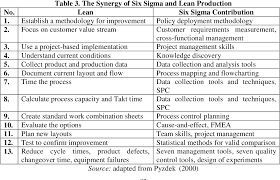
The Great Recession saw 166,000 jobs being lost by Ohio manufacturing companies. Ohio's manufacturing sector is slowly recovering, but this has not been faster than in other states. Ohio's manufacturing sector is still at a lower level than it was before the recession.
Ohio's drop in manufacturing jobs is due largely to the rise of European and Japanese manufacturing competition. Manufacturers have had to improve their technology and cut labor costs. The global economic climate has been lukewarm, which has contributed to job losses.
Ohio's current workforce crisis is a significant challenge for manufacturers. There are many initiatives that can be taken to address the state's skilled labor shortage. These initiatives are fragmented and siloed and don't address all the workforce issues manufacturers face. The Ohio Governor's Office of Workforce Transformation produced a special report on the workforce shortfall that recommended better collaboration between business and education. The report revealed a disconnect between school curriculum and business requirements.
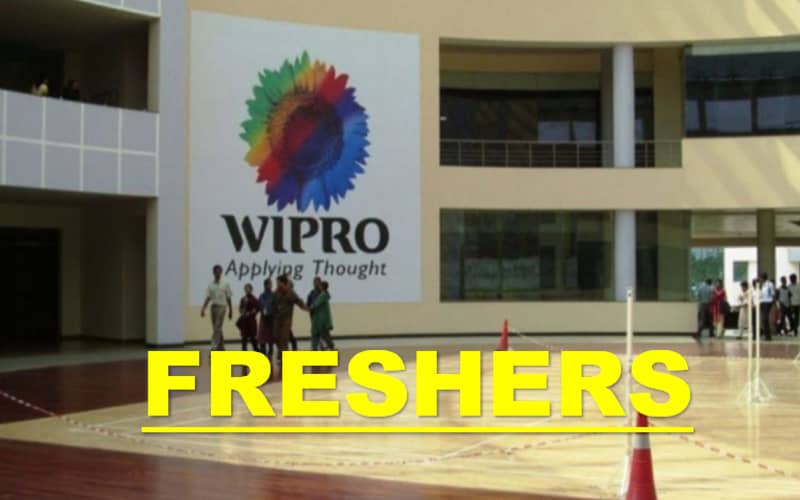
Ohio's workforce can be complex, multifaceted and varied. Manufacturing workers are less likely not to be represented by unions than workers in other industry sectors. Unionized manufacturing jobs provide solid benefits and livable earnings.
Ohio's manufacturing industry is a significant contributor to the state's economy. Utilizing interstate highways and railways as well as inland waterways, manufacturers can distribute their goods at a competitive price. Additionally, the state is a top exporter. Private investors are attracted to the state's natural gas production.
While the state has gained 50,000 manufacturing job opportunities over the past four years of his administration, Kasich's tenure in office has seen slow job gains. Manufacturing job gains averaged 7 per cent in Kasich's first three years. Manufacturing jobs have dropped by 1,771 jobs in the last two years. These losses are due primarily to the slowing economic growth, the auto industry and lukewarm global market demand.
Ohio is a major exporter of goods. It has top export markets such as the U.S., Canada and Mexico. However, exports have fallen by $1.4 million in the last year. Ohio manufacturers still face major challenges in trade policy. While trade policy changes may be helpful to certain workers, they will not address the whole range of problems.
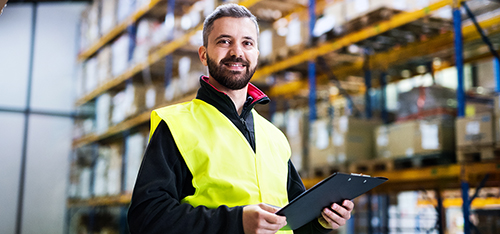
Ohio's main industry, manufacturing, is still very important. Manufacturing jobs offer semi-skilled workers the best opportunities for high-paying jobs without requiring post-secondary education. Wages have not kept up to the pace of Ohio's production. While manufacturing jobs are more lucrative than those in other industries, they are not sufficient to provide a middle-class lifestyle.
