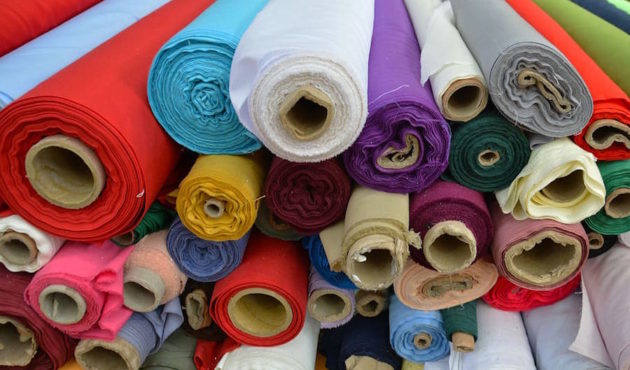
Japanese factories produce highquality products at low cost. They are the backbone and 5% of the GDP of Japan. They have had to deal with stricter standards, increased competition, and the cost pressures resulting from the recent recession.
In a whitepaper published last year by the government, it was found that Japanese businesses were not ready to deal with a cutoff in parts procurement. The recession took a toll on Japan's auto industry. Traditionally, the car manufacturing industry relies on 30,000 different parts, so a disruption to the supply chain can stop production. Some parts can't be substituted.
Japanese manufacturers have been working closely with their suppliers to find solutions and improve their efficiency to ensure high-quality products. They are also encouraging feedback from workers, salesmen and quality inspectors.
Japanese manufacturers are concerned about the high number of accidents on the factory floor. There have been numerous safety scandals in the country's industrial sector. This has led to increased scrutiny of the standard of factory work.
The influx of non-regular workers has also been a problem in the production of Japanese goods. The influx of non-regular labor allows companies to lower labor costs but increases the risk of accidents, and de-skills the production floor. Companies are focusing on training regular workers to make them safer and better.
Japan's shrinking birthrate is responsible for the growing labor force shortage. A 25-year high number of Japanese companies are complaining of a lack of labor. Japanese companies will face further challenges if their labor force shrinks.
Although there are fewer skilled workers, many factories have cut costs. There are a growing number of "factories", which employ less than ten people. Many of these small workshops produce the best in the world equipment.
China and South Korea are increasing their competition for the Japanese manufacturing sector. Many factories are trying reduce costs and increase productivity. However, the Japanese government has warned the industry that it will lose its competitive edge in international markets.
Japan is confronted with increased competition from Asia as well as abroad and it is questioning whether its ability to adapt and adjust its processes to meet this demand. Even if it is able to adapt, skilled workers are expected to increase.
Japanese factories are a major source of components for global markets. They also source advanced materials like silicon chips for smart phones and computers. While Chinese factories excel in low-cost assembly operations they still rely on Japan to supply the essential components.
Despite their efforts to improve productivity and quality, Japanese companies have been subject to increased competition from overseas. They have had to reduce their costs due to the fact that their products are less valuable in the domestic market. Despite these challenges the Japanese have managed to maintain a high level production standard.
FAQ
What are the essential elements of running a logistics firm?
A successful logistics business requires a lot more than just knowledge. Effective communication skills are necessary to work with suppliers and clients. You will need to know how to interpret data and draw conclusions. You must be able and able to handle stress situations and work under pressure. To improve efficiency, you must be innovative and creative. You must be a strong leader to motivate others and direct them to achieve organizational goals.
To meet tight deadlines, you must also be efficient and organized.
What skills are required to be a production manager?
You must be flexible and organized to become a productive production planner. Communication skills are essential to ensure that you can communicate effectively with clients, colleagues, and customers.
Is it possible to automate certain parts of manufacturing
Yes! Since ancient times, automation has been in existence. The wheel was invented by the Egyptians thousands of years ago. To help us build assembly lines, we now have robots.
Robotics is used in many manufacturing processes today. These include:
-
Robots for assembly line
-
Robot welding
-
Robot painting
-
Robotics inspection
-
Robots that produce products
Manufacturing could also benefit from automation in other ways. For instance, 3D printing allows us make custom products and not have to wait for months or even weeks to get them made.
What is the responsibility of a manufacturing manager?
Manufacturing managers must ensure that manufacturing processes are efficient, effective, and cost-effective. They must also be alert to any potential problems and take appropriate action.
They must also be able to communicate with sales and marketing departments.
