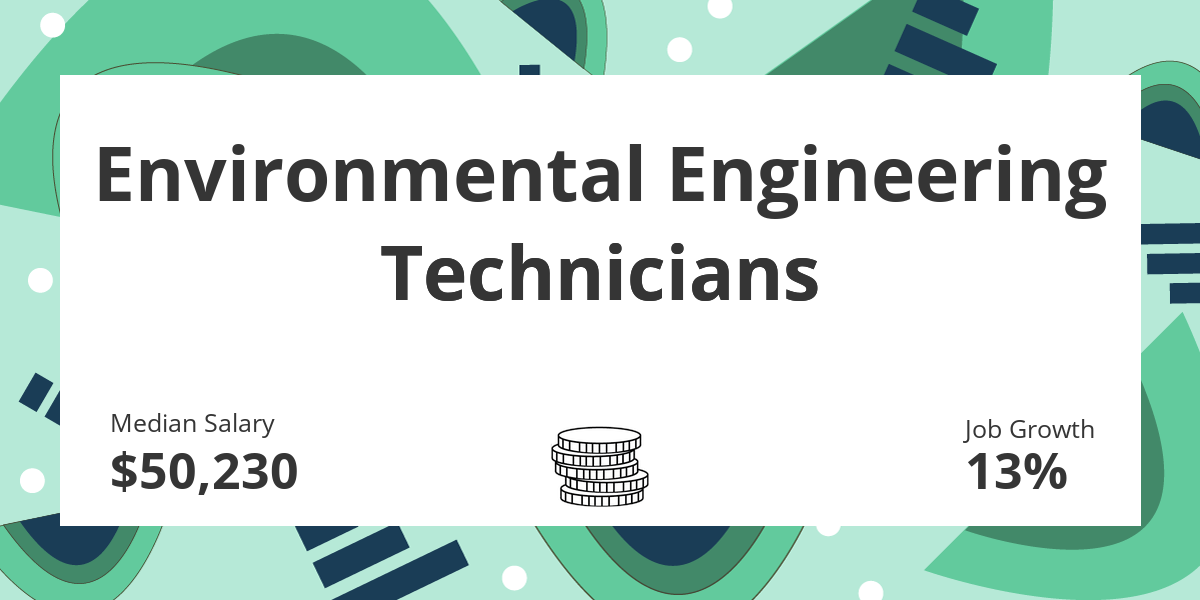
A cost estimate is required for almost everything a company does. This is the job of cost estimators. They assist companies in determining the cost of developing and manufacturing new products and services. They must also evaluate the costs of building a new structure. This includes cost analysis of labor and materials.
Construction companies employ the majority of cost estimators. They need to be able to understand construction processes and methods. They should also be proficient in computer-aided designing (CAD) software. This software can be used to improve the efficiency of manufacturing and design. Also, cost estimators must be able to access data from databases. They can also make use of other software like Microsoft Excel.
They work closely with other professionals to produce accurate cost estimates. They review the project blueprints and site conditions to determine the cost of each component. Engineers may be involved in determining the dimensions and machining procedures required.
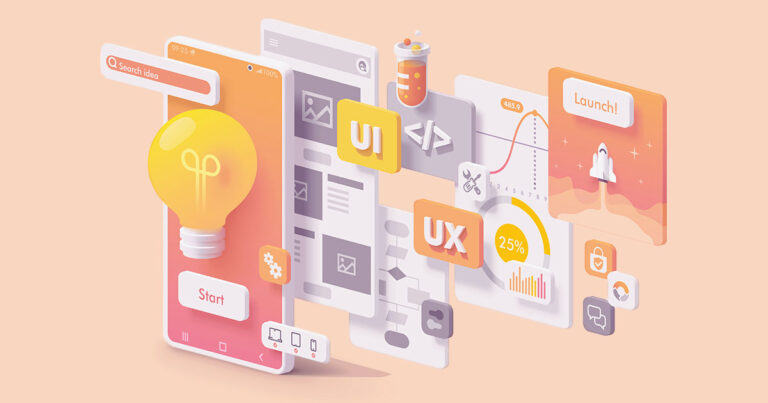
Cost estimators should be detail-oriented, assertive and reliable. They should be able analyze difficult information. They must also be able to present findings accurately and assertively. They must also be able and willing to collaborate with clients and professionals.
In most cases, cost estimators work for the engineering or cost department of a company. They must have a strong background in mathematics and science. They should also be familiarized with computer software, including BIM, CAD and commercial. You may need to take a certification class. Certified Cost Estimator/Analysts (CCEA), Professional Estimator/Analysts, and Certified Professional Estimators are just a few of the certifications available.
