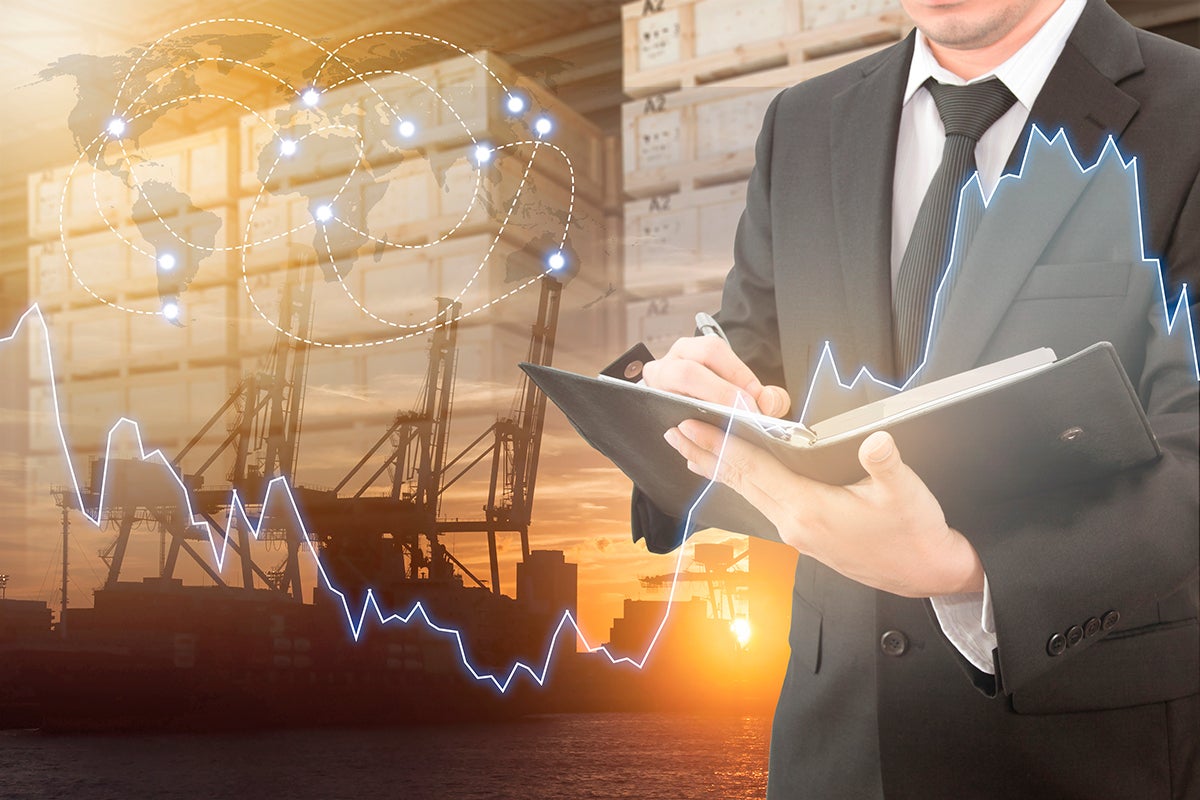
Apparel manufacturers today face a unique challenge in meeting the diverse demands of their customers. These consumers vary in terms of physiographics, socioeconomics, and demographics, and their preferences are not easily predictible. Additionally, consumer awareness of different products is increasing, and they can access information readily. Consumers are also becoming more inclined buy high-fashion, costly items.
Production efficiency
The overall strategy for apparel manufacturers includes a focus on increasing production efficiency. The clothing industry is highly dependent on human labor, and with ever-changing fashion trends, production planning is essential to meet the needs of consumers and the marketplace. Apparel manufacturers must be flexible enough to meet global demands and maintain a short product cycle. In addition to planning for new products, apparel manufacturers should evaluate the efficiency of their existing lines and implement digital technologies, which can reduce the product development cycle from months to days. Critical path analysis is an essential part of the planning process.
Although the apparel manufacturing industry is very labor-intensive, it is not impossible to increase production efficiency. To achieve this goal, you need the right tools as well as proper management. EBITDA can increase by as much as 35% if efficiency is increased by just 10 to 15%. Moreover, efficiency increases workers' wages and can improve the country's ability to compete in the global market.
