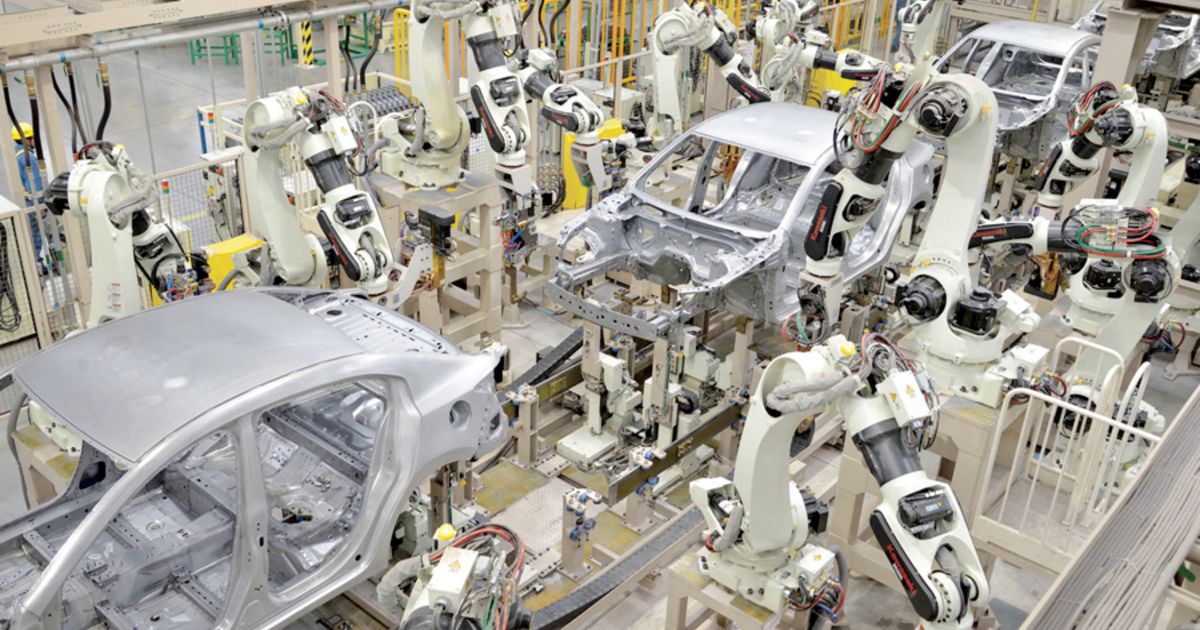
DMAIC stands for Define, Measure Analyze, Improve, Control. It is commonly used by Six Sigma professionals to make quality improvements in a company, but it can also be implemented independently as an effective and structured continuous improvement process.
Dmaic is a quality methodology that aims to reduce defects, cost and rework. It is a method that has been proven to improve customer satisfaction by ensuring products of high-quality, are efficient and perform consistently.
Using DMAIC is an easy way to solve issues in a business and it can be used to improve a variety of processes, including those that affect customer satisfaction, product quality, cost reductions, rework and cycle time. This is a key component of any quality improvement programme.
The DMAIC approach is a structured solution to problems that can help an organization identify and eliminate the root issues of any problem. The DMAIC Model uses a top down approach and systematic methodology to make it easier for teams implement foolproof, data-driven changes.
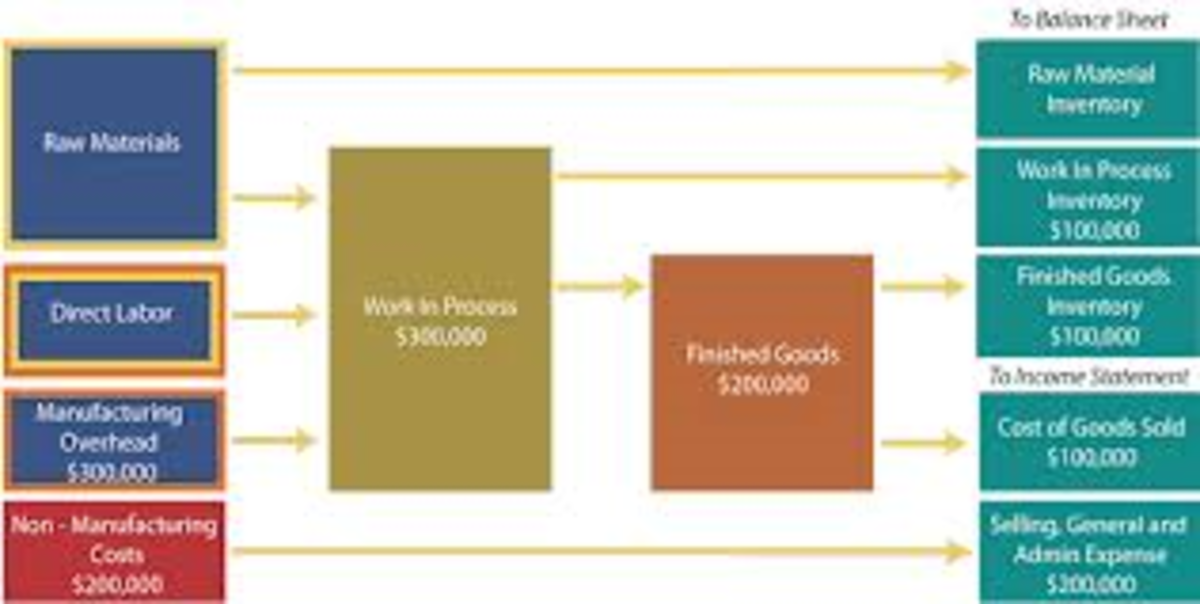
It is a powerful tool in Lean Six Sigma because it gives teams a defined and structured path to follow to find and fix quality problems. It is particularly important when dealing with complex problems that have unclear causes or involve risks from inaction.