Cost estimators might be experts in particular services or industries. One person may specialize in building costs or construction, while another might be more interested in software development costs. Cost estimators could also be employed in other areas like automotive repair and management, building construction, or specialty trade contractors.
These people communicate with engineers, clients, or suppliers. They also have a good understanding of industry terminology. Before preparing cost estimates, they also have a lot of knowledge. These individuals are skilled in cost estimations and many others conduct studies to determine the effects of different processes on prices, and then find ways to reduce them.
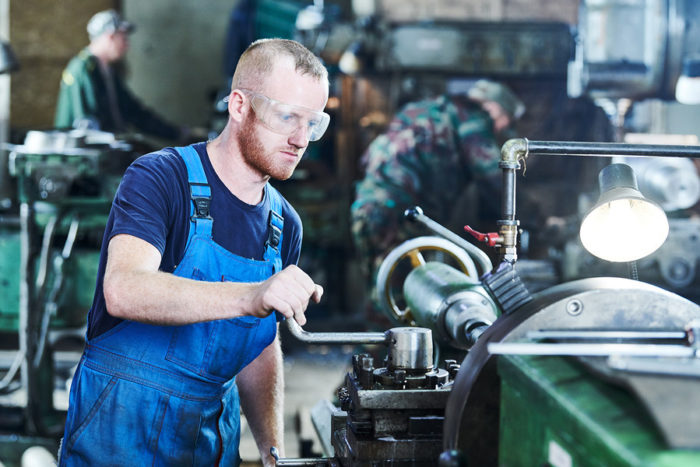
A bachelor's degree may be required depending on the industry. They may also require an internship. They may also benefit from cooperative education programs. A degree in building construction, or construction management is also an advantage for construction companies.
They work in construction and other manufacturing companies. They are responsible for estimating the costs of products and services to ensure that companies can place profitable bids. They also analyze data concerning the supply chain and other factors that can affect costs. Cost estimators can also work for government programs. They may also be required to redesign existing products.
Cost estimators must have a strong understanding of computer-aided design (CAD) software. They can also be trained in the use of automatic cost estimation software.
FAQ
Why is logistics so important in manufacturing?
Logistics are an essential part of any business. Logistics can help you achieve amazing results by helping to manage product flow from raw materials to finished products.
Logistics plays a significant role in reducing cost and increasing efficiency.
How does manufacturing avoid bottlenecks in production?
You can avoid bottlenecks in production by making sure that everything runs smoothly throughout the production cycle, from the moment you receive an order to the moment the product is shipped.
This includes both planning for capacity and quality control.
The best way to do this is to use continuous improvement techniques such as Six Sigma.
Six Sigma Management System is a method to increase quality and reduce waste throughout your organization.
It focuses on eliminating variation and creating consistency in your work.
How can manufacturing excess production be decreased?
Better inventory management is key to reducing excess production. This would reduce the time needed to manage inventory. This will allow us to free up resources for more productive tasks.
One way to do this is to adopt a Kanban system. A Kanban board can be used to monitor work progress. Kanban systems allow work items to move through different states until they reach their final destination. Each state represents an individual priority level.
To illustrate, work can move from one stage or another when it is complete enough for it to be moved to a new stage. But if a task remains in the beginning stages it will stay that way until it reaches its end.
This allows you to keep work moving along while making sure that no work gets neglected. Managers can view the Kanban board to see how much work they have done. This information allows them to adjust their workflow based on real-time data.
Lean manufacturing is another option to control inventory levels. Lean manufacturing is about eliminating waste from all stages of the production process. Anything that does nothing to add value to a product is waste. There are several types of waste that you might encounter:
-
Overproduction
-
Inventory
-
Unnecessary packaging
-
Overstock materials
These ideas can help manufacturers improve efficiency and reduce costs.
What skills are required to be a production manager?
A production planner must be organized, flexible, and able multitask to succeed. Also, you must be able and willing to communicate with clients and coworkers.
What is production plan?
Production Planning refers to the development of a plan for every aspect of production. This document aims to ensure that everything is planned and ready when you are ready to shoot. This document should include information about how to achieve the best results on-set. This information includes locations, crew details and equipment requirements.
The first step is to decide what you want. You may have decided where to shoot or even specific locations you want to use. Once you have identified the scenes and locations, you can start to determine which elements are required for each scene. You might decide you need a car, but not sure what make or model. In this case, you could start looking up cars online to find out what models are available and then narrow your choices by choosing between different makes and models.
After you have selected the car you want, you can begin to think about additional features. Do you have people who need to be seated in the front seat? Maybe you need someone to move around in the back. You might want to change your interior color from black and white. These questions will help guide you in determining the ideal look and feel for your car. The type of shots that you are looking for is another thing to consider. You will be filming close-ups and wide angles. Maybe you want to show your engine or the steering wheel. These things will help you to identify the car that you are looking for.