Ohio's diverse workforce of manufacturing workers includes many different workers. The state's manufacturing industries have been diversifying to match the rest of the nation. Ohio's economy has changed to be more service-oriented. Manufacturing no longer is the main employer. Manufacturers are more focused on international exposure and developing skills to support future generations.
FAQ
What is the distinction between Production Planning or Scheduling?
Production Planning (PP), is the process of deciding what production needs to take place at any given time. Forecasting demand is one way to do this.
Scheduling refers to the process of allocating specific dates to tasks in order that they can be completed within a specified timeframe.
What are manufacturing and logistics?
Manufacturing refers the process of producing goods from raw materials through machines and processes. Logistics manages all aspects of the supply chain, including procurement, production planning and distribution, inventory control, transportation, customer service, and transport. Sometimes manufacturing and logistics are combined to refer to a wider term that includes both the process of creating products as well as their delivery to customers.
What skills does a production planner need?
A production planner must be organized, flexible, and able multitask to succeed. It is also important to be able communicate with colleagues and clients.
Statistics
- According to the United Nations Industrial Development Organization (UNIDO), China is the top manufacturer worldwide by 2019 output, producing 28.7% of the total global manufacturing output, followed by the United States, Japan, Germany, and India.[52][53] (en.wikipedia.org)
- It's estimated that 10.8% of the U.S. GDP in 2020 was contributed to manufacturing. (investopedia.com)
- [54][55] These are the top 50 countries by the total value of manufacturing output in US dollars for its noted year according to World Bank.[56] (en.wikipedia.org)
- In 2021, an estimated 12.1 million Americans work in the manufacturing sector.6 (investopedia.com)
- You can multiply the result by 100 to get the total percent of monthly overhead. (investopedia.com)
External Links
How To
How to use the Just-In Time Method in Production
Just-in-time (JIT) is a method that is used to reduce costs and maximize efficiency in business processes. It's a way to ensure that you get the right resources at just the right time. This means that only what you use is charged to your account. Frederick Taylor was the first to coin this term. He developed it while working as a foreman during the early 1900s. He saw how overtime was paid to workers for work that was delayed. He then concluded that if he could ensure that workers had enough time to do their job before starting to work, this would improve productivity.
JIT teaches you to plan ahead and prepare everything so you don’t waste time. Look at your entire project, from start to end. Make sure you have enough resources in place to deal with any unexpected problems. You can anticipate problems and have enough equipment and people available to fix them. You won't have to pay more for unnecessary items.
There are many JIT methods.
-
Demand-driven JIT: You order the parts and materials you need for your project every other day. This will enable you to keep track of how much material is left after you use it. This will let you know how long it will be to produce more.
-
Inventory-based: This allows you to store the materials necessary for your projects in advance. This allows you to predict how much you can expect to sell.
-
Project-driven: This approach involves setting aside sufficient funds to cover your project's costs. When you know how much you need, you'll purchase the appropriate amount of materials.
-
Resource-based JIT : This is probably the most popular type of JIT. This is where you assign resources based upon demand. You will, for example, assign more staff to deal with large orders. If you don't receive many orders, then you'll assign fewer employees to handle the load.
-
Cost-based: This is a similar approach to resource-based but you are not only concerned with how many people you have, but also how much each one costs.
-
Price-based: This approach is very similar to the cost-based method except that you don't look at individual workers costs but the total cost of the company.
-
Material-based: This is very similar to cost-based but instead of looking at total costs of the company you are concerned with how many raw materials you use on an average.
-
Time-based JIT is another form of resource-based JIT. Instead of worrying about how much each worker costs, you can focus on how long the project takes.
-
Quality-based JIT: This is another variation of resource based JIT. Instead of thinking about how much each employee costs or how long it takes to manufacture something, you think about how good the quality of your product is.
-
Value-based JIT is the newest form of JIT. In this instance, you are not concerned about the product's performance or meeting customer expectations. Instead, your focus is on the value you bring to the market.
-
Stock-based. This method is inventory-based and focuses only on the actual production at any given point. It is used when production goals are met while inventory is kept to a minimum.
-
Just-intime (JIT), planning is a combination JIT management and supply chain management. This refers to the scheduling of the delivery of components as soon after they are ordered. This is important as it reduces lead time and increases throughput.