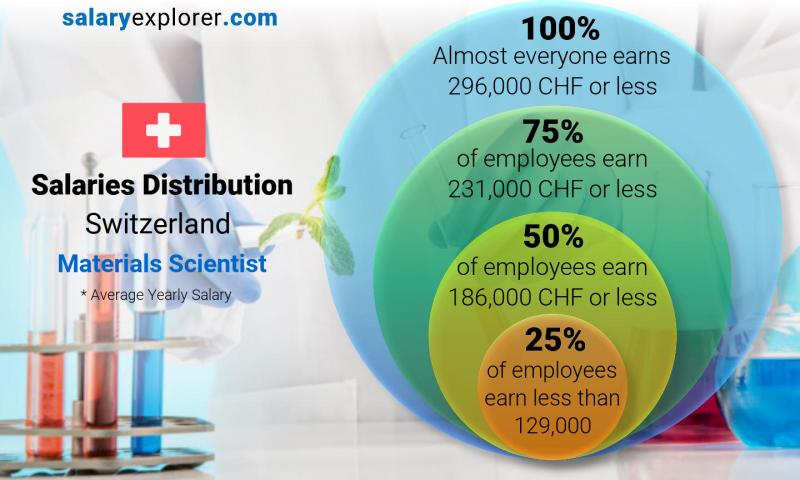
The United States is third in manufacturing in the world and saw its manufacturing output reach a record at $2.00 trillion in Q1 2018. This was nearly twice the amount it had before the Great Recession. Despite a strong domestic economy and a robust manufacturing sector, the United States is still taking a cautious approach to its current problems. This is either due to a lack in investment or a shortage of skilled labor. We must be more aggressive in confronting the challenges that face our industry.
Since 2000, 5 million fewer jobs have been created.
Since 2000, the US has lost five millions manufacturing jobs. While some people believe trade with China is the reason, it only accounts for a fourth to four percent of the decline in manufacturing job opportunities. Manufacturing jobs were also lost in countries that couldn't compete with Chinese imports. But there are many factors that contributed to the decline of manufacturing jobs. Here are some of these reasons:
During the last two decades, the US manufacturing sector lost nearly a third of its jobs. It stood at 17 million in 1965, and fell to just 12 million in 2010. Trade is not responsible for the decline in manufacturing jobs. However, it has been caused structural problems like a decline of capital investment, output, and productivity. These problems are not sustainable. While productivity gains have a major role to play in the decline, they weren't enough to offset the loss of manufacturing jobs. Automation is the problem, and not productivity improvements.
Strong demand is for manufactured products
Despite the decline in consumer spending, the US still has a strong demand to manufacture goods. In 1945 personal spending on durable goods accounted 58% of total spending. Today, it accounts for only 28%. The reason is that the price of making and selling these goods has fallen while their content has increased. As a result, the cost of computers, televisions, and sound equipment has fallen significantly.
The US has seen an increase in manufactured goods production due to the recovery in manufacturing activity. The Fifth District Manufacturing Activity Survey reveals that the demand for manufactured products is strong, with production increasing rapidly. However, supply chain problems are slowing down output. The increased production has stressed supply chains. Respondents report that they have experienced supply chain disruptions that impact their ability keep adequate inventories. Backlogs have increased as well, and vendors lead times have been longer.
In the last decade, the trade deficit in manufactured goods has more that doubled
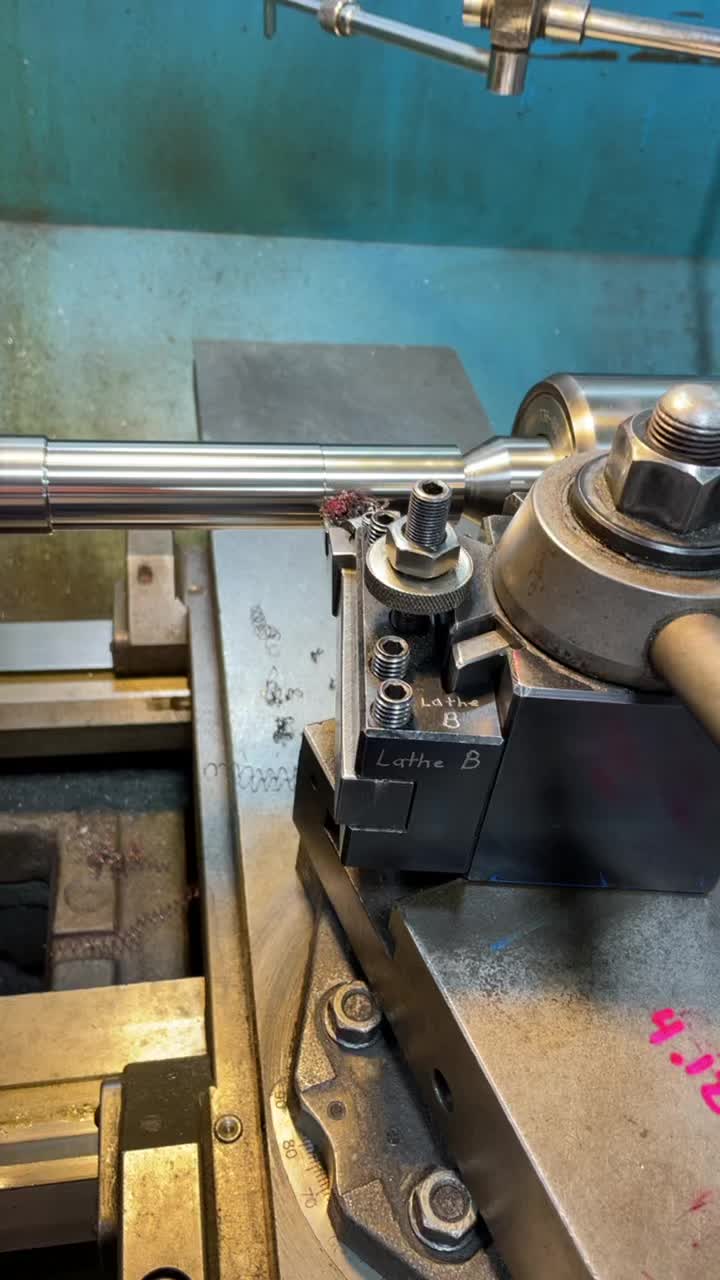
Some economists worry that the U.S.'s trade surplus will lower global growth and create more instability among its trading partners. High imports of US-made goods are not necessarily a negative thing for the U.S., as they are crucial to global economic stability. High levels of foreign market demand can make it difficult for the U.S. to achieve full employment.
