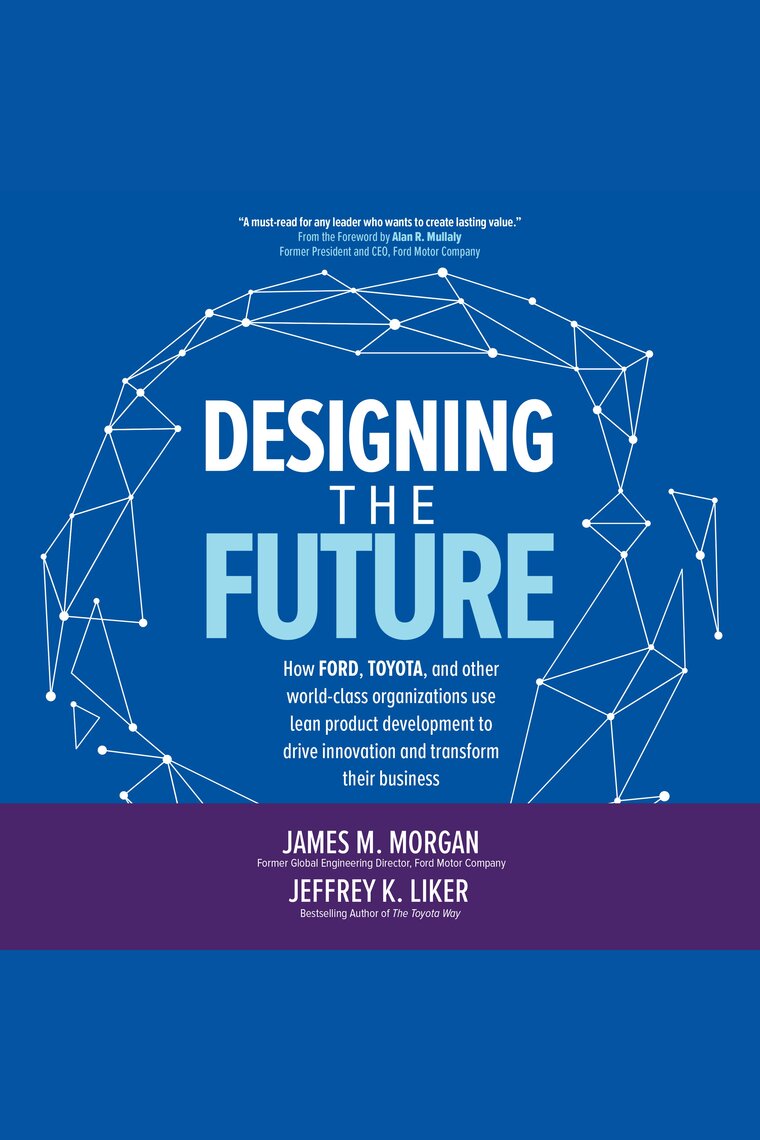
Demand management is a method that ensures that customers are satisfied. It basically involves bridging between supply and marketing, allowing companies to predict the demand. This process can increase speed and quality of delivery and reduce invoice disputes. It also lowers the cost of running a business.
Companies that have developed a mature demand management process tend to be more responsive to market changes. This is because they have a system in place to identify the ideal customer, which can lead to effective marketing.
Businesses can use demand management to plan for future demand and improve customer satisfaction. It can be used to reduce disputes over invoices and maximize asset utilization if done correctly. A solid demand management strategy is a good way to improve operational flexibility.
A demand management approach can be enhanced by using a project management software program. This software helps teams coordinate their work and prevents silos. Companies can quickly correct supply chain problems by creating a change management program.
