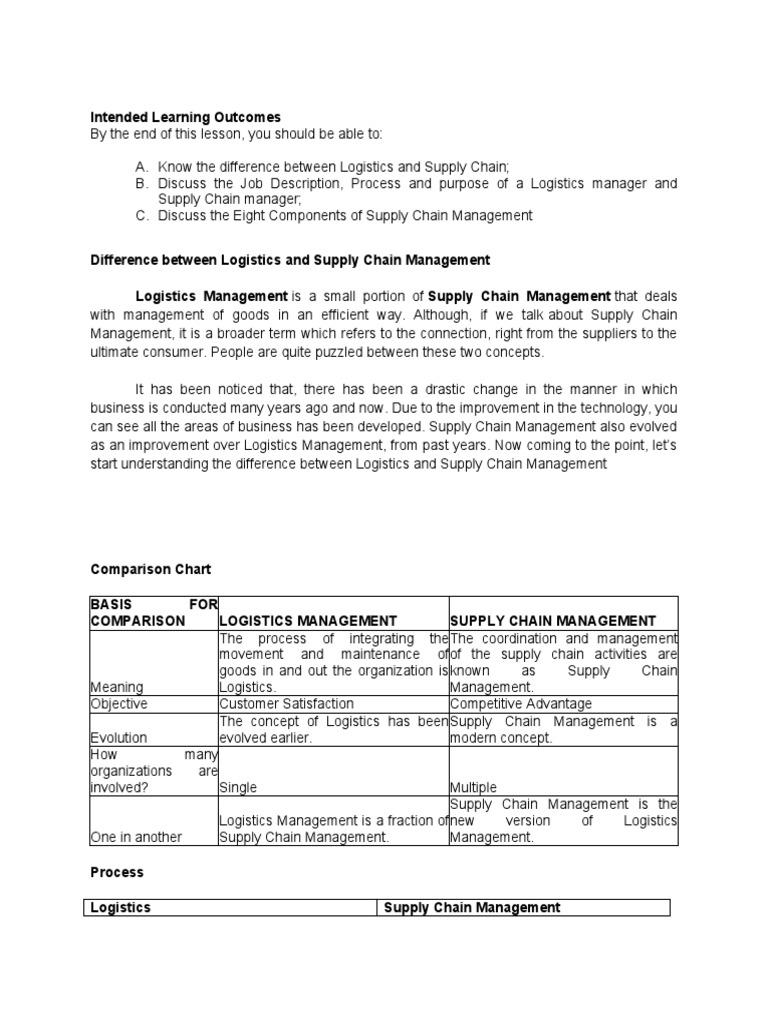
Event planners and meeting organizers plan everything involved in an event. They must also establish positive relationships with clients and suppliers. They should also be up to date with current trends in meeting management. This job can be very satisfying.
Event Planners typically work more than forty hours a week and must be able to multitask and meet a variety of objectives. They select meeting sites, choose speakers, and arrange audio-visual displays and entertainment. They should also consider the costs of hosting an event as well as the appropriate atmosphere. Often, they plan a meeting more than a year in advance. They must be able to communicate effectively with hundreds of people and convey the clients' needs with confidence.
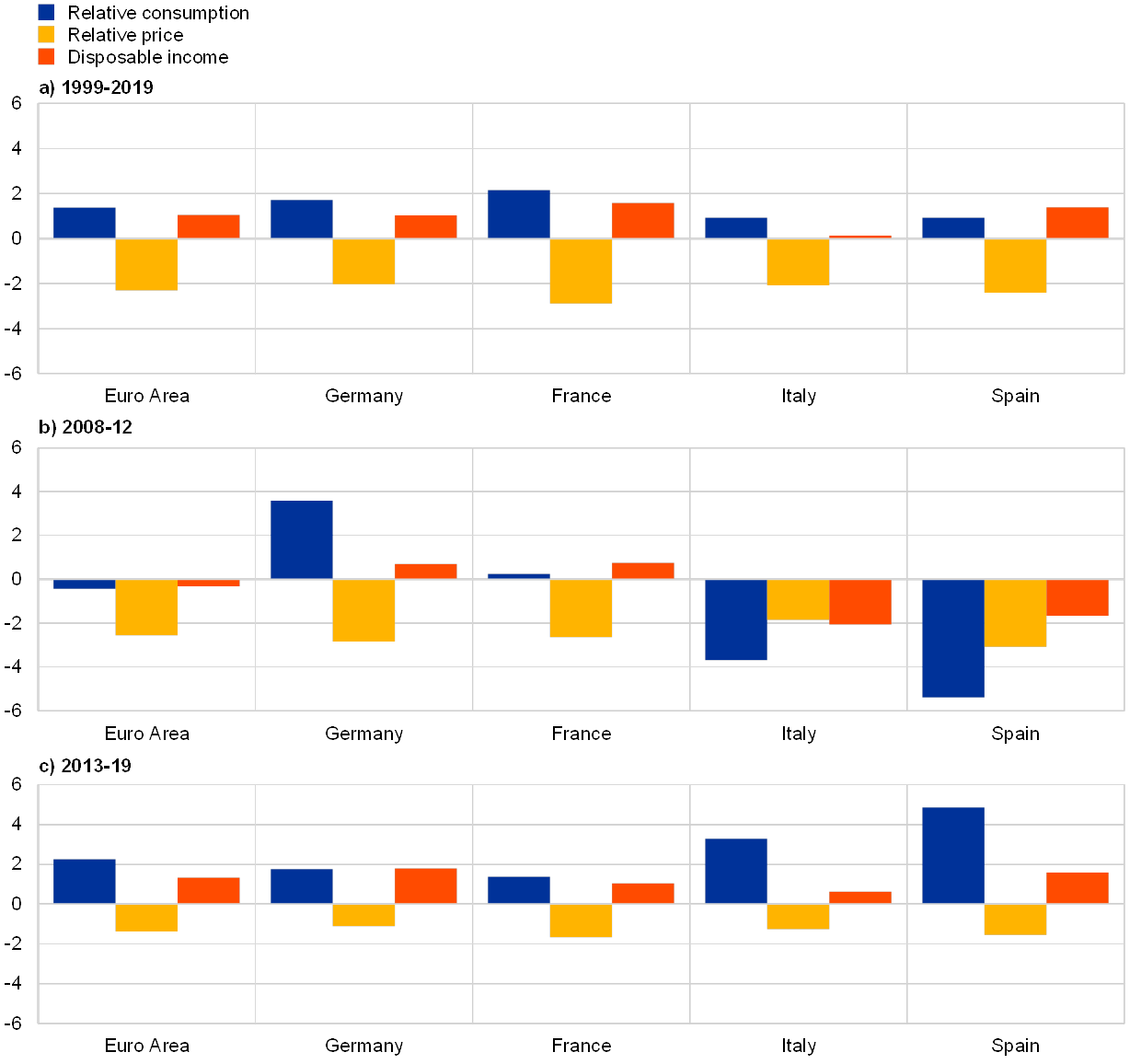
Many meeting, convention, and event planners work for professional associations or government agencies. They might also work at trade shows, convention centers, and fundraising events. They should be able work in a team to ensure that the meeting meets all ethical and legal requirements. They should also be able develop innovative solutions. They should also be able meet tight deadlines. Their salary can be quite high. Meeting convention and event planners could earn $55,891 per year depending on their experience and location. The median annual salary is $51,600.
For those who want to be a meeting planner, convention organizer or event planner, continuing education courses may be beneficial. They may also be eligible for certifications that show their knowledge. These certifications will help them stand out on a competitive job market. Some certifications, such as the Society of Government Meeting Professionals (SGMP) certification, require that the applicant have experience planning meetings. They also require applicants to pass a qualifying test.
