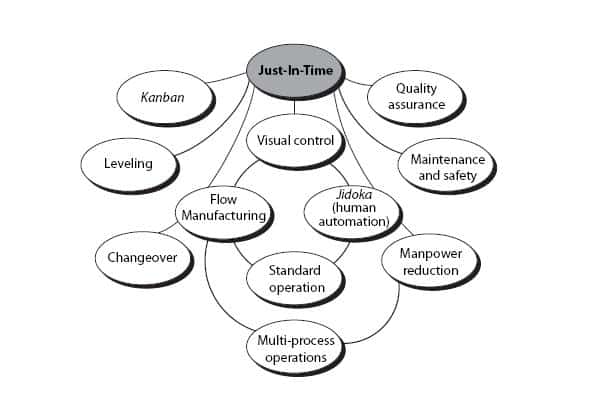
Flow is the state of being when all the steps in a production process follow each other smoothly without interruption. Each step adds to the product's value, and goods move smoothly through the manufacturing process without being stopped. Production of a specified quantity of stock is planned in many companies to make sure that production orders are met as efficiently as possible. This is Lean Manufacturing's term for "push" production. Here are some key elements to flow:
Manufacturing just-in-time
When lean manufacturing was first introduced to the U.S. in the late 1970s, "just-in-time" manufacturing was the dominant paradigm. Although the concept is useful, it's not the best way to run your company. Many new skills and mindsets are required to lower costs and improve efficiency. But it's worth trying if you want the best results.
Standardization and the ability to work with smaller lots are some of the key elements of just-in–time manufacturing. In order to encourage a just in time mindset, it is important to plan your facility layout. For example, cellular manufacturing can help to support production flow. Cellular organization of workstations or parts bins can help ensure a smoother flow. And just-in-time manufacturers should avoid long changeover times.
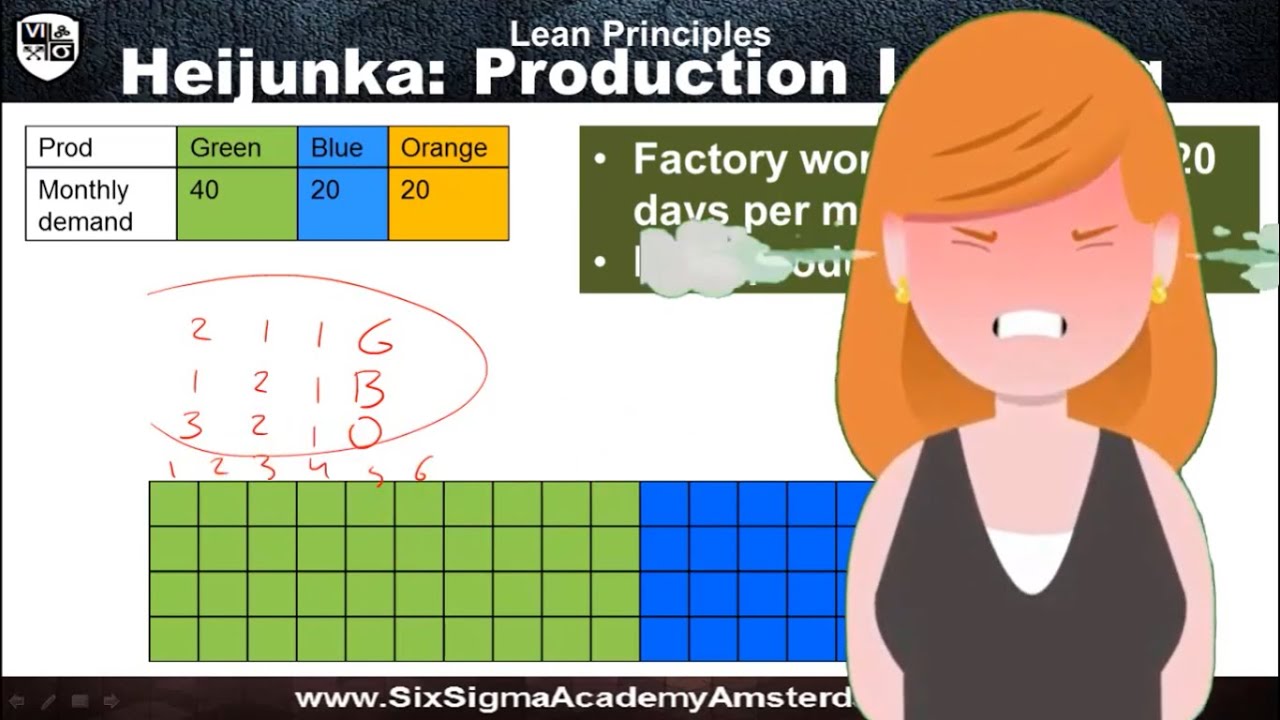
Standardized work
First, you have to create standardized work before applying lean manufacturing in manufacturing processes. This system of work focuses on the workers and what they must do to create a product or service. It also refers to the process of continuously improving the system through kaizen. Cell leaders are responsible for updating standardized work documentation as soon as the takttime changes. Standardized work documents provide a basis for improvement activities including kaizen or improvement activities.