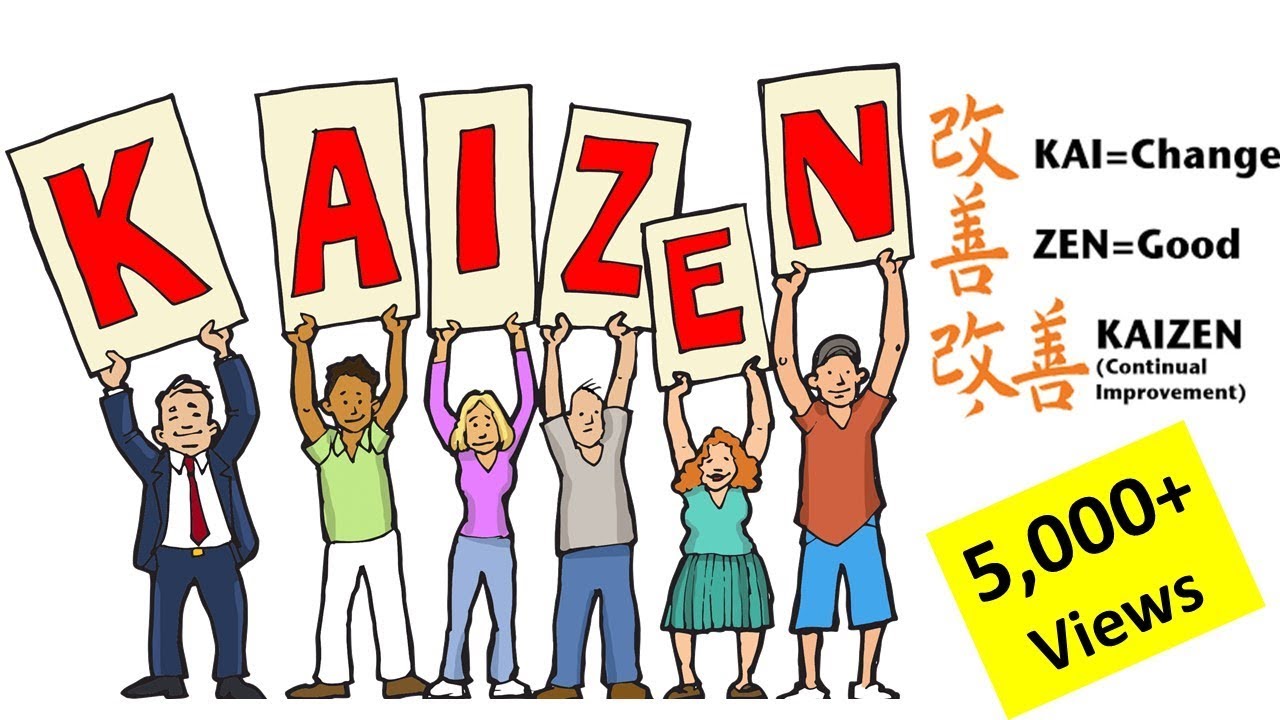
ILOG's PowerOps Suite combines manufacturing scheduling functions. Dynasys as well as QAD provide applications that allow organizations the ability to create and manage a demand/supply plan. These applications can be used to help organizations understand the impact of any changes made on their supply chains. Optiant provides ERP solutions that allow organizations to establish efficient, consistent, and effective order- and supply management processes.
Real-Time Inventory, Terra Technology, CDC Software and CDC Software offer real-time solutions for forecasting that can reduce supply chain disruptions. Companies can also benefit from the collaborative management strategy which allows them to share information. It incorporates performance indicators, knowledge-sharing, and planning for joint actions.
It is important to take into account a few things before you start to implement a demand-management strategy. These factors can be helpful for professionals to better understand the process and help them focus on the most crucial aspects.
Leadership buy in is an essential part of a demand management process. Demand management is a collaborative process that requires input from all levels of management. Managers and top executives are the most important players at the highest levels. They are responsible for ensuring all members are on the exact same page. Important to the success and sustainability of the initiative are those at the bottom.
There are many tools that can help you implement a demand/supply plan. But here are some things to keep in mind.
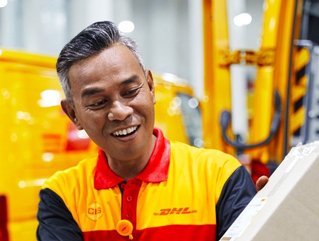
It is crucial to understand the market and identify the ideal customer. In addition to knowing who to target, the organization should be able to effectively measure and analyze the results of its efforts.
Businesses need to be more agile in order to develop a demand management plan that is easily adaptable to changing circumstances. An effective plan can decrease supply chain disruptions, tactical forecast error, and supply chain disruptions. Demand management is also a useful tool in the development and implementation of portfolio and strategic planning.
FAQ
How does a Production Planner differ from a Project Manager?