Once you have made all the necessary decisions, you can start to create a schedule. A schedule will tell you when you need to start shooting and when you need to finish. Every day will have a time for you to arrive at the location, leave when you are leaving and return home when you are done. This way, everyone knows what they need to do and when. It is possible to make arrangements in advance for additional staff if you are looking to hire. There is no point in hiring someone who won't turn up because you didn't let him know.
When creating your schedule, you will also need to consider the number of days you need to film. Some projects take only a few days while others can last several weeks. When creating your schedule, be aware of whether you need more shots per day. Multiple takes of the same location will lead to higher costs and take more time. It's better to be safe than sorry and shoot less takes if you're not certain whether you need more takes.
Budget setting is another important aspect in production planning. Setting a realistic budget is essential as it will allow you to work within your means. Keep in mind that you can always reduce your budget if you face unexpected difficulties. It is important to not overestimate how much you will spend. You'll end up with less money after paying for other things if the cost is underestimated.
Production planning can be a complex process. However, once you know how everything works together it will become easier to plan future projects.
What are the 4 types of manufacturing?
Manufacturing refers to the transformation of raw materials into useful products by using machines and processes. It includes many different activities like designing, building and testing, packaging, shipping and selling, as well as servicing.
Statistics
- [54][55] These are the top 50 countries by the total value of manufacturing output in US dollars for its noted year according to World Bank.[56] (en.wikipedia.org)
- According to the United Nations Industrial Development Organization (UNIDO), China is the top manufacturer worldwide by 2019 output, producing 28.7% of the total global manufacturing output, followed by the United States, Japan, Germany, and India.[52][53] (en.wikipedia.org)
- (2:04) MTO is a production technique wherein products are customized according to customer specifications, and production only starts after an order is received. (oracle.com)
- It's estimated that 10.8% of the U.S. GDP in 2020 was contributed to manufacturing. (investopedia.com)
- According to a Statista study, U.S. businesses spent $1.63 trillion on logistics in 2019, moving goods from origin to end user through various supply chain network segments. (netsuite.com)
External Links
How To
How to Use the Just In Time Method in Production
Just-in-time is a way to cut costs and increase efficiency in business processes. It allows you to get the right amount resources at the right time. This means that your only pay for the resources you actually use. Frederick Taylor, a 1900s foreman, first coined the term. Taylor observed that overtime was paid to workers if they were late in working. He realized that workers should have enough time to complete their jobs before they begin work. This would help increase productivity.
The idea behind JIT is that you should plan ahead and have everything ready so you don't waste money. Also, you should look at the whole project from start-to-finish and make sure you have the resources necessary to address any issues. You will have the resources and people to solve any problems you anticipate. This way, you won't end up paying extra money for things that weren't really necessary.
There are many types of JIT methods.
-
Demand-driven: This JIT is where you place regular orders for the parts/materials that are needed for your project. This will allow you to track how much material you have left over after using it. This will let you know how long it will be to produce more.
-
Inventory-based : You can stock the materials you need in advance. This allows for you to anticipate how much you can sell.
-
Project-driven: This method allows you to set aside enough funds for your project. When you know how much you need, you'll purchase the appropriate amount of materials.
-
Resource-based JIT: This is the most popular form of JIT. Here you can allocate certain resources based purely on demand. For example, if there is a lot of work coming in, you will have more people assigned to them. If there aren't many orders, you will assign fewer people.
-
Cost-based: This approach is very similar to resource-based. However, you don't just care about the number of people you have; you also need to consider how much each person will cost.
-
Price-based: This is a variant of cost-based. However, instead of focusing on the individual workers' costs, this looks at the total price of the company.
-
Material-based: This is very similar to cost-based but instead of looking at total costs of the company you are concerned with how many raw materials you use on an average.
-
Time-based: Another variation of resource-based JIT. Instead of focusing only on how much each employee is costing, you should focus on how long it takes to complete your project.
-
Quality-based JIT - This is another form of resource-based JIT. Instead of looking at the labor costs and time it takes to make a product, think about its quality.
-
Value-based JIT is the newest form of JIT. You don't worry about whether the products work or if they meet customer expectations. Instead, your goal is to add value to the market.
-
Stock-based: This inventory-based approach focuses on how many items are being produced at any one time. It's useful when you want maximum production and minimal inventory.
-
Just-intime planning (JIT), is a combination JIT/sales chain management. This refers to the scheduling of the delivery of components as soon after they are ordered. This is important as it reduces lead time and increases throughput.