Fabric layering
Fabric layering is an apparel manufacturing technique. It involves placing a pre-made pattern on top of a lay. The pattern can either be drawn manually or by using a plotter. The pattern components can be laid in the markers. After that, they are cut with a straight blade or other cutting method.
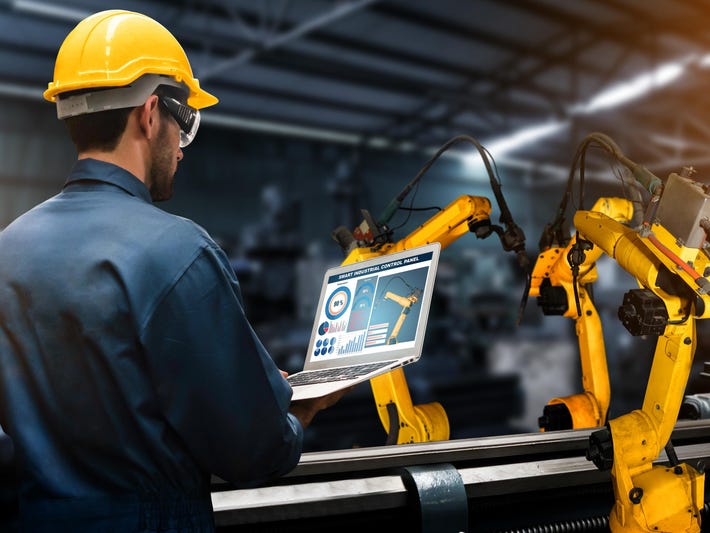
During this process, the fabric is spread evenly. It can be laid out in a pile or laid out in superimposed layers with the cutting marker on top. The maximum cut width is the fabric width less the needle marks and the selvedge. The fabric usage is also known as the fabric area. Half-garment layout and whole-garment layout are the two main types. Half-garment Lay involves placing fabric on only one side of a garment piece. Whole-garment Lay involves covering fabric on both sides. The downside to whole garment lay is the fact that it takes up more fabric.
Cutting
Cutting refers to the use of cutting tools to cut fabric into smaller pieces. Fabric can cost between 60 and 70 percent of a garment's price. It is crucial that every inch be used. It is important to use every inch of fabric when making apparel.
Spreading fabric onto a large surface is the first step to cutting fabric. Spreading fabric in mass production usually involves using a lot of layers. Based on the number and thickness of the fabric, the cutting master decides how many layers are needed to cover a particular garment. After the fabric has been spread it is measured to determine the maximum cutting width.
Pressing
In the manufacture of apparel, pressing is an important step. It controls the appearance of garments and helps them to maintain their comfort. It is usually done in a factory. The press can be either manually or automatically operated. Software can be used to control the automation level. Software can also program a press to follow a set of instructions. A factory that produces apparel can automate pressing to reduce human error. The increased number of fabric and fiber varieties will require more precise temperature and pressure control.
Pressing refers to using heat to soften the fibers. The shape of the garment is stabilized with the softened fibres. The correct temperature should be chosen to avoid damaging the yarn or fibres.
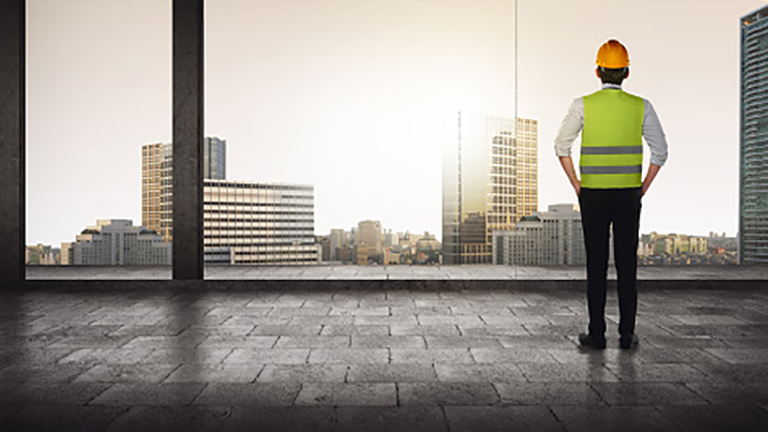
Minimum order quantity
You should know the minimum order quantity (MOQ) of any clothing manufacturer you are considering when you source for one. Many garment factories will not produce your garments without a minimum order amount. The MOQ is dependent on the technical characteristics of your designs and varies from one factory to another. Some factories are able to accept orders up to 100 items. Others require orders over a thousand.
