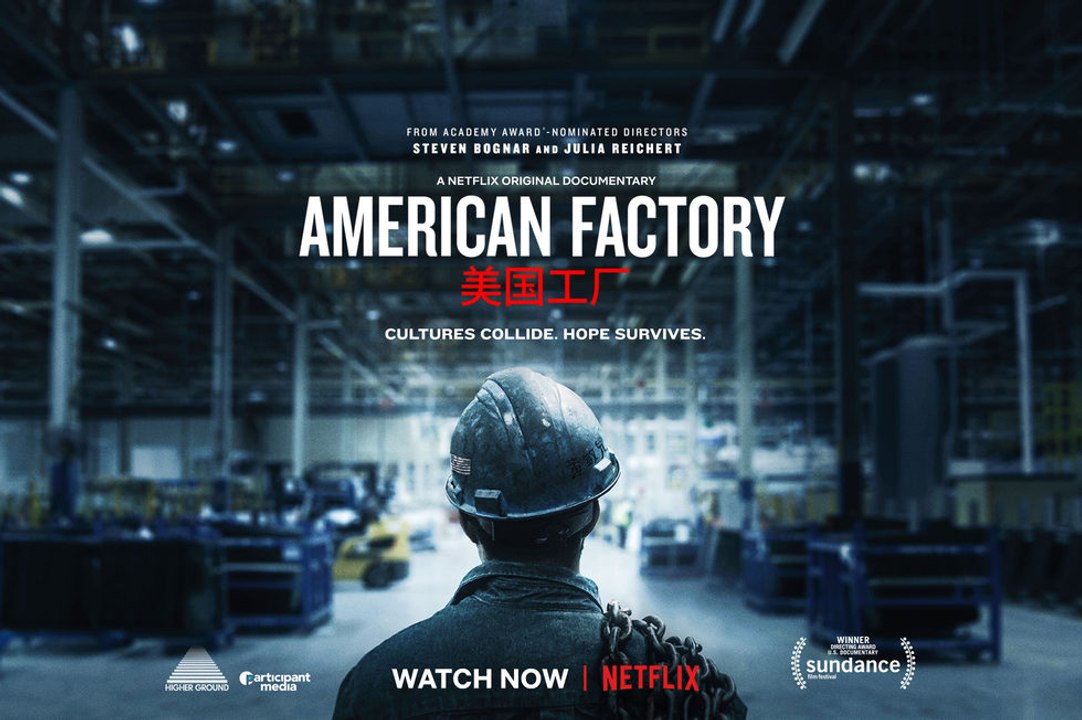
Andon is a visual indicator that draws attention to a problem in order to fix it permanently. It's a tool to empower plant floor operators, and speed up teamwork.
Andon
It is a Japanese word that comes from fixed paper-enclosed Lanterns used in the Edo Period, which was between the 17th and 19th centuries. In Japanese, the term can refer to an alert system which uses light or sound signals to signal a process problem.
Toyota uses this term to describe its Jidoka (or build-in quality), which is a major component of the TPS (Toyota Production System). It is often cited in the US as the origin of a concept which allows employees on the production line to stop it if there are safety or quality problems.
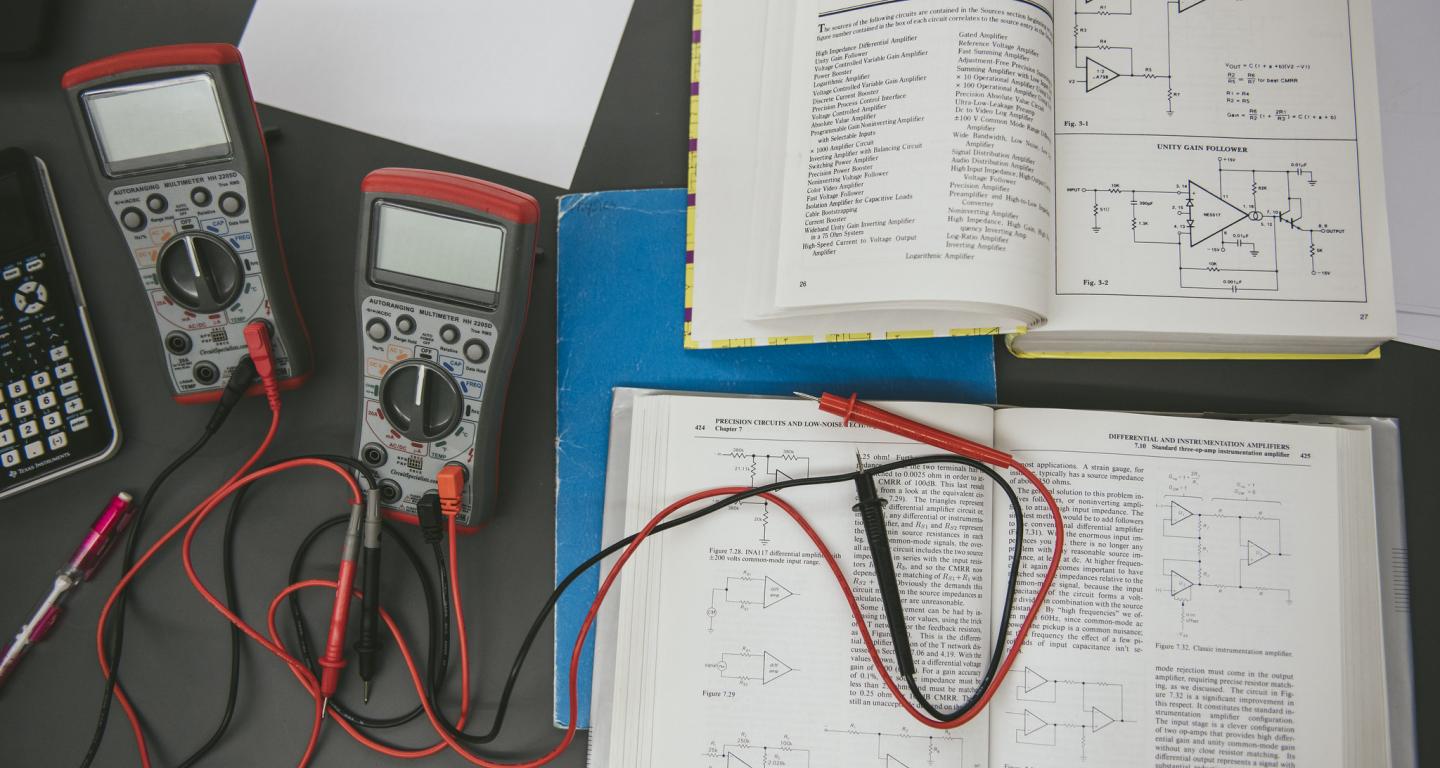
What is Andon?
Toyota pioneered the Andon lean manufacturing system. The system is simple and consists of an LED board with three colors: green, yellow, and red. Each color indicates the different status