Standardized work processes help improve service quality and productivity. These processes reduce product development time, and they reduce human error. This helps organizations to resolve problems more quickly because people understand the process better. This allows the company to improve its customer service and implement continuous improvement. Once standardized, it is not difficult to implement these processes in a company. A mission statement is an important part of any company.
Continuous improvement
Lean principles are a way to improve your company's performance. This leads to a number of benefits. These benefits are usually additive, but one thread links them all: increased productivity, lower costs, and shorter lead times. The ultimate goal of continuous improvement is to increase value creation. How does continuous improvement work? This article will show you some of the benefits of continuous improvement. It's simple: Continuous Improvement helps companies save money.
A company that is committed to continuous improvement will focus more on incremental changes than on large-scale ones. Even though individual improvements might seem insignificant or small, the overall effect of continuous improvement is significant. Improvement is a slow process that requires small measured steps, rather than big leaps. Continuous improvement is a process that aims to align goals in a lean manufacturing environment. This allows the business maximize productivity and profitability. Continuous improvement can streamline the production process and allow all processes to work together towards a common goal.
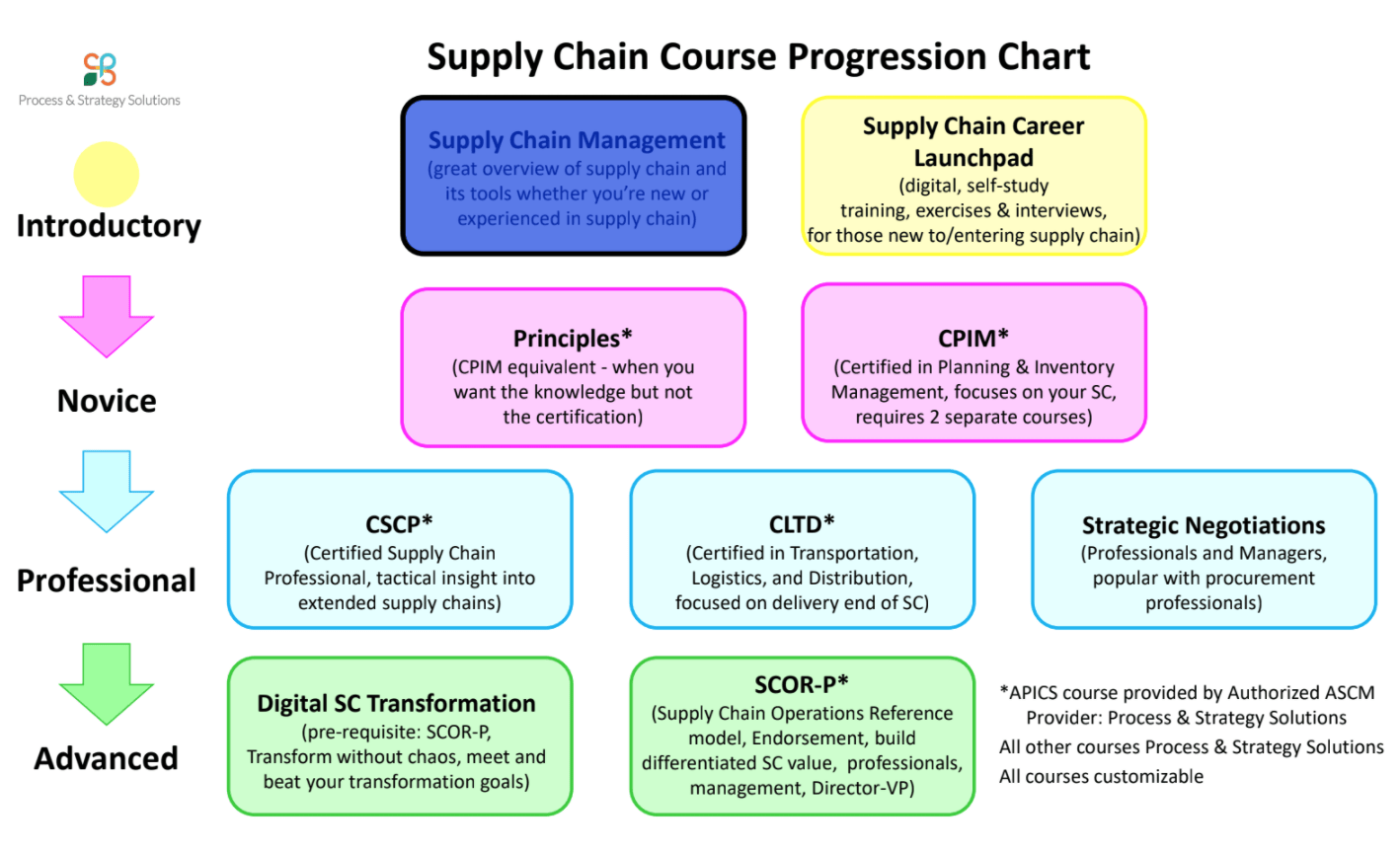
Kaizen
Kaizen in lean production focuses primarily on waste elimination. It is sometimes used to improve production yield or reduce lead times. Each role is assigned to a team of employees who will investigate the problem and develop possible solutions. A kaizen activity usually starts with the creation a process value stream map. Next, the team conducts time analyses of all relevant operations. The process continues until each step is improved, and the overall process becomes more efficient.