Most manufacturers need to have a minimum order quantity (MOQ), especially if they deal in bulk products. This quantity helps them to remain profitable and weeds out businesses that want to purchase items in small quantities but aren't necessarily looking to place a large order. This is especially important with custom orders.
FAQ
Can some manufacturing processes be automated?
Yes! Yes! Automation has existed since ancient times. The wheel was invented by the Egyptians thousands of years ago. Nowadays, we use robots for assembly lines.
There are many uses of robotics today in manufacturing. These include:
-
Robots for assembly line
-
Robot welding
-
Robot painting
-
Robotics inspection
-
Robots that create products
Manufacturing can also be automated in many other ways. 3D printing makes it possible to produce custom products in a matter of days or weeks.
What are the responsibilities for a manufacturing manager
A manufacturing manager has to ensure that all manufacturing processes work efficiently and effectively. They should also be aware and responsive to any company problems.
They should also be able and comfortable communicating with other departments like sales and marketing.
They must also keep up-to-date with the latest trends in their field and be able use this information to improve productivity and efficiency.
How can excess manufacturing production be reduced?
In order to reduce excess production, you need to develop better inventory management methods. This would reduce time spent on activities such as purchasing, stocking, and maintaining excess stock. This will allow us to free up resources for more productive tasks.
You can do this by adopting a Kanban method. A Kanban board is a visual display used to track work in progress. Kanban systems are where work items travel through a series of states until reaching their final destination. Each state is assigned a different priority.
To illustrate, work can move from one stage or another when it is complete enough for it to be moved to a new stage. It is possible to keep a task in the beginning stages until it gets to the end.
This allows you to keep work moving along while making sure that no work gets neglected. Managers can view the Kanban board to see how much work they have done. This allows them the ability to adjust their workflow using real-time data.
Another way to control inventory levels is to implement lean manufacturing. Lean manufacturing is about eliminating waste from all stages of the production process. Anything that doesn't add value to the product is considered waste. The following are examples of common waste types:
-
Overproduction
-
Inventory
-
Unnecessary packaging
-
Material surplus
Manufacturers can increase efficiency and decrease costs by implementing these ideas.
Statistics
- In the United States, for example, manufacturing makes up 15% of the economic output. (twi-global.com)
- In 2021, an estimated 12.1 million Americans work in the manufacturing sector.6 (investopedia.com)
- According to the United Nations Industrial Development Organization (UNIDO), China is the top manufacturer worldwide by 2019 output, producing 28.7% of the total global manufacturing output, followed by the United States, Japan, Germany, and India.[52][53] (en.wikipedia.org)
- (2:04) MTO is a production technique wherein products are customized according to customer specifications, and production only starts after an order is received. (oracle.com)
- According to a Statista study, U.S. businesses spent $1.63 trillion on logistics in 2019, moving goods from origin to end user through various supply chain network segments. (netsuite.com)
External Links
How To
How to use 5S to increase Productivity in Manufacturing
5S stands for "Sort", "Set In Order", "Standardize", "Separate" and "Store". Toyota Motor Corporation invented the 5S strategy in 1954. It allows companies to improve their work environment, thereby achieving greater efficiency.
The idea behind standardizing production processes is to make them repeatable and measurable. This means that daily tasks such as cleaning and sorting, storage, packing, labeling, and packaging are possible. Workers can be more productive by knowing what to expect.
There are five steps that you need to follow in order to implement 5S. Each step requires a different action to increase efficiency. Sorting things makes it easier to find them later. When you arrange items, you place them together. Then, after you separate your inventory into groups, you store those groups in containers that are easy to access. Finally, label all containers correctly.
This requires employees to critically evaluate how they work. Employees must be able to see why they do what they do and find a way to achieve them without having to rely on their old methods. To implement the 5S system, employees must acquire new skills and techniques.
The 5S method not only increases efficiency but also boosts morale and teamwork. They feel more motivated to work towards achieving greater efficiency as they see the results.