Meeting, convention and event planners typically have an interest in the following areas: persuading others, organizing and maintaining order. They are responsible for coordinating with suppliers and clients to help them develop and execute plans. They might also organize speakers or other activities. They might specialize in fundraising events, such as events for government and professional associations. They should be able manage tight deadlines and negotiate service contracts.
Training for a job as a meeting, convention, or event planner can take several years. The US Department of Labor says there are approximately 125.900 US meeting planners. The number of available jobs will continue to rise over the next decade. But many of them will be created by the need to replace workers. It is predicted that the number of jobs will increase by approximately seven percent in 2020 and 18% in 2028. The national wage distribution lists the salaries of meeting, convention, and event planners. The average annual salary for a senior convention planner or event planner is $88,360.
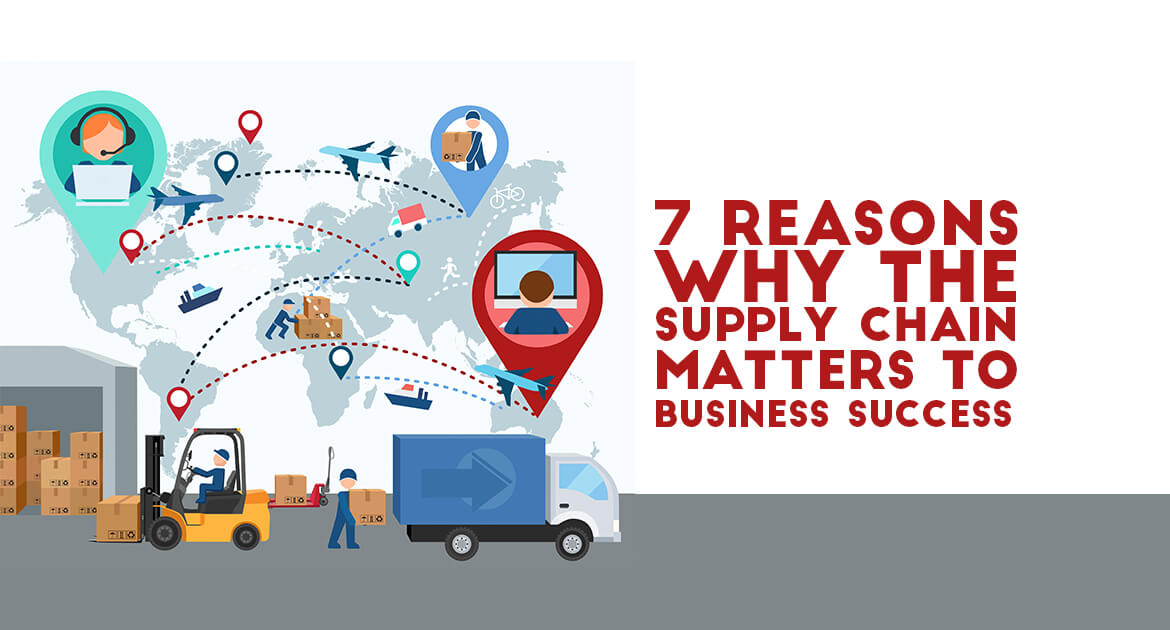
There are many different job titles that can be used for meeting, convention, or event planners. International Association of Exhibitions and Events provides the Certified Event Manager (CEM), designation. Additionally, the Events Industry Council manages the Certified Meeting Professional credential (CMP). These certifications are useful in helping a person stand out among the meeting- and event planning community.