The major difference between a Production Planner and a Project Manager is that a Project Manager is often the person responsible for organizing and planning the entire project. While a Production Planner is involved mainly in the planning stage,
How can I find out more about manufacturing?
Hands-on experience is the best way to learn more about manufacturing. However, if that's not possible, you can always read books or watch educational videos.
What are the responsibilities for a manufacturing manager
A manufacturing manager must ensure that all manufacturing processes are efficient and effective. They must also be alert to any potential problems and take appropriate action.
They should also be able communicate with other departments, such as sales or marketing.
They should also be knowledgeable about the latest trends in the industry so they can use this information for productivity and efficiency improvements.
How can manufacturing reduce production bottlenecks?
Avoiding production bottlenecks is as simple as keeping all processes running smoothly, from the time an order is received until the product ships.
This includes planning to meet capacity requirements and quality control.
Continuous improvement techniques such Six Sigma can help you achieve this.
Six Sigma management is a system that improves quality and reduces waste within your organization.
It is focused on creating consistency and eliminating variation in your work.
Why is logistics important in manufacturing?
Logistics are essential to any business. They are essential to any business's success.
Logistics are also important in reducing costs and improving efficiency.
Statistics
- In 2021, an estimated 12.1 million Americans work in the manufacturing sector.6 (investopedia.com)
- It's estimated that 10.8% of the U.S. GDP in 2020 was contributed to manufacturing. (investopedia.com)
- (2:04) MTO is a production technique wherein products are customized according to customer specifications, and production only starts after an order is received. (oracle.com)
- Many factories witnessed a 30% increase in output due to the shift to electric motors. (en.wikipedia.org)
- Job #1 is delivering the ordered product according to specifications: color, size, brand, and quantity. (netsuite.com)
External Links
How To
How to Use the Just In Time Method in Production
Just-in-time is a way to cut costs and increase efficiency in business processes. It is a process where you get the right amount of resources at the right moment when they are needed. This means you only pay what you use. The term was first coined by Frederick Taylor, who developed his theory while working as a foreman in the early 1900s. After observing how workers were paid overtime for late work, he realized that overtime was a common practice. He decided to ensure workers have enough time to do their jobs before starting work to improve productivity.
The idea behind JIT is that you should plan ahead and have everything ready so you don't waste money. Also, you should look at the whole project from start-to-finish and make sure you have the resources necessary to address any issues. If you expect problems to arise, you will be able to provide the necessary equipment and personnel to address them. This way you won't be spending more on things that aren’t really needed.
There are many JIT methods.
-
Demand-driven JIT: This is a JIT that allows you to regularly order the parts/materials necessary for your project. This will let you track the amount of material left over after you've used it. It will also allow you to predict how long it takes to produce more.
-
Inventory-based: This allows you to store the materials necessary for your projects in advance. This allows you to forecast how much you will sell.
-
Project-driven : This is a method where you make sure that enough money is set aside to pay the project's cost. Once you have an idea of how much material you will need, you can purchase the necessary materials.
-
Resource-based: This is the most common form of JIT. You assign certain resources based off demand. You will, for example, assign more staff to deal with large orders. If you don't have many orders, you'll assign fewer people to handle the workload.
-
Cost-based: This is a similar approach to resource-based but you are not only concerned with how many people you have, but also how much each one costs.
-
Price-based: This is a variant of cost-based. However, instead of focusing on the individual workers' costs, this looks at the total price of the company.
-
Material-based - This is a variant of cost-based. But instead of looking at the total company cost, you focus on how much raw material you spend per year.
-
Time-based JIT is another form of resource-based JIT. Instead of focusing on how much each employee costs, you focus on how long it takes to complete the project.
-
Quality-based JIT: This is another variation of resource based JIT. Instead of worrying about the costs of each employee or how long it takes for something to be made, you should think about how quality your product is.
-
Value-based JIT: One of the most recent forms of JIT. In this scenario, you're not concerned about how products perform or whether customers expect them to meet their expectations. Instead, you focus on the added value that you provide to your market.
-
Stock-based: This is an inventory-based method that focuses on the actual number of items being produced at any given time. This method is useful when you want to increase production while decreasing inventory.
-
Just-intime planning (JIT), is a combination JIT/sales chain management. It's the process of scheduling delivery of components immediately after they are ordered. It's important as it reduces leadtimes and increases throughput.