of production. The production line runs normally when the green light is on. When the yellow signal is lit, an issue has been detected and is under investigation. All production stops when the red signal is illuminated. Workers can take a break, prepare parts, go to help or fill their bins, etc.
Andon is very easy to use. Supervisors can understand immediately what happened. The system provides immediate feedback to ensure that any problems are dealt with as soon as they arise.
There are several types of andons. The most common one is a light that flashes red with a buzzer or sound to alert the production team. These signal alert and resolve systems help identify problems that might lead to downtime, or repeat issues.
A good andonboard helps to keep production moving when a fault occurs. It is a simple but effective tool which increases productivity and reduces downtime. It also improves the product quality and safety.
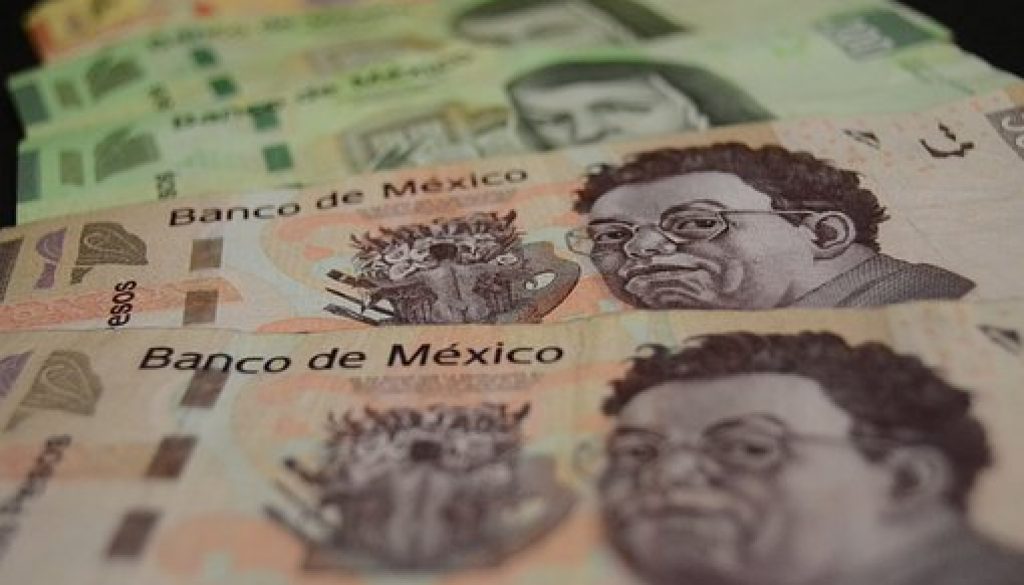
What is andon toyota?
