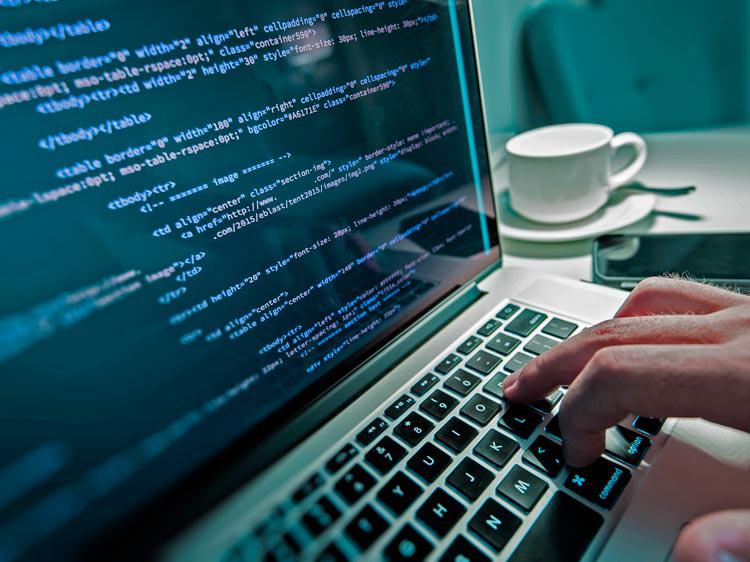
The US's manufacturing sector represents a significant part of the American economy. It accounts for about 11 percent of the nation’s total economic output. It also contributes a lot to the world economy, accounting for 18.2 per cent of global goods. However, growth in the manufacturing sector has been slowing in recent years.
Since 2000, the US has lost one-third of its factory jobs. According to the Bureau of Labor Statistics (BLS), manufacturing productivity rose 4.5 percent annually from 1995 to 2000. Manufacturing used to be viewed as a declining job source, but automation has led to a reexamination about how technology is impacting employment.
Walmart committed in January 2013 to support American jobs. Walmart intends to purchase $250 Billion in products from American companies within ten years. Walmart's commitment means that it can support more American manufacturing and encourage many companies to explore possibilities with the giant retailer.
The United States has been a major player on the global market but it has also faced many challenges. These challenges include the high cost of labor abroad, a rising corporate tax rate and a shortage of trade negotiation skills. These issues could impact the sector's ability to thrive in the future.
The US also faces a skills problem, with an estimated 1.42 million factory workers in desperate need of training. Trump's policies have been designed to encourage training and expand apprenticeship programs. But, the administration has raised concerns over the quality of such efforts.
Despite all the problems, however the US manufacturing sector has recovered from the Great Recession. In the first quarter, 2018, manufacturing output reached a record-breaking $2.00 trillion. This is more than the $1.95 trillion that was recorded in the year prior to the recession.
While the US's manufacturing sector has experienced slower growth than the US overall economy, the industry is expected to grow at an even faster pace in the next few years. The industry is expected to grow by 2.4 percent in 2020 and 1.9% 2021.
Exports are expected to increase, which will help the manufacturing sector. Shale oil has helped the industry reduce its energy costs. Furthermore, the United States has a competitive corporate tax rate, which is higher than most countries in the world.
In the meantime, China, Japan and South Korea are experiencing manufacturing declines. In these countries, this is the first time in nearly two years that the S&P Global purchasing manager index has fallen below 50.
Trump's administration is apparently working on a more efficient federal program to support manufacturing. Manufacturing Extension Partnership (MEP) is one of the most important federal programs. MEPs are responsible for $21 of new client investment per $21 federal government investment. MEP centers are located in every state, along with Canada, Mexico and Europe.
The US is in a weaker position than other industrial countries when it comes to trade negotiations. This means that the government does not have the skills to negotiate bilateral trade agreements. Therefore, the US is having difficulty attracting new manufacturers and maintaining existing businesses.
FAQ
Why is logistics important for manufacturing?
Logistics are an essential part of any business. They help you achieve great results by helping you manage all aspects of product flow, from raw materials to finished goods.
Logistics play a key role in reducing expenses and increasing efficiency.
How can manufacturing prevent production bottlenecks?
The key to avoiding bottlenecks in production is to keep all processes running smoothly throughout the entire production cycle, from the time you receive an order until the time when the product ships.
This includes both quality control and capacity planning.
Continuous improvement techniques such Six Sigma are the best method to accomplish this.
Six Sigma can be used to improve the quality and decrease waste in all areas of your company.
It's all about eliminating variation and creating consistency in work.
What is the responsibility of a logistics manager?
Logistics managers are responsible for ensuring that all goods arrive in perfect condition and on time. This is done using his/her knowledge of the company's products. He/she also needs to ensure adequate stock to meet demand.
What are the responsibilities of a manufacturing manager
A manufacturing manager must ensure that all manufacturing processes are efficient and effective. They should also be aware of any problems within the company and act accordingly.
They should also learn how to communicate effectively with other departments, including sales and marketing.
They should be up to date on the latest trends and be able apply this knowledge to increase productivity and efficiency.
Statistics
- You can multiply the result by 100 to get the total percent of monthly overhead. (investopedia.com)
- [54][55] These are the top 50 countries by the total value of manufacturing output in US dollars for its noted year according to World Bank.[56] (en.wikipedia.org)
- In 2021, an estimated 12.1 million Americans work in the manufacturing sector.6 (investopedia.com)
- In the United States, for example, manufacturing makes up 15% of the economic output. (twi-global.com)
- Job #1 is delivering the ordered product according to specifications: color, size, brand, and quantity. (netsuite.com)
External Links
How To
How to Use Six Sigma in Manufacturing
Six Sigma refers to "the application and control of statistical processes (SPC) techniques in order to achieve continuous improvement." Motorola's Quality Improvement Department developed it at their Tokyo plant in Japan in 1986. Six Sigma's core idea is to improve the quality of processes by standardizing and eliminating defects. In recent years, many companies have adopted this method because they believe there is no such thing as perfect products or services. The main goal of Six Sigma is to reduce variation from the mean value of production. This means that you can take a sample from your product and then compare its performance to the average to find out how often the process differs from the norm. If the deviation is excessive, it's likely that something needs to be fixed.
The first step toward implementing Six Sigma is understanding how variability works in your business. Once you've understood that, you'll want to identify sources of variation. This will allow you to decide if these variations are random and systematic. Random variations occur when people do mistakes. Symmetrical variations are caused due to factors beyond the process. For example, if you're making widgets, and some of them fall off the assembly line, those would be considered random variations. If however, you notice that each time you assemble a widget it falls apart in exactly the same spot, that is a problem.
Once you have identified the problem, you can design solutions. This could mean changing your approach or redesigning the entire process. Test them again once you've implemented the changes. If they don't work you need to rework them and come up a better plan.