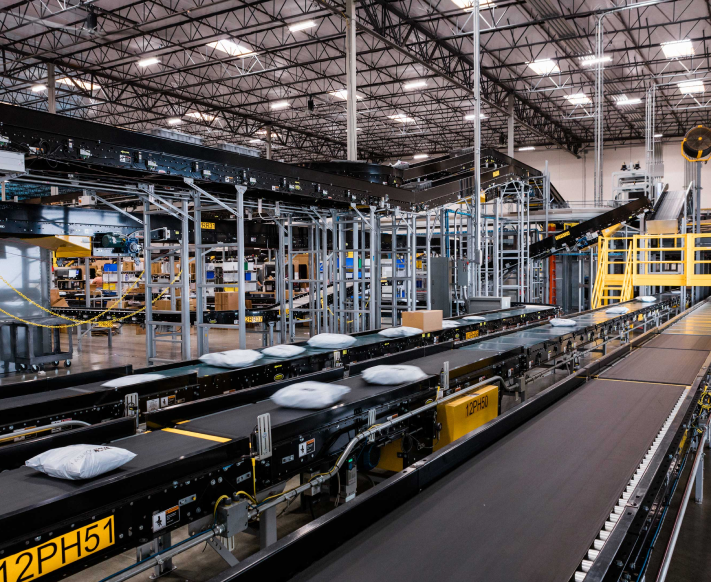
A wide range of backgrounds are available for advanced manufacturing workers. Some people start in the manufacturing field right out of high school. Other workers have been working for many years in another industry before switching to it. They might have completed a degree at school, or may have joined the workforce after serving in the military. Many companies will pay tuition for advanced manufacturing programs. Other programs provide wage subsidies for entry-level training.
Technical education options have been reintroduced at the state's Comprehensive High School. One example of this is the Grasso Tech welder program which will start in fall 2019. Employers that recruit through the EB would be interested in hiring students from Connecticut. The Eastern Connecticut Manufacturing Pipeline supports the region's advanced manufacturing businesses. It was inspired by the Eastern Connecticut Workforce Investment Board's Manufacturing Pipeline.
The Manufacturing Careers Program is designed to help job seekers who are interested in manufacturing careers demonstrate their readiness for entry level work. This program matches pre-screened job candidates with employers and manufacturers. The program offers a CNC Basics training course as well as a career path that is industry-focused. The Advanced Manufacturing Employer Partnership provides wage subsidies and entry-level training to those who are enrolled in this program.
The manufacturing industry may be unfamiliar to young workers entering the workforce. This lack of awareness may make it difficult for them to participate in these education programs. These programs are funded by the state with millions of dollars. These programs are not accessible to young people because they don't know about the existence of these jobs.
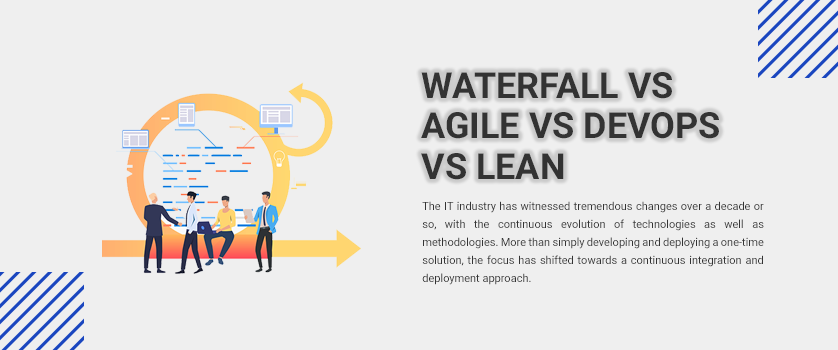
A statewide STEM Town initiative is one innovative way to address Connecticut's shortage of manufacturing jobs. This would require reallocating resources and improving education programs in order to meet the needs for manufacturers.
FAQ
What makes a production planner different from a project manger?
The major difference between a Production Planner and a Project Manager is that a Project Manager is often the person responsible for organizing and planning the entire project. While a Production Planner is involved mainly in the planning stage,
What is the job of a production plan?
A production planner makes sure all project elements are delivered on schedule, within budget, as well as within the agreed scope. They ensure that the product or service is of high quality and meets client requirements.