Since 2000, the U.S. manufactured goods trade deficit has almost doubled. Partially, the US trade deficit in manufactured goods has doubled since 2000. The bigger problem is that the imbalance is concentrated within the manufacturing sector where wages and employment have declined since the 1990s. US manufacturing employment has declined dramatically, from 26 percent in 1970 down to 8.5 percent in 2016. Some economists attribute China's increasing competition to the decline, but most blame the decline on automation, productivity increases and the shifting of consumer demand away form goods to services.
Industry has a shotgun approach
The US manufacturing sector is well-known for its many advanced manufacturing initiatives. Some countries, however, are taking a more focused approach to bringing the internet into manufacturing. The US, on other hand, is focused on different technologies and blends traditional mass media with Internet advertisement. The result is a shotgun approach, where companies focus on many different technologies and aim for a broad customer base.
FAQ
What are the 7 Rs of logistics?
The acronym 7R's for Logistics stands to represent the seven basic principles in logistics management. It was developed and published by the International Association of Business Logisticians in 2004 as part of the "Seven Principles of Logistics Management".
The acronym is made up of the following letters:
-
Responsible - ensure that actions are in compliance with legal requirements and do not cause harm to others.
-
Reliable - You can have confidence that you will fulfill your promises.
-
Reasonable - use resources efficiently and don't waste them.
-
Realistic – consider all aspects of operations, from cost-effectiveness to environmental impact.
-
Respectful - treat people fairly and equitably.
-
Resourceful - look for opportunities to save money and increase productivity.
-
Recognizable: Provide customers with value-added service
How can excess manufacturing production be reduced?
Improved inventory management is the key to reducing overproduction. This would reduce the amount of time spent on unnecessary activities such as purchasing, storing, and maintaining excess stock. This will allow us to free up resources for more productive tasks.
You can do this by adopting a Kanban method. A Kanban Board is a visual display that tracks work progress. Kanban systems allow work items to move through different states until they reach their final destination. Each state represents a different priority.
When work is completed, it can be transferred to the next stage. But if a task remains in the beginning stages it will stay that way until it reaches its end.
This allows work to move forward and ensures that no work is missed. A Kanban board allows managers to monitor how much work is being completed at any given moment. This allows them to adjust their workflows based on real-time information.
Lean manufacturing can also be used to reduce inventory levels. Lean manufacturing focuses on eliminating waste throughout the entire production chain. Anything that does nothing to add value to a product is waste. Some common types of waste include:
-
Overproduction
-
Inventory
-
Unnecessary packaging
-
Overstock materials
These ideas can help manufacturers improve efficiency and reduce costs.
How does manufacturing avoid bottlenecks in production?
To avoid production bottlenecks, ensure that all processes run smoothly from the moment you receive your order to the time the product ships.
This includes both quality control and capacity planning.
Continuous improvement techniques like Six Sigma are the best way to achieve this.
Six Sigma Management System is a method to increase quality and reduce waste throughout your organization.
It emphasizes consistency and eliminating variance in your work.
Statistics
- In the United States, for example, manufacturing makes up 15% of the economic output. (twi-global.com)
- You can multiply the result by 100 to get the total percent of monthly overhead. (investopedia.com)
- In 2021, an estimated 12.1 million Americans work in the manufacturing sector.6 (investopedia.com)
- Job #1 is delivering the ordered product according to specifications: color, size, brand, and quantity. (netsuite.com)
- According to the United Nations Industrial Development Organization (UNIDO), China is the top manufacturer worldwide by 2019 output, producing 28.7% of the total global manufacturing output, followed by the United States, Japan, Germany, and India.[52][53] (en.wikipedia.org)
External Links
How To
How to Use Six Sigma in Manufacturing
Six Sigma refers to "the application and control of statistical processes (SPC) techniques in order to achieve continuous improvement." Motorola's Quality Improvement Department created Six Sigma at their Tokyo plant, Japan in 1986. The basic idea behind Six Sigma is to improve quality by improving processes through standardization and eliminating defects. This method has been adopted by many companies in recent years as they believe there are no perfect products or services. Six Sigma's primary goal is to reduce variation from the average value of production. You can calculate the percentage of deviation from the norm by taking a sample of your product and comparing it to the average. If it is too large, it means that there are problems.
Understanding the nature of variability in your business is the first step to Six Sigma. Once you understand that, it is time to identify the sources of variation. These variations can also be classified as random or systematic. Random variations are caused when people make mistakes. While systematic variations are caused outside of the process, they can occur. For example, if you're making widgets, and some of them fall off the assembly line, those would be considered random variations. If however, you notice that each time you assemble a widget it falls apart in exactly the same spot, that is a problem.
Once you've identified where the problems lie, you'll want to design solutions to eliminate those problems. The solution could involve changing how you do things, or redesigning your entire process. Once you have implemented the changes, it is important to test them again to ensure they work. If they didn't work, then you'll need to go back to the drawing board and come up with another plan.