They should be informed about industry trends and be able make use of this information to improve their productivity and efficiency.
Why automate your warehouse
Modern warehousing has seen automation take center stage. With the rise of ecommerce, there is a greater demand for faster delivery times as well as more efficient processes.
Warehouses must adapt quickly to meet changing customer needs. Technology investment is necessary to enable warehouses to respond quickly to changing demands. Automation of warehouses offers many benefits. These are some of the benefits that automation can bring to warehouses:
-
Increases throughput/productivity
-
Reduces errors
-
Accuracy is improved
-
Safety enhancements
-
Eliminates bottlenecks
-
Allows companies scale more easily
-
Increases efficiency of workers
-
The warehouse can be viewed from all angles.
-
Enhances customer experience
-
Improves employee satisfaction
-
This reduces downtime while increasing uptime
-
You can be sure that high-quality products will arrive on time
-
Human error can be eliminated
-
Helps ensure compliance with regulations
How can we improve manufacturing efficiency?
The first step is to determine the key factors that impact production time. Next, we must find ways to improve those factors. If you don’t know how to start, look at which factors have the greatest impact upon production time. Once you've identified them, try to find solutions for each of those factors.
Statistics
- (2:04) MTO is a production technique wherein products are customized according to customer specifications, and production only starts after an order is received. (oracle.com)
- You can multiply the result by 100 to get the total percent of monthly overhead. (investopedia.com)
- [54][55] These are the top 50 countries by the total value of manufacturing output in US dollars for its noted year according to World Bank.[56] (en.wikipedia.org)
- In the United States, for example, manufacturing makes up 15% of the economic output. (twi-global.com)
- According to a Statista study, U.S. businesses spent $1.63 trillion on logistics in 2019, moving goods from origin to end user through various supply chain network segments. (netsuite.com)
External Links
How To
How to Use Just-In-Time Production
Just-in-time is a way to cut costs and increase efficiency in business processes. It's a way to ensure that you get the right resources at just the right time. This means that only what you use is charged to your account. Frederick Taylor was the first to coin this term. He developed it while working as a foreman during the early 1900s. Taylor observed that overtime was paid to workers if they were late in working. He then concluded that if he could ensure that workers had enough time to do their job before starting to work, this would improve productivity.
JIT is an acronym that means you need to plan ahead so you don’t waste your money. The entire project should be looked at from start to finish. You need to ensure you have enough resources to tackle any issues that might arise. You will have the resources and people to solve any problems you anticipate. This will ensure that you don't spend more money on things that aren't necessary.
There are many JIT methods.
-
Demand-driven: This JIT is where you place regular orders for the parts/materials that are needed for your project. This will allow you to track how much material you have left over after using it. This will allow you to calculate how long it will take to make more.
-
Inventory-based: This type allows you to stock the materials needed for your projects ahead of time. This allows for you to anticipate how much you can sell.
-
Project-driven : This is a method where you make sure that enough money is set aside to pay the project's cost. You will be able to purchase the right amount of materials if you know what you need.
-
Resource-based: This is the most common form of JIT. This is where you assign resources based upon demand. If you have many orders, you will assign more people to manage them. If you don't have many orders, you'll assign fewer people to handle the workload.
-
Cost-based: This is a similar approach to resource-based but you are not only concerned with how many people you have, but also how much each one costs.
-
Price-based: This is very similar to cost-based, except that instead of looking at how much each individual worker costs, you look at the overall price of the company.
-
Material-based: This is quite similar to cost-based, but instead of looking at the total cost of the company, you're concerned with how much raw materials you spend on average.
-
Time-based JIT is another form of resource-based JIT. Instead of worrying about how much each worker costs, you can focus on how long the project takes.
-
Quality-based: This is yet another variation of resource-based JIT. Instead of worrying about the costs of each employee or how long it takes for something to be made, you should think about how quality your product is.
-
Value-based JIT is the newest form of JIT. In this scenario, you're not concerned about how products perform or whether customers expect them to meet their expectations. Instead, your focus is on the value you bring to the market.
-
Stock-based: This inventory-based approach focuses on how many items are being produced at any one time. This method is useful when you want to increase production while decreasing inventory.
-
Just-intime (JIT), planning is a combination JIT management and supply chain management. It's the process of scheduling delivery of components immediately after they are ordered. It's important because it reduces lead times and increases throughput.