Before choosing a DMAIC, it's important to know the criteria you should meet. It is important to understand the tools that can be used in this process, like fishbone diagrams or Pareto charts.
When you have chosen a DMAIC-qualified project, you should identify its goals and objectives. It is best to select projects that are relevant to the current state of the business and that meet the criteria for using DMAIC.
In the Define phase, DMAIC requires that the problem to be solved and the scope of improvement are clearly defined. It is usually done as part of a formal project chart, but can also be informal. It specifies the CTQ (critical-to-quality) issues, as well as the core processes and scope of the project.
This step is important in the DMAIC procedure because it enables the team to understand what needs to be done first, and what metrics should be used to track their success. It allows teams to determine their project champions and create the foundation for a successful DMAIC process.
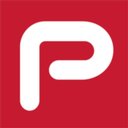
In the Measure phase teams compare the data collected from the current state to the desired state. The teams then use the information they have collected to identify gaps between two states and opportunities for improvement. This can also be achieved using tools such a scatterplots.
Teams identify possible solutions and test them for effectiveness after analyzing data. They implement the solutions, and confirm that they have measurable and durable results.
FAQ
What is the difference between manufacturing and logistics
Manufacturing is the process of creating goods from raw materials by using machines and processes. Logistics encompasses the management of all aspects associated with supply chain activities such as procurement, production planning, distribution and inventory control. It also includes customer service. Manufacturing and logistics are often considered together as a broader term that encompasses both the process of creating products and delivering them to customers.
Is it necessary to be familiar with Manufacturing Processes before we learn about Logistics.
No. You don't have to know about manufacturing processes before learning about logistics. Understanding the manufacturing process will allow you to better understand logistics.
What are the 7 Rs of logistics.
The acronym 7R's for Logistics stands to represent the seven basic principles in logistics management. It was developed by the International Association of Business Logisticians (IABL) and published in 2004 as part of its "Seven Principles of Logistics Management" series.
The acronym is composed of the following letters.
-
Responsible - to ensure that all actions are within the legal requirements and are not detrimental to others.
-
Reliable - Have confidence in your ability to fulfill all of your commitments.
-
Reasonable - use resources efficiently and don't waste them.
-
Realistic - consider all aspects of operations, including cost-effectiveness and environmental impact.
-
Respectful – Treat others fairly and equitably.
-
Responsive - Look for ways to save time and increase productivity.
-
Recognizable - Provide value-added services to customers
Statistics
- In 2021, an estimated 12.1 million Americans work in the manufacturing sector.6 (investopedia.com)
- It's estimated that 10.8% of the U.S. GDP in 2020 was contributed to manufacturing. (investopedia.com)
- [54][55] These are the top 50 countries by the total value of manufacturing output in US dollars for its noted year according to World Bank.[56] (en.wikipedia.org)
- Job #1 is delivering the ordered product according to specifications: color, size, brand, and quantity. (netsuite.com)
- Many factories witnessed a 30% increase in output due to the shift to electric motors. (en.wikipedia.org)
External Links
How To
How to Use the 5S to Increase Productivity In Manufacturing
5S stands as "Sort", Set In Order", Standardize", Separate" and "Store". Toyota Motor Corporation developed the 5S method in 1954. It allows companies to improve their work environment, thereby achieving greater efficiency.
This method has the basic goal of standardizing production processes to make them repeatable. This means that daily tasks such as cleaning and sorting, storage, packing, labeling, and packaging are possible. Workers can be more productive by knowing what to expect.
There are five steps that you need to follow in order to implement 5S. Each step requires a different action, which increases efficiency. For example, when you sort things, you make them easy to find later. When you arrange items, you place them together. Then, after you separate your inventory into groups, you store those groups in containers that are easy to access. Finally, label all containers correctly.
This requires employees to critically evaluate how they work. Employees need to be able understand their motivations and discover alternative ways to do them. They will need to develop new skills and techniques in order for the 5S system to be implemented.
The 5S Method not only improves efficiency, but it also helps employees to be more productive and happier. They are more motivated to achieve higher efficiency levels as they start to see improvement.