FAQ
How can manufacturing efficiency improved?
The first step is to determine the key factors that impact production time. The next step is to identify the most important factors that affect production time. If you don’t know how to start, look at which factors have the greatest impact upon production time. Once you have identified the factors, then try to find solutions.
What skills does a production planner need?
To become a successful production planner, you need to be organized, flexible, and able to multitask. It is also important to be able communicate with colleagues and clients.
What is the role of a production manager?
Production planners ensure all aspects of the project are delivered within time and budget. They also ensure the quality of the product and service meets the client's requirements.
What are the responsibilities of a manufacturing manager
Manufacturing managers must ensure that manufacturing processes are efficient, effective, and cost-effective. They should also be aware and responsive to any company problems.
They should also know how to communicate with other departments such as sales and marketing.
They should also be aware of the latest trends in their industry and be able to use this information to help improve productivity and efficiency.
What do we need to know about Manufacturing Processes in order to learn more about Logistics?
No. No. It is important to know about the manufacturing processes in order to understand how logistics works.
How can manufacturing prevent production bottlenecks?
The key to avoiding bottlenecks in production is to keep all processes running smoothly throughout the entire production cycle, from the time you receive an order until the time when the product ships.
This includes planning to meet capacity requirements and quality control.
This can be done by using continuous improvement techniques, such as Six Sigma.
Six Sigma management is a system that improves quality and reduces waste within your organization.
It focuses on eliminating variation and creating consistency in your work.
Can certain manufacturing steps be automated?
Yes! Yes. Automation has been around since ancient time. The Egyptians invent the wheel thousands of year ago. Today, robots assist in the assembly of lines.
There are many applications for robotics in manufacturing today. These include:
-
Automated assembly line robots
-
Robot welding
-
Robot painting
-
Robotics inspection
-
Robots that make products
Manufacturing could also benefit from automation in other ways. 3D printing makes it possible to produce custom products in a matter of days or weeks.
Statistics
- It's estimated that 10.8% of the U.S. GDP in 2020 was contributed to manufacturing. (investopedia.com)
- In the United States, for example, manufacturing makes up 15% of the economic output. (twi-global.com)
- (2:04) MTO is a production technique wherein products are customized according to customer specifications, and production only starts after an order is received. (oracle.com)
- In 2021, an estimated 12.1 million Americans work in the manufacturing sector.6 (investopedia.com)
- According to a Statista study, U.S. businesses spent $1.63 trillion on logistics in 2019, moving goods from origin to end user through various supply chain network segments. (netsuite.com)
External Links
How To
Six Sigma in Manufacturing:
Six Sigma refers to "the application and control of statistical processes (SPC) techniques in order to achieve continuous improvement." Motorola's Quality Improvement Department in Tokyo, Japan developed Six Sigma in 1986. Six Sigma is a method to improve quality through standardization and elimination of defects. This method has been adopted by many companies in recent years as they believe there are no perfect products or services. Six Sigma seeks to reduce variation between the mean production value. This means that you can take a sample from your product and then compare its performance to the average to find out how often the process differs from the norm. If there is a significant deviation from the norm, you will know that something needs to change.
Understanding how your business' variability is a key step towards Six Sigma implementation is the first. Once you've understood that, you'll want to identify sources of variation. You'll also want to determine whether these variations are random or systematic. Random variations occur when people do mistakes. Symmetrical variations are caused due to factors beyond the process. For example, if you're making widgets, and some of them fall off the assembly line, those would be considered random variations. But if you notice that every widget you make falls apart at the exact same place each time, this would indicate that there is a problem.
Once you have identified the problem, you can design solutions. That solution might involve changing the way you do things or redesigning the process altogether. After implementing the new changes, you should test them again to see if they worked. If they fail, you can go back to the drawing board to come up with a different plan.