Toyota provided a special cord for employees to pull in the event that they noticed a potential problem with one of its cars. If a worker felt the car was compromised, they could instantly stop the production line by pulling this cord.
Modern andon systems also use technology to curate information, which makes it easier to identify emerging problems, send notifications to stakeholders in real-time, and determine the root cause of a problem that requires a long term fix. Human touch is essential to interpret and act upon this information.
How can I make andon function?
Creating a culture of openness and honesty among workers and supervisors is essential. They are more likely to hide problems if they hesitate, and they may miss the opportunity to solve them. It is best to link line stops and problem resolution to encourage workers to pull the cord or press the button when they notice something wrong.
FAQ
What are the responsibilities for a manufacturing manager
A manufacturing manager must ensure that all manufacturing processes are efficient and effective. They should be alert for any potential problems in the company and react accordingly.
They should also be able and comfortable communicating with other departments like sales and marketing.
They should be informed about industry trends and be able make use of this information to improve their productivity and efficiency.
What are the logistics products?
Logistics refers to the movement of goods from one place to another.
They encompass all aspects transport, including packaging and loading, transporting, storage, unloading.
Logisticians ensure that the product is delivered to the correct place, at the right time, and under safe conditions. They provide information on demand forecasts as well stock levels, production schedules and availability of raw material.
They coordinate with vendors and suppliers, keep track of shipments, monitor quality standards and perform inventory and order replenishment.
What are the 7 Rs of logistics?
The acronym 7R's of Logistic is an acronym that stands for seven fundamental principles of logistics management. It was created by the International Association of Business Logisticians and published in 2004 under its "Seven Principles of Logistics Management".
The following letters form the acronym:
-
Responsible – ensure that all actions are legal and don't cause harm to anyone else.
-
Reliable – have faith in your ability and capability to keep promises.
-
Use resources effectively and sparingly.
-
Realistic - consider all aspects of operations, including cost-effectiveness and environmental impact.
-
Respectful - show respect and treat others fairly and fairly
-
Reliable - Find ways to save money and increase your productivity.
-
Recognizable - provide customers with value-added services.
What is the responsibility for a logistics manager
A logistics manager ensures that all goods are delivered on time and without damage. This is done through his/her expertise and knowledge about the company's product range. He/she should ensure that sufficient stock is available in order to meet customer demand.
Statistics
- Many factories witnessed a 30% increase in output due to the shift to electric motors. (en.wikipedia.org)
- You can multiply the result by 100 to get the total percent of monthly overhead. (investopedia.com)
- Job #1 is delivering the ordered product according to specifications: color, size, brand, and quantity. (netsuite.com)
- In the United States, for example, manufacturing makes up 15% of the economic output. (twi-global.com)
- According to a Statista study, U.S. businesses spent $1.63 trillion on logistics in 2019, moving goods from origin to end user through various supply chain network segments. (netsuite.com)
External Links
How To
How to Use 5S to Increase Productivity in Manufacturing
5S stands in for "Sort", the "Set In Order", "Standardize", or "Separate". The 5S methodology was developed at Toyota Motor Corporation in 1954. It allows companies to improve their work environment, thereby achieving greater efficiency.
This method has the basic goal of standardizing production processes to make them repeatable. Cleaning, sorting and packing are all done daily. Through these actions, workers can perform their jobs more efficiently because they know what to expect from them.
There are five steps that you need to follow in order to implement 5S. Each step has a different action and leads to higher efficiency. You can make it easy for people to find things later by sorting them. Once you have placed items in an ordered fashion, you will put them together. Then, after you separate your inventory into groups, you store those groups in containers that are easy to access. Labeling your containers will ensure that everything is correctly labeled.
This requires employees to critically evaluate how they work. Employees must understand why they do certain tasks and decide if there's another way to accomplish them without relying on the old ways of doing things. They must learn new skills and techniques in order to implement the 5S system.
In addition to increasing efficiency, the 5S method also improves morale and teamwork among employees. They feel more motivated to work towards achieving greater efficiency as they see the results.