How can overproduction in manufacturing be reduced?
Improved inventory management is the key to reducing overproduction. This would reduce the amount of time spent on unnecessary activities such as purchasing, storing, and maintaining excess stock. This will allow us to free up resources for more productive tasks.
One way to do this is to adopt a Kanban system. A Kanban board, a visual display to show the progress of work, is called a Kanban board. In a Kanban system, work items move through a sequence of states until they reach their final destination. Each state is assigned a different priority.
When work is completed, it can be transferred to the next stage. It is possible to keep a task in the beginning stages until it gets to the end.
This helps to keep work moving forward while ensuring that no work is left behind. Managers can view the Kanban board to see how much work they have done. This information allows them to adjust their workflow based on real-time data.
Lean manufacturing, another method to control inventory levels, is also an option. Lean manufacturing seeks to eliminate waste from every step of the production cycle. Anything that doesn't add value to the product is considered waste. There are several types of waste that you might encounter:
-
Overproduction
-
Inventory
-
Unnecessary packaging
-
Exceed materials
Manufacturers can increase efficiency and decrease costs by implementing these ideas.
Can we automate some parts of manufacturing?
Yes! Automation has been around since ancient times. The Egyptians invent the wheel thousands of year ago. Robots are now used to assist us in assembly lines.
In fact, there are several applications of robotics in manufacturing today. These include:
-
Line robots
-
Robot welding
-
Robot painting
-
Robotics inspection
-
Robots that produce products
Automation can be applied to manufacturing in many other ways. 3D printing, for example, allows us to create custom products without waiting for them to be made.
What are the requirements to start a logistics business?
A successful logistics business requires a lot more than just knowledge. Good communication skills are essential to effectively communicate with your suppliers and clients. You will need to know how to interpret data and draw conclusions. You need to be able work under pressure and manage stressful situations. You need to be innovative and creative to come up with new ways to increase efficiency. You will need strong leadership skills to motivate and direct your team members towards achieving their organizational goals.
It is also important to be efficient and well organized in order meet deadlines.
What does the term manufacturing industries mean?
Manufacturing Industries are those businesses that make products for sale. Consumers are those who purchase these products. To accomplish this goal, these companies employ a range of processes including distribution, sales, management, and production. These companies produce goods using raw materials and other equipment. This includes all types and varieties of manufactured goods, such as food items, clothings, building supplies, furnitures, toys, electronics tools, machinery vehicles, pharmaceuticals medical devices, chemicals, among others.
Statistics
- According to a Statista study, U.S. businesses spent $1.63 trillion on logistics in 2019, moving goods from origin to end user through various supply chain network segments. (netsuite.com)
- You can multiply the result by 100 to get the total percent of monthly overhead. (investopedia.com)
- It's estimated that 10.8% of the U.S. GDP in 2020 was contributed to manufacturing. (investopedia.com)
- Many factories witnessed a 30% increase in output due to the shift to electric motors. (en.wikipedia.org)
- In the United States, for example, manufacturing makes up 15% of the economic output. (twi-global.com)
External Links
How To
How to use 5S in Manufacturing to Increase Productivity
5S stands to stand for "Sort", “Set In Order", “Standardize", and "Store". Toyota Motor Corporation developed the 5S method in 1954. This methodology helps companies improve their work environment to increase efficiency.
The idea behind standardizing production processes is to make them repeatable and measurable. This means that tasks such as cleaning, sorting, storing, packing, and labeling are performed daily. This knowledge allows workers to be more efficient in their work because they are aware of what to expect.
Implementing 5S involves five steps: Sort, Set in Order, Standardize Separate, Store, and Each step requires a different action, which increases efficiency. For example, when you sort things, you make them easy to find later. When you set items in an order, you put items together. After you have divided your inventory into groups you can store them in easy-to-reach containers. You can also label your containers to ensure everything is properly labeled.
Employees will need to be more critical about their work. Employees must be able to see why they do what they do and find a way to achieve them without having to rely on their old methods. They will need to develop new skills and techniques in order for the 5S system to be implemented.
In addition to increasing efficiency, the 5S method also improves morale and teamwork among employees. Once they start to notice improvements, they are motivated to keep working towards their goal of increasing efficiency.