A manufacturing plant might purchase a new forklift after identifying inefficiencies. Its operator could move inventory around to make loading/unloading more efficient. Similar to the value stream, it is a map of all processes that produce products or services. Five different S's can be used during the mapping process to improve employee productivity and workplace practices. There are seven types of muda. Each type of muda focuses only on one aspect of a manufacturing procedure.
FAQ
What skills are required to be a production manager?
You must be flexible and organized to become a productive production planner. It is also important to be able communicate with colleagues and clients.
Why is logistics so important in manufacturing?
Logistics is an integral part of every business. They help you achieve great results by helping you manage all aspects of product flow, from raw materials to finished goods.
Logistics play an important role in reducing costs as well as increasing efficiency.
What does warehouse mean?
A warehouse, or storage facility, is where goods are stored prior to being sold. It can be an outdoor or indoor area. It could be one or both.
What are the requirements to start a logistics business?
To be a successful businessman in logistics, you will need many skills and knowledge. Effective communication skills are necessary to work with suppliers and clients. You will need to know how to interpret data and draw conclusions. You must be able manage stress and pressure under pressure. To increase efficiency and creativity, you need to be creative. To motivate and guide your team towards reaching organizational goals, you must have strong leadership skills.
You must be organized to meet tight deadlines.
How can manufacturing efficiency be improved?
First, determine which factors have the greatest impact on production time. Then we need to find ways to improve these factors. If you don't know where to start, then think about which factor(s) have the biggest impact on production time. Once you've identified them all, find solutions to each one.
What are the 4 types manufacturing?
Manufacturing is the process by which raw materials are transformed into useful products through machines and processes. It can involve many activities like designing, manufacturing, testing packaging, shipping, selling and servicing.
Statistics
- (2:04) MTO is a production technique wherein products are customized according to customer specifications, and production only starts after an order is received. (oracle.com)
- Many factories witnessed a 30% increase in output due to the shift to electric motors. (en.wikipedia.org)
- In the United States, for example, manufacturing makes up 15% of the economic output. (twi-global.com)
- Job #1 is delivering the ordered product according to specifications: color, size, brand, and quantity. (netsuite.com)
- [54][55] These are the top 50 countries by the total value of manufacturing output in US dollars for its noted year according to World Bank.[56] (en.wikipedia.org)
External Links
How To
How to use the Just-In Time Method in Production
Just-in-time (JIT) is a method that is used to reduce costs and maximize efficiency in business processes. It's a way to ensure that you get the right resources at just the right time. This means that your only pay for the resources you actually use. Frederick Taylor developed the concept while working as foreman in early 1900s. He noticed that workers were often paid overtime when they had to work late. He decided to ensure workers have enough time to do their jobs before starting work to improve productivity.
JIT is a way to plan ahead and make sure you don't waste any money. Also, you should look at the whole project from start-to-finish and make sure you have the resources necessary to address any issues. You'll be prepared to handle any potential problems if you know in advance. This will ensure that you don't spend more money on things that aren't necessary.
There are different types of JIT methods:
-
Demand-driven JIT: You order the parts and materials you need for your project every other day. This will let you track the amount of material left over after you've used it. This will allow you to calculate how long it will take to make more.
-
Inventory-based: This type allows you to stock the materials needed for your projects ahead of time. This allows you to forecast how much you will sell.
-
Project-driven: This method allows you to set aside enough funds for your project. Knowing how much money you have available will help you purchase the correct amount of materials.
-
Resource-based JIT is the most widespread form. You assign certain resources based off demand. You will, for example, assign more staff to deal with large orders. If you don't receive many orders, then you'll assign fewer employees to handle the load.
-
Cost-based : This is similar in concept to resource-based. But here, you aren't concerned about how many people your company has but how much each individual costs.
-
Price-based pricing: This is similar in concept to cost-based but instead you look at how much each worker costs, it looks at the overall company's price.
-
Material-based: This approach is similar to cost-based. However, instead of looking at the total cost for the company, you look at how much you spend on average on raw materials.
-
Time-based: This is another variation of resource-based JIT. Instead of worrying about how much each worker costs, you can focus on how long the project takes.
-
Quality-based JIT: This is another variation of resource based JIT. Instead of looking at the labor costs and time it takes to make a product, think about its quality.
-
Value-based: This is one of the newest forms of JIT. This is where you don't care about how the products perform or whether they meet customers' expectations. Instead, you focus on the added value that you provide to your market.
-
Stock-based is an inventory-based system that measures the number of items produced at any given moment. This method is useful when you want to increase production while decreasing inventory.
-
Just-intime planning (JIT), is a combination JIT/sales chain management. It's the process of scheduling delivery of components immediately after they are ordered. It's important because it reduces lead times and increases throughput.